AS/RS Applications and Benefits
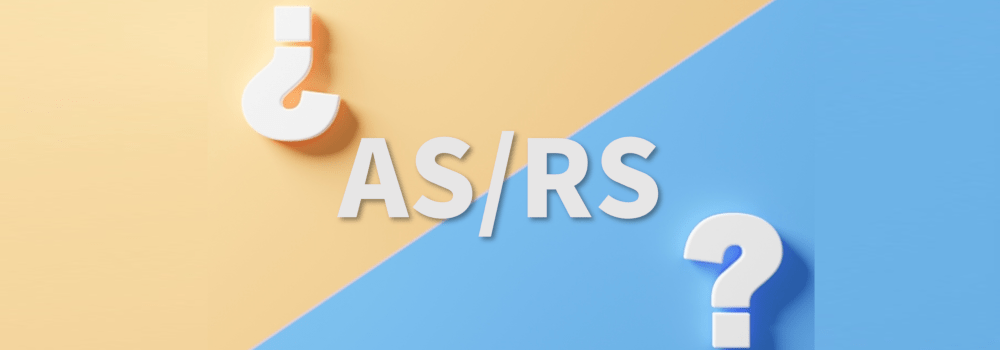
AS/RSs (automated storage and retrieval systems) are computer-controlled warehouses, or automated warehouses, in which automated cranes or shuttle vehicles automatically transport, store, and sort pallets loaded with raw materials, containers with parts, cardboard cases of products, and various other cargo onto shelves and racks. In addition to making effective use of vertical space, AS/RSs promote labor and workforce savings and improve inventory control accuracy. They are used in a variety of processes, from work-in-progress and finished goods storage in the manufacturing industry to inventory storage and sortation in the distribution industry. AS/RSs combined with robots for high-level automation are now the typical equipment driving digital transformation in the logistics sector.
- 1. Benefits of an AS/RS
- 2. AS/RS Applications
- 3. Types of Carrier Device in an AS/RS
- 4. Automated Warehouse Rack Structures
- 5. AS/RS Environments
- 6. Unit Load AS/RS Configurations
- 7. Mini Load AS/RS Configurations
- 8. Earthquake Countermeasures
- 9. Material Handling Terminology
- 10. Useful Life of an AS/RS
- 11. AS/RS upkeep and maintenance
1. Benefits of an AS/RS
Whether you are in manufacturing, retail, e-commerce, or 3PL, AS/RSs can deliver a range of benefits to your operations.
- Effective use of unused vertical space
- Increased inventory storage density
- Increased throughput
- Increased order picking accuracy
- Improved ergonomics, safety, and working environment
- Improved product security
- Reduced labor costs
- Fewer labor constraints linked with labor shortages
2. AS/RS Applications
There are various AS/RS applications in both the manufacturing and distribution industries.
Manufacturing
- Raw material storage
- Parts storage and supply to assembly lines
- Work-in-progress buffer
- Aging-process management
- Finished product storage
- Improved product security
- Production tool storage such as dies and molds
- Service parts storage and order preparation
Distribution
- A temporary buffer of received products from suppliers
- Automatic inventory supply to order picking lines
- Sequencing or grouping of shipping items
3. Types of Carrier Device in an AS/RS
Automated warehouses are composed of racks for storing goods, conveyors that interface with forklifts and peripheral equipment, and devices that transport goods between the conveyors and rack bays. Conveying devices can be broadly classified into two types.
The most common type is called the stacker crane. The stacker crane, anywhere from 5 to 40 meters high, runs back and forth on a lower rail fixed to the floor and an upper rail attached to the top of the rack, while simultaneously lifting and lowering the carriage section that carries the load. Upon arrival at the desired rack bay, a fork on the carriage is inserted into the bay to scoop up or unload the item.
There are two types of automated warehouses: unit load automated warehouses for heavy loads such as raw materials and molds loaded onto pallets, and mini load automated warehouses for light loads such as plastic containers, corrugated boxes, and trays.
The second most common type, and growing in number globally in recent years, is the shuttle vehicle. Shuttle-based systems come in numerous variations, such as those consisting of a conveyor, lifter, and shuttle vehicle; those in which the cart travels in all directions (3-dimensional movement) inside the rack; and those in which the cart travels in all directions on top of a structural grid. Shuttle systems for pallet storage are typically used for high-density storage of large-lot products such as beverages, while those for case storage are often used for pre-shipment sorting in the distribution industry.
