Coca-Cola Bottlers Japan Inc.
การเพิ่มประสิทธิภาพเครือข่ายการจัดจำหน่ายและการขายผ่านระบบอัตโนมัติแบบ end-to-end ขั้นสูง
ในเดือนกุมภาพันธ์ พ.ศ. 2564 Coca-Cola Bottlers Japan Inc. (CCBJI) ได้เริ่มดำเนินการที่ Saitama Mega DC ที่เพิ่งสร้างใหม่ในบริเวณโรงงานในไซตามะ โรงงานแห่งนี้มีพื้นที่จัดเก็บและขนส่งที่ใหญ่ที่สุดแห่งหนึ่งของ Coca-Cola ในญี่ปุ่น
ตั้งแต่เดือนพฤษภาคม พ.ศ. 2559 บริษัทได้เข้าร่วมใน "โครงการ Shinsei" ซึ่งมีจุดมุ่งหมายเพื่อเพิ่มประสิทธิภาพเครือข่ายโลจิสติกส์เพื่อให้สามารถตอบสนองต่อสภาวะตลาดที่เปลี่ยนแปลงไปและความต้องการที่หลากหลายของผู้บริโภคได้รวดเร็วยิ่งขึ้น โดยมุ่งสร้าง "คุณภาพสูงและต่ำ -ต้นทุนและห่วงโซ่อุปทานที่มั่นคง"
Saitama Mega DC ก่อตั้งขึ้นโดยเป็นส่วนหนึ่งของโครงการดังกล่าว และดำเนินการเป็นศูนย์กลางการขนส่งหลักสำหรับพื้นที่โตเกียวและจังหวัดไซตามะ
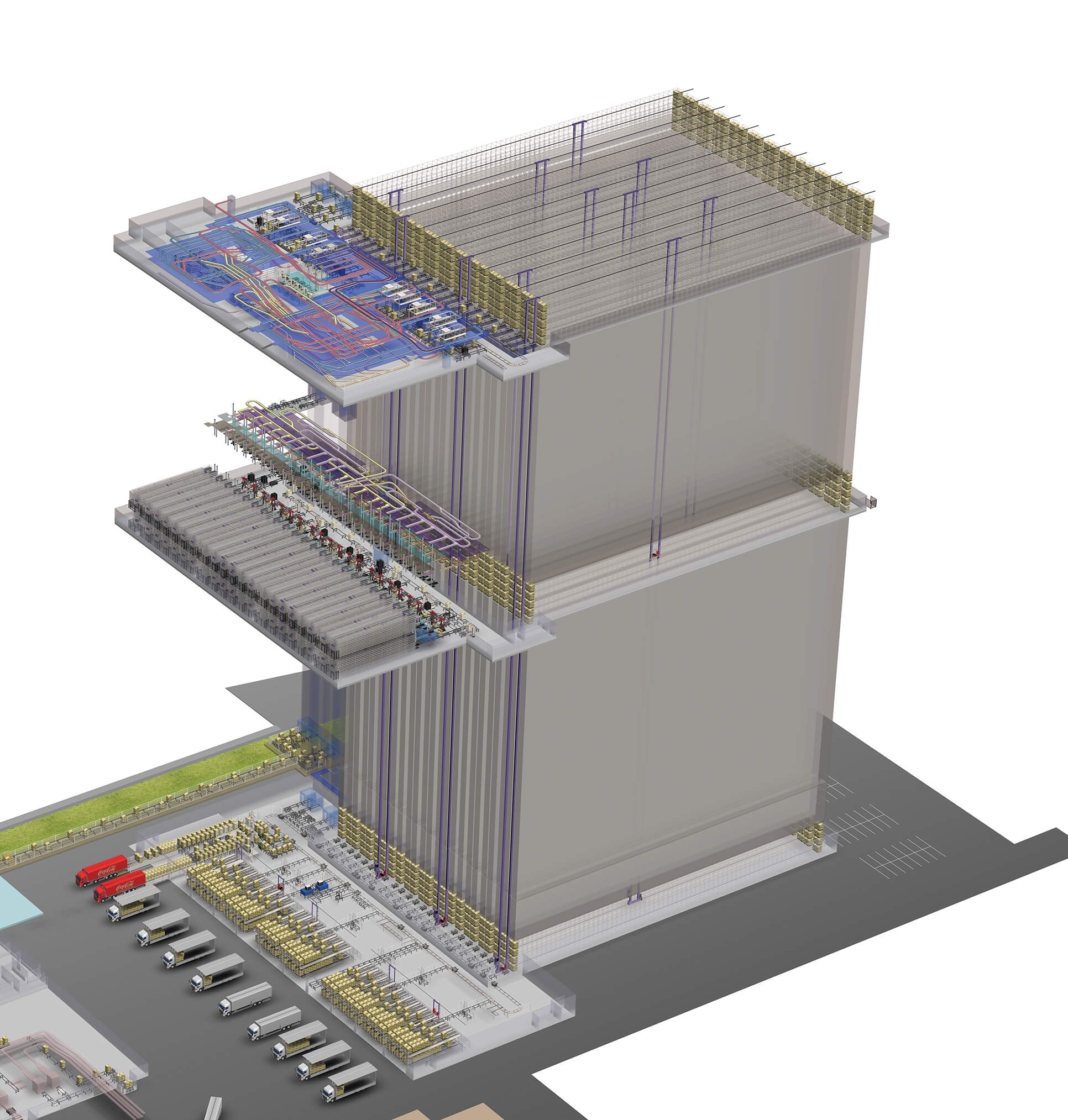
