Choosing the Ideal Warehouse Automation System for Pallet Storage
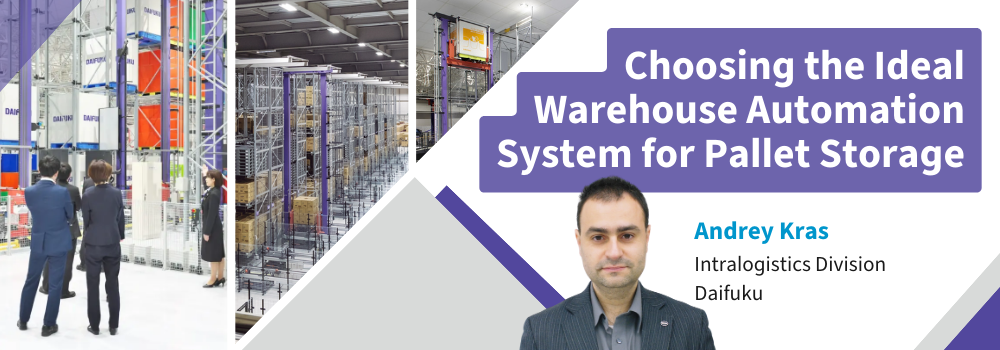
If you're grappling with inefficiencies, errors, and staffing shortages in your warehouse, automation is the solution. While many can recognize the promise of automation, one might find themselves daunted by the array of solutions on offer and their associated costs, concerned about the impact of choosing the wrong system. In this article, we’ll take a look at the differences in some of these systems, specifically, pallet storage and retrieval solutions—unit load automated storage and retrieval systems (AS/RSs).
Essential factors to consider for system selection
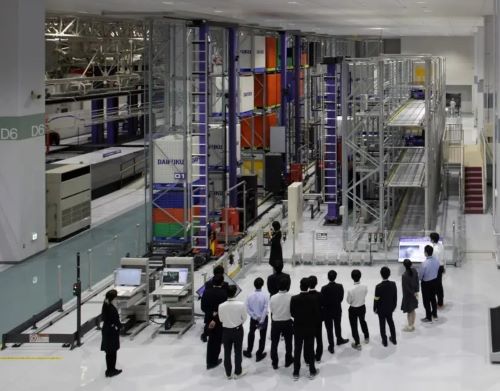
Navigation through the sea of pallet handling solutions should begin before setting sail, starting with awareness of your onsite handling and distribution situation. A clear picture, consisting of the following elements, should be shared with management and other members in the decision making process. This step is the key to determining the most optimal system for your warehouse.
- Characteristics of stored goods
-
- SKU count
- Pallets per SKU count
- Order line count per day and the busiest hour
- Shipping volume and schedules
- What is the company's annual growth rate, and what is the expected growth over the next 5 years?
- Is it possible to build a high-rise warehouse, or must the system fit into the existing low-bay warehouse?
Why these factors matter
In a nutshell, the composition of goods in your current warehouse and their behavior patterns hold the key to determining which system to choose for the future. Why is this the case?
- Pattern 1—a small but busy warehouse
- Suppose your warehouse is small, but nearly every pallet is a different SKU, and you pick items from each to create small orders. In this scenario, you need a system that retrieves the pallet for picking and then returns it to storage.
- Pattern 2—a factory warehouse
- Suppose you have 10 production lines, each producing 10 SKUs simultaneously, batch after batch. As a result, you have large volumes of homogeneous pallets that are shipped out whole from the factory. In this case, you need a completely different system, specifically a dense storage system where all identical pallets are stored tightly together in a row.
- Pattern 3—a larger distribution center
- Alternatively, suppose you have a larger warehouse with fast-moving goods in large quantities, slow-moving items with 2-3 pallets per SKU, and very slow-moving items with less than one pallet per SKU. In this case, a hybrid system is required, where different types of goods are stored and processed in different sections using various types of equipment.
The process of planning a new automated system starts at your existing warehouse. Specifically, it starts with understanding not just how many pallets are stored in your warehouse (though that is important), but (1) how many SKUs you have, (2) how many pallets are stored for each of these SKUs, and (3) how many times per hour items are picked from them (the number of order lines), as well as (4) how these figures will grow in the future. These four parameters will help you take the first steps in the right direction when choosing an automated system.
