Connectwell Industries
Empowering Connectwell’s Journey to Operational Excellence
In the competitive landscape of electromechanical and electronic products, Mumbai-based Connectwell Industries has established itself as a trusted name. However, managing a warehouse with over 20,000 SKUs posed a significant challenge. High variability, demanding throughput, and complex dispatch operations created obstacles to achieving their ambitious growth targets. They needed a solution that was both innovative and reliable—one that aligned with their vision of operational excellence.
To address these challenges, Connectwell partnered with Daifuku in 2017-2018 to revolutionise their warehouse operations. A state-of-the-art Mini-Load Automated Storage and Retrieval System (AS/RS) transformed their 800 m² facility into a hub of efficiency and precision.
Key features of the Daifuku AS/RS system
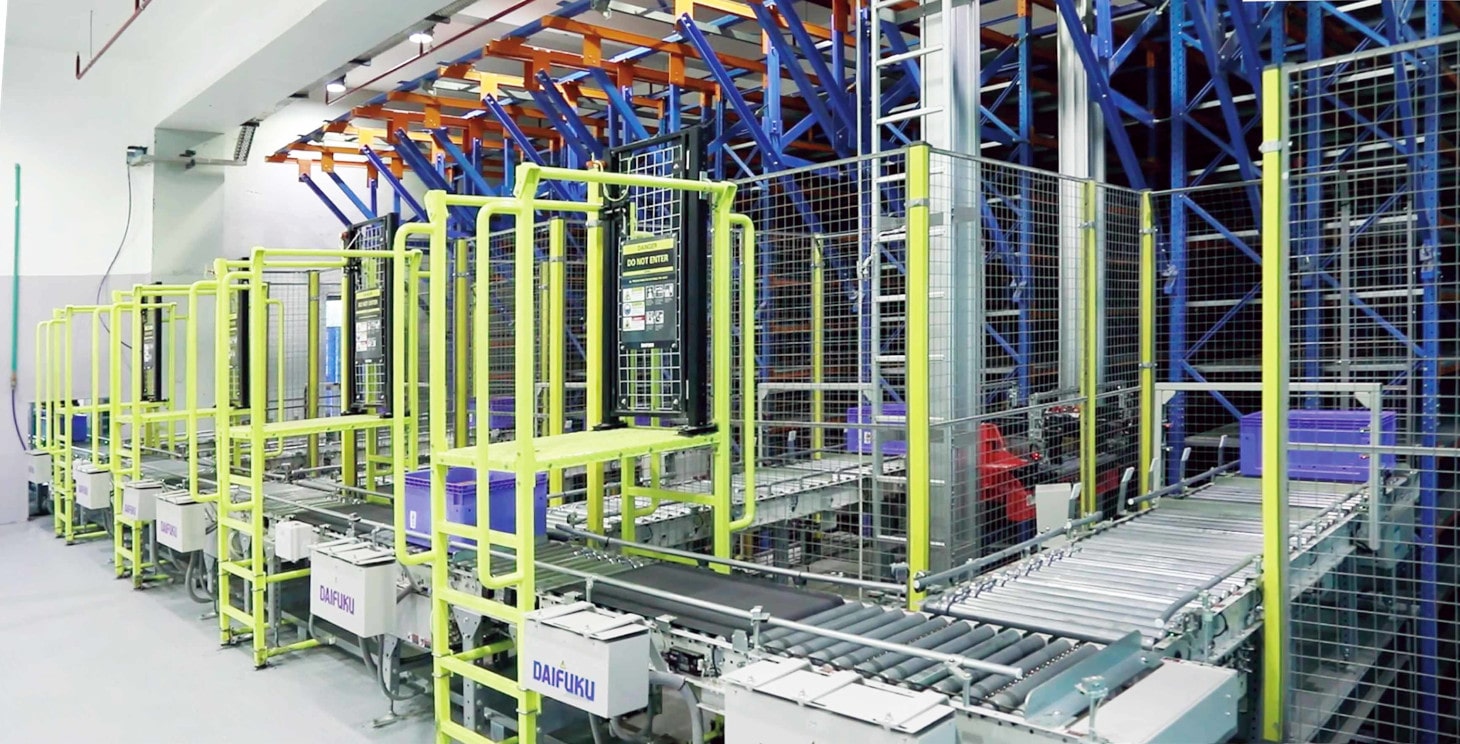
- Five 15-meter-high stacker cranes: Maximising vertical storage space.
- 27,360 bin storage locations: Efficiently handling raw materials, work-in-progress (WIP), and finished goods.
- WareNavi integration: Enabling real-time inventory management for streamlined and accurate operations.
