How Automation is Meeting the Challenges of Today’s Supermarkets
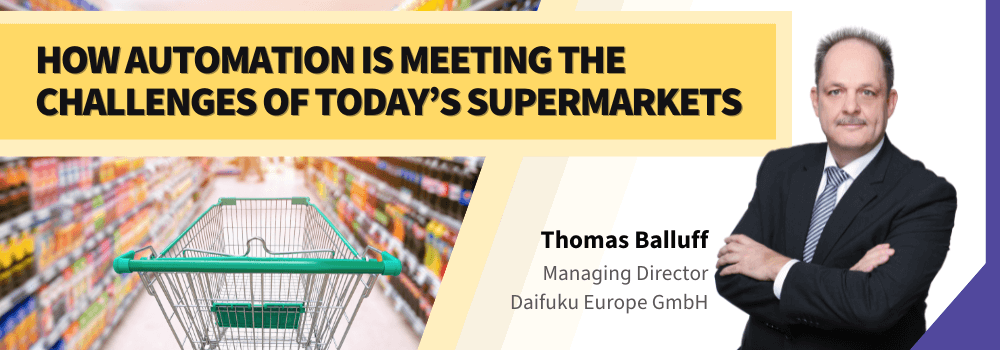
Supermarkets are leading the way when it comes to automation in ambient, chilled and cold chain environments. Thomas Balluff, managing director of Daifuku Europe, looks at some of the main technologies that are driving efficiencies in today’s retail outlets.
Within the European grocery sector, the term ‘automation’ can include a wide range of technologies including the use of robots to process, pack and sort items, conveyor systems in distribution centres and even self-scan systems within supermarkets. In this article, we will focus on the key external drivers encouraging the adoption of automated systems such as automated storage and retrieval systems (AS/RS) and how this flexible technology is evolving to meet the challenges of the modern retail environment.
The changing world
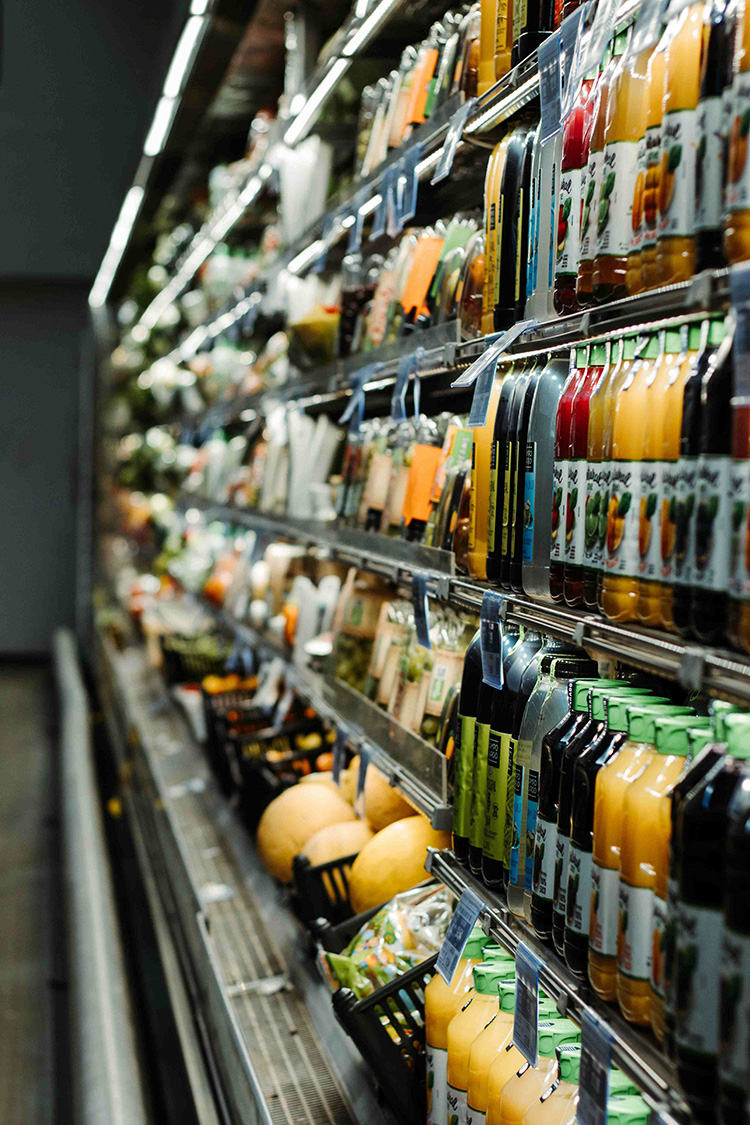
The world is changing faster than ever before – and this includes supermarket retailing. Issues such as our aging population, safety at work, the demand for more ethical products and people’s mobility are all having a huge influence on the way we shop. External factors such as fragile supply chains, urbanization and climate change are other developments that are having a profound influence on the supermarket sector which is often a pioneer when it comes to the adoption of flexible and innovative logistics concepts.
