Revving up Efficiency in Automotive Spare Parts Centers
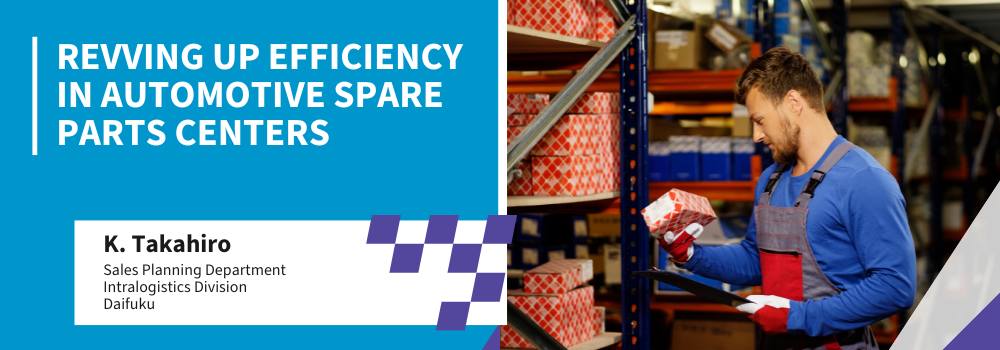
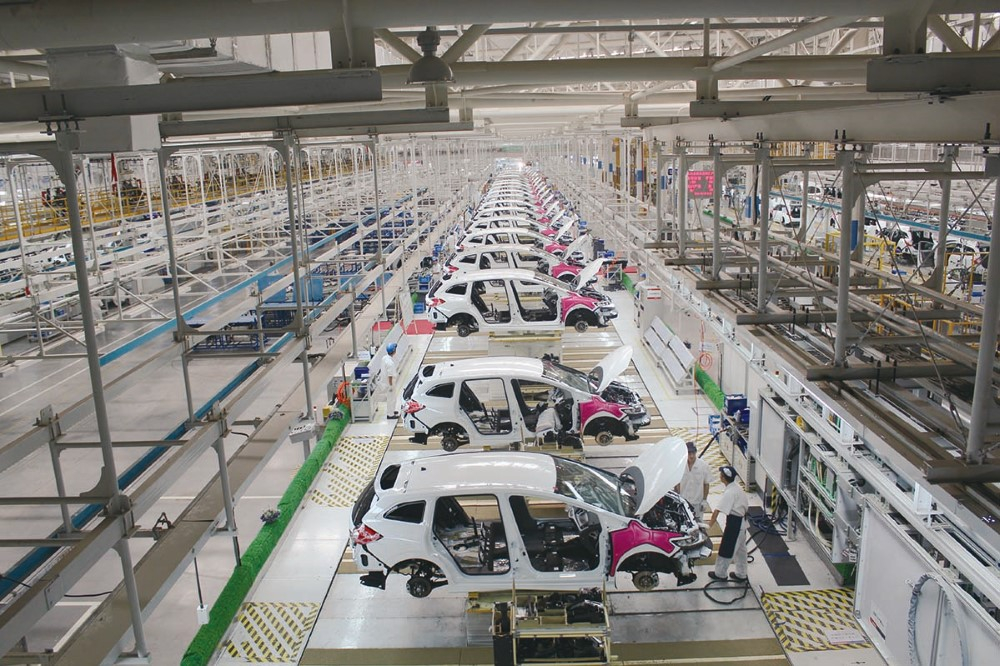
The automotive manufacturing industry has long embraced automation, creating highly efficient production lines characterized by robotic arms, conveyor systems, and automated vehicles. These elements work seamlessly together to transport automobile bodies through various stages of assembly.
However, the story doesn't end with the sale of a vehicle. Once it’s on the road, it requires regular maintenance and repair, necessitating a robust supply chain for automotive parts. Surprisingly, while manufacturing processes have become increasingly automated, parts handling in automotive parts centers has lagged behind, often relying on manual processes, fixed racking, and forklifts.
The complexity of parts handling
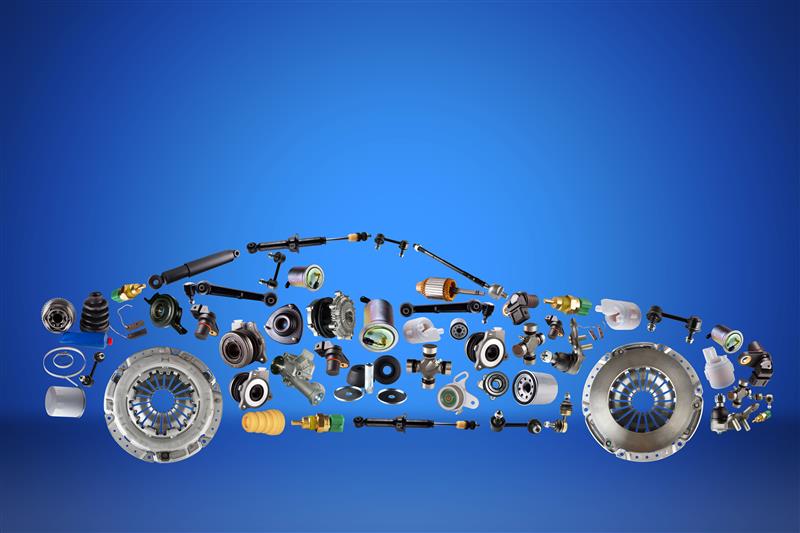
Automotive spare parts centers can manage an extensive inventory of tens of thousands of different sized components, ranging from bumpers, windshields, exhausts, cables and connectors, and even the smallest nuts and bolts. This diversity poses significant challenges in inventory management and logistics.
