ダイフク流課題解決新車型対応を支えるドア自動取付システム(いすゞ自動車株式会社様)
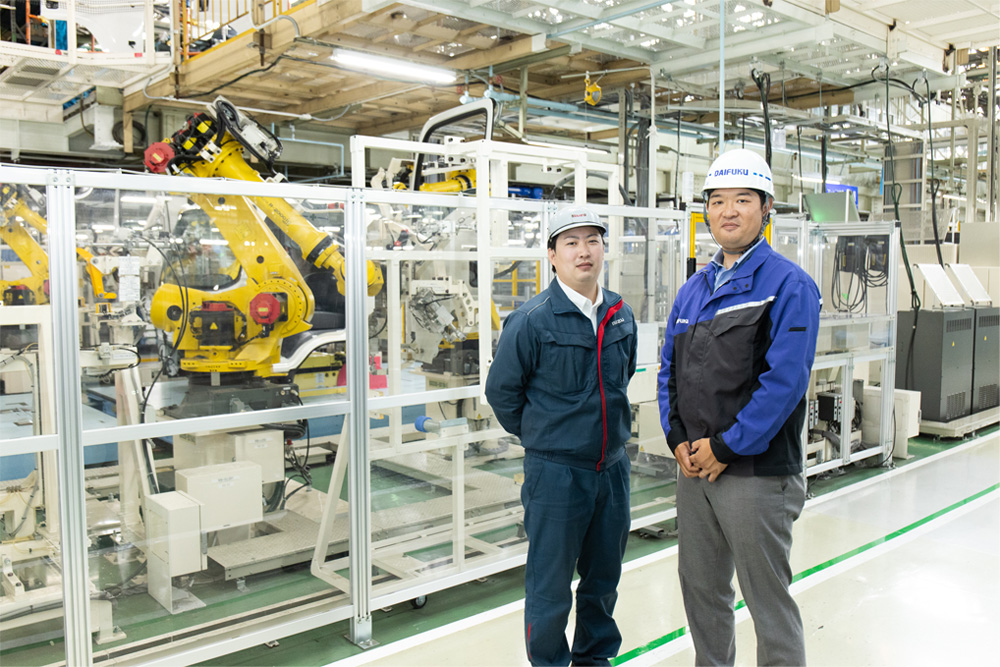
商用車の国内トップシェアを誇るいすゞ自動車株式会社様(以下敬称略)。同社の栃木工場では主にエンジンを製造し、それ以外の製造や組立を含む生産工程は神奈川県の藤沢工場が担っています。1962年操業開始の藤沢工場ではこれまでも時代に合わせて設備更新を実施しており、2022年夏にドアの自動取付システムを更新しました。同社車両技術部 キャブ組立グループの植木裕介様(写真左)と、本件を担当したダイフク オートモーティブ事業部の林勇佑係長(写真右)がこの新システムの導入で何が変わったのかをご紹介します。
藤沢工場ではエンジン製造以外のほぼすべてのプロセスを担っているそうですね。
植木(敬称略) ここでは大型・中型・小型トラックの組み立てを行っており、研究施設も併設しています。敷地面積は約82万m2で、端から端まで歩くと約20分かかります。敷地内には4つの工場建屋があり、第一工場はプレスや溶接、塗装など、第二工場はキャビンの艤装(ぎそう)と車両の組立、第三工場と第四工場はアクスル(車軸)やトランスミッションなどのパワートレインの製造をそれぞれ手掛けています。
第二工場で行う艤装とはどういった作業ですか。
植木 キャビンにフロントガラスやシート、インストルメントパネルなどの部品を取り付けることや、ドアを取り付けることも艤装の一種です。第一工場では金属を加工してキャビンとドアのフレームを作り、ドアを取り付けた状態で最後に塗装を実施して第二工場に送ります。しかし、艤装を行う際にドアがあるとキャビンの内側の作業がしにくいですし、ドアにも窓ガラスや開閉システム、各種スイッチなどを取り付ける作業を行わなければなりません。そこで、第二工場では艤装ラインの入り口でキャビンからいったんドアを外し、キャビンとドアを別のラインに流してそれぞれの艤装を行ってから再合流させ、キャビンにドアを再度取り付けています。今回はこのドアを自動で取り付けるシステムを更新しました。
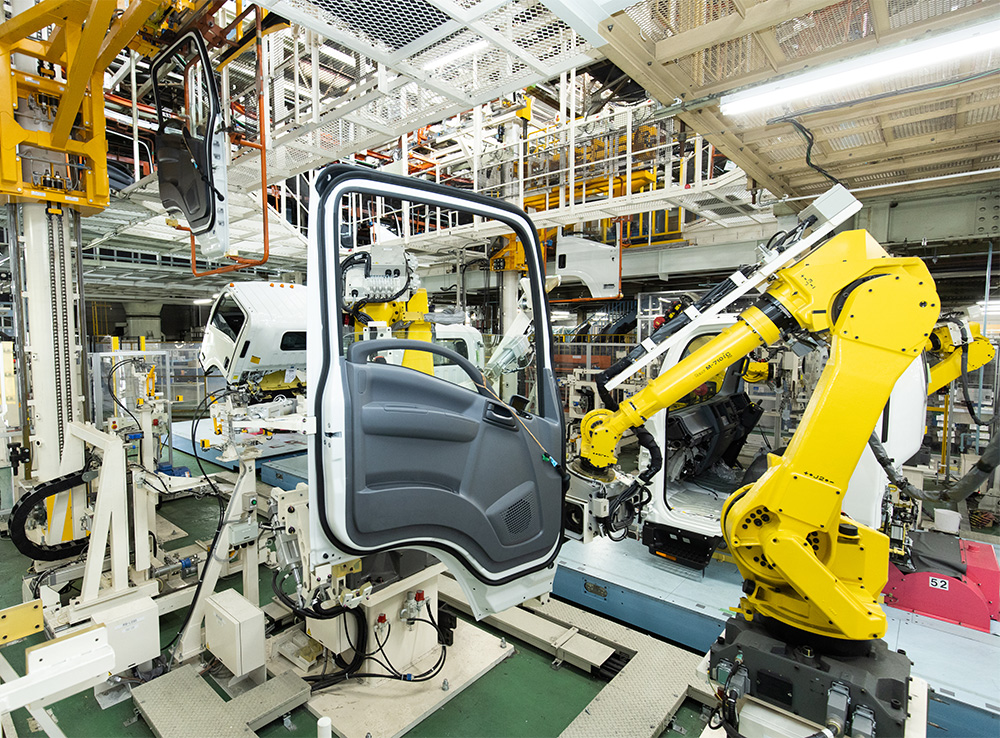
ドアとキャビンが別ルートで流れると、工場内のラインは複雑になるのではないでしょうか。
