Work-in-Progress Handling
Solving Challenges: Space Shortages, Production Inefficiencies, Labor Shortages, and Workplace Safety
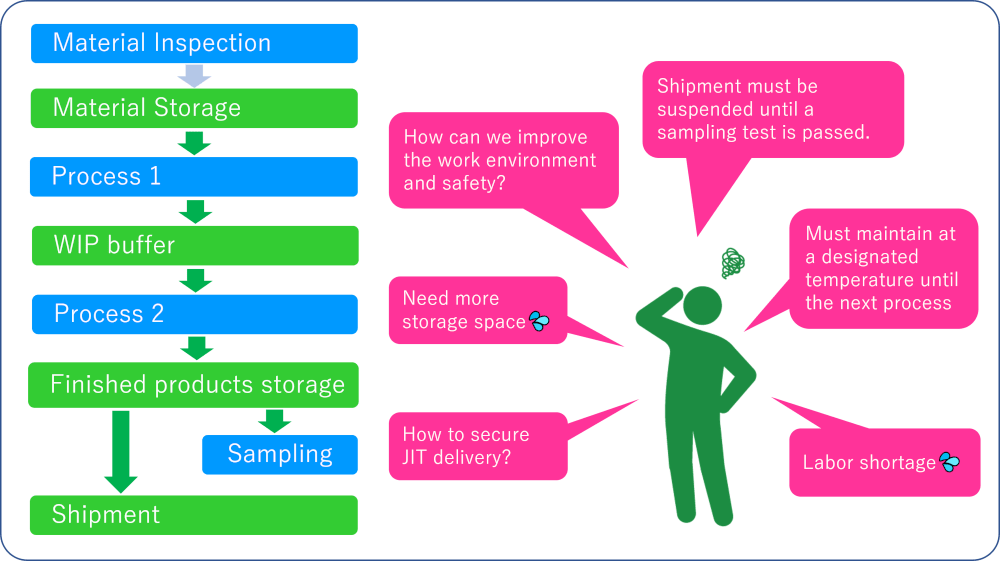
From raw material storage to processing, front-end and back-end processes, through to assembly and inspection, raw materials and works-in-progress (WIPs) on a manufacturing line go through many processes. The just-in-time (JIT) supply―the right goods, at the right time, in the right quantity―of materials and WIPs to each process is key to increasing production efficiency.
Further, with ESG and the SDGs now a social expectation, company efforts toward health and safety in the workplace are increasingly in the spotlight. According to Japan's Ministry of Health, Labor and Welfare, in 2018 there were 2,100 workplace accidents involving forklifts in Japan, of which 31% happened within the manufacturing industry.
Facilities that rely on manual labor and forklifts can face many challenges:
- Insufficient WIP storage space: While WIPs can be stacked directly on the floor, there is a risk of them toppling and are a workplace hazard.
- Front-end and back-end process sequencing: It takes considerable time and effort just to retrieve the necessary items from the storage area where multiple products are mixed.
- Labor shortages: Maintaining a group of forklift operators can be challenging. All companies seek to assign their limited human resources to high-value tasks.
- Safety: Accidents between forklifts and personnel or equipment occur.
Installing an AS/RS as an Inter-Process Buffer Solves Issues of Space, Labor, Safety, and Efficiency
By introducing a buffer system that combines an automated storage and retrieval system (AS/RS) with transport equipment such as shuttle carts or AGVs, it is possible to solve the above four problems and increase operational efficiency and safety.