การรวมกระบวนการลอจิสติกส์ให้ประสิทธิภาพที่เพิ่มขึ้น
ศูนย์กระจายสินค้าขนาดใหญ่นี้รวมไซต์โลจิสติกส์ของ Coca-Cola ที่มีขนาดเล็กกว่า 24 แห่งภายในโตเกียวและไซตามะ และรวมเอาการคัดแยกสินค้า การหยิบสินค้า และกระบวนการด้านลอจิสติกส์อื่นๆ ทั้งหมด รวมทั้งคลังสินค้าและพื้นที่จัดเก็บ การจัดการทั้งสินค้าที่ผลิตในสถานที่และสินค้าที่ผลิตในโรงงานอื่น ไซตามะ เมกะ ดีซี จัดเก็บและจัดส่งผลิตภัณฑ์โคคา-โคลา ซึ่งรวมถึงผลิตภัณฑ์เรือธงระดับโลกอย่าง โคคา-โคลา ไปยังซูเปอร์มาร์เก็ต ร้านสะดวกซื้อ ร้านขายยา หรือแม้แต่ตู้จำหน่ายสินค้าอัตโนมัติ .
ไซต์งานประสบความสำเร็จในการจัดการวัสดุอัตโนมัติแบบครบวงจรผ่านอุปกรณ์หลากหลาย รวมถึงระบบจัดเก็บและเรียกคืนอัตโนมัติแบบโหลดหน่วยลึกสองเท่า (AS/RS) และ Shuttle Rack M สำหรับการจัดเก็บ การคัดแยกยานพาหนะขนส่ง (STVs); หุ่นยนต์วางบนพาเลทและนำออกจากพาเลท และสถานี RORO (โรลออน/โรลออฟ)
