Weaving Your Way Through Apparel Material Handling
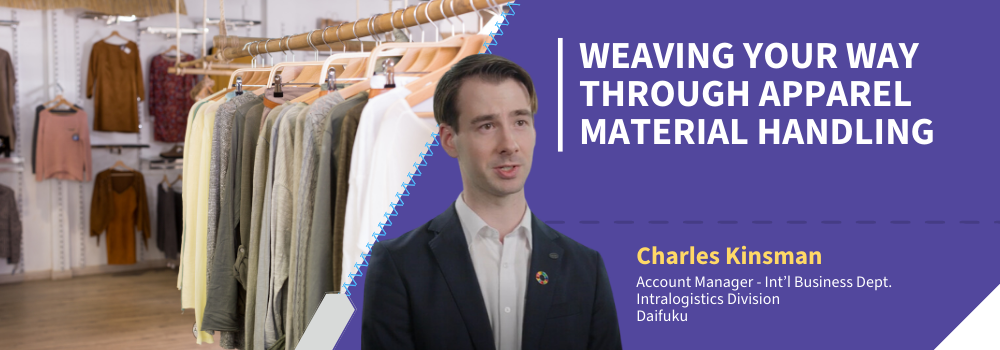
From the initial weave of fabric to delivering the final garment or footwear to customers, the global apparel industry demands unparalleled speed efficiency and quality assurance. As trends evolve rapidly and consumer expectations heighten, companies are increasingly deploying automated material handling systems in their distribution centers and warehouses. This shift not only addresses soaring demand but also helps control labor costs. In this article, we’ll explore how automated material handling technology can enhance each stage of the process—from receiving and sorting through to shipment—ultimately maximizing warehouse efficiency and enhancing overall operations.
In a distribution center or warehouse, intralogistics involves several key processes: goods are first received, unloaded, and inspected. They are then put away in storage locations using forklifts or automated systems. Products remain in inventory until needed, at which point they are picked based on customer orders using picking systems. The picked items are packed, labeled, and prepared for shipment before being loaded onto transport vehicles and dispatched to customers. Automation can enhance each stage, boosting efficiency and accuracy.
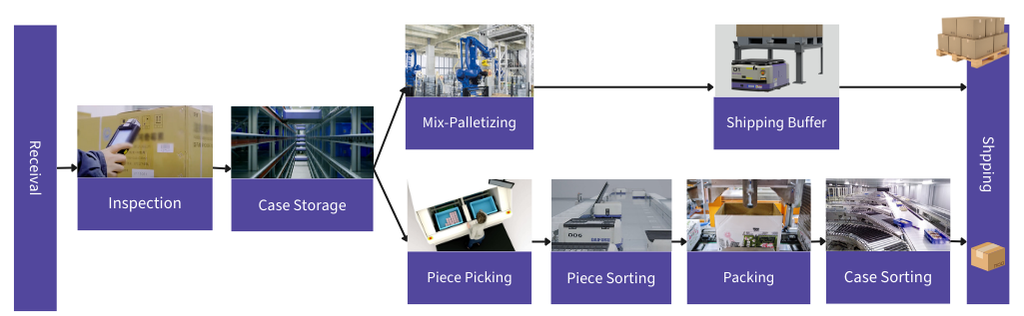
Receiving the first package
At distribution centers (DCs), goods arrive via trucks bulk loaded with boxes or cases, or pallet loaded. Bulk-loaded trucks, while dense, are less productive and benefit from automated conveyors like boom conveyors that link to the DC’s other systems, improving throughput. Palletized loads, though less dense, are more productive but require forklifts for unloading and must be depalletized for further handling. Choosing the right automated technology depends on the way goods are received for processing—pallet or case. Material handling experts can help optimize the entire intralogistics process, from inbound to outbound operations.
Storage in inventory
Once received, goods must be stored in a manner that allows for efficiency picking, consolidation, and shipment. Automated Storage and Retrieval Systems (AS/RSs) are crucial here.
For case storage—common in the apparel industry—Mini Load systems using cranes or shuttles are ideal. Shuttle-based systems offer greater sorting and sequencing functions compared to a crane-based system. These systems use shuttle vehicles, conveyors, and lifters to buffer products efficiently and automatically handle sorting and sequencing based on order batches, which streamlines later sorting and packing processes.
AS/RS solutions ensure quick and accurate storage and retrieval, even during peak seasons, meaning that stores and online customers will always get their order in good time.
Picking and sorting through each order
Stored products must be transported to picking and consolidation areas for order preparation. Whether it be for batch or piece picking, a crane- or shuttle-based Mini Load AS/RS can seamlessly integrate with other automated systems, such as picking robots or goods-to-person picking stations, to facilitate rapid and accurate picking operations.
Further, depending on whether it is a fast or slow-moving SKU there are a range of technologies that can further support operations, including pouch sorters, piece sorting systems, and put-to-light sorting systems.
GTP Picking Station
Put-to-Light System
Picking Robots
Pouch Sorter
Sorting Robots
Shuttle Rack
Packing up for shipment
Automated packing stations are enhancing efficiency in warehouses by complementing human workers. These systems, which include automated packing, labeling, and conveyor solutions, streamline operations and allow workers to focus on other value-added tasks.
This integration of automation and human labor helps achieve a balanced, efficient packing process adaptable to varying demands, crucial for industries like apparel. High-capacity sorters, such as the Slide-Shoe Sorter, are also effective for quickly sorting diverse box sizes into the appropriate shipping chute.
Automated Box Packing
Cross Belt Sorter
Slide-Shoe Sorter
Stitching it all together
The apparel industry presents unique challenges when it comes to warehouse automation. Whether the need for rapid processing to meet peak demand or optimizing storage to manage a wide range of SKUs efficiently, automated material handling systems offer significant advantages. Leveraging these technologies can lead to more efficient, cost-effective operations. For insights on how automation has transformed operations in the apparel sector, explore two of our case studies that highlight substantial improvements in efficiency and cost saving through advanced material handling solutions.
Case Study 1: Read how our approach to automation in the apparel industry has helped save costs and space, by taking a look at our case study for Sketchers USA, where our Mini Load AS/RS facilitated efficient storage and helped reduce labor by at least 50%.
Case Study 2: Logisteed East Japan’s Kashiwa Platform Center boosts efficiency with a high-throughput, automated material handling system, achieving 140% increased productivity for sports shoe logistics and sustainable 3PL operations.
Mini Load Systems
Check out our Mini Load AS/RS and Shuttle Rack M pages to learn more about two small-load handling automated storage systems.
Charles Kinsman
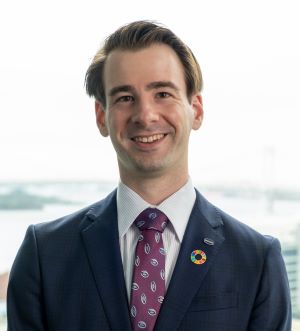
Account Manager, International Business Dept., Intralogistics Division, Daifuku
Originally from the United States, Charles relocated to Japan in 2019 after earning a degree in International Business and Japanese. Since joining Daifuku in 2023, he has played a key role in overseeing Intralogistics projects in Oceania and supporting Global Firms with their projects in Japan.