Unlike industries with a high volume of direct-to-consumer sales, such as e-commerce, automotive parts centers often operate in a B2B environment, typically meaning a slower shipping requirement compared to B2C environments that can also boast a huge number of SKUs. However, automotive parts centers still need to maintain a steady flow of parts to service centers, dealerships, and repair shops, ensuring that every component is readily available when needed.
With such a high number and variety of parts, depending on location, securing labor or land for a large enough site can be challenging. Automation can alleviate these issues and streamline many operations and processes on site, ensuring that you are as efficient as possible.
The case for automation
The adoption of automated material handling technologies can significantly enhance the efficiency of automotive parts centers. These innovations streamline operations, improve accuracy, reduce labor costs, and optimize space utilization. Additionally, automation typically leads to a decrease in forklift traffic, enhancing workplace safety. Many facilities still rely on manual methods, which increases the risk of accidents and potential damage to inventory.
Let’s explore some of the key automated systems that can transform parts handling in the automotive industry.
Please enlarge the screen to view
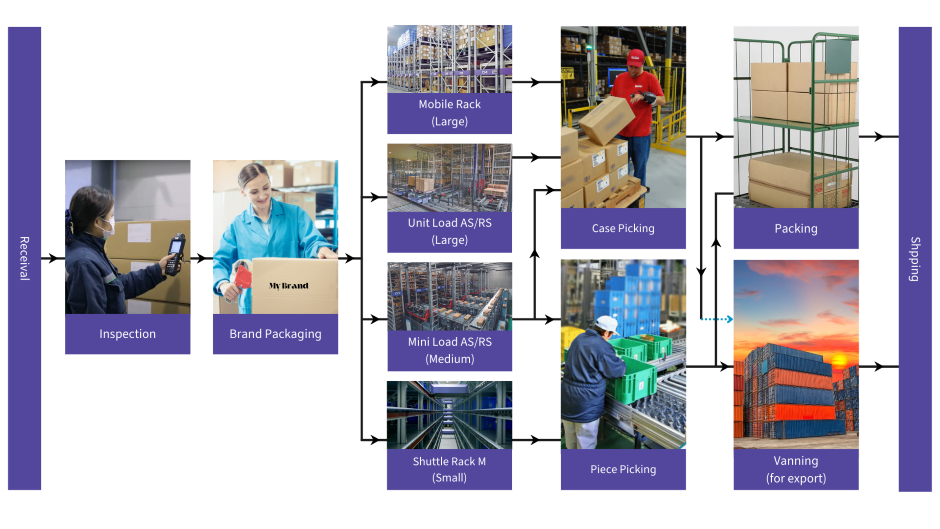
Large items: bumpers, windshields, and doors
For larger automotive components such as bumpers, windshields, and doors, the appropriate solutions include the Unit Load Automated Storage and Retrieval Systems (AS/RS) and Mobile Racks.
The Unit Load AS/RS maximizes available vertical space and efficiently stores and retrieves heavy items, minimizing the need for manual handling. The Unit Load stacker crane and its racking component can be adjusted to accommodate large and long items and unique pallets. Mobile Racks in comparison are a semi-automated system and typically cheaper than fully automated systems like a Unit Load. While not using as much vertical space as an AS/RS, its functionality provides high storage density and facilitates case picking operations.
Furthermore, the integration of Sorting Transfer Vehicles (STVs), Autonomous Mobile Robots (AMRs) and Automated Guided Vehicles (AGVs) can enhance the movement of large loads. These systems can transport items to set locations, such as shipping points or picking stations, within the facility, significantly reducing the time and labor associated with manual transportation.
Mobile Rack
Unit Load AS/RS
Mid-sized items: brake calipers, alternators, fuel pumps, filters, oil elements
For mid-sized items, both the Unit load or Mini Load AS/RS offer a practical solution depending on the size of the load and shipping frequency. The Unit Load can handle cases stacked on pallets, while the Mini Load is designed to handle smaller loads, such as singular cases and totes, efficiently while maintaining high throughput.
The Mini Load system can further be enhanced with its own STVs dedicated for case and small load handling.
Additionally, both systems can actively support picking operations—the systems release a case of pallet, which is then to a picking or collection point using a goods-to-person approach. Further, in recent times, robotic picking is also becoming an additional option.
