Sorting Transfer Vehicle (STV)
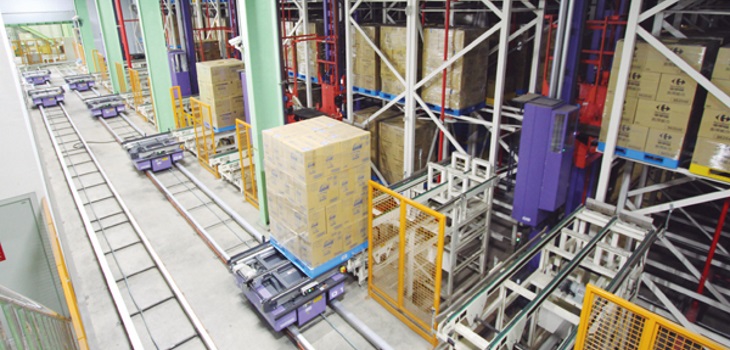
Daifuku's Sorting Transfer Vehicle (STV) is a pallet sorting system that employs rail-guided vehicles for swift and efficient material handling. Designed to integrate seamlessly with Automated Storage and Retrieval Systems (AS/RSs), the STV ensures high-throughput operations. It facilitates sorting onto conveyors linked to an STV line or loop, optimizing warehousing tasks such as transferring goods between automated warehouse aisles, order picking stations, and sorting based on shipping directions. Additionally, a freezer model is available, catering specifically to cold chain automation and warehousing needs.
Features
High Throughput
The STV operates smoothly and quietly, capable of reaching a maximum travel speed of 200 m/min and transferring loads at 30 m/min. Each vehicle's speed adjusts automatically based on its position and the availability of goods—whether loaded or unloaded. In loop and dual systems featuring multiple vehicles, the controller optimizes vehicle allocation to minimize redundant movements and energy consumption, thereby enhancing overall system efficiency.
Flexible
Available in Single Shuttle, Dual Shuttle, or Loop configurations, the STV system is adaptable to various building layouts and transport volume requirements. It offers high scalability, allowing easy expansion to accommodate changes in business needs, such as extending rails for additional automated warehouses or increasing the number of vehicles to enhance throughput.
Reliable
In traditional conveyor-based transport systems, physical movement of pallets on the conveyor can lead to operational issues depending on pallet quality. In contrast, the STV system operates with vehicles traveling on rails, ensuring smooth and stable transport of goods. Furthermore, maintenance work, except for the single shuttle system, can be conducted while the system remains operational, minimizing downtime.
Layout Variations
We offer three types of systems tailored to accommodate varying business volumes and operational needs.
Single Shuttle System
A single vehicle travels along a straight rail to transport loads, eliminating the need for forklift operators to traverse the entire warehouse, thereby enhancing operational efficiency.
The straight rail can also be configured with a 90° curved rail to create an L-shaped layout. This setup is particularly effective in buildings with complex layouts or where production equipment placement necessitates non-linear configurations.
Dual Shuttle System
This system features two vehicles operating on straight rails simultaneously, increasing throughput by 1.5 times compared to a single shuttle system.
It includes the capability to isolate one vehicle for maintenance or evacuation purposes, ensuring operational continuity in case of vehicle failure.
Multi-Vehicle Loop System
In this configuration, multiple vehicles operate on a loop rail system comprising straight and U-shaped curved rails. Each vehicle can handle loads concurrently, significantly boosting processing capacity over shuttle systems.
To accommodate future increases in workload, additional vehicles can be seamlessly integrated into the loop. The loop design can also be expanded to support additional cranes in automated warehouses, making it highly adaptable for expanding businesses.
During vehicle maintenance, affected units can be safely moved to maintenance stations outside the loop, allowing uninterrupted operation with the remaining vehicles.
Vehicle Variations
We provide the most suitable vehicles tailored to accommodate the shape and weight of the goods being transported, the strength of the pallets, and the specific installation environment.
Double-chain conveyor
Triple-chain conveyor
Roller conveyor
Cold-resistant STV designed for operations in environments as cold as -30°C, ideal for efficient conveying and sorting in cold warehouses.
Applications
Supply of raw materials and packaging materials from the warehouse to the production line
Transfer of work in progress between processes
Transfer of finished goods from production lines to AS/RS
Supply and collection of pallets for case picking robots
Sorting of products by shipping truck
Manpower saving in cold storage
Case Study
Contact Us
For product inquiries, please reach out to us via our Contact Us page.
Contact UsContact Us
For product inquiries, please reach out to us via our Contact Us page.
Contact Us