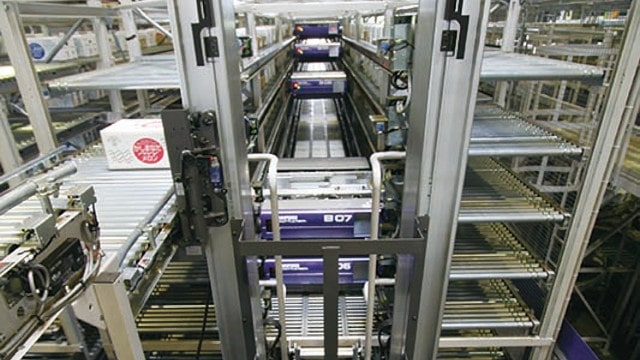
Mini load shuttle AS/RS
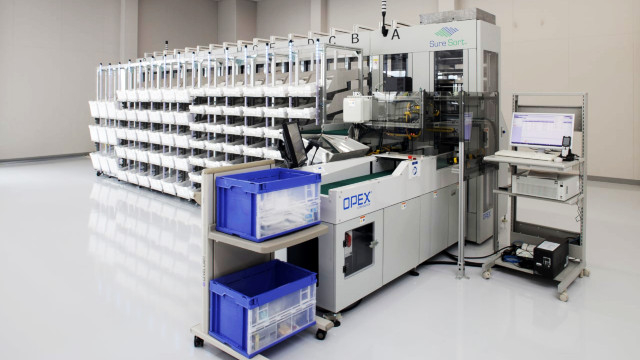
3D mini load shuttle AS/RS
4. Automated Warehouse Rack Structures
There are two types of racking structures used with automated warehouses for pallets: (1) free standing rack AS/RSs and (2) rack-supported building AS/RSs, also known as automated clad-rack AS/RSs.
- Free-standing rack AS/RS: The rack is installed separately from the roof and walls of the building – it is a free-standing structure. This is the most common type as it can be installed in either existing or new buildings.
- Rack-supported building AS/RS: In this instance the rack functions as the structural support for the building’s walls and roof. Rack-supported building AS/RSs are typically used in large-scale warehouses holding tens of thousands of pallets. As it is subject to building regulations as a building, the planning process requires the participation of architects who understand both the automated warehouse and the building regulations of the country where the warehouse will be installed.
Mini load automated warehouses are rarely done as rack-supported building AS/RSs because the racking strength is typically not suitable as a building frame. As a result, free-standing racks are the norm. Two types are widely used: open face and shelving. The applied type is selected according to the stored items and the type of crane or shuttle vehicle required.
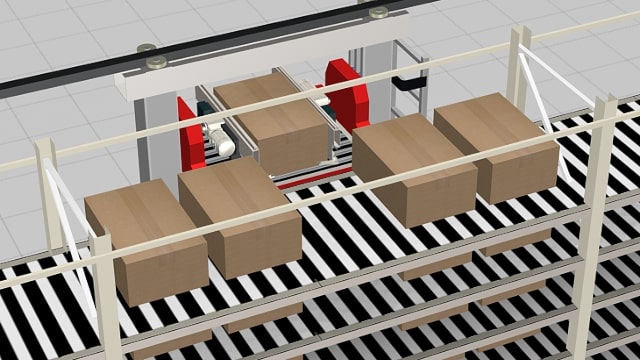
Shelving rack for mini load AS/RSs
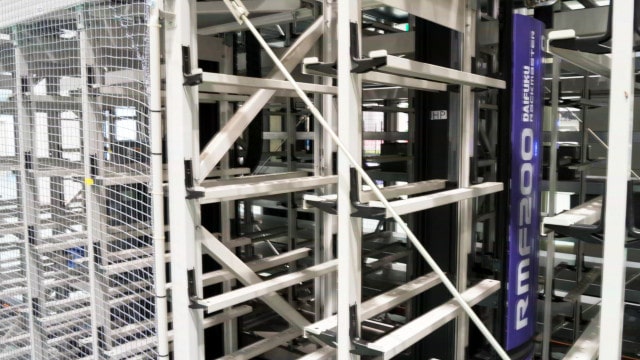
Open-face rack for mini load AS/RSs
5. AS/RS Environments
Since Japan's first cold storage unit load AS/RS went into operation in 1973, automated warehouses have been installed in numerous frozen and refrigerated warehouses. Traditionally, automated pallet warehouses have been the main type of automated warehouses. However, in recent years, the number of cold storage mini load AS/RSs has been increasing in response to the growing need for high-mix, low-volume distribution and heightened awareness of the need to improve working environments.
The second most common type, and growing in number globally in recent years, is the shuttle vehicle. Shuttle-based systems come in numerous variations, such as those consisting of a conveyor, lifter, and shuttle vehicle; those in which the cart travels in all directions (three-dimensional movement) inside the rack; and those in which the cart travels in all directions on top of a structural grid. Shuttle systems for pallet storage are typically used for high-density storage of large-lot products such as beverages, while those for case storage are often used for pre-shipment sorting in the distribution industry.
