Top 5 Automated Material Handling System Trends in India for 2025
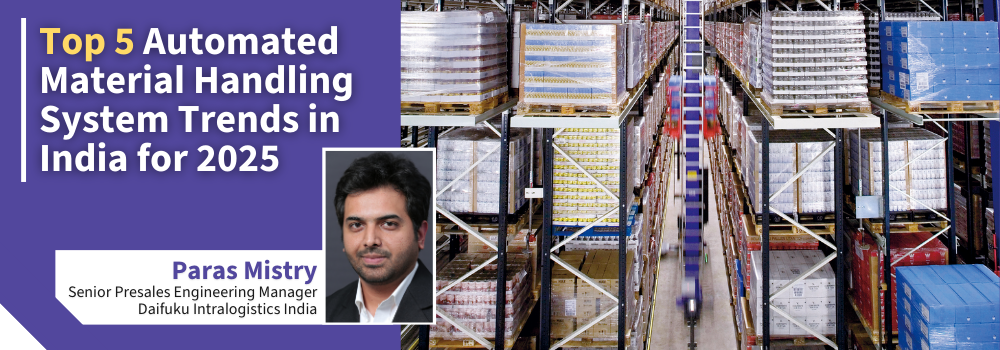
The rise in demand, shorter turnaround times, and increased productivity have made automation a necessity rather than a luxury. As the Indian manufacturing landscape undergoes a major transformation, businesses are adopting automated material handling systems (AMHS) to stay ahead of the curve. Several key trends are shaping the future of material handling in India.
With advancements in AMHS, businesses are shifting towards scalable, space-efficient, and tech-driven solutions. This blog explores the top trends that will define warehouse management in India in 2025.
1. Expansion in Storage Capacity
The demand for higher storage capacity in warehouses is increasing as businesses seek to optimize their supply chain operations. Traditionally, warehouses in India had storage capacities of 2,000 to 6,000 pallets per location. However, with the integration of automated material handling systems, modern warehouses now accommodate over 10,000 pallets, significantly enhancing efficiency and inventory management.
One of the primary reasons for this shift is the implementation of the Goods and Services Tax (GST) in 2017. Before GST, companies managed multiple small warehouses across different regions to optimize tax benefits. However, with GST simplifying the tax structure, businesses started consolidating their storage facilities into larger, centralized warehouses. The unified tax also eliminated the need for various checkpoints at state borders which caused significant delays pre-GST. This has streamlined logistics, reduced operational costs, and improved inventory accuracy (*1).
