Occupational Safety and Health
Basic Approach
Safety is the foundation of our business activities and supersedes all else—this slogan underpins our belief that establishing a corporate culture that prioritizes the safety and health of all workers, including temporary workers, contractors, and suppliers, in each workplace is indispensable for sound business activities. The Daifuku Group has obtained the occupational safety and health management system certification (ISO 45001) at all its major sites. We are committed to continuing our safety culture and striving for total safety at our workplaces by identifying all potential risks.
Group Code of Conduct (extract)
2. Safety and health
- We will place safety as a top priority in all of our business activities.
- We will develop and provide safe, high-quality products and services.
- We will strive to maintain and increase the health and well-being of our employees as well as provide comfortable and clean workplaces.
Safety Policy
- Safety slogan
Safety is the foundation of our business activities and supersedes all else. - Safety target
Through a Safety First*1 mindset, eliminate occupational accidents resulting in lost time and traffic accidents. - Safety policy
- Develop and support safety and health activities in which all employees*2 participate.
- Promptly adopt revisions to the Industrial Safety and Health Act and other related laws and regulations.
- Operate the PDCA cycle of the Occupational Safety and Health Management System (ISO 45001) to manage risks and continuously improve safety.
- Establish an education system for safety and health management and expand it throughout the company.
- Utilize and implement new DX and IoT technologies.
- Apply past disaster case studies to eliminate similar disasters.
- Expand support for autonomous safety and health management activities at partner companies.*3
- *1The Japanese term Anzen Senichi (Safety First) is a registered trademark of Furukawa Co., Ltd.
- *2“All employees” includes temporary workers, contractors, and suppliers.
- *3“Partner companies” refers to temporary staffing agencies, contractors, and suppliers.
Supply chain management grounded in law
When embarking on product or system installation, we ensure compliance with the provision in the Construction Business Act that states, “the parties to a contract for construction work shall conclude the contract fairly based on agreements made on terms of equality and shall fulfill the contract honestly and in good faith,” and we strive to ensure that both the safety and health of workers are not harmed as stipulated in the Industrial Safety and Health Act.
Further, we engage in transactions with suppliers applicable under the Subcontractor Act in the spirit of the law, while also making known and requesting cooperation with the Group’s Code of Conduct and CSR Procurement Standards to build appropriate relations with our suppliers.
Promotion System
We at the Daifuku Group place the greatest priority on the safety of all employees, contractors, and suppliers who work at our global locations. In order to eradicate occupational accidents, the Group has established the Central Safety and Health Committee under the direct control of the CEO. Subsidiaries outside of Japan also participate in the Central Safety and Health Committee and provide status reports and exchange information on a quarterly basis. Regional committees for safety and health as well as various specialized committees (installation, manufacturing, and procurement) have been set up under this Committee to ensure safety at all Group companies and establish health management systems throughout the Group.
Additionally, having experienced serious accidents in the past, we now hold the Safety Cooperation Association and the Management and Safety Policy and Production Trends Presentation for suppliers to participate in. Through these efforts to share information, we are aiming to strengthen ties with our suppliers and achieve safety based on mutual awareness and education.
Please enlarge the screen to view
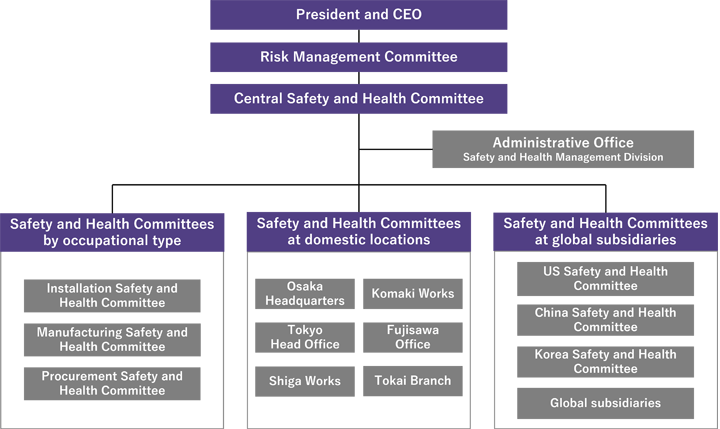
Implementing audits of the safety management system
We carry out annual internal audits based on ISO 45001 standards at our main locations, and we verify the efficacy of our management system and the state of safety activities at our workplaces with inspections by the top management, including the CEO. Further, we also undergo a yearly audit by an external certifying body, as we maintain and expand the scope of our certification.