Mini Load AS/RS
Mini Load STV
Small-sized items: bolts, lamps, and electronics
Managing small-sized items—such as fasteners, connectors, and electronic components—can be effectively streamlined with a Shuttle Rack or Mini Load Automated Storage and Retrieval System (AS/RS). These systems facilitate both storage and retrieval operations, providing a goods-to-person approach for picking stations. By automating the picking process, organizations can significantly reduce errors and enhance operational efficiency compared to a fully manual approach.
Shuttle Rack
Conveyor-based GTP station
Optimizing space and efficiency
One of the most significant advantages of automated systems is their ability to optimize vertical space. In many cases there is something automated storage solutions allow parts centers to take full advantage of their available footprint. By maximizing vertical space, these systems create opportunities for increased inventory without the need for additional square footage.
Moreover, fully automated systems like Unit Load and Mini Load AS/RSs can drop off cases and pallets on different floors (depending on layout and building), further enhancing the flow of materials throughout the facility. This design flexibility not only increases the level of automation but also streamlines operations, leading to faster turnaround times and improved service delivery.
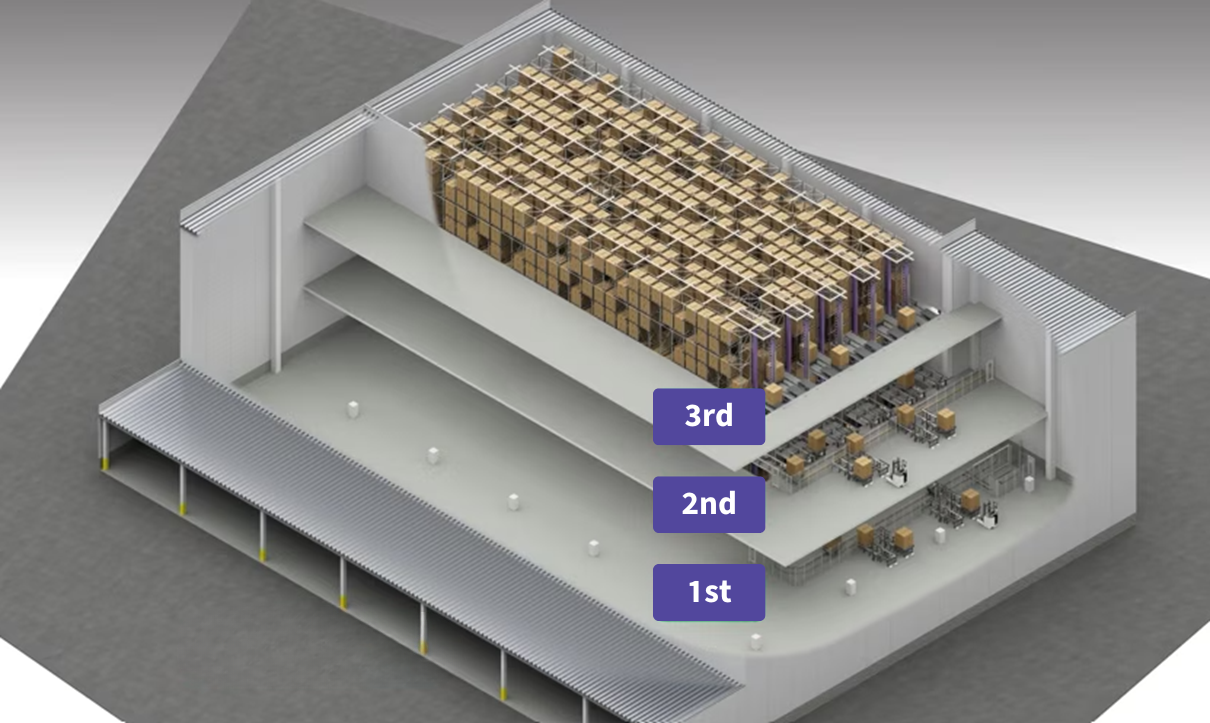
Driving it home
As the automotive industry continues to evolve, the push for automation in spare parts centers will become increasingly vital. By embracing automated material handling technologies, automotive parts centers can enhance their efficiency, improve accuracy, and optimize their operations. The integration of solutions such as a Unit Load AS/RS, Mini Load AS/RS, or Shuttle Rack allows for a comprehensive approach to handling and shipping a wide range of automotive components.
Deploying automation is not only about efficiency but safety as well, automated material handling systems typically facilitate a reduction in forklift traffic, providing a safer work environment.
In a competitive landscape where speed and reliability are paramount, the transition to automation is not just beneficial; it’s becoming essential.
Real-world success
For a real-world example of successful automation of an automotive parts center, read our case study on Indonesia-based MPM. Deploying a Mini Load AS/RS, STVs, and a picking system in their handling and shipping operations, MPM significantly improved their ability to handle and ship 13,000 SKUs.
K. Takahiro
Sales Planning Department, Intralogistics Division, Daifuku
Takahiro possesses extensive experience in sales and engineering of automotive production systems, having worked in this field for an extended period. He later switched his focus to Intralogistics and is currently an integral part of the Sales Planning Department, where he is actively involved in various marketing activities.