Additionally, as awareness of automated material handling systems grows, businesses are now incorporating Automated Storage and Retrieval Systems (AS/RS) in their factory planning stages. Previously, AS/RS was an afterthought, leading to costly and time-consuming retrofits. However, by planning AS/RS integration from the outset, companies can achieve better warehouse efficiency while saving on installation costs and operational downtime.
Daifuku's AS/RS had a transformative impact on Everest Spices, boosting processing speed by 400% and reducing truck loading times from six hours to just two. With system uptime consistently exceeding 95%, Everest reliably met growth commitments.
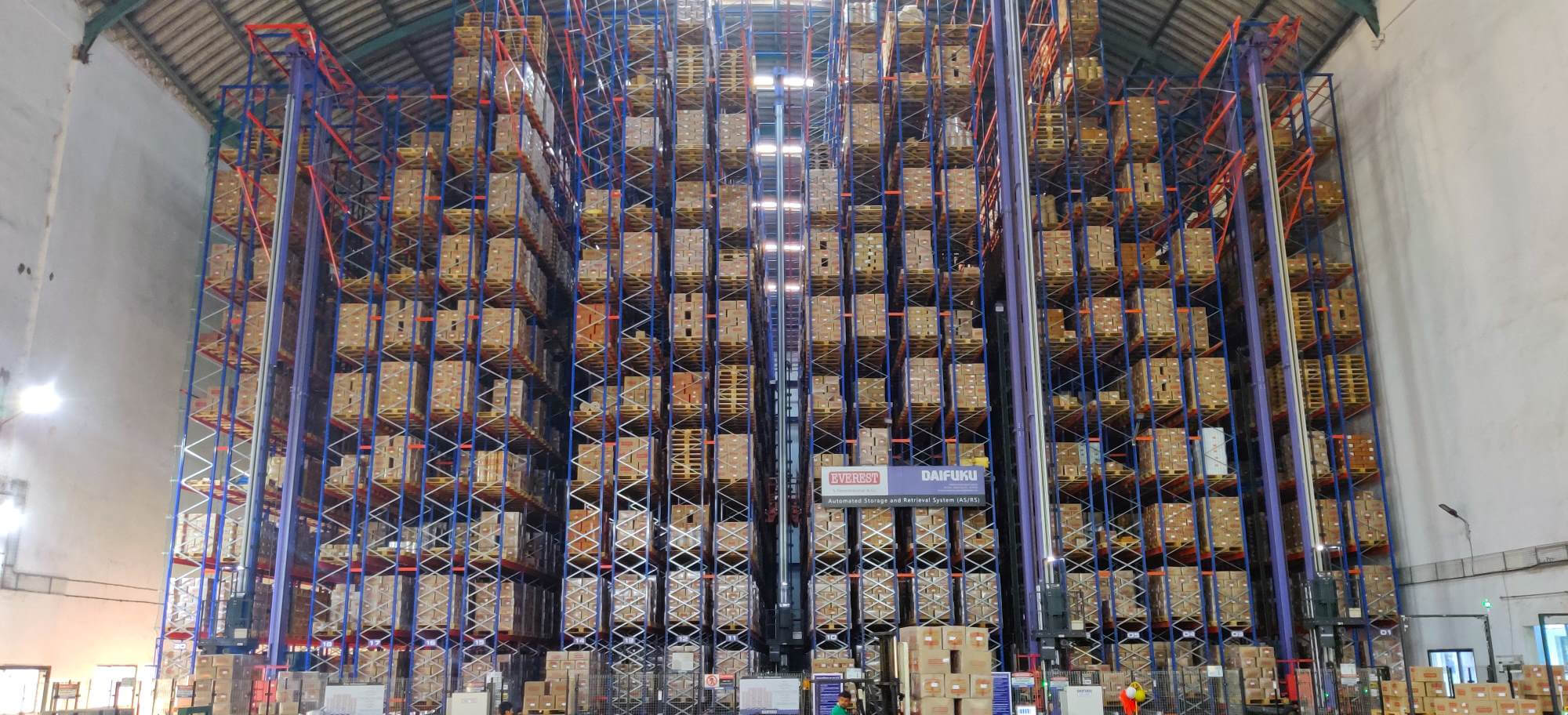
2. Adoption of Clad Rack Warehouses (Rack-Supported AS/RS Buildings)
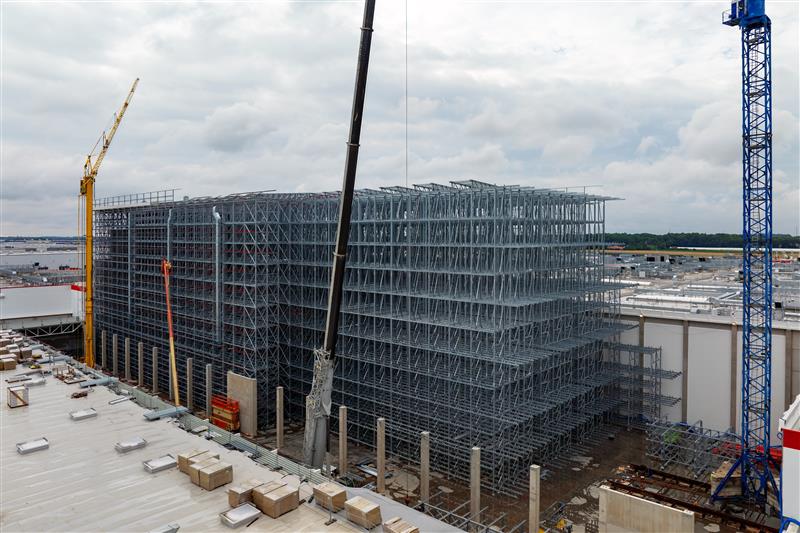
Another major trend in the Indian warehouse automation sector is the adoption of clad rack warehouses, a rack-supported AS/RS building. These structures integrate storage racks as part of the building’s framework, allowing for taller warehouse structures that maximize vertical space.
The acceptance of 20+ meter high AS/RS buildings is increasing, as companies recognize the advantages of space-efficient storage. Clad rack buildings eliminate the need for conventional construction, significantly reducing project timelines and sometimes costs.
Furthermore, organizations prefer turnkey AS/RS projects, where the automation provider designs and installs the entire system, simplifying execution and reducing risks.
Advantages of Clad Rack AS/RS buildings:
- Maximizes storage capacity within a smaller footprint.
- Reduces construction costs by eliminating traditional infrastructure.
- Enhances automation efficiency through optimized layouts.
- Faster project completion compared to conventional warehouse construction.
According to an article by Workplace Material Handling & Safety, rack-supported AS/RS warehouses can save construction cost up to 50% while increasing storage efficiency (*2).
