Lao Gan Ma
The Automation Behind the Flavor
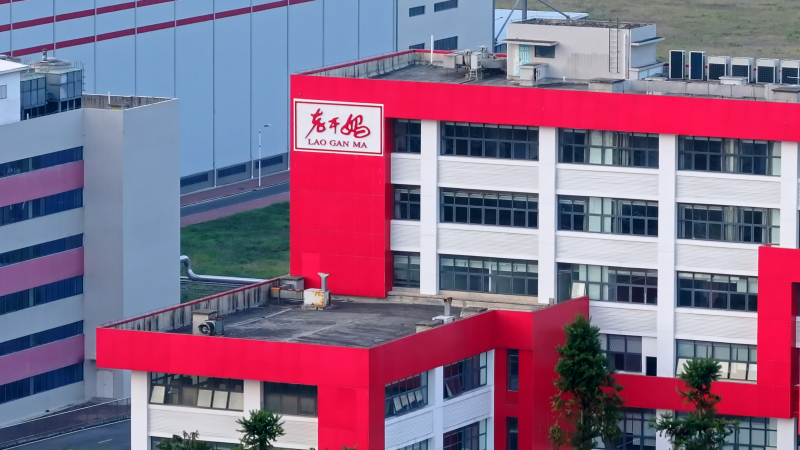
As a flagship Chinese brand, Lao Gan Ma has won the hearts of consumers worldwide with its high-quality chili condiments. With rapid growth in market demand, Lao Gan Ma faced challenges such as low storage efficiency, complex inventory management, and insufficient storage space.
Traditional manual operations and semi-automated processes could no longer meet these needs. To address this, Lao Gan Ma partnered with Daifuku to create an intelligent automated warehouse, significantly enhancing production and storage efficiency while providing a strong basis for future business expansion.
Key features of the Daifuku solution
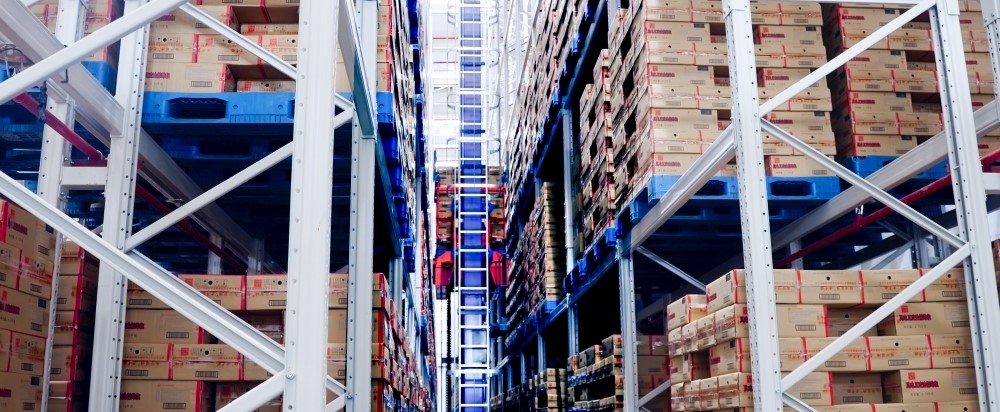
The Daifuku AS/RS system provides 34,164 pallet locations with 12 stacker cranes
Lao Gan Ma's automated warehouse, located in Guiding County, Guizhou Province, began operations in 2020. The solution features an Automated Storage and Retrieval System (AS/RS) with 34,164 pallet locations and 12 pallet stacker cranes, and 9 Sorting Transfer Vehicles (STVs) operating within a loop system with seven vehicles and a dual-shuttle system, ensuring efficient goods handling.
Additionally, the project includes five palletizing robots, a sorting system, and a case and pallet conveyor system connected to the production lines. This setup has achieved end-to-end automation across production, storage and outbound logistics, significantly improving overall operational efficiency.