植木 ドアを外したキャビンは1階のラインを流れていき、外されたドアはリフターで持ち上げられて、中二階のドアサブラインで艤装を行います。このドアサブラインはダイフクさんのシステムです。導入から約30年が経っていますが、長期運用に耐え得る品質は素晴らしいと思っています。そのほかのラインにもダイフクさんのシステムが入っており、普段からお付き合いがあったことから、ドア自動取付システムの更新の際にも相談しました。
新車型への柔軟な対応と生産性の向上を目指し
システム更新を考え始めたきっかけは何でしたか。
植木 理由は2つあります。1つは設備の能力を高めて生産効率の向上を図ることです。自動車業界は変革期の真っただ中にありますから、市場の変化に対応していかなければなりません。生産拠点は効率の向上を常に考えているので、ごく自然な発想だったと思います。
もう1つは、ドア取り付け時の開閉角度を見直した新車型に対応させるためです。従来のドアは、取り付け時には90度近く開き、出荷前に追加で部品を取り付けて70度で出荷していました。それを今回、部品点数の削減などの改善を行うため、取り付け時から開閉角度を70度にした車型の開発に乗り出しました。それまで使っていたドアの自動取付システムでは70度に対応できなかったので、2021年の春頃からシステム更新を本格的に考え始めました。
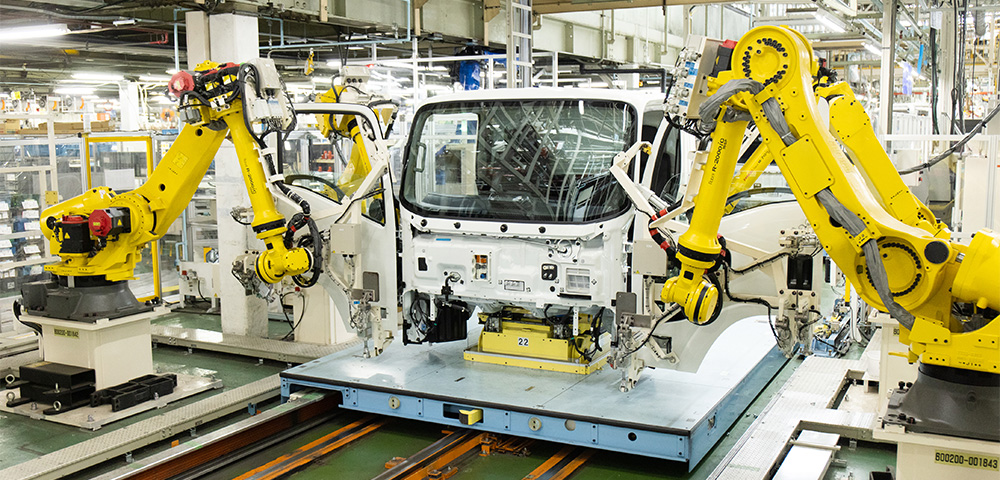
片側に2台、両側で計4台のロボットがある。1台がドアを掴み、もう1台が固定位置の特定と固定作業を担う。
90度と70度で、それほど違うものなのでしょうか。
植木 大きく違いますね。ドアを取り付ける際には内側からロボットアームを入れてボルトを締めるのですが、開閉角度が70度になるとアームが動ける範囲が一気に狭まります。狭い範囲での作業でドアや車体に傷がつけば出荷できませんから、厳しい条件下でも安全かつ確実に取り付け作業ができるシステムが必要でした。
もう1つこだわったのは、キャビンの位置決めをなくすことでした。これまでは、コンベヤで搬送されてきたキャビンがドアの自動化工程に入ったところでキャビンの位置を正していたのですが、これではサイクルタイムとしては時間がかかってしまうので、この工程の生産性を高めたいと思っていました。
ドアの開閉角度70度への対応
20度の違いが大きな課題
ドア開閉角度70度への対応と、サイクルタイムの短縮が2大テーマだったわけですね。
