Kagetsudo
Product storage system directly connected to production lines
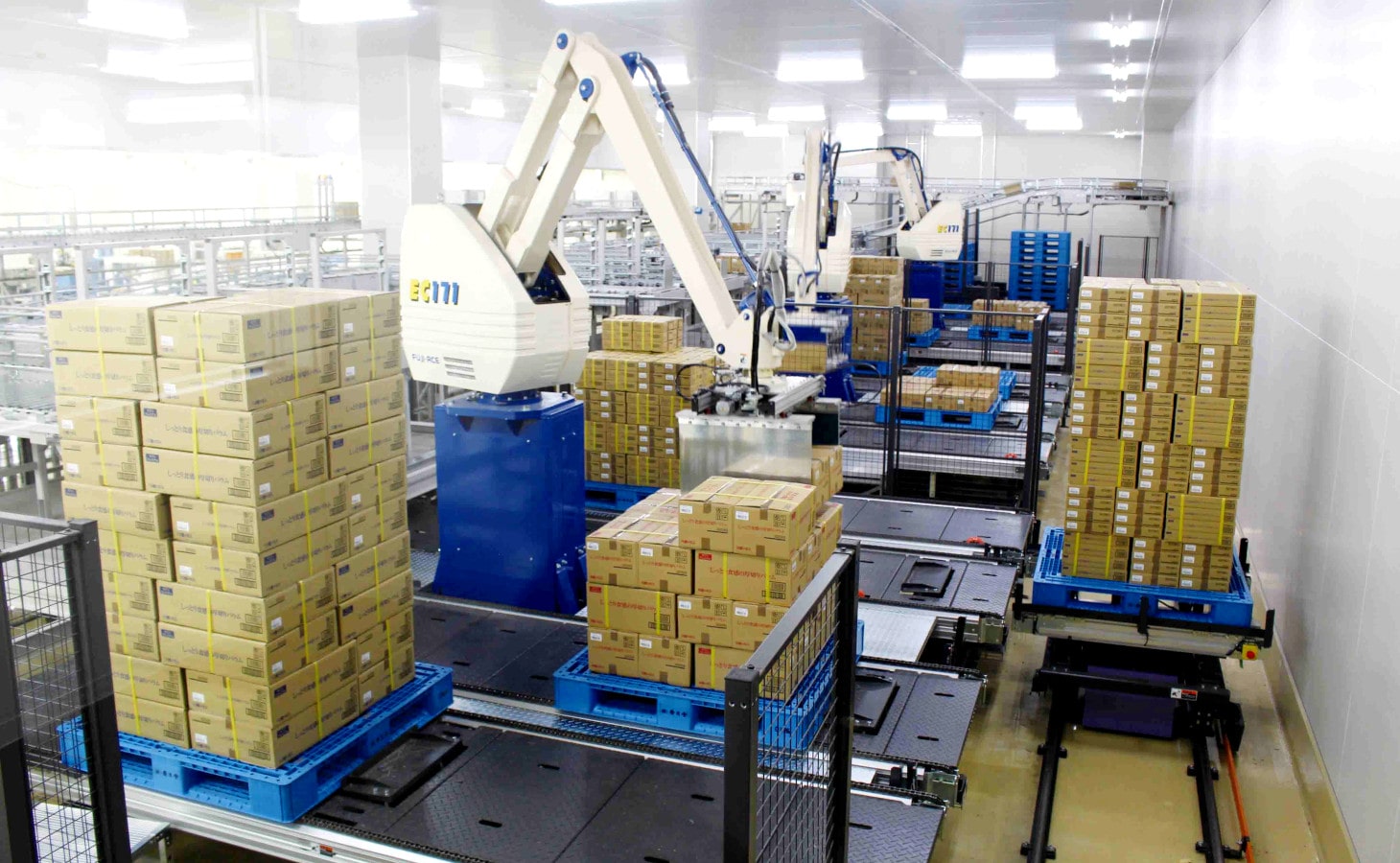
Kagetsudo Co., Ltd. established a Shirotori plant that functions similar to their headquarters in Toyokawa, Japan. Kagetsudo manufactures and sells confectioneries like baumkuchen and pound cake. They upgraded their production facilities and built a product storage system connected directly to production lines. In addition to increasing production capacity, Kagetsudo adopted automated systems for post-manufacturing processes to further streamline production. The new system is designed with room for future growth and reflects the Kagetsudo motto to "deliver safe, trustworthy, delicious, value products."
