自動車生産ラインにおける当社、搬送システム技術の変遷
当社は1957年、米国の世界的コンベヤメーカー、ウェブ社(Jervis B Webb International Co.)とチェンコンベヤについて技術提携。同年、その第1号機として「トロリーコンベヤ」(当社商品名、以下同)をトヨタ車体(株)・刈谷工場へ納入しました。この年の自動車生産台数は2年前、1955年の3倍にのぼる18万2,000台。ちょうど自動車メーカー各社が本格生産に突入した時期にあたり、米国の大量生産ラインで活躍していたウェブ式チェンコンベヤの日本における幕開けの年となりました。
日本の自動車産業発展の原動力ともなったウェブ式チェンコンベヤから、現在の主力機種「Newフレキシブルドライブシステム」に至る、自動車生産ラインにおける当社の搬送システム技術の変遷を、主要機種に絞ってご紹介します。
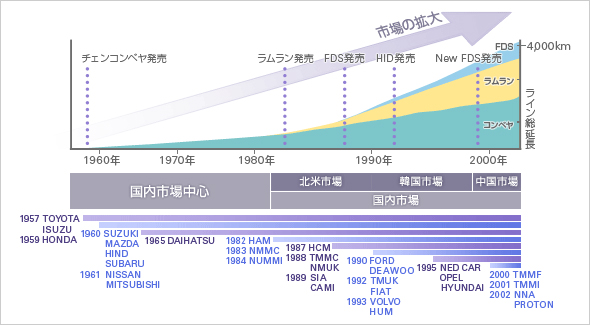
画面を拡大してご覧下さい。
チェンコンベヤシステム
ウェブ社のチェンコンベヤシステムに使用されるチェンは、鍛造で強度が高く、人手で簡単に組み立て・分解できるリベットレス方式が最大の特長。傾斜角度を大きく取ることができ、フレキシブルなレイアウトが可能な軽量物搬送用のUコンベヤチェンと、高い破断強度を持つ重量物搬送用のJX型チェンの2種類に分かれています。また、設置場所によりオーバーヘッドタイプとフロアタイプ、さらに搬送機能によりトロリータイプとダイフクマジックタイプに分かれており、さまざまな搬送条件に対応できるよう工夫されています(図1)。その高度な機能・信頼性は現在でも十分通用するものであり、自動車メーカー各社はもとより、さまざまな業界の搬送システムとして多数採用され実績を重ねてきました。
直吊り搬送のみのトロリータイプのコンベヤに、アキュムレーションなど複雑な搬送ができるよう発展させたのが、ダイフクマジックタイプのコンベヤ(写真1)。1957年、1号機をいすゞ自動車(株)・鶴見製造所のエンジン組立ラインへ納入しました。このコンベヤは従来、組立ラインで一般的に使用されていたローラコンベヤに代わる画期的な方式として注目され、その後の乗用車専用工場新設ラッシュに併せて、受注が活発化していくことになります。
-
図1: チェンコンベヤの種類
-
写真1: ダイフクマジックパワー&フリーコンベヤ(オーバーヘッドタイプ)
1980年代前半、日本車の米国向け輸出が180万台と北米でのシェアが20%を超えたころ、貿易摩擦が表面化し始めました。国内自動車メーカーは相次いで海外進出を表明し、現地生産化に着手。当社も本田技研工業(株)・オハイオ工場や日産自動車(株)・テネシー工場などへ、各種コンベヤシステムを相次ぎ納入しました。一方、この時期、自動車生産台数の増加に伴い生産ラインの自動化が急務となり、産業用ロボット導入が全盛期を迎えました。しかし、産業用ロボットの機敏な動きにチェンコンベヤの能力が伴わず十分な生産効果が得られなかったことから、新しい搬送システムへの要求が出てきました。
そこで1983年、モノレールシステム「ラムラン」を開発(写真2)。同年、トヨタ自動車(株)・元町工場と関東自動車工業(株)・東富士工場へ1・2号機を納入しました。コンピュータ制御による連続・間欠搬送が可能で、高度な自動車生産ラインを構築できることが「ラムラン」の最大の特長。最大搬送速度120m/分、変速範囲1:20などの高性能に加え次のような利点を持っています。
- ロボットだけでなく人手による作業にも対応できる
- 柔軟なレイアウトが組める
- 機能の拡張・縮小が容易
- 音が静かでほこりの発生が少ない
- 美観に優れ快適な労働環境づくりに貢献
ラムランは当時のお客さまのニーズを的確にキャッチ。驚異的な売れ行きを示し、当社の大ヒット商品となりました。さらに、シリーズ機種として開発したリニア誘導モータ搭載の「ラムランリム」も、軽量小物の高速搬送(400m/分)を実現し、仕掛かり台車の削減に貢献しました。
-
写真2: ラムラン(オーバーヘッドタイプ)
-
写真3: フレキシブルドライブシステム(フロアタイプ)
パレット式フレキシブルドライブシステム(Flexible Drive System:FDS)