นอกเหนือจากการส่งมอบประสิทธิภาพที่ดีขึ้นในการดำเนินงานด้านลอจิสติกส์แล้ว โรงงานแห่งนี้ยังสร้างเครือข่ายที่บรรลุการส่งมอบผลิตภัณฑ์แบบครบวงจรในเวลาที่เหมาะสมตั้งแต่การผลิตไปจนถึงลูกค้าโดยตรงและเครื่องจำหน่ายสินค้าอัตโนมัติ
“Saitama Mega DC นั้นก้าวหน้าพอๆ กับไซต์โลจิสติกส์ของ Coca-Cola อื่น ๆ และฉันก็จะบอกว่ามันอยู่ใน 10 อันดับแรกของระบบอัตโนมัติที่ Coca-Cola มีทั่วโลก” Bruce Herbert หัวหน้าซัพพลายเชนแสดงความคิดเห็น เจ้าหน้าที่ ที่ CCBJI
ในแง่ของการไหลเวียนของลอจิสติกส์ที่โรงงาน ผลิตภัณฑ์จะเข้าสู่คลังสินค้าด้วยวิธีใดวิธีหนึ่งจากสองวิธี ทั้งโดยตรงจากโรงงานในไซต์งานหรือผ่านรถบรรทุกขนส่งที่บรรทุกสินค้าจากไซต์การผลิตอื่น ผลิตภัณฑ์ที่ผลิตในไซต์งานจะถูกวางบนแท่นวางก่อนที่จะบรรทุกเข้าคลังสินค้า โดยจะรวมผลิตภัณฑ์บนพาเลทที่ผลิตในไซต์อื่น พาเลทที่จัดส่งไปยังคลังสินค้า