6. Unit Load AS/RS Configurations
Automated pallet warehouses are available in a variety of system configurations, depending on the warehousing capacity, storage efficiency, and lot size.
- Single deep: This is the most common configuration in which one stacker crane accesses a total of two rows of racks, one on each side.
- Double deep: One stacker crane accesses two rows of shelves on each side, for a total of four rows. Since this configuration has higher storage efficiency than the single deep configuration, it is used in systems with large lots and where storage efficiency is important, such as refrigerated warehouses and manufacturers' finished goods warehouses.
- Dual cranes: Two cranes are installed in one aisle, providing approximately 1.5 times the storage and retrieval capacity compared to single deep. This system is employed when high capacity is required, such as automatic replenishment of picking rack inventory, or when cargo is long or heavy and crane speed cannot be increased.
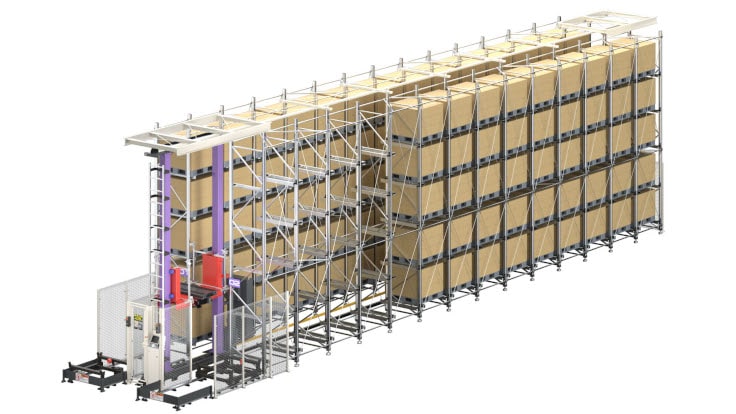
Single deep
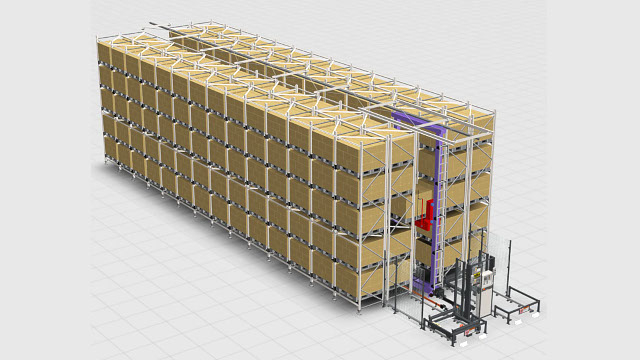
Double deep
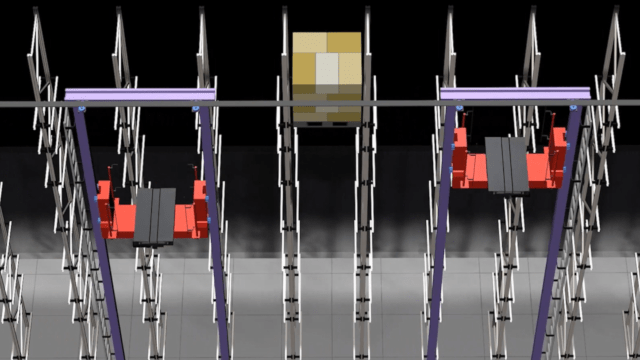
Dual crane
7. Mini Load AS/RS Configurations
Mini load automated warehouses are also available in a range of configurations, with transfer devices selected according to the shape and size of cargo, such as those that scoop up plastic containers like Euro containers, those that directly grab rolls of paper and film, and those that grab corrugated boxes of various sizes. There are also types that mount two transfer devices on the carriage to increase throughput and simultaneously load and unload two items. Double-deep types that increase storage efficiency are also available.
