Komatsu Ltd.
New solution for parts distribution improves picking efficiency and safety

As part of its goal to improve its operating processes, Komatsu Ltd. introduced a new material handling system at its Tochigi Plant. The new system, includes a mini load AS/RS (automated storage and retrieval system) that uses projection mapping technology for rack-side picking operations.
Komatsu, a manufacturer of construction and mining equipment, forklifts, industrial machinery, and other products, has twelve manufacturing locations in Japan. Among them, its Tochigi Plant is the only one in Japan that handles the entire process from development to production of small construction machinery and forklifts.
The plant was opened in 1968, and while the production facilities were consolidated and transferred within the Komatsu group, processes and operations were spread throughout many small buildings on the grounds, making it difficult to achieve efficient production and distribution. In 2014, with the buildings aging and production and distribution efficiency lagging, Komatsu began to reform its operational processes.
To improve its onsite logistics, the company reorganized its existing buildings, consolidating many of the processes and functions that had been dispersed through the site. As part of this effort, Komatsu moved its distribution building that held parts for vehicle production to the assembly building being expanded on site.
In 2018, the company introduced Daifuku’s Shuttle Rack M as the first step to improve the efficiency of both inventory storage and picking operations in its assembly plant. The Shuttle Rack, which stores approximately 6,600 small and medium-sized parts, allows personnel to pick parts in fixed positions, greatly improving work efficiency.
Another feature of the Shuttle Rack M is its high-throughput capacity. While the old distribution building used to use another company’s AS/RS for picking, its low throughput resulted in a bottleneck, with it only able to manage receiving and storage operations during the day, preventing any retrieval and picking operations until midnight. The installation of Daifuku’s Shuttle Rack M improved throughput, thus facilitating a reduction in the amount of required overtime work.
Outbound conveyor is laid out in a U-shape to ensure that pickers can work at a fixed position.
The Shuttle Rack M has a double-deep storage rack to increase storage efficiency, with a maximum capacity of 2,880 cases. It is possible to simultaneously replenish and pick containers for retrieval and reentry into the AS/RS.
Points
- Improves picking efficiency by reducing the need to walk and search
- Easy-to-understand visual work instructions reduce errors
- Safety maintained through various sensors.
Clear picking instructions through colors and text information
In 2020, Daifuku also introduced a mini load AS/RS that boasted Japan’s first system using projection mapping technology for rack-side picking operations. Of the installation, Ikuo Yamazaki of the facility’s Production Engineering Section commented, “Daifuku was able to coordinate the entire process, which made it possible for us to install the system without issue.”
The mini load AS/RS stores 1,500 different parts that are required to always be kept in stock. Across 12 picking areas, there are 240 picking slots along the sides of AS/RS racking. The new system provides a wider variety of information than standard digital displays, including not only the picking quantity but also the destination, target model, and part number. Each are equipped with a unique sensor that signals through a red light and buzzer when a picking error has occurred.
Previously, a certain number of parts had to be retrieved from the old AS/RS in the prior distribution building, but this took time and resulted in many picking errors. After the introduction of Daifuku’s system, parts can be picked from the picking slots within each area in a designated order upon being retrieved from the AS/RS and can be supplied directly to the production line. “We can easily pick parts for multiple units at once based on the color and text information on the display, removing the need for handheld lists. This has improved efficiency and reduced picking errors,” commented Yamazaki.
In terms of safety, there are zone and area sensors in each area to ensure that the stacker cranes do not handle loads in and out of areas where personnel are present.
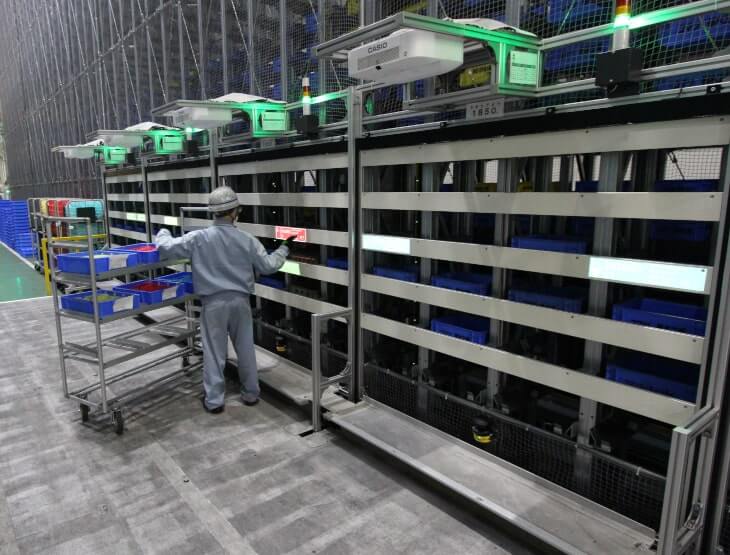
Customer’s comment
Ikuo Yamazaki Production Engineering Section Production Department Production Division Tochigi Plant
“Through the AS/RS and other measures, will can strengthen our production framework and ensure a timely supply of parts to the production line.”
Contact Us
For product inquiries, please reach out to us via our Contact Us page.
Contact UsContact Us
For product inquiries, please reach out to us via our Contact Us page.
Contact Us