社会インフラを支えるダイフクの技術小型化と急速充電を両立したワイヤレス充電システム「D-PAD」
工場や物流センターの自動化に欠かせないAGV(無人搬送車)やAMR(自律走行搬送ロボット)を安定稼働させるには、電池切れを防ぐことが重要になります。人手不足が進む中で、充電作業の自動化も大きな課題です。そこで当社は、ワイヤレス充電システム「D-PAD(ディー・パッド)」の大幅な小型・軽量化を実現し、低床式AGVなどにも装着できるようにしました。さらに、最大100Aでの急速充電ができるモデルも発売。作業の合間にたびたび充電する「ちょこちょこ」充電を可能にし、作業効率の向上に貢献します。システムのポイントなどを開発者であるCR事業部 生産本部 パワーデバイス部の布谷 誠さんと、同部HIDグループの二宮 大造さんが紹介します。
「D-PAD」はどのようなシステムですか。
D-PADはAGVやAMRなどに装着することで、そのバッテリーにワイヤレスで自動的に充電するシステムです。
工場や物流センターで稼働しているAGVを安定稼働させるためには、電池切れを未然に防ぐことが重要です。しかし、バッテリー交換には手間と時間がかかるため、人手不足に悩む工場や物流センターでは最近、その作業を自動化するシステムが求められています。プラグなどを用いた接触式の充電システムも実用化されていますが、充電中は些細な振動でもスパークするリスクがあり、火災につながることもあります。