Multi-floor design—a strategic advantage
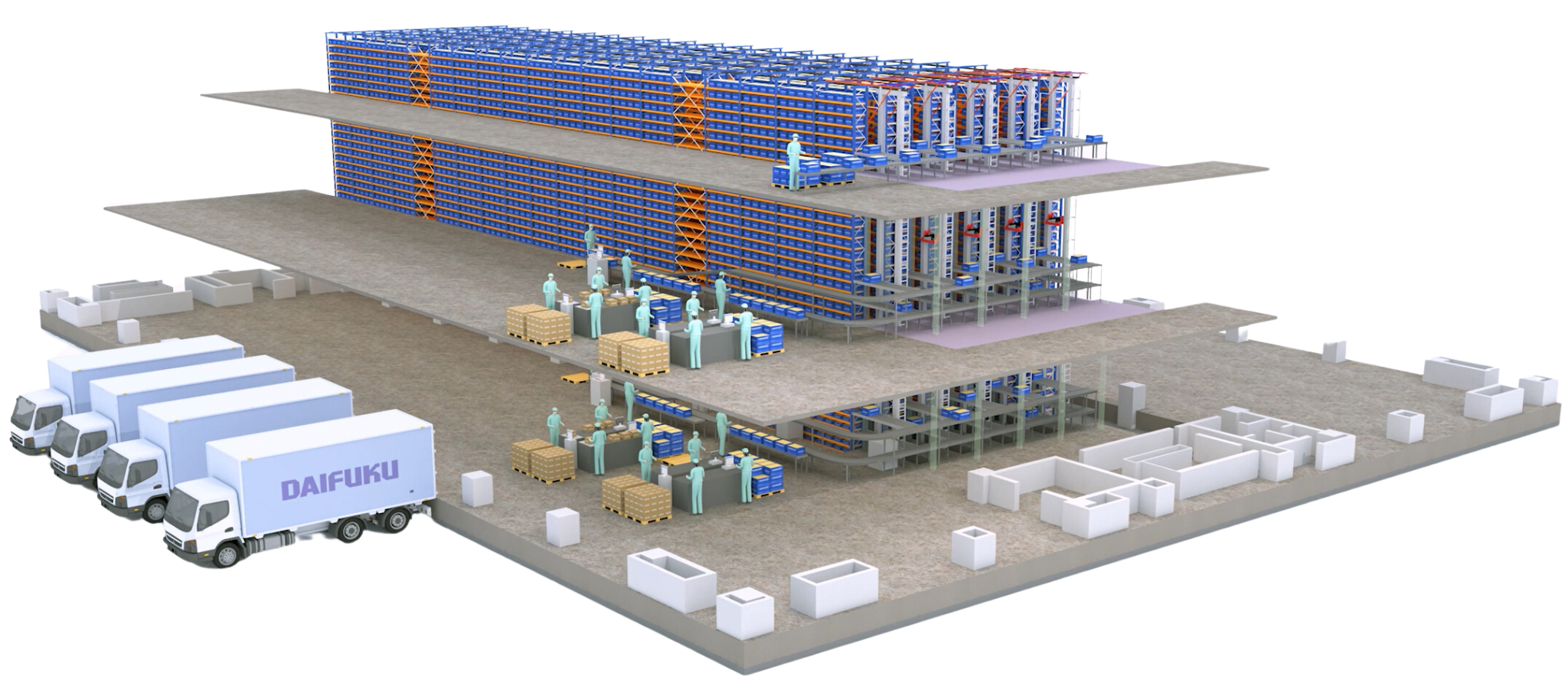
The innovative multi-floor design maximized the system’s potential.
- Ground Floor: Optimised for receiving raw materials and dispatching finished goods.
- First Floor: Dedicated to finished goods retrieval, ensuring quick and accurate dispatch.
- Second Floor: Focused on picking, kitting, and processing WIP, seamlessly integrating into the production cycle.
This design significantly reduced space requirements compared to conventional storage methods.