3. Growth of Sunrise Sectors: Battery, EV, and Semiconductor Industries
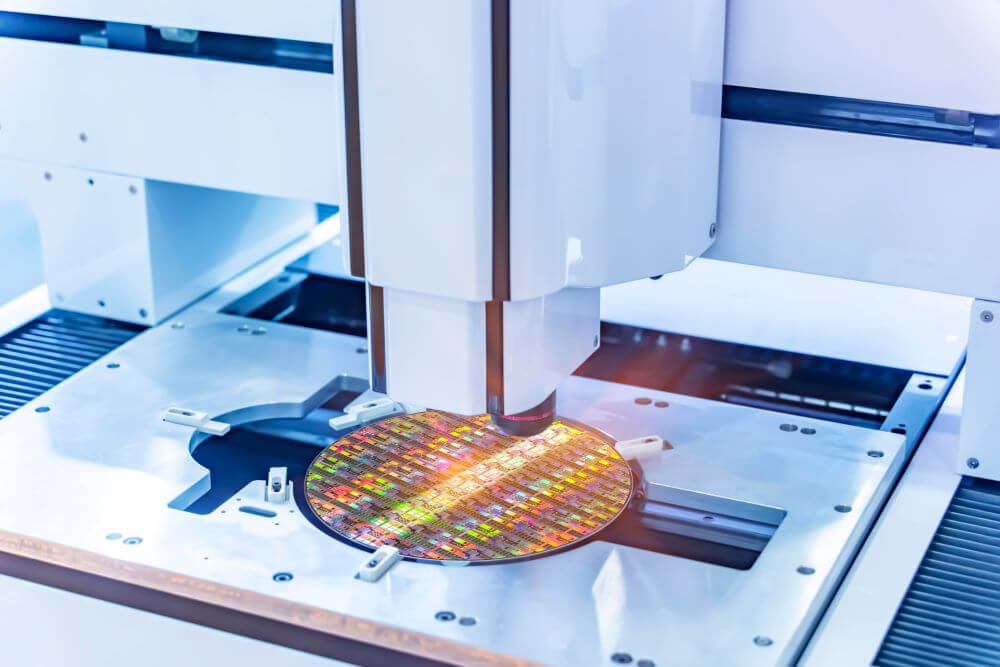
India’s push towards self-reliance and advanced manufacturing under the Make in India initiative has led to significant growth in sunrise sectors such as battery production, electric vehicles (EVs), and semiconductors. The industry is actively promoting automation in these industries to enhance self-reliance and global competitiveness.
With initiatives like the Production Linked Incentive (PLI) scheme, which provides financial incentives to companies in the battery and EV sectors, have motivated them to scale up their operations and increasingly adopt automated material handling systems (*3). These sectors require precision handling of components, making AS/RS and robotics crucial for material movement, storage, and retrieval.
Additionally, major global players are collaborating with Indian conglomerates to establish manufacturing hubs. For example:
- Tesla have signed a strategic deal with Tata Electronics to procure semiconductor chips for its worldwide operations and is likely to invest at least $2-3 billion in India to manufacture electric cars (*4).
- Ola Electric is setting up an automated battery production facility and has announced an investment of $500 million for establishing a Battery Innovation Center (BIC) in Bangalore (*5).
The rise of these industries will further accelerate the adoption of AMHS, ensuring seamless logistics, error-free handling, and high-throughput operations.
4. Robust After Sales Services
The adoption of modular AMHS solutions in India is expected to grow by 12.7% CAGR during 2025-2030, driven by increasing demand for automation in the e-commerce, pharmaceuticals, and FMCG industries (Mordor Intelligence report) (*6). As more such businesses in India integrate Automated Storage and Retrieval Systems (AS/RS) into their warehouses, the demand for after-sales services is set to rise significantly.
With AS/RS systems becoming critical to supply chain functions, businesses are actively seeking reliable after-sales support, including timely servicing, system upgrades, and quick access to spare parts. One of the key factors influencing companies’ decisions on AS/RS providers is the presence of an established base in India, ensuring quicker resolution of technical issues, minimal downtime, and easy availability of spare parts when needed. A strong after-sales network reduces operational risks and enhances system longevity, making it a crucial consideration for businesses investing in automation.
Recognizing this need, Daifuku has strengthened its presence in India with a dedicated manufacturing plant, ensuring seamless supply chain support and local expertise. To further enhance operations and meet the growing demand, Daifuku is expanding its footprint by setting up a second manufacturing facility in India. This move underscores Daifuku’s commitment to providing end-to-end ASRS solutions, from installation to post-implementation support, making it a trusted partner for businesses looking to optimize their material handling systems.