1988年、スラットコンベヤに代わる方式としてパレット式FDSを開発しました(写真3)。これは、ボディを搭載したパレットをウレタンローラの駆動力で連続的に前進させるコンベヤ。パレット上に作業者も一緒に乗り込んで組立作業が行えるため、従来のスラットコンベヤのように、作業者がラインの動きに合わせて連れ歩く必要や船酔い現象がなくなり、「人に優しい作業環境」を構築できるのが特長です。1号機は同年、関東自動車工業(株)・深浦工場へ納入しました。
非接触給電システム(High Efficiency Inductive Power Distribution Technology:HID)
1993年、ニュージーランドのオークランド大学と共同で世界初の非接触給電システム「HID」を開発。ラムラン(写真4)やパレット式FDSなどの昇降ユニットの給電に採用し、安全・クリーンな労働環境の実現や、メンテナンス費用の大幅削減に効果を挙げました。
従来のトロリー線と集電子を使った接触給電方式には、集電子の磨耗や磨耗粉(粉じん)の発生、さらに離線によるスパーク・騒音発生、感電などの問題がありました。これに対し、HIDは従来のトロリー線に代わる2本の誘導線、集電子に代わるピックアップコイル、および受電ユニットで構成されています(図2)。給電は、電源盤で商用電源を非接触給電に適した周波数に変換して誘導線へ電力を送ることで誘導線の周囲に磁場を発生させ、移動体に電力を効率良く伝達します。
HIDは、関東自動車工業(株)・岩手工場へ納入したラムランに初めて採用されました。その後、同様の搬送システムを米国GMへ納入したことでHID方式が世界中に認知され、今日までに多くのお客さまに利用されています。現在、HIDは自動車工場だけでなく、高度なクリーン環境が要求される半導体・液晶工場のマテハン設備などにも幅広く使用されています。
-
写真4: ラムランHID(オーバーヘッドタイプ)
-
図2: HIDシステムの構成
Newフレキシブルドライブシステム(New FDS)
1999年、パレット式だけだったFDSを能力アップし、オーバーヘッドタイプ、フロアタイプの2機種を追加(写真5)して、New FDSとしてラインアップの充実を図りました。New FDSの利点は、従来のFDSと異なり、フリクション駆動(図3)以外にもチェン駆動やローラ駆動などのドライブ方式を自由に選択できることにあります。例えば、乾燥ラインをチェン駆動、搬送ラインをフリクション駆動にするなど、1本のラインに複数のドライブ方式を採用することで、キャリア同士でのボディ移載が不要になるほか、次のような特長を持っています。
- 搬送速度を1~40m/分(基本スペック)の範囲で自由に設定できる
- キャリア自体には駆動源がないシンプルな構造でメンテナンスが容易。コストパーフォーマンスにも優れている
- ライン制御には省配線ユニットを採用し、工事期間短縮を実現
- フリクション駆動のウレタンローラは、必要な駆動部分のみ稼働。省エネに優れており、騒音もチェンコンベヤに比べ10デシベル以上も少ない
FDSにより、従来のように単一機種で構成するのではなく、必要に応じて最適な駆動方式を選択し、生産ラインの用途にマッチした搬送システムを構築することが可能になりました。なおFDSは、現在、自動車生産ラインで最も多く採用されています。
-
写真5: New FDS(オーバーヘッドタイプ)
-
図3: New FDS(フロアタイプ)のフリクション駆動
終わりに
第2次世界大戦後、日本の自動車メーカーは驚異的な発展を遂げました。1980年代後半には年間生産台数1,100万台を記録。その後、貿易摩擦や円高などを経て海外進出が進み、現在では全世界で生産が行われるようになりました。この間、自動車メーカーの搬送システムへのニーズも、大量生産から自動化システム導入、多車種生産、リードタイム短縮、さらにエコロジー・安全など目まぐるしく変化。当社もそれに合わせたマテハン設備を開発してきました。
近年、自動車業界はいっそう多様化傾向を強めてきており、生産ラインは"多車種混流生産"が主流となっています。また、新車の開発期間も年々短くなり、マテハン設備には納期短縮が厳しく求められています。当社ではこれらのご要望に対して、デジタルエンジニアリングや、世界最適地生産体制の確立など設計・生産の効率化でお応えしています。
関連リンク
自動車生産ライン向けシステムお問い合わせ
ソリューションのご相談やお見積もり、
事例についてなど、お気軽に
お問い合わせください。