Features of pallet storage systems
The below table features the most common groups of existing pallet handling AS/RSs into a single table, outlining their main characteristics and linking them with their typical applications.
Please enlarge the screen to view
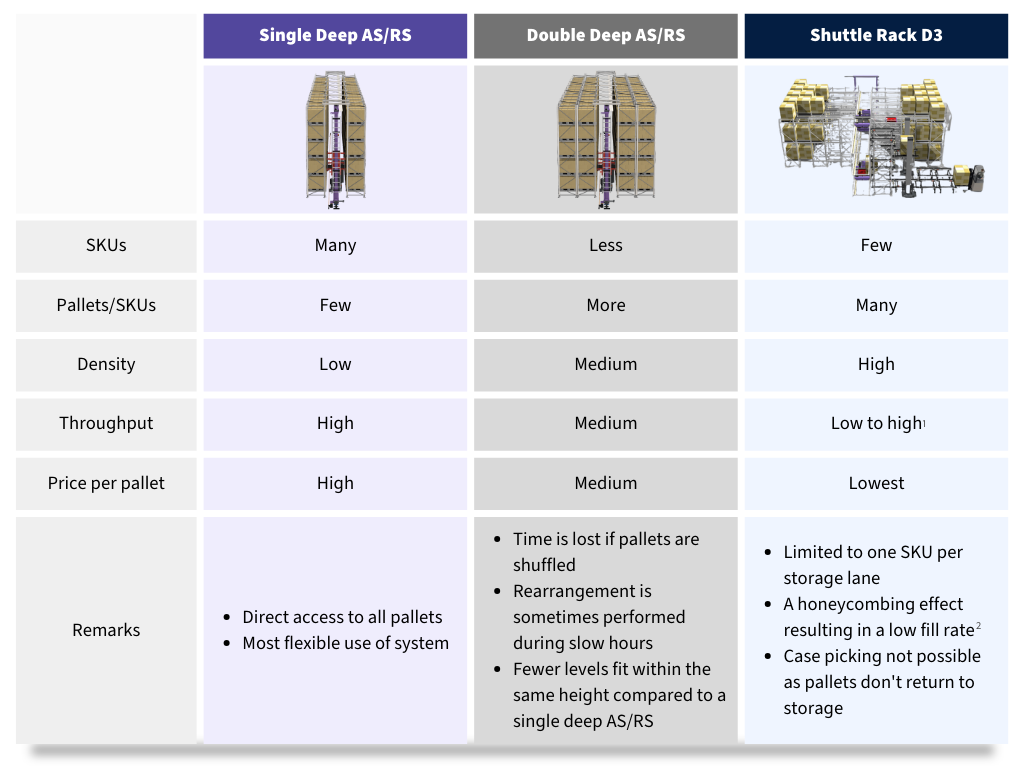
As we can see in the table, automated systems are designed to meet different needs: (1) some are for storing a relatively small number of pallets for quick small-scale picking (many order lines and small picking quantities), (2) some are for storing a larger quantity of goods with slower picking (fewer order lines and larger picking quantities), and (3) others are mainly for storing a large number of pallets that are stored and retrieved as full pallets, where case picking is either non-existent, minimal, or done elsewhere using other means.
- 1Shuttle systems can deliver high throughput, depending on the technology used.
- 2Empty spots in rack unused for storage in order not to block the stored pallets.
The foundational steeping stone
Consulting specialists to identify the ideal equipment for your business is not always necessary right from the start. Valuable insights can often be gleaned from assessing your existing warehouse setup, serving as a foundational stepping stone for your journey.
Recognizing these insights is paramount in pinpointing the appropriate equipment, facilitating a fruitful and constructive dialogue with a specialist. A seasoned professional can meticulously scrutinize your warehouse, often surpassing your own understanding, to ascertain its intricacies.
From initial assessment to final implementation, a specialist will expertly guide you through the selection process, from consulting through to after-sales service, ensuring the chosen system aligns seamlessly with your business objectives. For a detailed overview of the Daifuku approach to project handling with customers, check out our Total Solution Experience page.