โดยแต่ละพาเลทจะเก็บเฉพาะประเภทผลิตภัณฑ์ในคราวเดียว จะถูกขนส่งไปยังชั้น 3 ด้วยสายพานลำเลียง รถยก และรถขนย้าย (STV) อย่างไรก็ตาม ในกรณีที่จำเป็นต้องจัดส่งผลิตภัณฑ์อย่างเร่งด่วน ก็สามารถโหลดพาเลทที่เกี่ยวข้องได้ เข้าไปใน AS/RS ผ่านชั้น 1 สินค้าที่จะวางบนพาเลทเป็นพาเลทผสมจะถูกส่งไปยังชั้น 3 และแยกย่อยเป็นกล่องๆ ผ่านเครื่องแยกพาเลท จากนั้นขนส่งโดยสายพานลำเลียงไปยังระบบ Shuttle Rack M บนชั้น 2 เพื่อจัดเก็บชั่วคราว
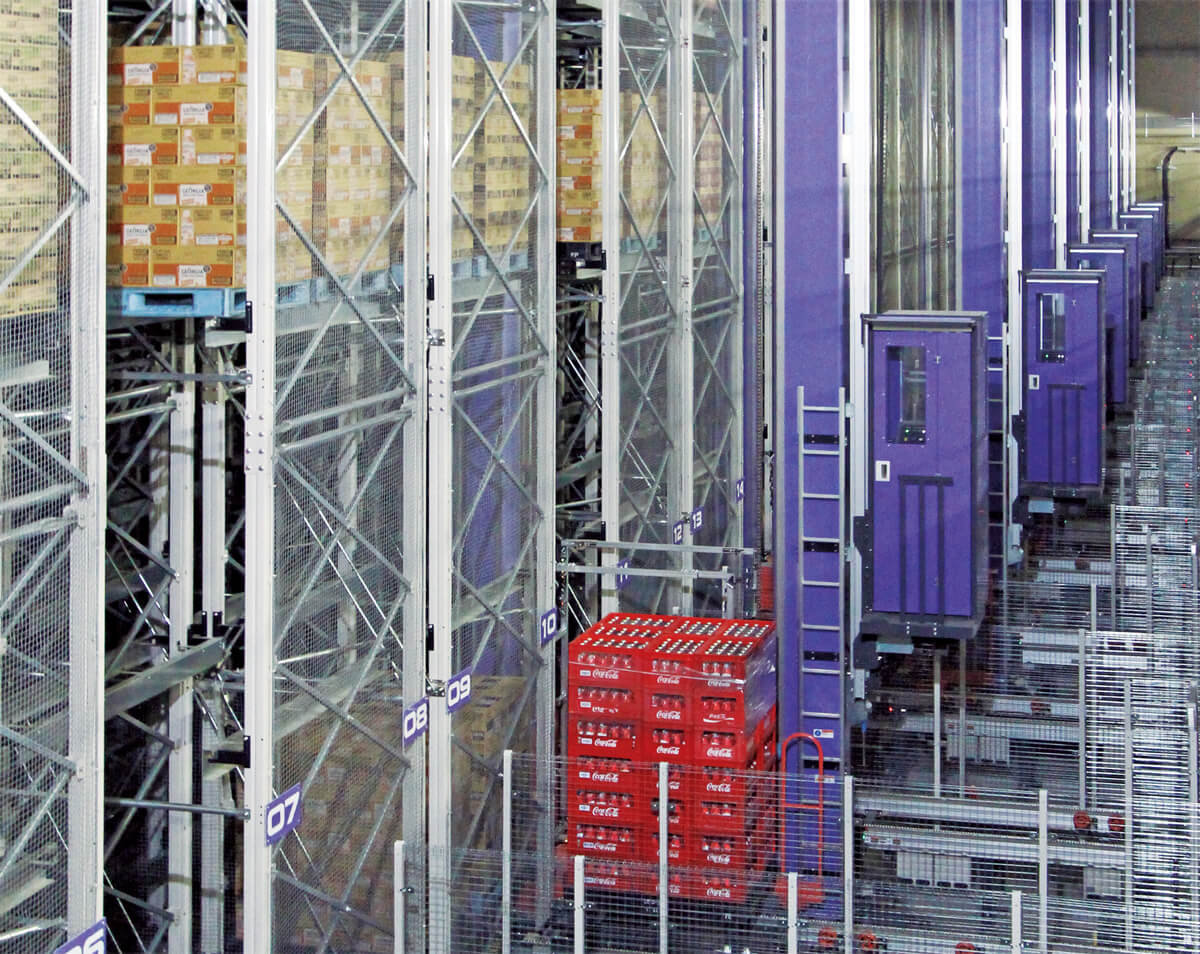
เมื่อพร้อมที่จะวางบนพาเลทและจัดส่ง กล่องต่างๆ จะถูกดึงออกจาก Shuttle Rack M และขนส่งไปยังหุ่นยนต์วางบนพาเลทหนึ่งใน 21 ตัวที่อยู่บนชั้นเดียวกัน หุ่นยนต์จะหยิบกล่อง กระเป๋าพลาสติก และลังพลาสติกที่มีรูปร่างและขนาดต่างกันอย่างรวดเร็ว แล้วบรรจุลงในพาเลทโหลดแบบผสม
ตามธรรมเนียมแล้ว ล็อตผสมจะต้องถูกส่งออกผ่านโรงงานของโคคา-โคลาหลายแห่ง แต่ด้วยการติดตั้งหุ่นยนต์จัดเรียงพาเลท บริษัทสามารถรวมงานนี้เข้ากับไซตามะ เมกะ ดีซี ซึ่งทำให้ประสิทธิภาพเพิ่มขึ้นอย่างมาก
