Quality Assurance
Daifuku Group Quality Policy
Basic Approach
The Daifuku Group will contribute to the creation of a sustainable society by engaging in sound business practices in accordance with our company creed, management philosophy, and Group Code of Conduct. We will strive to attain greater customer satisfaction and earn the trust of society by pursuing quality and safety in the products and services we provide.
Basic Policy
We will ensure that all Group officers and employees are aware of this policy and work to assure the quality of our products and services.
- Compliance with laws and regulations
- We will comply with all applicable laws and regulations of each country and region governing our products and services, and we will respond appropriately to mandatory standards and norms.
- Building and operating a quality management system
- We will establish a quality management system by clearly defining procedures and setting targets for each process from product development and design to production, installation, and service. The effectiveness of the system will be continuously evaluated and improved.
- Collaborating with suppliers and business partners
- We will make every effort to ensure that our business partners, including contractors and suppliers, understand and implement this policy. By providing guidance and support to business partners as needed, we will strengthen our collaboration and work toward improving quality.
- Quality education and awareness
- We will provide educational and awareness-raising activities relating to the quality and safety of our products and services. We will also share information and expand our initiatives within the Group to further improve quality.
- Information disclosure and communication
- We will accurately and appropriately disclose information regarding the quality and safety of our products and services, and we will use stakeholder feedback for their improvement.
Established: August 31, 2023
Promotion System
In accordance with the ISO 9001 Quality Management System regulated by ISO (International Organization for Standardization), the pursuit of customer satisfaction is our fundamental policy and we guarantee quality at every stage of planning, sales, design, manufacturing, installation, and after-sales service.
We conduct quality management system initiatives based on top management reviews of the quality assurance system, which is linked with feedback from business operation management reviews that evaluate the achievements of each business operation and implement nonconformity corrective measures. In addition, as a company-wide management review, the CEO evaluates and makes judgments on the necessity for changes in the quality management system by reviewing the progress made in achieving our product quality goals with the aim to strive for continuous improvements.
Please enlarge the screen to view
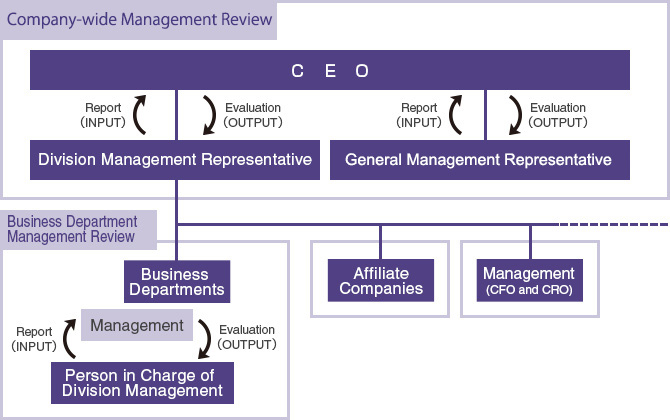
Quality management system certification
We promote ISO 9001 certification, the international standard for quality management systems, at all major production sites within and outside of Japan. All three of our Japan production locations as well as 21 of our production locations outside of Japan have been ISO certified. 89% of our production facilities have obtained certification.
Certification standards | Production sites (consolidated) | Number of certified locations among total | Proportion of certified locations |
---|---|---|---|
ISO 9001 | 27 | 24 | 89% |
Major Initiatives
Response to quality issues
Should a major accident occur with our product, we carry out cross-company measures that incorporate other departments according to the need for detailed accident information by other operational departments and to register the corrective measures taken in a database. Reporting procedures are set out in the ISO Corrective Action and Preventive Measures Procedural Guide. We are thorough in preventing the recurrence of accidents and carrying out preventive measures, and we regularly implement management reviews through the CEO to verify the suitability of the quality management system.
Please enlarge the screen to view
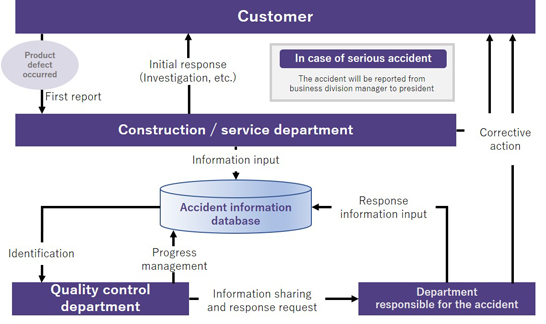
Number of serious accidents* related to product and system safetyKPI
FY2022 | FY2023 | FY2024 | |
---|---|---|---|
Number of serious accidents related to product and system safety | 0 | 0 | 0 |
- *Accidents caused by the malfunction of our products or systems during operations leading to death or serious illness and/or injury (illness or injury requiring 30 days or more of treatment)
Product safety
We conduct risk assessments on all existing and newly developed products to ensure their safe operation. Specifically, we conduct reviews during the design and development process and do advance checks for safety in accordance with the ISO Product Safety Evaluation Procedural Guide and the Development and Standardization Design Implementation Guide, stipulated in the ISO 9001 Management System. In addition, we also promote the training of young designers and the acquisition of external safety assessor* credentials. We also provide assistance to contractors in obtaining these credentials.
- *A person with the basic knowledge and capability required to confirm the adequacy of safety, as well as the ability to judge overall safety adequacy
Hini Arata Kaizen Activities,*1 Kaizen Proposal Activities
At Daifuku, we emphasize improvement (kaizen) activities such as our Hini Arata Kaizen Activities and Kaizen Proposal Activities, and we have made significant achievements by continuously conducting improvements at our work sites. Regarding Kaizen Proposal Activities, there were 3,104 proposals*2 for the improvement of operations, cost reduction, quality, safety, environment, and other matters made in fiscal 2024. The highlight of the Hini Arata Kaizen Activities is a presentation convention held once a year, attended by top management, for teams that pass the preliminary selection round. In fiscal 2024, the convention was held as a hybrid event, both in person and online. 12 teams selected from various divisions in Japan as well as global subsidiaries presented their activities and results, and the convention was streamed live online to the entire Group.
- *1 Hini Arata Kaizen Activities is the new name for the Small Group Activities that have been held in the past, effective fiscal 2025
- *2 Due to the change in business term (the end of the financial year), the period for fiscal 2024 activities was the 9-month period from April through December