State-of-the-art plant to further streamline production
Kagetsudo was founded in 1953 as a Japanese confectionery manufacturer and, in the 1970s, expanded to produce Western confectionery, too. In recent years, the company has expanded its business scale to include private brands for major convenience stores and mass retailers.
To meet these new demands, Kagetsudo built the Honohara plant (in Toyokawa, Japan) in April 2007. They later constructed the Shirotori plant to compensate for their aging main plant. Kagetsudo's focus was on streamlining production in their two new plants. The Honohara plant used a Unitload Automated Storage and Retrieval Systems (Unitload AS/RS) and had already achieved a certain level of automation. However, when the Shirotori plant was planned, Kagetsudo wanted a higher level automation. The Shirotori plant uses a product storage system consisting of pallet AS/RS, high-speed rail-guided vehicle system Sorting Transfer Vehicle System (STV), and palletizing robots, achieving full automation of processes from storage to shipping.
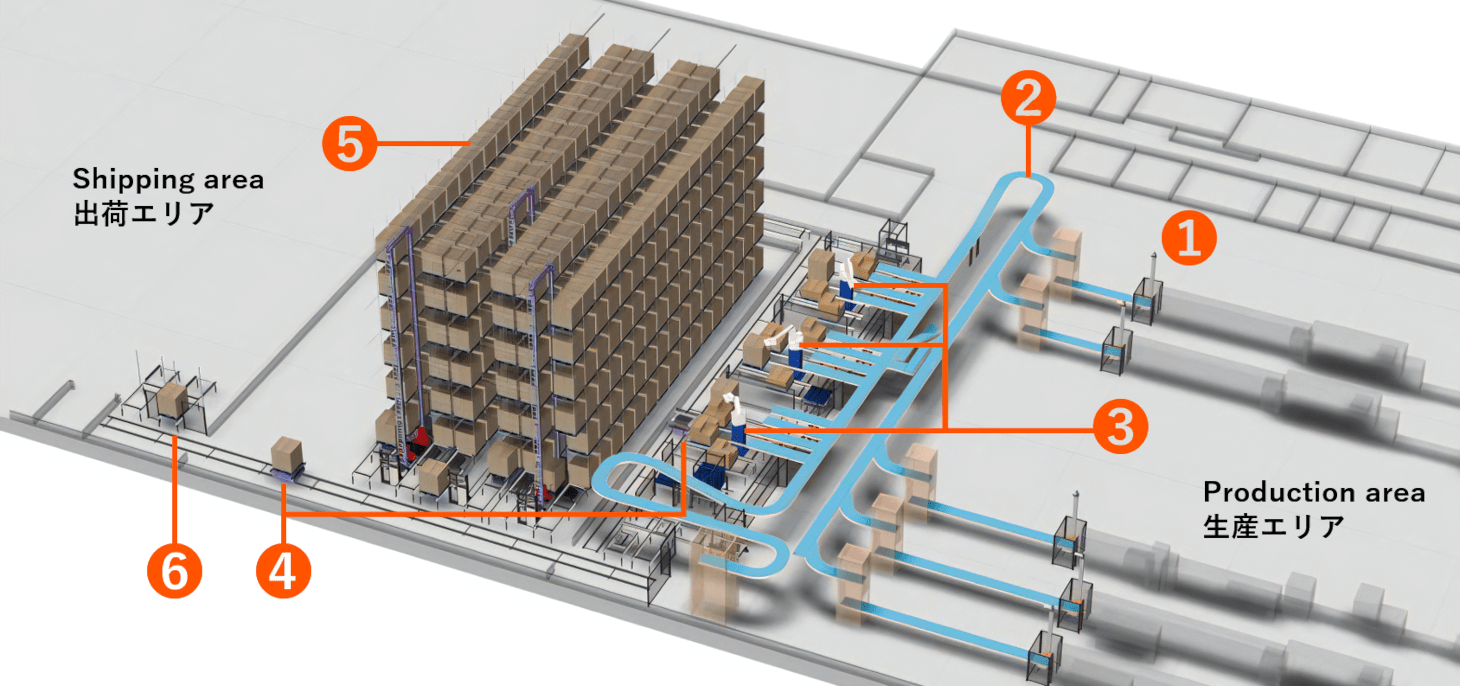
Automated operations and increased storage capacity
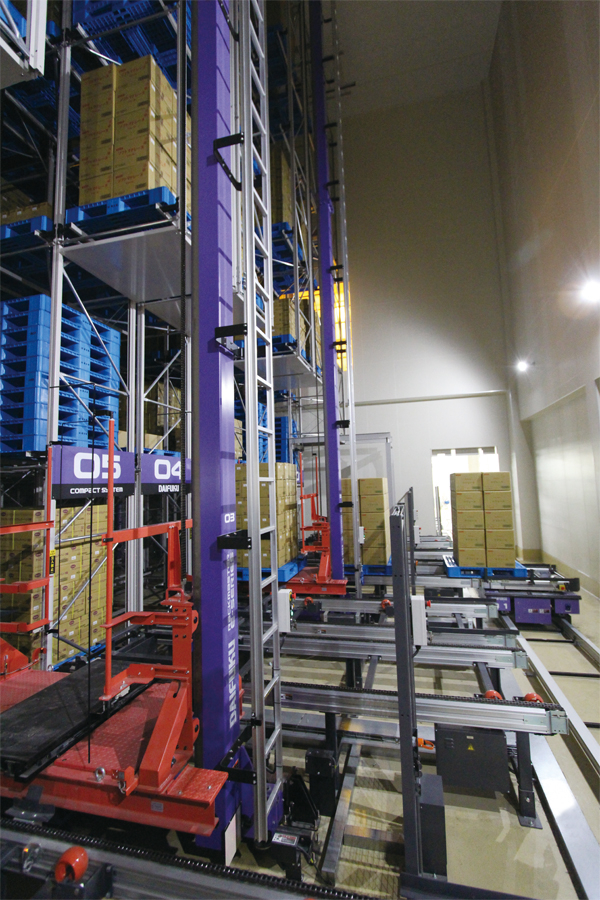
13-meters-high pallet AS/RS with three stacker cranes, stores 598 pallets
Because Kagetsudo's old main plant used conventional storage methods, load handling was a time-consuming process. In addition, the plant's storage space was insufficient for the peak production season, so they had to rent public warehouses to meet storage needs.
The new plant's storage system eliminates manual work and maximizes storage space by using high-rise racks. The new storage capacity is double that of a conventional warehouse, and using of inventory control computers makes FIFO order handling simple and easy. Packaging films are also stored in part of the rack to further conserve space.
The Shirotori plant produces a total of 300,000 individually packaged items (82 confectionery types) each day. To produce baumkuchen, for example, it takes only four hours to go through the manufacturing processes: material measurement, mixing, baking, cool down, cutting, wrapping/packaging. Confectionery produced at the Shirotori plant are typically shipped the next day and delivered to around 300 different locations, including food wholesalers.
Customer's Voice
Mori
Deputy Manager, System Group, Purchasing Department
We built the Shirotori plant based on our desire to have an automated, worker-friendly plant with increased production capacity. The storage system is also based on these concepts. Post-manufacturing processes have been significantly streamlined, which in turn speeds up the shipping process. Manual work has been eliminated, labor costs have been reduced, and our working environment has been improved.
Contact Us
For product inquiries, please reach out to us via our Contact Us page.
Contact UsContact Us
For product inquiries, please reach out to us via our Contact Us page.
Contact Us