เมื่อพาเลทโหลดแบบผสมเสร็จสิ้นแล้ว พวกเขาจะถูกส่งไปยังเครื่องห่อแล้วส่งไปยังพื้นที่จัดส่งที่ชั้นหนึ่งโดยใช้ STV และรถยก
ที่พื้นที่จัดส่ง รถ STV และรถ stacker cranes จะบรรทุกพาเลทเข้าในช่องทางการจัดเตรียม ซึ่งประกอบด้วยชั้นวางแบบเอียงหลายขั้นตอนที่สามารถรองรับรถบรรทุกหนึ่งคันสำหรับแต่ละปลายทาง เมื่อรถบรรทุกมาถึงหน้างาน งานขนถ่ายจะเริ่มขึ้น
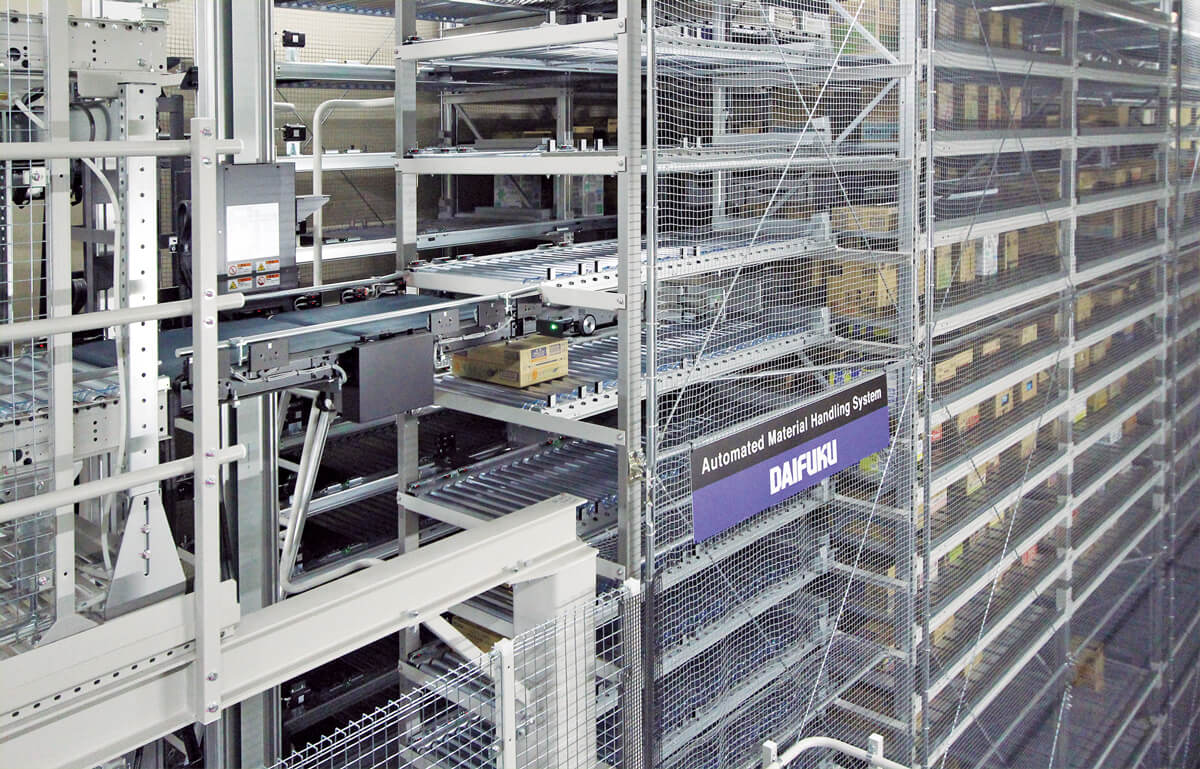
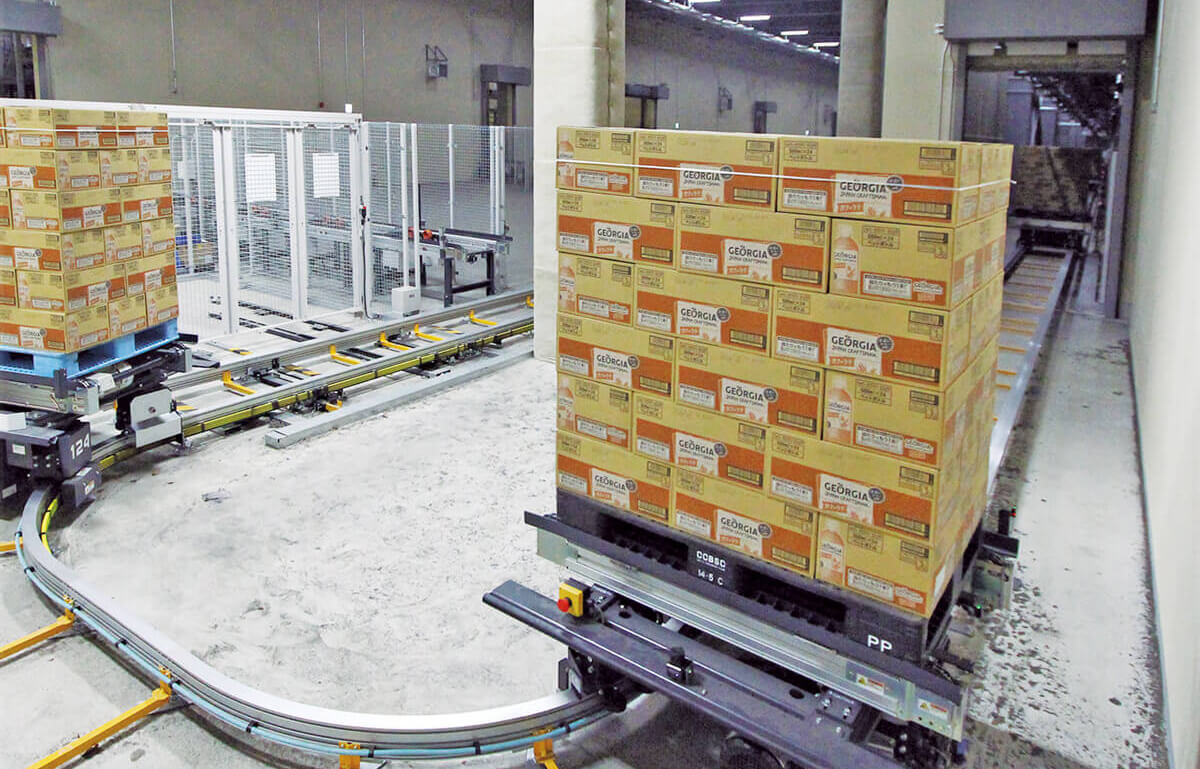
การขนถ่ายรถบรรทุกอัตโนมัติช่วยลดการขนถ่ายที่จำเป็นลงเหลือหนึ่งในสาม
ในพื้นที่เลนแสดงละคร สถานี RORO สองแห่งซึ่งเป็นสถานีแรกในญี่ปุ่น ทำการโหลดและขนถ่ายรถบรรทุกเป็นชุดโดยอัตโนมัติอย่างสมบูรณ์ การใช้รถยกใช้เวลาประมาณ 60 นาทีในการโหลดรถบรรทุกหนึ่งคัน แต่ RORO สามารถทำได้ภายใน 20 นาทีเท่านั้น