Andrey Kras
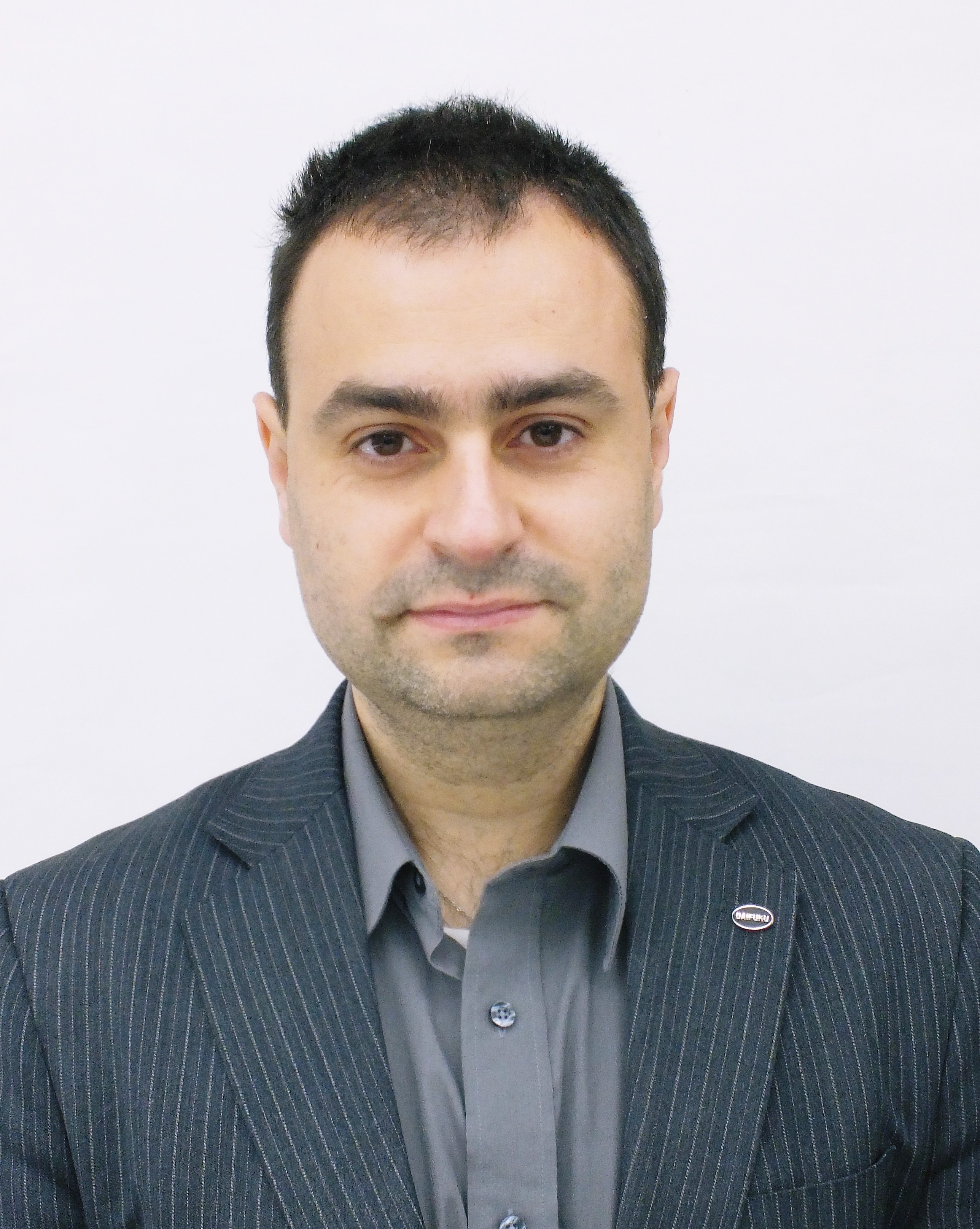
Intralogistics Business, Daifuku
Born and raised in Russia, Andrey was educated in Japan and earned a PhD from Waseda University in 2008. After several years as a business consultant, he joined Daifuku in January 2012 as a sales manager. His responsibilities include warehousing and intralogistics consulting as well as marketing.