Occupational health and safety management system certification
We promote ISO 45001 certification, the international standard for occupational health and safety management systems, at all major production sites within and outside of Japan. Two of our production sites in Japan and ten of our production sites outside of Japan have obtained this certification. The ISO certification rate for our production sites is 46%.
Certification standards | Production sites (consolidated) |
Number of certified locations among total | Proportion of certified locations |
---|---|---|---|
ISO 45001, etc. | 26 | 12 | 46% |
Major Initiatives
Safety indicatorsKPI
The Group uses accident frequency rate and severity rate as safety management indicators. We share this information and provide appropriate guidance and safety awareness training to departments that need to improve their safety measures. We are working toward zero fatal accidents.
In fiscal 2023 in Japan, the number of injuries resulting in lost time increased by one compared to the previous year, and targets for frequency and severity rates were not met. Outside of Japan, there was a significant reduction in the number of accidents, and our targets were achieved.
For each accident that occurs, we analyze the cause, create and disseminate new work plans, and eliminate unsafe actions and conditions. Additionally, beginning in fiscal 2023, we implemented an occupational accident management system throughout the entire Group, including subsidiaries outside of Japan. Information on occupational accidents that occur both within and outside of Japan as well as materials for safety and health training are shared in real time in order to ensure that measures are taken to prevent recurrence and to further strengthen safety training.
For the following indicators, contractors in installation are included in calculations and target management.
Frequency rate: The number of casualties per one million employee-hours worked at bases and companies. This rate indicates the frequency of accidents.
Severity rate: The number of lost work days experienced per 1,000 work hours. This rate indicates the severity of accidents.
Indicator*1 | Scope | FY2021 | FY2022 | FY2023 |
---|---|---|---|---|
Frequency rate | Japan | 0.21 | 0.45 | 0.551 |
Outside of Japan | 0.65 | 0.90 | 0.580 | |
All industries in Japan*2 | 2.09 | 2.06 | 2.14 | |
Severity rate | Japan | 0.002 | 0.006 | 0.016 |
Outside of Japan | 0.009 | 0.216 | 0.011 | |
Number of serious accidents*3 | Japan | 0 | 0 | 0 |
Outside of Japan | 0 | 1 | 0 |
- *1Data for the period from January to December. These indicators are calculated including installation contractors.
- *2Provided by the Ministry of Health, Labour and Welfare
- *3Accidental deaths occurring during work at Daifuku (occupational accidents)
Risk assessment of workplace safety and health
The Group conducts risk assessments in accordance with our own standards based on ISO 45001. We identify and manage risks that have a significant impact on safety and health, and we consider and implement risk mitigation measures according to the level of risk. The scope of application covers regular and irregular activities in our business operations, as well as the activities of all persons entering and leaving our premises. Risks are identified and assessed at the beginning of each fiscal year, during the construction planning stage of new projects, as well as any time circumstances change, such as when new processes are introduced or new materials are used.
Disaster preparedness drills
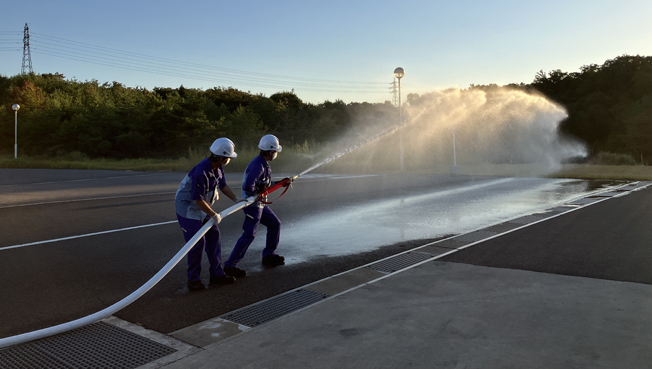
We conduct disaster preparedness drills at our major sites in Japan at least once a year to simulate a large-scale disaster. Based on the initial response manual, we conduct drills for evacuation assistance, reporting, initial firefighting, first aid, and shutting down equipment in the event of an emergency, thereby confirming procedures for a rapid response in the event of a disaster. Group sites outside of Japan also conduct similar disaster drills in accordance with the laws and regulations of their respective countries and regions.