Smart intralogistics automation
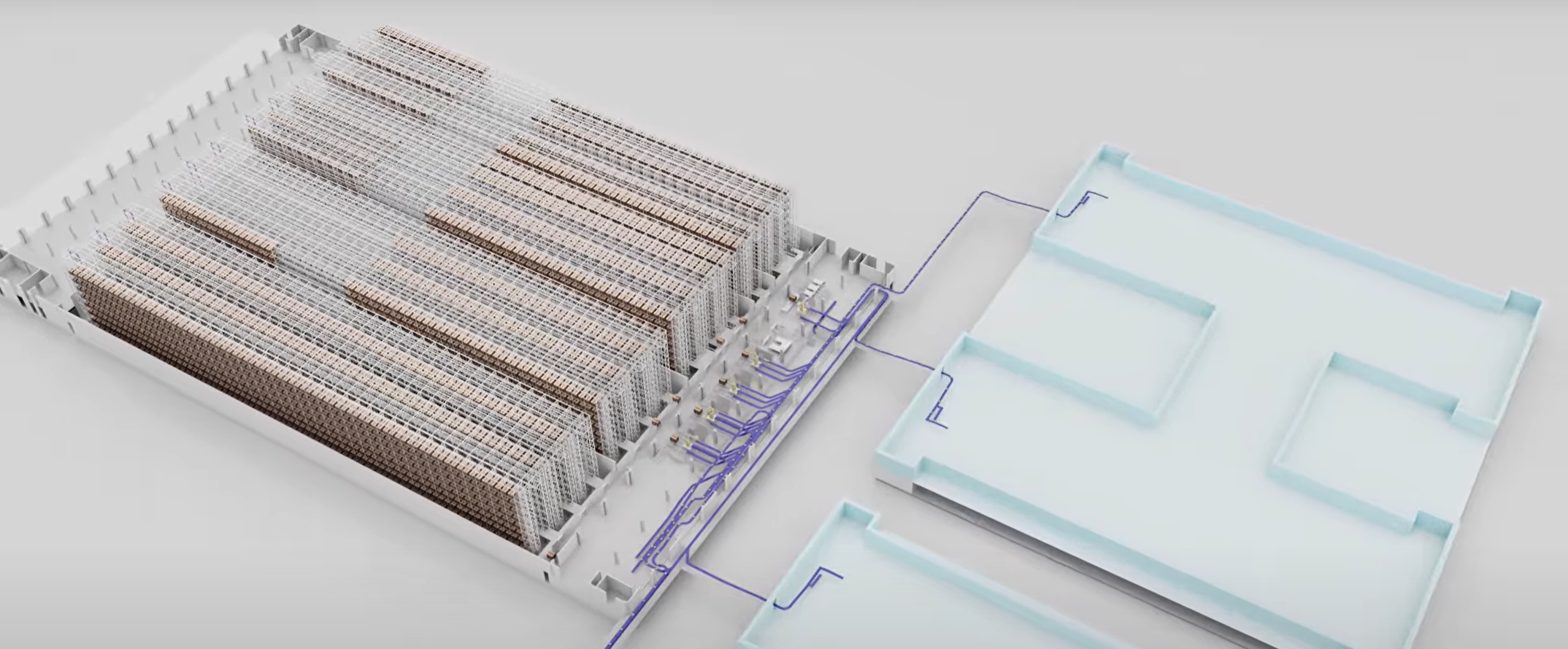
Conveyors leading from the six factory buildings transport cases automated warehouse
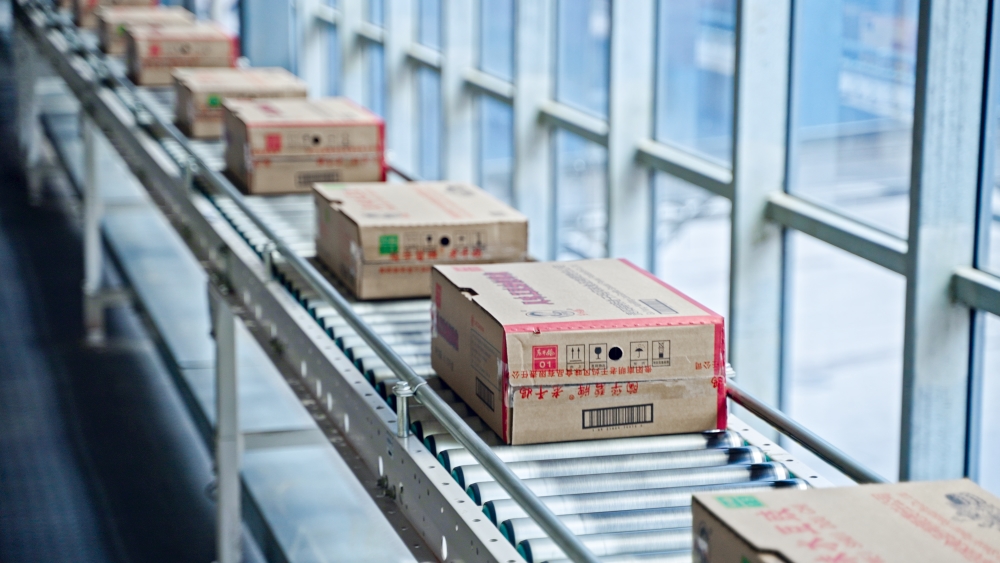
The intralogistics process begins with the connection between the production line and the automated warehouse. Finished products from seven production lines across six manufacturing buildings on the site are transported via the case conveyor system to the front end of the inbound loop. The system then completes the intelligent and efficient intralogistics processes of storage, retrieval, and dispatch through integrated sorting, palletizing, storage, and outbound processes.