This ethos also applies to the intralogistics operations of supermarket chains. In the past, common warehouse and picking tasks were carried out manually or semi-automatically. Concepts such as man-to-goods or goods-to-man were developed, but the fulfillment of in-store pallets was still done manually, due to the variation of SKUs and number of goods.
In recent years, the chronic shortage of skilled workers coupled with increasing workplace health and safety legislation, has acted as a catalyst for change in the area of automated processes.
The challenge of temperature
From an automation perspective, supermarket warehousing represents particular challenges for logisticians, due to the fact that most distribution centres are divided into different temperature zones. In addition to deep-freeze and refrigerated areas, there are also ambient storage locations which are usually sub-divided by type of good. These wide differences in temperature have significant implications for the type of technology that can be considered in each warehouse environment.
Another challenge facing warehouse managers considering automation is the sheer variety of SKUs that need to be handled, which can include cartons, plastic containers and trays, stretched PET bottles and glass. Not only are the varying dimensions of the items a challenge, but their weights also need to be carefully considered.
Delivering the goods
In our experience, the key success factors in food and, by association, cold chain logistics are the intelligent application of automation and the efficient delivery of products at every stage of the retail supply chain.
Automation is fundamental to the future success of the supermarket sector as it solves labour shortages by removing the need for personnel to work in a challenging cold environment. In the dispatch area, it also facilitates faster order preparation which increases capacity, perishable goods freshness and customer satisfaction. Well planned automation also helps prevent food loss which is often brought on by inefficient inventory management.
Unlike sites that rely on manual fulfillment, automated facilities can work continuously and thus deliver tangible efficiencies 24/7. Using today’s state-of-the-art automation is also remarkably energy efficient, by maintaining cold air flow and minimizing loss.
Automation also helps achieve efficient delivery by supporting a range of material handling operations, such as replenishment storage, de-palletization, collation storage, palletizing (mixed-case palletizing), and sequential and grouped shipping. This results in automatically sequenced and optimally dimensioned pallet loads that reduce transport volume and streamline operations.
-
Mixed-case palletizing
-
The robot arm automatically detects the optimal position to stack boxes
Energy efficiency built-in
Such a nuanced and complex set of requirements needs a highly flexible, sophisticated technology that can operate in a range of temperatures. In these days of sustainability and high energy costs, new automation that is designed with the environment in mind has a huge advantage.
For the storage of goods, Daifuku uses high speed automatic stacker cranes which include built-in energy recovery as standard. Energy generated by the stacker cranes during movement and braking is fed back into the power supply grid and can be used for other operations. This ingenious system reduces power consumption and contributes to the organization’s corporate social responsibility.
Utilizing the flexibility of Daifuku’s Shuttle Rack M, goods are sequenced for the subsequent packing process, immediately creating supply chain efficiencies. This storage system delivers a remarkably high throughput and has up to 60% reduced energy consumption compared to conventional stacker cranes. Once the goods are automatically and precisely placed on the load carrier (pallet or roll container), they are ready for dispatch to the supermarket floor.
The palletizing robot uses optimization algorithms to ensure a stable packing pattern which also increase packing density. Subsequently, the pallet is automatically wrapped and prepared in the goods dispatch area. For packing processes that cannot be automated due to the nature of the product, manual ergonomic packing stations take over this task.