Tangible benefits for connectwell
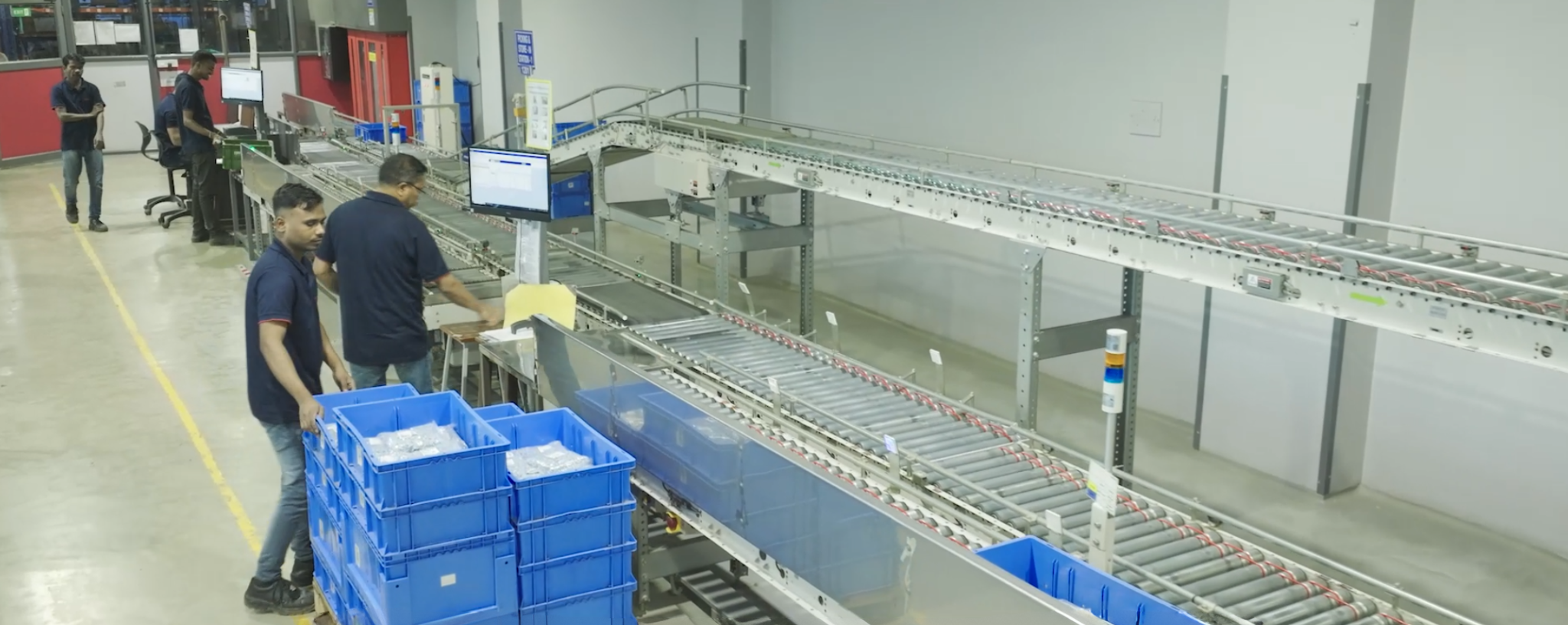
Daifuku’s AS/RS technology delivered substantial results for Connectwell, including:
- 80% increased storage capacity: Leveraging vertical space for enhanced storage.
- Throughput of 600+ bins per hour: Meeting high demand with ease.
- Superior accuracy and control: Minimizing errors and ensuring precision.
- Increased labor efficiency: Streamlining workflows and reducing manual intervention.
Beyond addressing immediate operational challenges, the system provided a scalable foundation for future growth, enabling Connectwell to confidently meet evolving market demands.
Customer's Voice
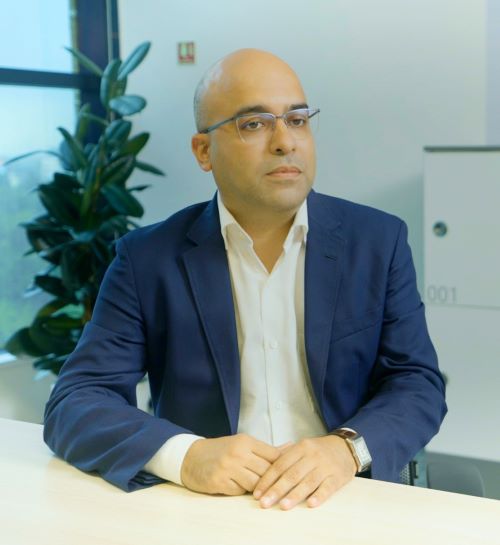
Sandeep Saheta, Managing Director at Connectwell
"Daifuku provided a customised solution to manage our massive inventory of over 20,000 SKUs. Their multi-level operations effectively handle raw materials, work-in-progress, and finished goods while meeting our high-throughput requirement of 600+ bins per hour.
Additionally, their after-sales service is exceptional. Our customer service has dramatically improved, and we are more responsive to market demands. Daifuku has truly been an integral part of our growth story."
Connect with Us
For direct inquiries regarding Intralogistics projects in India, please visit our Daifuku Intralogistics India page for contact details. For projects in other regions, reach out to us through the Contact Us page.
Contact Us
For product inquiries, please reach out to us via our Contact Us page.
Contact UsContact Us
For product inquiries, please reach out to us via our Contact Us page.
Contact Us