Hyderabad Factory
New factory under construction
India team engaged in O&M
5. Government Initiatives Boosting Automation in Warehousing
The Indian government has introduced multiple initiatives to encourage automation and smart manufacturing. Programs such as SAMARTH Udyog Bharat 4.0 are promoting digital transformation in the industrial sector, enabling businesses to implement advanced automation solutions like automated material handling systems.
Additionally, according to a report by IESA, India’s local semiconductor market is likely to grow to $103 billion by 2030 (*7). It will require developing an ecosystem of local suppliers and improving the supply chain. Infrastructure projects under the National Logistics Policy aim to reduce logistics cost. As part of this push, government-backed schemes are facilitating investments in warehouse automation, robotics, and smart logistics technologies.
Summing It Up
The future of automated material handling systems in India looks promising, driven by increasing storage demands, advanced AS/RS adoption, government-backed initiatives, and the rise of new-age industries. Businesses that embrace these trends will gain a significant competitive advantage, ensuring efficiency, scalability, and long-term growth.
As India moves towards becoming a global manufacturing hub, automated material handling systems will be at the core of this transformation, redefining logistics, warehousing, and supply chain management. Companies investing in these advanced solutions today are not just preparing for 2025 but are setting the foundation for sustained success in the decades to come.
References:
- *1Business Para: GST Impact on the Logistics Industry in India
- *2Workplace—Material Handling & Safety: Rack-Supported Warehousing Meets Growing Demand
- *3ET Edge insights: The role of PLI schemes in promoting local EV component manufacturing
- *4The Economic times: ata Electronics seals semicon deal with Teslat
- *5OLA: Ola to invest USD 500 million in battery innovation and indigenous cell R&D
- *6Mordor Intelligence: India Automated Material Handling Market Size & Share Analysis - Growth Trends & Forecasts (2025 - 2030)
- *7Outlook Startup: India Semiconductor Market To Cross $100 Billion By 2030 (IESA Report)
Find Out More About AS/RS Solutions
Stay ahead of the curve with automated material handling solutions. Explore our detailed AS/RS solutions pages and delve into the rich history of automated warehouses at Daifuku.
Daifuku's Cleanroom Business
Along with our Intralogistics, Automotive, and Airport business units, we also have a Cleanroom business dedicated to providing automated systems to the semiconductor and flat panel industries. If you're looking to find out more about the business and its offerings, check out our dedicated Cleanroom Business site.
Paras Mistry
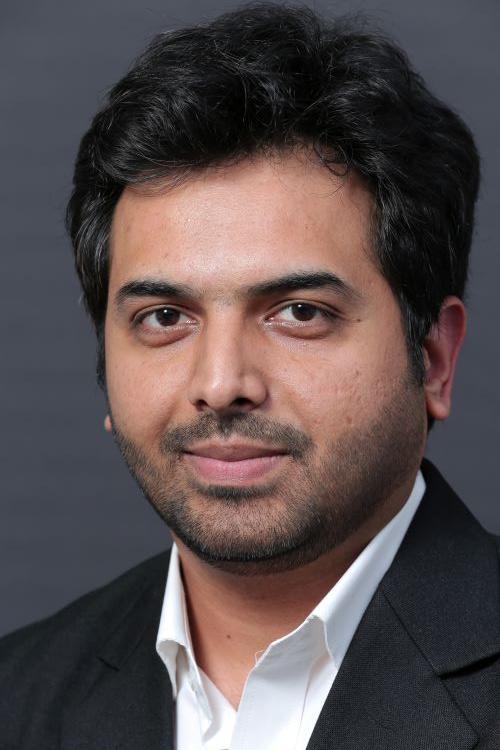
Senior Presales Engineering Manager, Daifuku Intralogistics India
Paras Mistry joined Daifuku Intralogistics India Pvt Ltd. in 2017 and currently serves as a Senior Presales Engineering Manager for the Intralogistics business, focusing on the Indian market. He is passionate about leveraging innovative solutions to enhance operational efficiency and drive business success. Paras has built his credibility by working with top-tier companies across various industries, including paints, tyres, food (Everest Foods), and Electricals (Connectwell Industries).
Paras is committed to delivering high-quality work and striving for excellence in all his professional endeavours. Ensuring client satisfaction with the services and solutions provided is a key value for him. He embraces new technologies and innovative approaches to enhance processes and outcomes. Paras values continuous learning and staying updated with industry trends and advancements. Additionally, he collaborates effectively with teams and clients to achieve common goals.
He holds a management degree in business administration and a mechanical engineering degree. With over a decade of experience in the material handling industry, starting from 2011, Paras brings a wealth of knowledge and expertise to his role.