- Finished product inbound process
- Finished products are laser-coded and transported by the case conveyor to the sorting area. The slide-shoe sorter accurately sorts goods from different manufacturing buildings to the corresponding palletizing positions. After palletizing, full pallets are transported to the corresponding storage aisles by the pallet conveyor and dual-STV system, and finally stored in the designated storage location in the automated warehouse by the stacker crane.
- Outbound operations
- When the system receives an order, the outbound process rapidly begins. For full pallets, the stacker crane first retrieves the pallets, and then STVs transports them to the outbound area. For product shipping in partial pallets, a goods-to-person picking strategy is used, where pallets are transported to a picking station for case picking operations, further enhancing flexibility and efficiency. The STVs not only transport goods but also recover empty pallets, ensuring the efficient operation of subsequent intralogistics processes.
The slide-shoe sorter rapidly directs cases
STVs automatically transport pallets on site
Palletizing robots are fed automatically via conveyor
Transformation that delivers game-changing results
- Energy saving and cost control
- During the design phase, the Daifuku project team carefully balanced investment, long-term operating costs, and low-carbon development needs. For example, they optimized the path between the production line and the warehouse to the shortest route, effectively reducing energy consumption from multiple turns and corners that would have arisen in the conveyor system. Additionally, optimizing their approach, the team placed the palletizing system at the end, allowing each robot to handle products from multiple production lines simultaneously. This strategy reduced both system carbon emissions and overall investment costs for Lao Gan Ma.
- System stability and efficiency
- Daifuku’s tried-and-tested technology ensures Lao Gan Ma’s 24/7 production needs—an inbound capacity of up to 139 pallets per hour, an outbound capacity of 166 pallets per hour, and a maximum single pallet load capacity of 1.34 tons.
- Intelligent logistics scheduling
- STVs offer great flexibility in outbound intralogistics, supporting sequential and batch outbound operations, as well as the recovery and rapid transportation of empty pallets, greatly improving system operational efficiency. STVs also provide a level of scalability, able to adjust to outbound strategies according to different production needs, ensuring Lao Gan Ma's logistics operations remain efficient.
- Efficient warehouse management system
- The warehouse's WMS (Warehouse Management System) seamlessly connects with the vehicle management system, ensuring that trucks entering Lao Gan Ma’s facility can directly proceed to the designated dock for loading and unloading operations. This system linkage significantly reduces loading wait times and optimizes the outbound logistics process.
Customer's Voice
"Thanks to this project, we've significantly improved production efficiency, saved on labor and energy costs, expanded storage space, and successfully achieved the digital transformation of our factory management."
Looking ahead
The partnership between Lao Gan Ma and Daifuku showcases the synergy between a major national brand and top-tier international automation technology. Lao Gan Ma's automated warehouse project not only supports current operations but also sets the stage for future growth. Moving forward, both parties will continue to explore new opportunities together, ensuring sustained momentum as Lao Gan Ma expands in the global market.
Discover More
To learn more about our operations in China, explore case studies from the region, and stay updated through our local social media channel in the country, visit our Daifuku (China) Manufacturing page.
Contact Us
For product inquiries, please reach out to us via our Contact Us page.
Contact UsContact Us
For product inquiries, please reach out to us via our Contact Us page.
Contact Us