植木 どのようにしたらそれが実現できるのか、複数のメーカーさんに相談したところ、各社ともさまざまな技術やアイデアを提案してくださいました。その中で我々が必要とする情報を的確に提供してくれたのがダイフクさんでした。
例えば、キャビンの位置決めをやめると、ナットホールの位置が毎回変わってくるため、より高性能なカメラやセンサーなどが必要になりますが、すべての要求を満たす万能ツールは存在せず、どれも一長一短がありました。ダイフクさんは各製品の特徴や組み合わせの相性、その組み合わせを提案する理由など、技術的な観点から一目で比較検討できる資料を提供してくれました。この資料は社内稟議を通す場面でも非常に役立ちました。
実は、ドア自動取付システムは、設備更新の際に同じ第二工場内で設置場所を変えることが決まっており、ダイフクさんには先にドアサブラインの改修の相談をしていました。その流れでドア自動取付システムも相談したところ、提案内容がすばらしく、ドアの搬送から自動取付までを一括で依頼すれば品質がさらに上がるのではという期待もありました。
また、問い合わせに対する対応も好印象でした。返信のスピードは各社とも差がありませんでしたが、ダイフクさんは回答が的確かつ迅速で、技術部門と営業担当者の連携体制ができていて風通しの良さを感じました。
新しいドア自動取付システムの設置場所を変更したのはなぜですか。
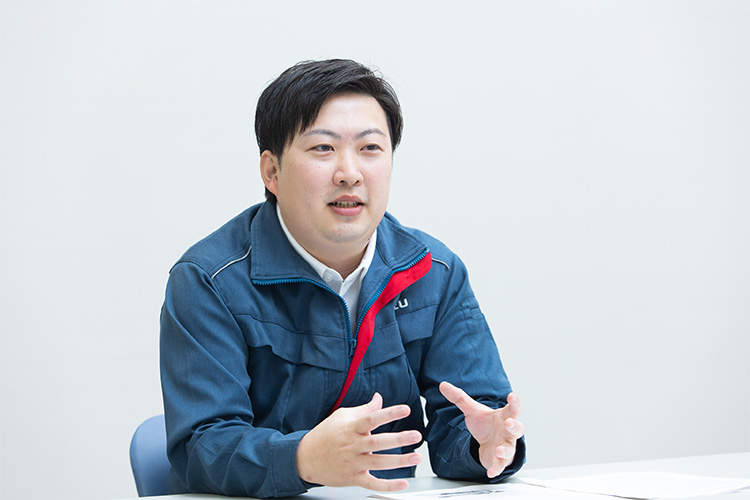
植木 並行生産のためです。稼働中の工場では設備更新のためとはいえ簡単には生産を止められませんので、もともとの設備を動かしながら新設備の設置工事を進める必要があります。先に行ったのは中二階のドアサブラインから1階の自動取付システムへとドアを供給するドロップリフターの設置工事でした。作業は工場が休みの土曜と日曜に限定されており、日曜は月曜からの生産に影響が出ないように早めに作業を切り上げて生産用設備の試運転を行わなければならず、そのためのスケジュール調整や工程管理に苦労しました。
ドロップリフターの設置工事と並行して、新たなドア自動取付システムの要件定義や設計を進めました。打ち合わせはほぼ毎週で、ダイフクさんからの質問や確認事項に我々が回答するといったやり取りを2カ月ほど続けた後、図面と3Dデータをいただきました。それを社内でチェックし、懸念事項を洗い出して修正していただきながら、最終的な図面が仕上がりました。
