Pallet Handling: Unit Load AS/RS vs. Mobile Rack – Fully Automated or Semi-Automated?
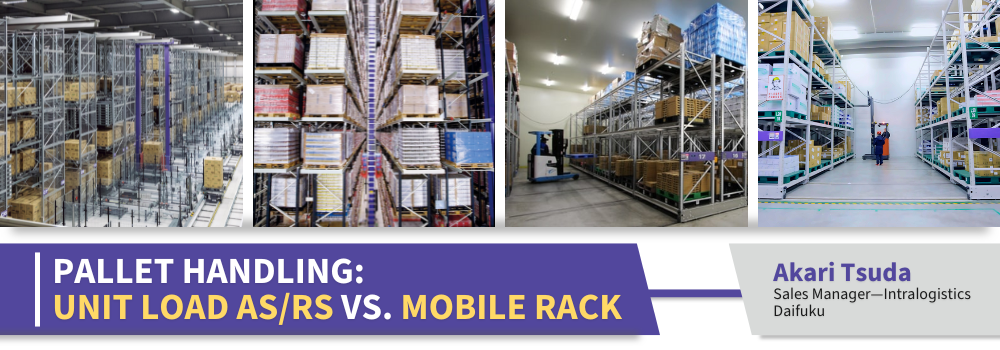
When selecting a pallet storage system for your warehouse, distribution center, or factory, many key areas must be considered, such as operational efficiency, space utilization, and cost-effectiveness.
Two popular pallet storage solutions, the Unit Load Automated Storage and Retrieval System (AS/RS) and Mobile Rack, offer distinct advantages depending on your specific needs. This article will compare these systems to help you make the right choice for your operations.
What is a Unit Load and a Mobile Rack?
Before we delve into a deep comparison, let's see what each system actually is.
Unit Load AS/RS
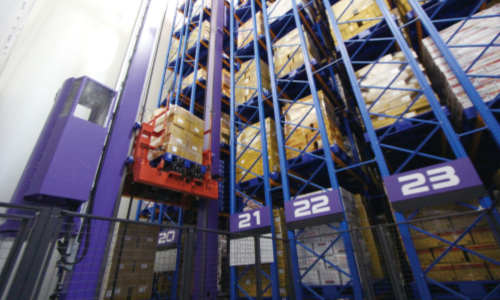
A Unit Load AS/RS is an automated system designed for high-capacity storage and retrieval of palletized goods. It efficiently utilizes vertical space and employs automated cranes to move pallets in and out of a racking system with minimal human intervention. This system is ideal for high-volume operations in facilities where horizontal space is limited.
Mobile Rack
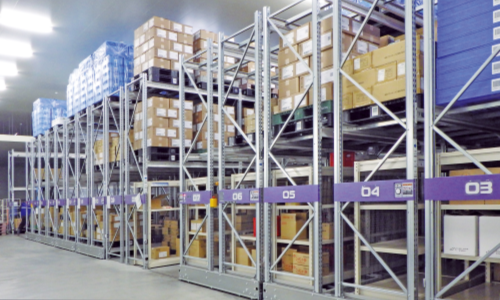
A Mobile Rack is a semi-automated pallet storage system consisting of fixed racks at each end, with movable racks mounted on dollies in between. These racks can be shifted along the dollies to create aisles for forklift or personnel access during retrieval and case picking. While the Unit Load offers greater storage capacity, the Mobile Rack provides higher storage density, allowing more pallets to be stored in a smaller area. It is an ideal solution for facilities with a sufficient labor pool, low ceilings, lower pallet handling throughput requirements, or where a higher level of automation is not necessary.
Key Considerations for Choosing a Storage System
When deciding between a Unit Load AS/RS and Mobile Rack, consider these factors:
1. Building type and space availability
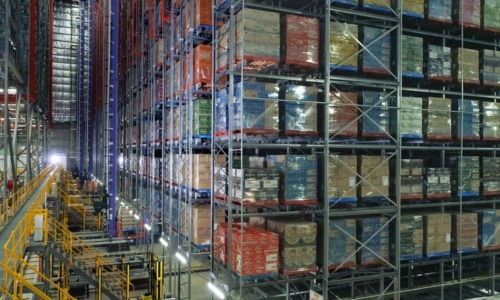
Unit Load
Can typically go up to 40 meters; thus, require tall ceilings and strong floors, making it ideal for new or high-ceiling facilities.