อันเป็นผลมาจากการใช้งานระบบอัตโนมัติในวงกว้าง โรงงานแห่งนี้สามารถขนส่งสินค้าได้มากถึง 85 ล้านกล่องต่อปี
Saitama Mega DC ได้ช่วยอำนวยความสะดวกในห่วงโซ่อุปทานที่มีคุณภาพสูงและมีเสถียรภาพ และคาดว่าจะกลายเป็นพื้นฐานสำหรับการเติบโตอย่างยั่งยืนของระบบ Coca-Cola ในอนาคต
“ตอนนี้ เราไม่ได้ดำเนินการคลังสินค้าเพียงแห่งเดียว แต่จริง ๆ แล้วเรากำลังดำเนินการเครือข่ายในลักษณะที่แยกจากกันในอดีต ซึ่งให้ประสิทธิภาพในวงกว้าง เริ่มจาก Saitama Mega-DC เรากำลังค่อยๆ เปลี่ยนจาก แบบดั้งเดิมไปจนถึงแบบขั้นสูง” แสดงความคิดเห็นเฮอร์เบิร์ต
สถานี RORO – ส่งมอบประสิทธิภาพการบรรทุกสูงสุด
สถานี RORO (โรลออน/โรล-ออฟ) ทำการโหลดและขนถ่ายรถบรรทุกเป็นชุดโดยอัตโนมัติ ซึ่งไม่เพียงแต่ช่วยลดเวลาในการขนถ่ายของรถบรรทุกเท่านั้น แต่ยังช่วยเพิ่มความคล่องตัวในการปฏิบัติงานและลดปริมาณการใช้รถยก ซึ่งช่วยเพิ่มความปลอดภัยในสถานที่ทำงาน