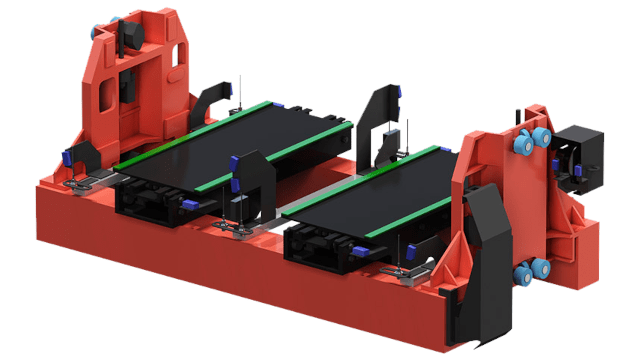
Fork extractor
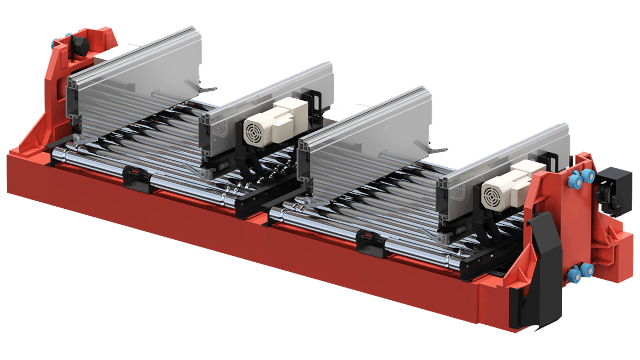
Side clamp extractor
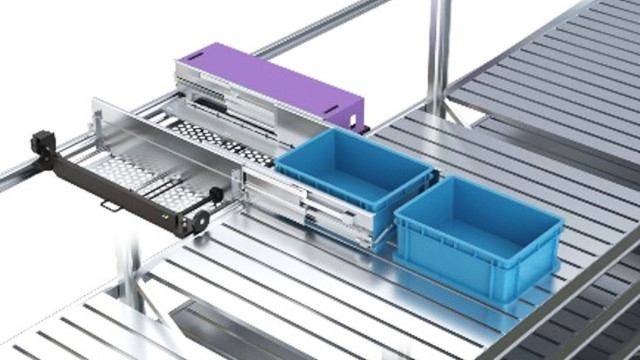
Double deep extractor
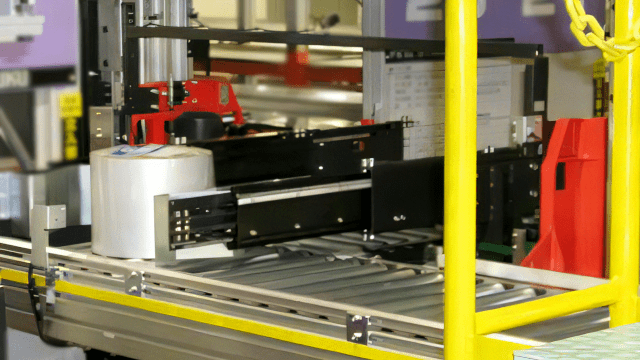
Roll clamp extractor
8. Earthquake Countermeasures
AS/RSs can be tall systems, sometimes as tall as 40 meters, making some people ask whether these systems can withstand earthquakes. In Japan, where earthquakes are common, even during major earthquakes there have been almost no reports of damage to automated warehouse structures designed and constructed in compliance with laws and regulations. On the other hand, there are various countermeasures available to address the problems that prevent the re-operation of warehouses after the earthquake subsides. For more information, please visit our AS/RS Earthquake Countermeasures page.
9. Material Handling Terminology
Like many other industries, the material handling industry too has its own terminologies.
Europe
European Materials Handling Federation (Fédération Européenne de la Manutention, FEM), a non-profit trade association consisting of EU, Switzerland and Turkey, is producing the technical recommendations on the use and maintenance of the various categories of material handling equipment. FEM 9.101 document provides a general overview and terminologies of the storage and retrieval machine (SRM) and related topics.
U.S.
The MHI Glossaryprovides over 600 material handling and supply chain definitions, acronyms, and terms. MHI is the U.S. trade association for the material handling, logistics and supply chain industry and organizes the ProMat and Modex shows.
Japan
The Japanese industrial standard JIS B8941 defines terminology for automated warehouse systems and much of that terminology is used in material handling manufacturer glossaries.
10. Useful Life of an AS/RS
Japan
Material handling systems such as automated warehouses, mobile racks, and sorters are considered depreciable assets under the Japanese accounting system, and the National Tax Agency's guidelines for the useful life of depreciable assets are approximately 8 to 12 years. However, useful life does not equal the life of the equipment. With regular inspections, maintenance, and retrofits, the equipment can be used for 20 to 30 years. For more information, please visit out Retrofit Solutions page.
11. AS/RS upkeep and maintenance
An AS/RS brings significant benefits. But like any working equipment, inspections and maintenance are key to ensuring that the system consistently works at maximum efficiency throughout its operational life. The wearing-down of consumable parts or malfunctions in inventory control computers can lead to delays in shipping operations. For this reason, automated warehouse manufacturers offer a maintenance menu that includes periodic inspections and computer system maintenance.
New technologies are always being developed in the material handling industry, so what we have described here is not all there is. If you are interested in learning more about automated warehousing, please contact us.
Contact Us
For product inquiries, please reach out to us via our Contact Us page.
Contact UsContact Us
For product inquiries, please reach out to us via our Contact Us page.
Contact Us