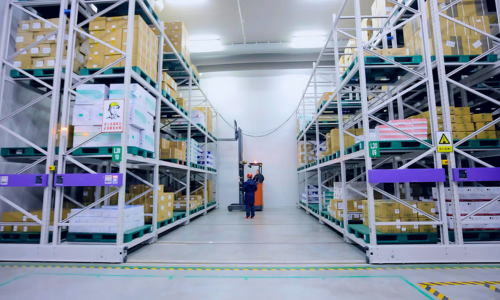
Mobile Rack
Typically reaching heights of 7-8 meters—with racking height determined by forklift reach capabilities—it offers flexibility in existing or smaller spaces, adapting to various facility shapes and sizes.
2. Space layout and utilization
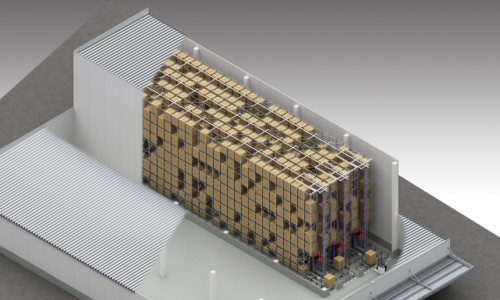
Unit Load
Maximizes long, vertical space.
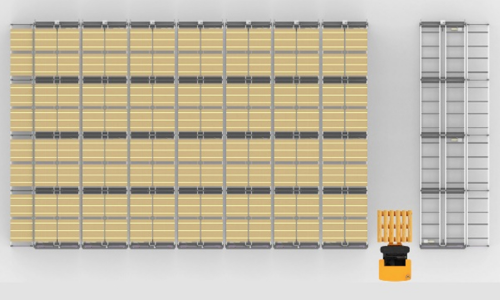
Mobile Rack
Better for square or rectangular spaces and have a low storage footprint thanks to their high-density nature.
3. Storage capacity and density
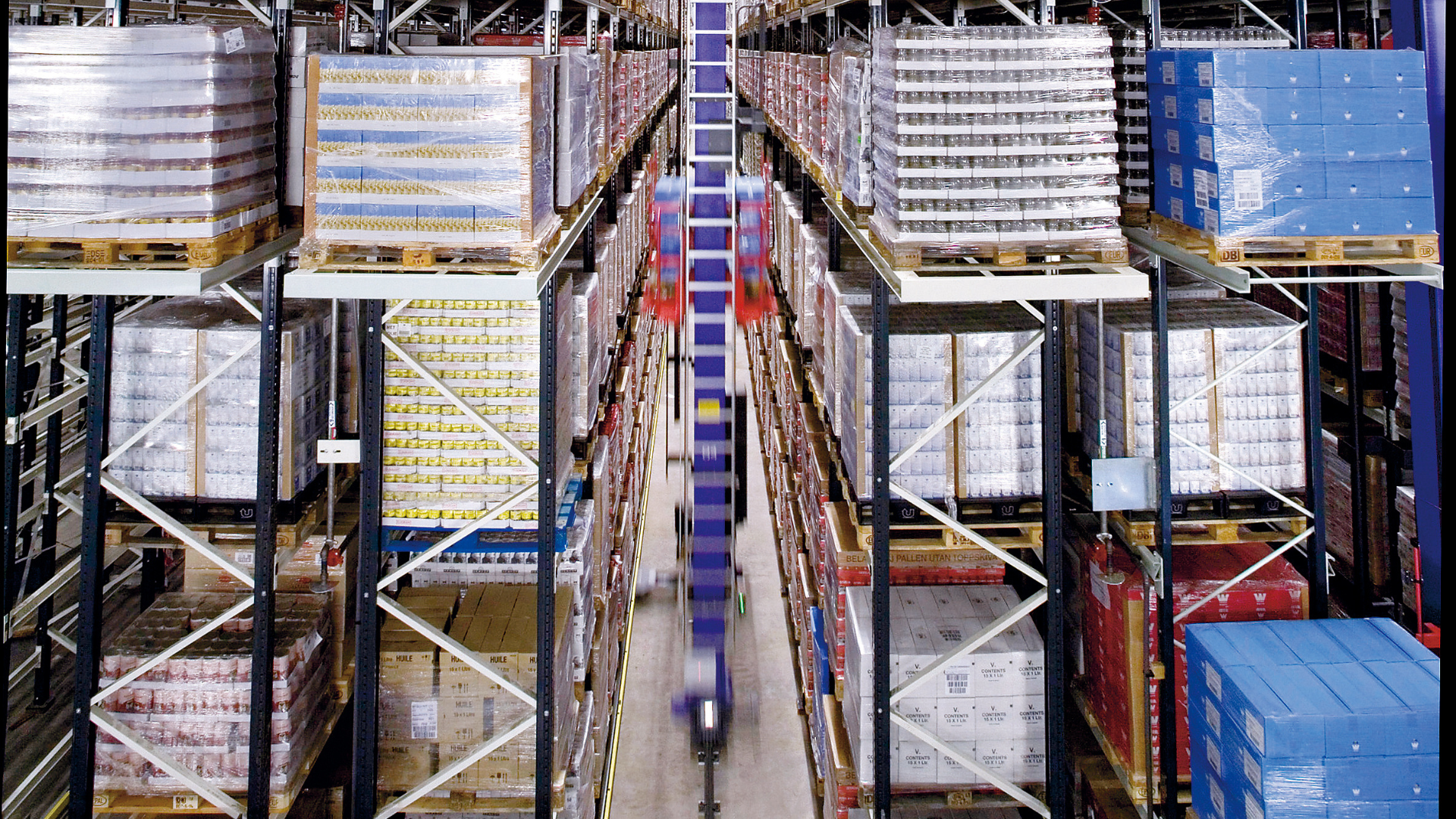
Requires a crane aisle per 2 or 4 rack banks.
Unit Load
Capable of rising up 40 meters high, the Unit Load is optimal for high-capacity storage, fully utilizing that vertical height. However, the system does have lower storage density compared to the Mobile Rack.
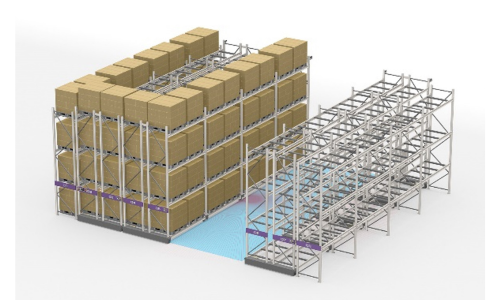
Requires only one aisle.
Mobile Rack
Offers greater storage density, particularly for small to medium pallet volume requirements.
4. Operational efficiency
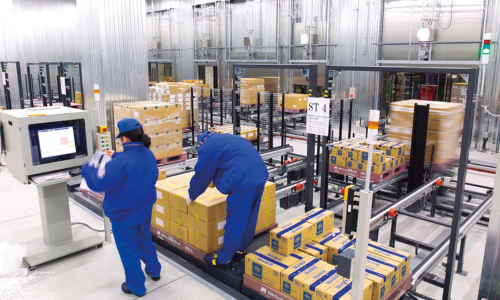
Case picking in 0-5°C
Unit Load
The Unit Load AS/RS is perfect for high-throughput storage and retrieval in any environment—ambient, chilled, or frozen. Fully automated, it operates continuously, with storage and retrieval performed at fixed conveyor stations, which eliminates the need for workers to search or drive through aisles. In frozen environments, the conveyors can be in areas with ambient temperatures around 0-5°C, reducing the physical burden on workers compared to the extreme conditions of -30°C. This improves labor productivity and minimizes the need for frequent breaks, making the operation more efficient.

Storage, retrieval and case picking at -30°C
Mobile Rack
Mobile Racks are better suited for low-throughput operations. Since only one forklift-accessible aisle can be opened at a time, the system becomes inefficient with high-frequency movements. In cold environments, the semi-automated nature of Mobile Racks means workers or forklift drivers must operate directly in freezing conditions, which can reduce efficiency due to the physically demanding work and frequent breaks required for safety.