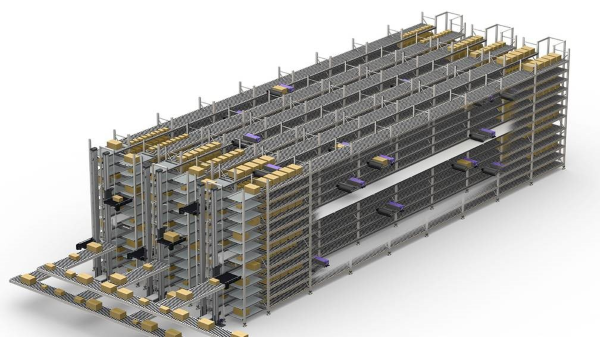
The future is flexible
More sophisticated automation is a major trend currently being seen within the retail sector. As influences such as urbanization, sustainability and a shortage of manual labour (especially in cold storage areas), continue to challenge retailers, their adoption of more flexible technology has increased. The adoption of fully automated systems also enables supermarkets to fully realize the potential of their warehousing footprint. Our experience in Japan and Europe proves again and again that the use of AS/RS systems allow the same amount of product to be stored in a facility that is half the size of a conventional warehouse.
Specifically, the ability to manage mixed-case palletization without manual intervention is now becoming an essential element within the supermarket supply chain. Even better, automation can now optimize energy consumption and reduce costly handling interventions, thereby offering a more rapid return on investment for warehouse managers.
Thomas Balluff
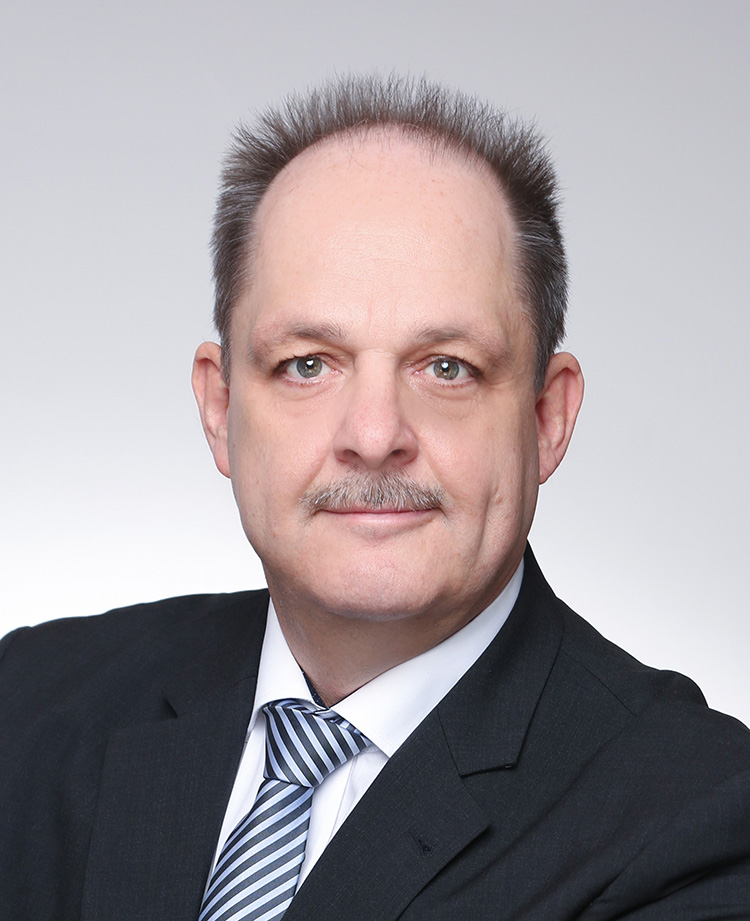
Managing Director, Daifuku Europe GmbH
Thomas Balluff holds more than 30 years of experience in intralogistics. In 2006 he joined Daifuku as the sales manager for Central and Northern Europe. Since 2010, he has been branch manager for Daifuku’s Intralogistics branches in Europe, and became managing director of Daifuku Europe GmbH in 2021.