設計において特に苦労したのはどういった点でしたか。
植木 ダイフクさんとのやり取りが最も多かったのはナットランナー・マテハンです。ドアの自動取付システムでは、ロボットアームの先端に取り付けたナットランナーというボルトを自動で締め付ける工具を取り付けたものです。新車型への対応でロボットアームの可動範囲が狭くなる中でも、キャビンやドアに当たらない設計にしてほしいとお願いしました。
林 狭い環境でも動かせるナットランナーがないかをメーカーさんに相談したところ、既製品では対応できないとの回答でした。そこで当社は3Dデータを使ってナットランナーのヘッドを薄くしたりブラケットの形状を工夫したりするなどの検討を重ね、独自の形状を開発し、メーカーさんに提案しました。そのナットランナーが採用され、ゆとりが2~3mmしかない場所でも安全に作業できるシステムができました。
想定していた効果を実現
今後も多様な車型に挑戦
それだけ厳しい条件となると、カメラやセンサーを含めたシステム全体の設計も難易度が高かったのではないでしょうか。
植木 「ナットランナーをフローティングさせてズレを微調整できる仕組みにしてほしい」という要望への対応も大変だったのではないかと思います。ナットランナーはボルトを組み付け用の穴に差し込みますが、位置がずれるとボルトが斜めに入ってしまいます。そうなると人が手作業で直すしかなく、場合によってはドアそのものを交換しなければなりません。旧設備でも多少は動くようにしていましたが、新設備ではもっと柔軟に動くようにしたいと考えました。ただし、最初からユラユラと動くとナットランナーがボルトをうまく持ち上げられないという別の問題が生じるので、フローティングはボルトを穴に押し込むときだけになるよう、何度も設計のやり取りをさせていただきました。
林 このあたりは位置決めの問題と関わってきます。旧設備ではキャビンをいったん引き上げて位置を正してからドアの取り付け工程に入りましたが、今回はコンベヤに載せたままでドア取付作業を行うため、キャビンの位置にばらつきが出るのは避けられません。そこで、最新のシステムを導入し、位置補正機能を強化しました。
ボルトを入れる穴の位置の特定にはカメラを使用しますが、旧設備で使っていたカメラは決まった場所しか撮影できず、キャビンの位置がぶれると正確な情報を得られません。我々が想定したのは1つのロボットにカメラを持たせ、その情報をもとに2つのロボットの位置を定める制御システムです。条件に合うカメラを求めて複数のメーカーにあたりましたが、既存の製品にはなく、その中の一社と連携して新しいカメラシステムとして開発しました。
