自動車生産ライン向けシステム
自動車生産ライン向けシステムにおいて1世紀近くの実績を持つダイフクグループ。プレス・溶接・塗装・組立、部品の保管・供給、エンジンテストに至るまで、その全域にわたって自動化・省人化システムを供給しています。地球規模で展開されるエコカーや現地志向のナショナルカーなどグローバルに広がるモータリゼーションを、自動車生産に寄与する最先端の物流技術・ソリューションで支えています。
オートモーティブ事業紹介
製品ラインアップ
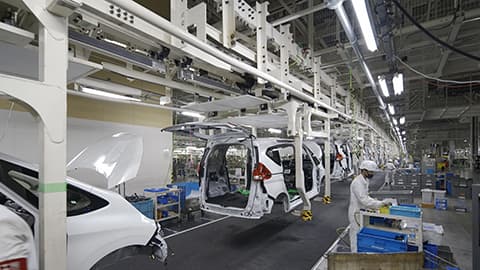
チェンレス搬送システム「フレキシブルドライブシステム」
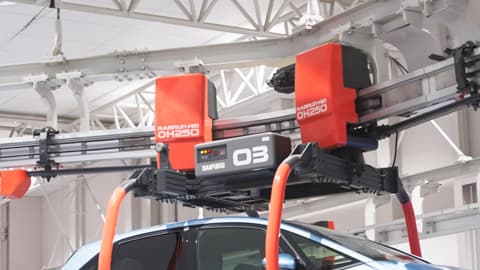
モノレールシステム「ラムラン®」
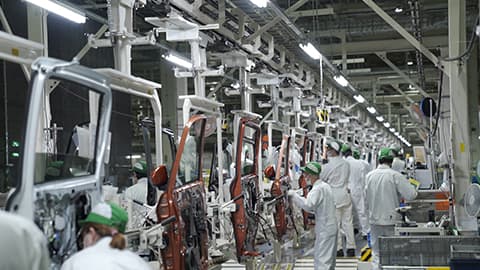
チェンコンベヤシステム「パワー&フリーコンベヤ」
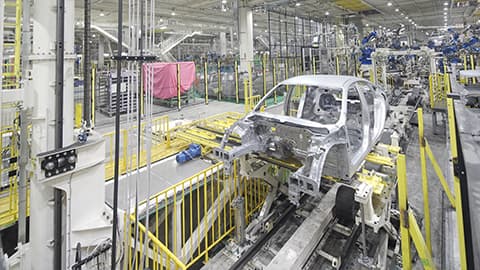
移載機・高さ変更装置
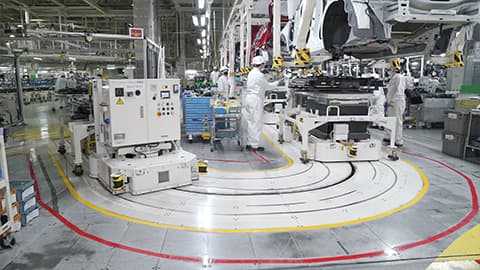
EVバッテリー取り付け装置
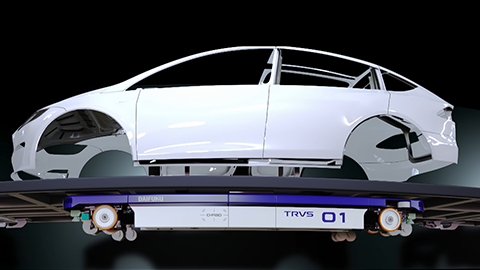
重量級台車けん引AGVシステム「TRVS」
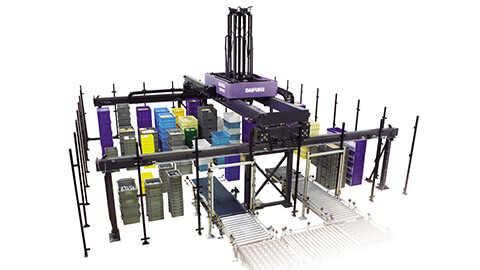
部品用一時保管・仕分けシステム「SPDR®(スパイダー)」
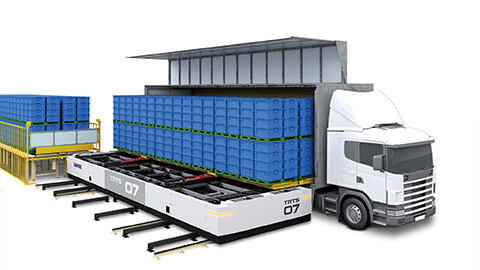
ドライブスルー型トラックステーション「TRTS(トータス)」
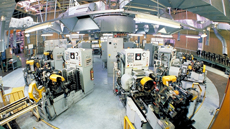
エンジンテストシステム
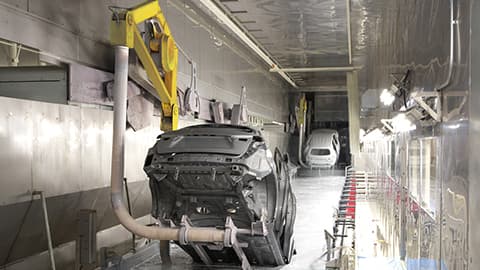
塗装システム「E-DIP®」
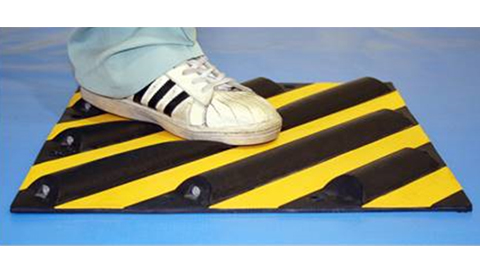
安全マット「ピー太・ピーコ」
製品活用イメージ
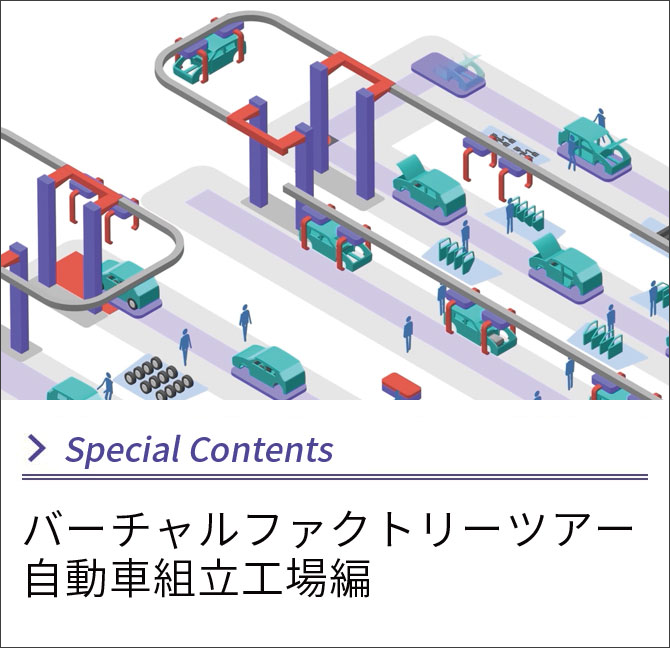
導入事例
お問い合わせ
ソリューションのご相談やお見積もり、
事例についてなど、お気軽に
お問い合わせください。