こうした問題を解決したシステムがD-PADです。D-PADを活用すれば、工場の組み立て工程や物流センターのピッキング工程といった、AGVが一時停止する場所に充電ステーションを設け、停止中に継ぎ足し充電することで、電池切れを心配することなく、AGVを24時間安定稼働させることが可能になります。
技術的な特長はどのような点にあるのでしょう。
D-PADは、コイルとフェライトによる電磁誘導を利用して発生させた電力を、共振回路を活用することで、離れた場所にあるバッテリーに効率よくワイヤレスで電力を伝送するものです。その原理は古くから知られていましたが、通常の円形コイルを用いた電磁誘導システムの場合は、長い距離を伝送するためには大型のコイルが必要で、AGVなどに装着することは難しかったのです。
その欠点を克服したのがD-PADで、独自のD型のコイルを採用したことが最大のポイントです。D型コイルを活用すれば、同サイズの円形コイルに比べて伝送距離を延ばすことが可能になり、D-PADでは、円形コイルを用いた同サイズのシステムに比べて伝送距離を約2倍に延ばすことができました。充電ステーションに設置した送電パッドとAGVに装着した受電パッドが、約3cm離れていても充電することが可能です。(100Aモデルは6cm)
画面を拡大してご覧下さい。
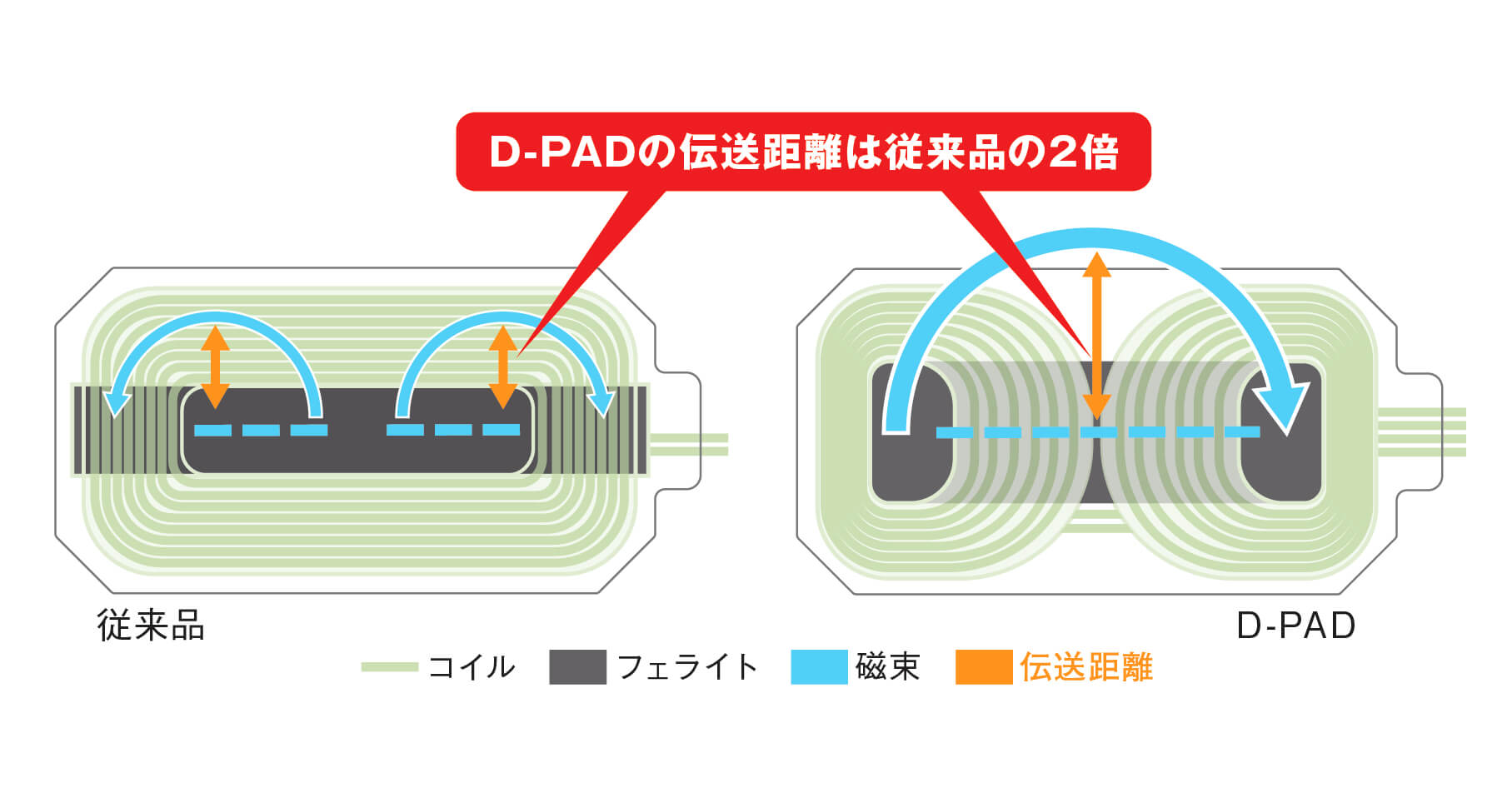
ワイヤレス給電モノレール式搬送システムの実用化はダイフクが世界初
開発の経緯を紹介してください。
