Daiichi Storehouse & Refrigeration Co., Ltd.
Cold storage AS/RS significantly streamlines distribution operations
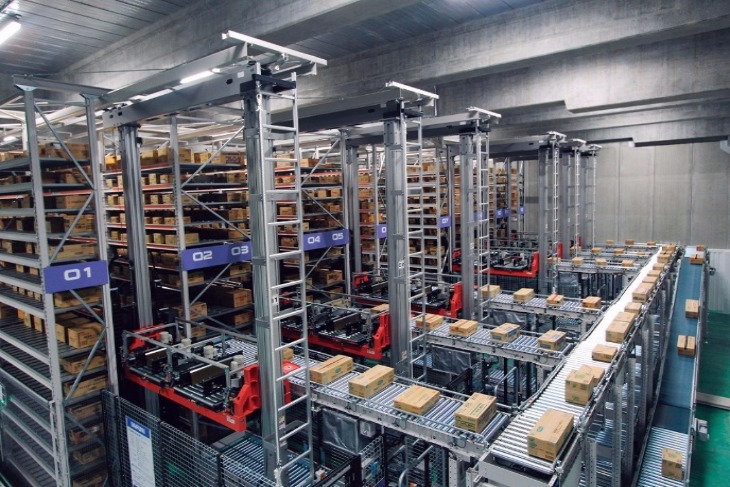
In April 2015, Daiichi Storehouse & Refrigeration Co., Ltd. established the Iwatsuki Nagamiya Distribution Center (Saitama City, Saitama Prefecture), a four-story, seismically isolated building. The company designated the second floor of the center as a frozen item distribution area (known as the “Frozen DC”) that covers chains stores handling home deliveries all the way up to major food wholesalers. While the site has continued to provide logistics services that meet the needs of its customers, in April 2016, Daiichi Storehouse & Refrigeration introduced new IT and material handling equipment to streamline and automate its logistics operations, and reduce the number of manual tasks required within the frozen warehouse.
Supports high-mix, low-volume deliveries of 600 frozen food items
Daiichi Storehouse & Refrigeration’s Frozen DC, located in Saitama City, is responsible for the delivery of frozen food items to approximately 400 stores of 36 chain stores in Saitama, Chiba, Ibaraki, Tochigi, and Gunma Prefectures. The company handles around 1,500 frozen commercial food items, including ice cream and precooked frozen foods. Of the 1,500, around 600 are high-turnover products, thus high-mix, low-volume deliveries are required, as well as strict lot control by expiration date. When the Frozen DC was initially put into operation, the majority of receiving inspections, and storage and retrieval operations, were conducted manually. However, the cold environment, which is -25°C in the frozen area, was particularly challenging for personnel. With labor shortages increasing and with the number of products anticipated to increase, the company sought to streamline its operations.
Notable reduction in required work hours and fewer shipping errors
The delivered material handling system includes wireless handheld terminals with character recognition, a cold storage (-25°C) mini load AS/RS with cranes equipped with dual extractors, cold storage Mobile Racks, automatic labelers for attaching shipping labels, and a conveyor line that can handle an average of 12,500 cases per day.
When products arrive at the warehouse, personnel scan the JAN or ITF codes, and best-before and manufactured-on dates shown on the cases with a handheld terminal. After scanning, a portable label printer automatically issues a receiving label, which is attached to each case, where they are then transported to one of four areas: products designated as A are sent to the Mobile Racks, B and C products to the mini load AS/RS, and D products to the fixed racking.
When shipping, personnel pick A and D products from the Mobile Racks and fixed racking using a handheld terminal. Picked products are consolidated into orders and fed into an auto labeler line, which automatically attaches shipping labels based on shipping destination. When the products are transported further downstream, they are automatically sorted to shipping lines based on the attached label. Before loading the sorted goods into shipping trolleys, operators confirm that gathered cases are in the correct line. Products B and C stored in the mini load AS/RS are automatically consolidated and retrieved, requiring very little involvement from personnel on site and freeing them up to handle other tasks. Once retrieved from the AS/RS, B and C products are transported by conveyor and then handled in the same way as the other products.
Handheld terminals are equipped with character recognition and read barcodes, expiration dates, and production dates
Picked products are delivered to approximately 400 stores of 36 chain stores
Two auto labeling lines sort products
Customer's Comment
Katsuhiro Kawamata
Executive Officer and General Manager
Refrigerated Storage Division
The installed system allows anyone to work easily by eliminating the need for manual operations at -25°C. Further, required work hours for related processes have been greatly reduced and shipping errors are now almost non-existent. However, what is most gratifying is that our personnel are now working with smiles on their faces.
Contact Us
For product inquiries, please reach out to us via our Contact Us page.
Contact UsContact Us
For product inquiries, please reach out to us via our Contact Us page.
Contact Us