5. System budget
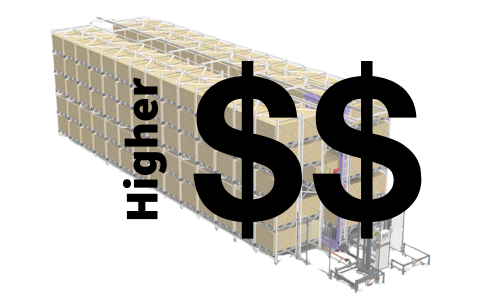
Unit Load
Has a higher upfront investment due to greater automation, integration, and infrastructure costs.
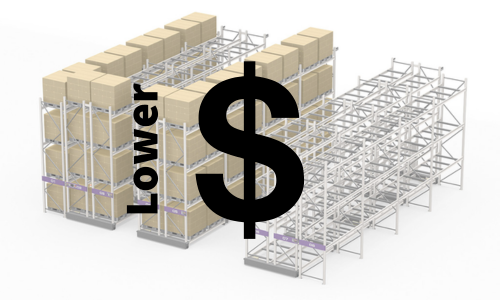
Mobile Rack
More cost-effective for facilities that don’t need full automation.
Direct Comparison: Unit Load AS/RS vs. Mobile Rack
Please enlarge the screen to view
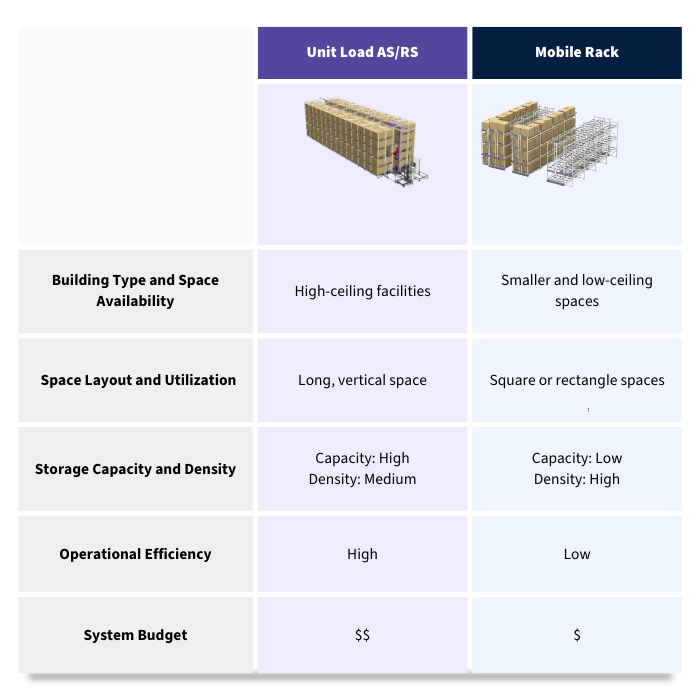
Which Is the Right One for My Business?
Choosing between a Unit Load AS/RS and Mobile Rack depends on your operational needs and situation:The Unit Load AS/RS is ideal if you have ample vertical space, require maximum storage capacity, and prioritize throughput, particularly in cold storage environments. While it requires a significant upfront investment, it offers long-term savings in labor and energy costs. Additionally, the Unit Load can integrate with other automated peripherals, further enhancing your system’s automation and future-proofing your operations.
The Mobile Rack is an ideal storage solution for businesses that require high-density storage in low-bay warehouses or buildings with limited ceiling height. It is particularly suitable for businesses with budget constraints and low-to-moderate throughput needs.
By assessing your facility’s layout, operational needs, and budget, you can determine the system that will best optimize your warehouse’s efficiency and scalability. At the same time, it’s important to consult with your automation partner to leverage their expertise and ensure the best fit for your business’s needs and long-term goals.
Real-Life Examples
Check out some of our case studies featuring the Unit Load and Mobile Rack, including Vinamilk (Unit Load), Charoen Pokphand Foods (Unit Load), and Nikko Sangyo Transport (Unit Load and Mobile Rack).
Akari Tsuda
Account Manager, International Business Dept., Intralogistics Division, Daifuku
Since joining Daifuku in 1999, Akari has primarily worked in the company’s Intralogistics business, focusing on Southeast Asia. Based at Daifuku’s Tokyo Headquarters, she has supported sales activities and projects for Group companies across the region, including in Vietnam, Thailand, Singapore, Malaysia, and Indonesia. With a wealth of experience in managing Intralogistics projects throughout Southeast Asia, Akari has built a fantastic track record in the region.