Response to occupational accidents
We have established a BCP promotion system, and when a work-related accident occurs, the disaster and accident reporting route used at all Group companies is followed to report the situation to the CEO from the workplace involved. Additionally, the department involved and the Safety Promotion Department conduct a joint investigation and analysis of the accident, and report the results to the Safety and Health Committee of all companies.
Please enlarge the screen to view
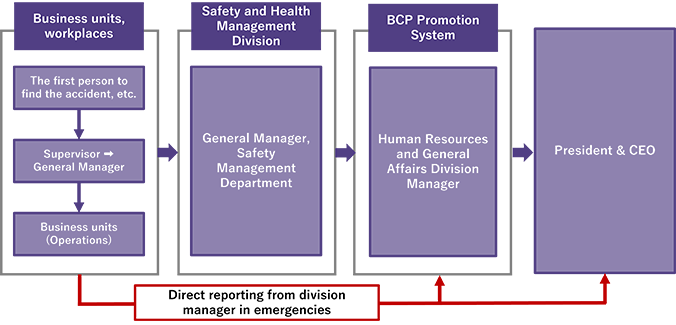
Safety and health training
In addition to training at the time of employment, the Group periodically conducts the following training programs to maintain and improve the safety and health knowledge and skills of its employees.
Safety training program
Skill, awareness, and knowledge are necessary to work safely. External organizations are brought in to provide technical workshops, and special training is offered externally each year to build awareness and knowledge. We focus on in-house training that can be immediately put into practice in the workplace and provide special training that includes crane operation, low-voltage work, full harness work, and particulate matter control.
Safety training facility
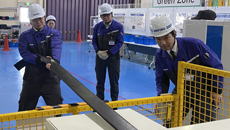
At the Safety Simulation Center at Shiga Works, we cultivate human resources with a high awareness of safety and the ability to take appropriate actions through yearly programs that simulate the real-life dangers of production, installation, and operations. The training is for not only our employees, but also for temporary workers and contractors.
Simulation-based hazard training
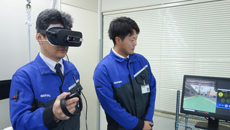
Simulation-based hazard training aims to raise the safety awareness of each employee and make up for any lack of workplace experience by simulating dangerous situations so that employees can viscerally experience them as direct and real threats to their workplace safety. We have started using virtual reality (VR) to also visually recreate the dangerous processes leading to occupational accidents that were difficult to simulate using existing equipment. We are using auxiliary devices that enable employees to experience the simulated shock and sensations felt during an accident.
Safety training worldwide
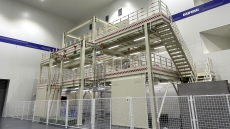
The newly established safety
training facility at Daifuku
(Suzhou) Cleanroom Automation
Co., Ltd.
The same as in Japan, we conduct annual training for supervisors in installation departments at Group companies. This training focuses on the importance of safety management, methods, risk assessment, and work safety standards and aims to raise the standards of safety management. Training facilities that simulate dangerous situations have also been installed at some of our global subsidiaries in China, South Korea, Indonesia, and North America.
Spreading understanding of our daily safety and health standards
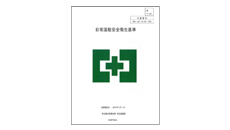
Based on the principle that understanding and practicing proper conduct every day will help prevent occupational and traffic accidents, we implement yearly e-learning programs to enhance employee familiarity with our daily safety and health standards. In fiscal 2023, these programs were held three times for all employees in Japan, and the participation rate for each session was 100%. We will continue these efforts to make sure that all employees have acquired the necessary knowledge about safety and health to prevent occupational and traffic accidents.