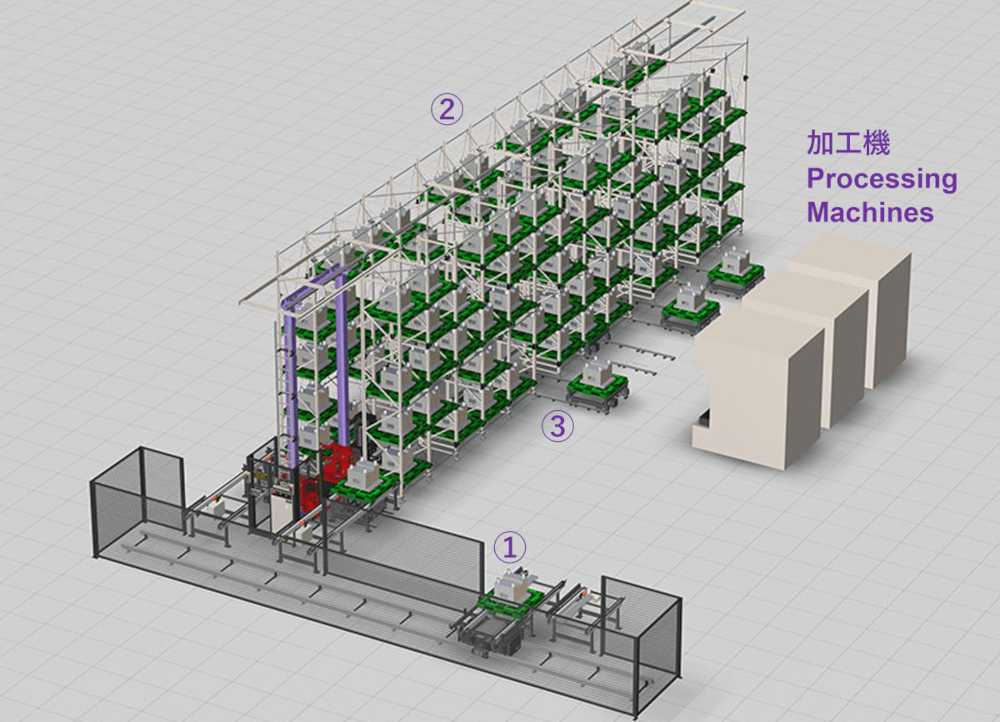
- STVs (1) transport raw materials and WIPs to the AS/RS (2) from the raw material warehouse or previous process.
- In response to a request from the processing side, the AS/RS delivers the required cargo to the self-propelled cart (3).
- AGVs transport raw materials and WIPs to the processing equipment.
- Goods that pass through many processes can be stored in the AS/RS between each process.
-
TRANSPORT: In-process transport equipment
From the raw material warehouse to the front-end and back-end processes, through to the final process and inspection line, an AS/RS connects the processes and automatically supplies the necessary items in the required order and at the required time. Thus removing the need for a large forklift fleet.
-
STORAGE: Building vertically to solve space constraints
When the processing and fabrication speeds of front-end and back-end processes are different, it becomes necessary to store inventory between the two. By installing an AS/RS, it is possible to effectively use the vertical space of the building for temporary buffer storage.
-
SEQUENCE: Receiving WIPs in the right sequence at the required time
Any item stored in an AS/RS can be accessed immediately, allowing for timely supply to the next process. The WMS provides crucial sequencing functions, such as location management, FIFO (first-in/first-out) management, and blocking of outgoing shipment lots that have not yet been inspected.
-
SAFETY: Reducing forklift traffic
Reducing the volume of forklift traffic in the production area improves workplace safety.
Model System
![]() |
Configuration | 2 banks x 14 bays x 5 levels |
---|---|---|
Size | 25 x 4 x 8 meters | |
Floor area | 100 m2 | |
Load size | 1,100 x 1,100 x 1,200 millimeters | |
Load weight | 1,000 kilograms | |
Storage capacity | 132 pallets | |
Equipment | 1x stacker crane 4x shuttle cart 1x I/O conveyor |
Add-ons
-
Dual crane system
If the installation of additional processing equipment is planned in the future, it is possible to increase the transport capacity by extending an AS/RS aisle or adding a stacker crane. The dual crane system can also be operated with only one crane, which is an effective measure against downtime.
-
Automatic guided vehicle (AGV)
Adding an AGV enables the AS/RS to automatically supply processes that are further away.
Typical products
Contact Us
For product inquiries, please reach out to us via our Contact Us page.
Contact UsContact Us
For product inquiries, please reach out to us via our Contact Us page.
Contact Us