World-First Temporary Storage and Sortation System “SPDR”
In 1957, Daifuku supplied Japan’s first chain conveyor for car body transport to an automobile plant. Since then, we have achieved many results in almost all processes of automobile production. In addition to innovative conveyor systems, we have provided various solutions for improving productivity of parts handling in and parts supply to the line side of main assembly lines. However, traditional systems for the reception and storage of parts from suppliers and timely retrieval according to production schedules often required manual labor. To improve said process, we developed and launched the SPDR (pronounced spider), a temporary storage and sortation system for parts, in December 2014.
Flexible handling of cases varying in size
The SPDR comprises the arm, which automatically raises and lowers to grasp cases of parts; a girder, which enables movement in four directions; and the rails and support columns for the girder. The system is able to stack cases directly on the floor area within the support columns. The chuck on the arm is a proprietary technology, and is the world’s first to handle cases of varying sizes. It can grasp cases one by one or in a stack, and thus can easily handle cases on lower layers. It facilitates picking retrieval and grouping retrieval operations, flexibly satisfying line side demand.
Demand for mechanized parts logistics
In automobile plants, parts need temporary storage before being supplied to production lines. In many cases, they were temporarily loaded on the floor and then manually retrieved and sorted, which placed a heavy burden on workers, particularly since a case containing parts weighs up to 20 kg. In addition, we received many requests from customers who wished to accomplish the following:
- Utilize limited space more effectively
- Automate operations without seperating different case sizes
- Install and make the system operational in a short period
- Minimize time required for relocation and layout change after installation
- Improve efficiency of case sortation by direction and time
- Introduce flexible automatic systems
- Retrieve cases even if the system is down
Please enlarge the screen to view
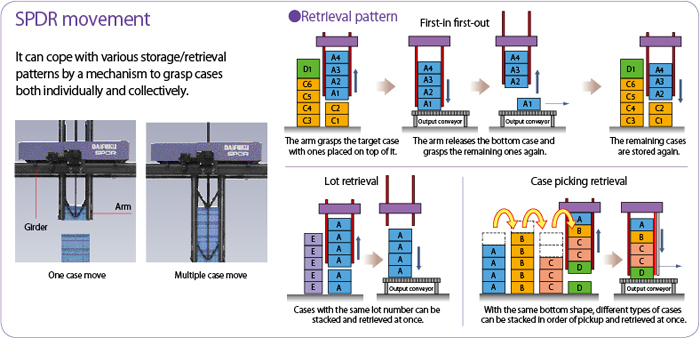
Solution for various issues related to parts logistics
Development of the SPDR was started in response to the above wishes on the concept of automating operations while using a minimal amount of fixed parts, such as racks, and enabling workers to manually handle cases if the system is down. The SPDR flexibly stores cases, of which sizes and quantities may change every day, using conventional floor loading.
The system has a high throughput of up to 80 storage and retrieval cycles per hour (7x7 meter configuration), and is highly flexible, allowing input and output ports to be located anywhere as needed and to be modified or added in a short time, even after installation.
For retrieval, the following three patterns are available: first-in first-out to retrieve only one of the grasped cases and re-store the others, lot retrieval to output a stack of cases with the same lot number, and case picking retrieval to pick up different types of cases into an ordered stack and deposit them at once. The system can handle most commercially available containers, including standard, handled, two-colored, and collapsible containers, which can weigh up to 20 kg individually and up to 150 kg in total when grasped as a stack. Besides extensive functions for inventory control, the SPDR provides various expansion interfaces that enable storage, retrieval, and inventory check via tablets.
Please enlarge the screen to view
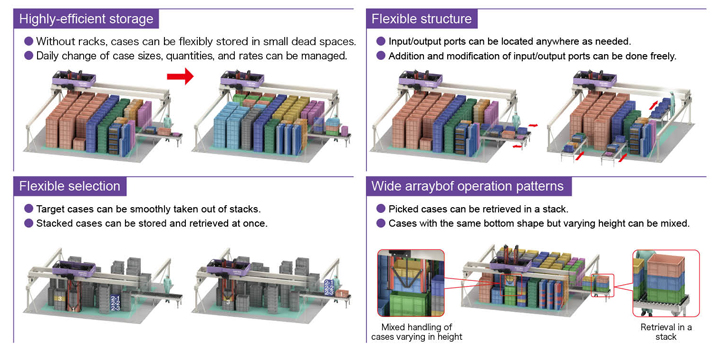
Contact Us
For product inquiries, please reach out to us via our Contact Us page.
Contact UsContact Us
For product inquiries, please reach out to us via our Contact Us page.
Contact Us