Logisteed East Japan, Ltd (formerly Hitachi Transport System Metropolitan Co., Ltd.)
A model center of automation and labor saving for sustainable 3PL operations
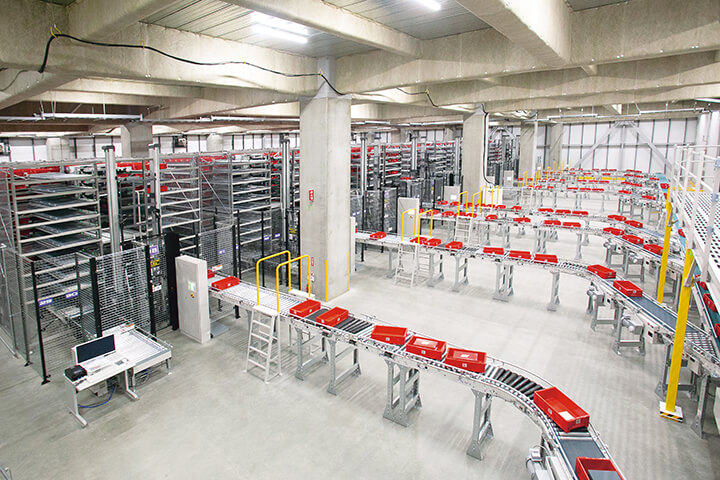
Logisteed East Japan launched the Kashiwa Platform Center, a logistics base for handling sports shoes, in Kashiwa City, Chiba. In line with its management strategy of promoting automation and labor saving, the company has built a model facility featuring a material handling system with a high-throughput case automated warehouse at its core.
Implementing a material handling system to deal with the growth of the shippers
Since 2015, Logisteed East Japan has been operating a distribution center in the Tokatsu region on behalf of a major foreign sports shoe manufacturer as a 3PL. With strong sales of sports shoes, shipment volume had been expanding year on year. In response, the company had gradually set up seven logistics facilities to match the growth in the volume of goods. However, those goods were often having to be moved between the facilities. In addition, the increasing number of sites and lack of automated equipment meant that many of the company's logistics operations were handled manually, which impacted efficiency. To tackle these problems, the company proposed to the consignor to build a highly automated distribution center centered on a material handling system that would bring about labor savings. While short-term contracts are common in the 3PL industry, Logisteed East Japan started to tackle the issue by signing long-term contracts with shippers.
From order picking to batch picking for higher efficiency.
In contrast to the order-picking method that was used primarily at the previous centers, Logisteed East Japan changed to a batch picking and sorting method, in which products for multiple orders are picked together and then sorted by shipping order. While batch picking requires less travel distance for picking operators, it requires sorting in the next process. To improve the efficiency of this sorting process, the company sought an automated material handling system. Logisteed East Japan initially considered installing a piece sorter, a put-to-light system, and an automated case warehouse. The company finally selected Daifuku as its partner after evaluating our comprehensive capabilities, our system layout proposal that met throughput requirements while meeting space constraints, our ability to respond to desired delivery dates, and our after-sales service capabilities.
The material handling system on the fourth floor, which is responsible for sorting operations, consists of the Shuttle Rack M, a high-throughput case buffering and sequencing system; receiving stations; shipping stations; empty container pool lines; shipping sorting lines; automatic box-making machines; automatic box-sealing machines; a scrap compressor; and a conveyor system connecting everything together.
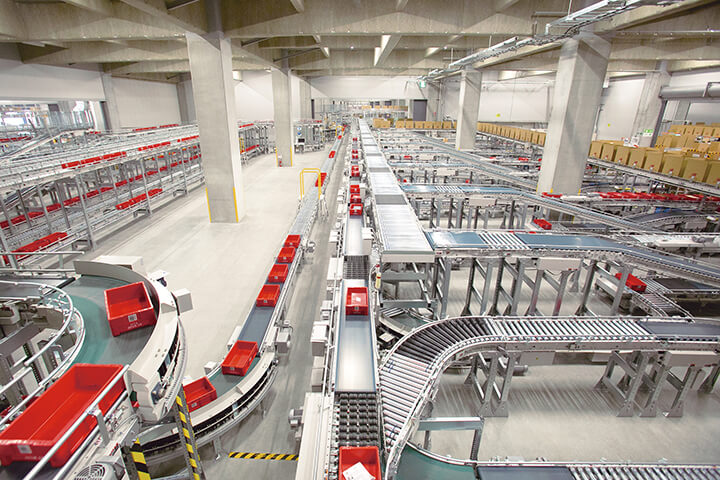
140% higher productivity achieved
The center receives all footwear products for the Japanese market from overseas factories and stores them in pallets on the Mobile Rack on the fifth floor. The products are then picked in batches, stacked on pallets, and transported by vertical conveyors to the fourth floor. After attaching price tags for the stores, each shoe case is placed into a dedicated plastic container from a receiving station and temporarily stored in the Shuttle Rack M. Based on the shipping and packaging information data, up to 13,000 pairs can be batch-processed. When all the items for an order are ready, they are retrieved from the Shuttle Rack M according to shipping order and sent to a shipping station, where they are inspected and packed before being shipped out all over Japan.
The Shuttle Rack M consists of high-speed lifters and a shuttle vehicle on each rack level. By switching to goods-to-person operations at the fixed receiving and shipping stations, the entire process of picking, sorting, and shipping has been greatly streamlined, resulting in a 140% increase in productivity.
Customer’s comment
Strategic investment for the future
The introduction of material handling systems is a strategic investment with an eye on the future. In constructing the new distribution center, we focused on the sustainability of the operation to respond to changes in the business environment. In the future, we will propose the Center's strengths in automation and labor saving to other shippers as well. The needs of shippers vary widely depending on the type of business and the items handled. We are always one step ahead in creating logistics infrastructure to meet each of these needs.
Related links (typical products)
Shuttle Vehicle Miniload AS/RS "Shuttle Rack M"Contact Us
For product inquiries, please reach out to us via our Contact Us page.
Contact UsContact Us
For product inquiries, please reach out to us via our Contact Us page.
Contact Us