Health training (courses for emergency first aid and AEDs)
In order to properly administer first aid in the event of an emergency, it is essential to learn and acquire first aid knowledge and skills regularly. At our major locations in Japan, we are working to make sure that at least 20% of the personnel in each building or area is adequately trained.
Safety activities
Working with contractors and suppliers
The safety initiatives of our Group are not limited to our own employees, but are also developed in cooperation with our contractors and suppliers. We apply our ISO 45001-based safety standards to all workers who enter and leave our premises, and we provide assistance in advancing contractors’ safety activities.
Safety audits
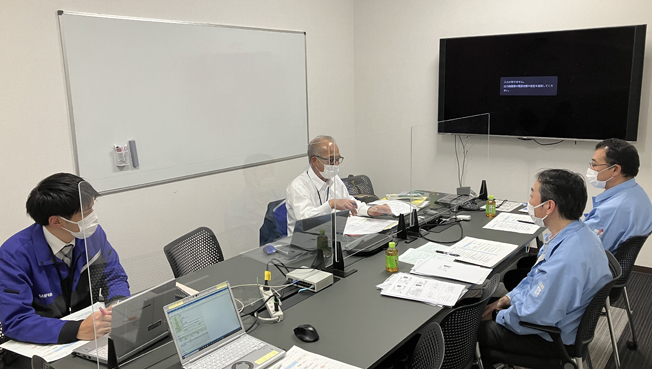
We monitor the safety and health conditions at the workplaces of our contractors and suppliers through visits and surveys. Depending on the results, we visit them again to reassess the situation and provide advice on how to resolve any issues.
Information sharing
We regularly conduct safety and health training for manufacturing and installation personnel, including those from contractors and suppliers. As part of this training, we share information on any changes in laws and regulations related to safety and health as well as on occupational accidents that have occurred in the workplaces of our Group and other contractors and suppliers.
Safety seminars for suppliers
Each year, we hold a Management and Safety Policy and Production Trends Presentation for the top management at our suppliers. At this presentation, we strive to foster safety awareness by informing our suppliers of the safety policies of each of our business divisions as well as presenting awards from specialized committees (installation, manufacturing, and procurement) to suppliers who have actively implemented safety and health initiatives. In fiscal 2023, we invited 311 companies to attend.
Strengthening global collaboration
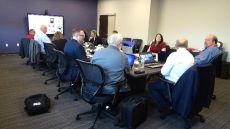
Meeting in North America
In order to strengthen safety and health management throughout the Group, we publish a global safety newsletter that introduces the initiatives of each company, including global subsidiaries, as well as share information at the Global Sustainability Meeting, which is attended by supervisors of each global company. In 2023, the Safety and Health Management Division visited our subsidiary in Michigan, U.S.A., and participated in a meeting along with managers responsible for safety at the five Group companies in the U.S.A. During the meeting, the participants shared their initiatives for and challenges regarding reducing occupational accidents at each of their companies and deepened their mutual understanding of safety and health management. We will continue to promote the fortification of cooperation throughout the entire Group in an effort to facilitate Group-wide safety and health management.
Preventing traffic accidents
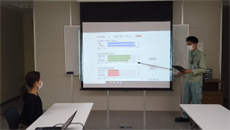
We are taking physical measures to eliminate traffic accidents in company cars. Specifically, the mandatory installation of autonomous emergency brakes (AEB), back monitors, rear corner sensors, and telematics drive recorders in our entire fleet of around 900 company cars. Moreover, when employees are approved to drive company cars, they are tested to a certain standard to determine their driving skills, thereby boosting their driving manners and safety awareness.
Safety and health patrols and exemplary workplace awards
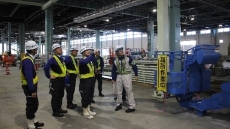
A safety and health patrol
by the president
In order to improve the level of safety and health in the workplace, we conduct safety and health patrols to confirm the 5Ss* at each workplace. In addition, we have been expanding positive examples to other workplaces through the Safety and Health Committee, and in fiscal 2023 we again recognized the most exemplary workplaces. These activities will foster a culture of safety and create safe and pleasant workplaces throughout the company.
- *Sort, set in order, shine, standardize, sustain