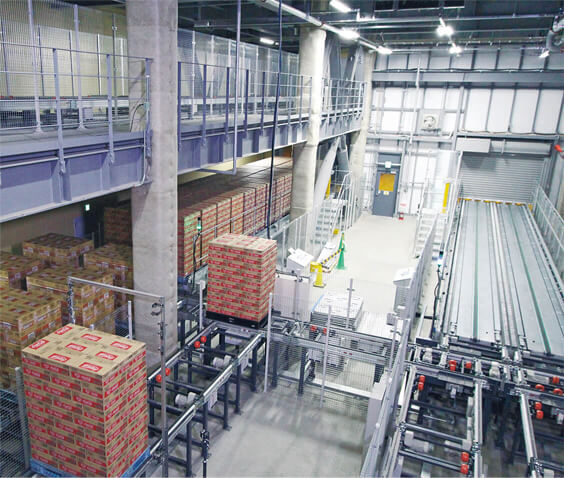
ภาพรวมระบบการจัดการวัสดุ
AS/RS | ชนิดลึกสองเท่า เครนยกซ้อน: 12, ที่เก็บพาเลท: 60,000 ตำแหน่งพาเลท รวมถึง 15,000 พาเลทในคลังสินค้าที่มีอยู่ |
---|---|
Shuttle Rack M | 21 ระบบ 462 คัน 74,000 เคส |
Sorting Transfer Vehicle | 1F: 24 ยูนิต, 2F: 3 ยูนิต, 3F: 15 ยูนิต |
depalletizer ชั้นออกจากพาเลท | 8 ยูนิต |
หุ่นยนต์จัดเรียงสินค้า | 21 ยูนิต |
สถานี RORO | 2 ระบบ |
เลนสเตจ | 100 เลน |
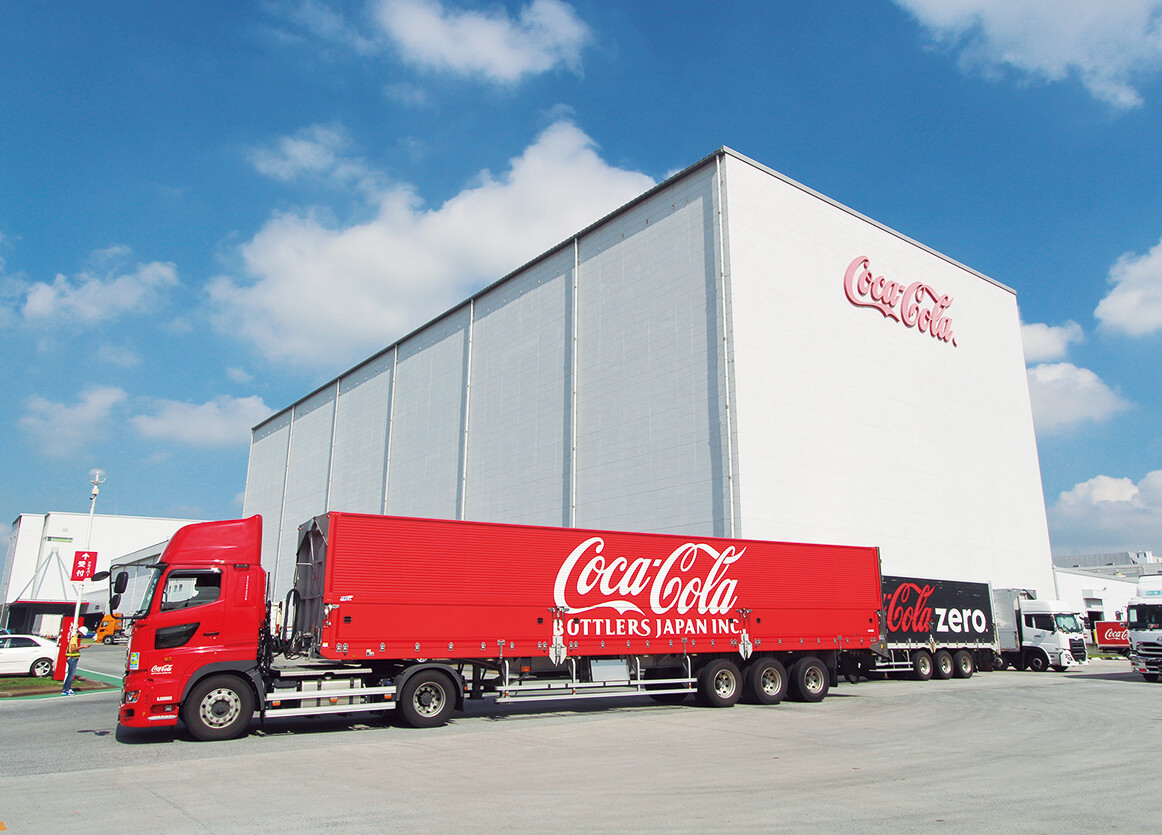
ภาพรวมไซตามะ Mega DC
ที่ตั้ง: 943-1 Shimohosoya, Yoshimi-machi, Hiki-gun, จังหวัดไซตามะ Coca-Cola Bottlers Japan Inc. โรงงานในไซตามะ
พื้นที่อาคาร: 14,747m 2
พื้นที่ชั้น: 23,548m 2 (3 ชั้น)
เริ่มดำเนินการ: กุมภาพันธ์ 2021
ติดต่อเรา
ติดต่อสอบถามสินค้าได้ที่หน้า Contact Us
ติดต่อเราติดต่อเรา
ติดต่อสอบถามสินค้าได้ที่หน้า Contact Us
ติดต่อเรา