固定位置をカメラで特定し(左)、ドアを取り付ける(右)
今回の設備更新では新しい試みも多数盛り込まれていますから、実際に稼働するまでは不安もあったのではないでしょうか。
植木 当社では設備更新の際には必ず実際に稼働させての試運転をお願いしています。3Dデータを使ったシミュレーションで問題がなくても、実際に動かしてみると何かしら不具合や改善点が見つかることがあります。本稼働後に問題が見つかると、修正するにも作業時間や手法で制約が出てきますから、そういった事態を避けるために事前のテストをお願いしているのです。今回は2022年2月にテストしていただきました。実際に動いているところを見たときは、「オーダー通りのことができていて、すごい」と思いましたし、多少の修正箇所はあったものの、非常に完成度が高かったです。
本稼働が始まって間もなく1年ですが、順調でしょうか。

植木 サイクルタイムを短縮するという目的をクリアし、新車型にも問題なく対応できているので、計画段階で想定していた効果は十分に得られています。自動車業界が変化している中で、当社は今後もさまざまな車型に挑戦することになるでしょう。生産現場はその変化に対応していく必要があり、今回の設備更新でキャビンの位置決めをなくせたことは大きな意味があると思います。工場全体としても、より柔軟に対応できる体制を整えていきたいので、ダイフクさんにはまたご相談したいと思っています。
林 当社は近年、従来の搬送システムだけでなく、ロボット化への対応も強化しています。そうした中で今回の新システム導入は当社としてもチャレンジが多く、いすゞ自動車さまには新しいアイデアや提案を行いやすい環境を整えていただき、ありがたかったです。今後とも多様化する自動車業界の自動化ニーズに応えていきますので、よろしくお願いいたします。
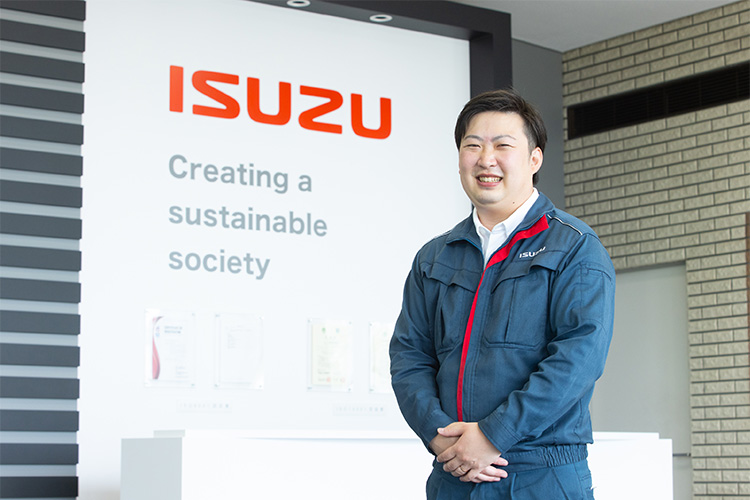
いすゞ自動車株式会社
車両技術部 キャブ組立グループ
植木 裕介 様
2014年、いすゞ自動車株式会社入社、製造部に配属。保全課など複数の部署を経験したのち、2016年にキャブ組立グループに異動。大型・中型・小型トラックの組み立てを行う神奈川県の藤沢工場に勤務。