当社は1992年にワイヤレス給電技術に関してニュージーランドのオークランド大学と提携し、1993年に世界初のワイヤレス給電モノレール式搬送システムを実用化しました。そのワイヤレス給電技術を応用して当社が開発した充電システムがD-PADです。充電ステーション停止時に、「①D-PADインバーター」から高周波電流を「②送電パッド」に流し、電磁誘導を利用して「③受電パッド」に電力を伝送、その電力を「④充電コントローラー」でバッテリーなどの蓄電システムに充電するというのがD-PADの構成です。
2013年に大型のAGV向けに販売を開始し、2016年には通常のAGVにも搭載できるようにシステム全体を小型化したD-PADを開発しました。2019年4月に発売した新型モデルは、そのD-PADの「充電コントローラー」を大幅に小型化したものです。寸法は約17×23×7cm、従来モデルに比べ体積比で約60%小型化しました。重量比でも、約70%軽量化しています。
画面を拡大してご覧下さい。
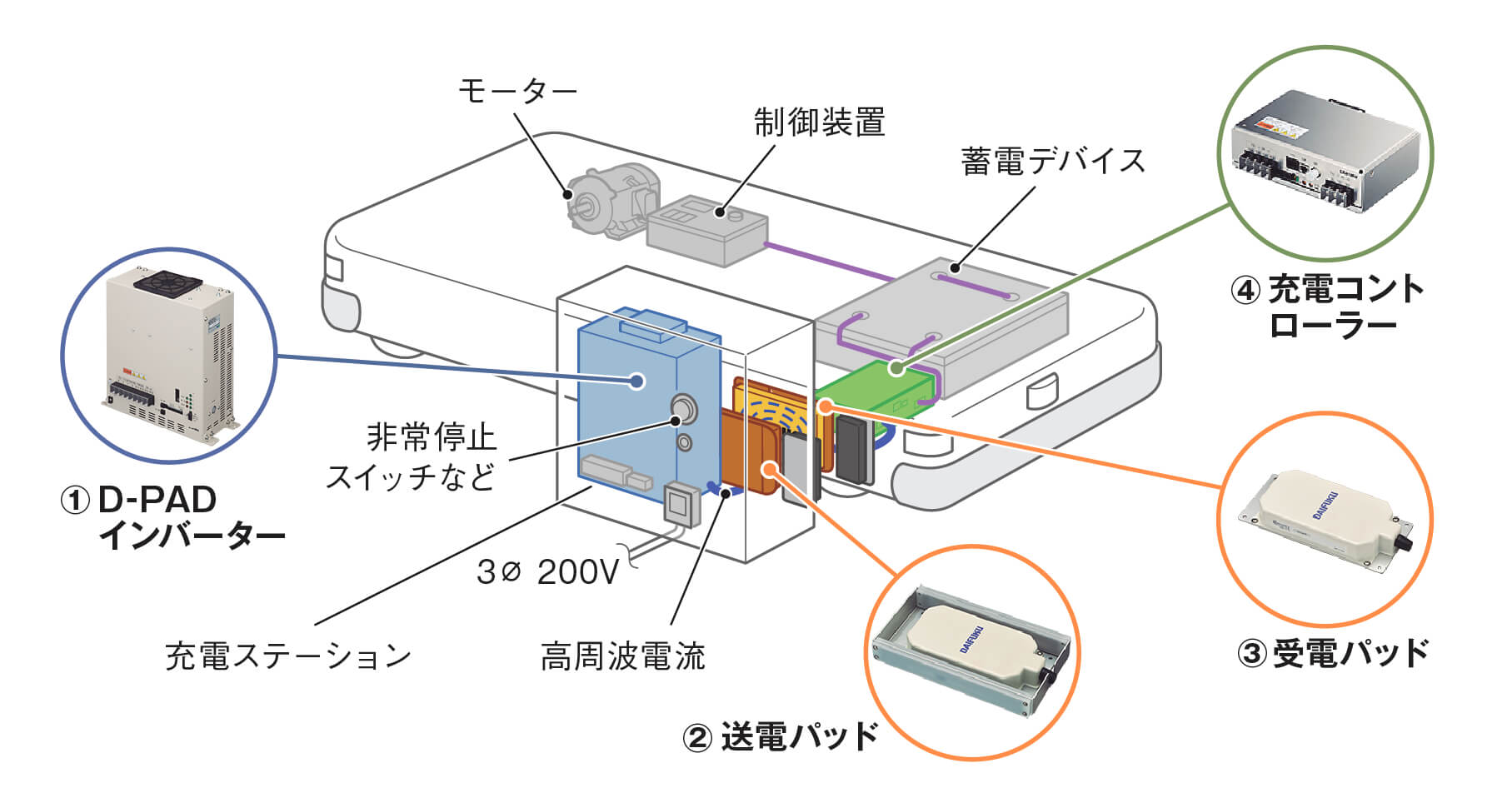
なぜ小型化したのですか。
小型化したのは、近年、工場や物流センターで多く用いられるようになった低床式のAGVやAMRにも対応するためです。
D-PADを活用するには、AGVやAMRの表面に受電パッドを取り付けると同時に、内部に充電コントローラーを組み込まなければなりません。しかし、低床式AGVやAMRといった小型の搬送機器は内部の空きスペースが少なく、充電コントローラーを組み込むことが難しかったのです。小型化したことで、現状のAGVやAMRを設計変更しなくても、充電コントローラーを組み込むことが可能になりました。
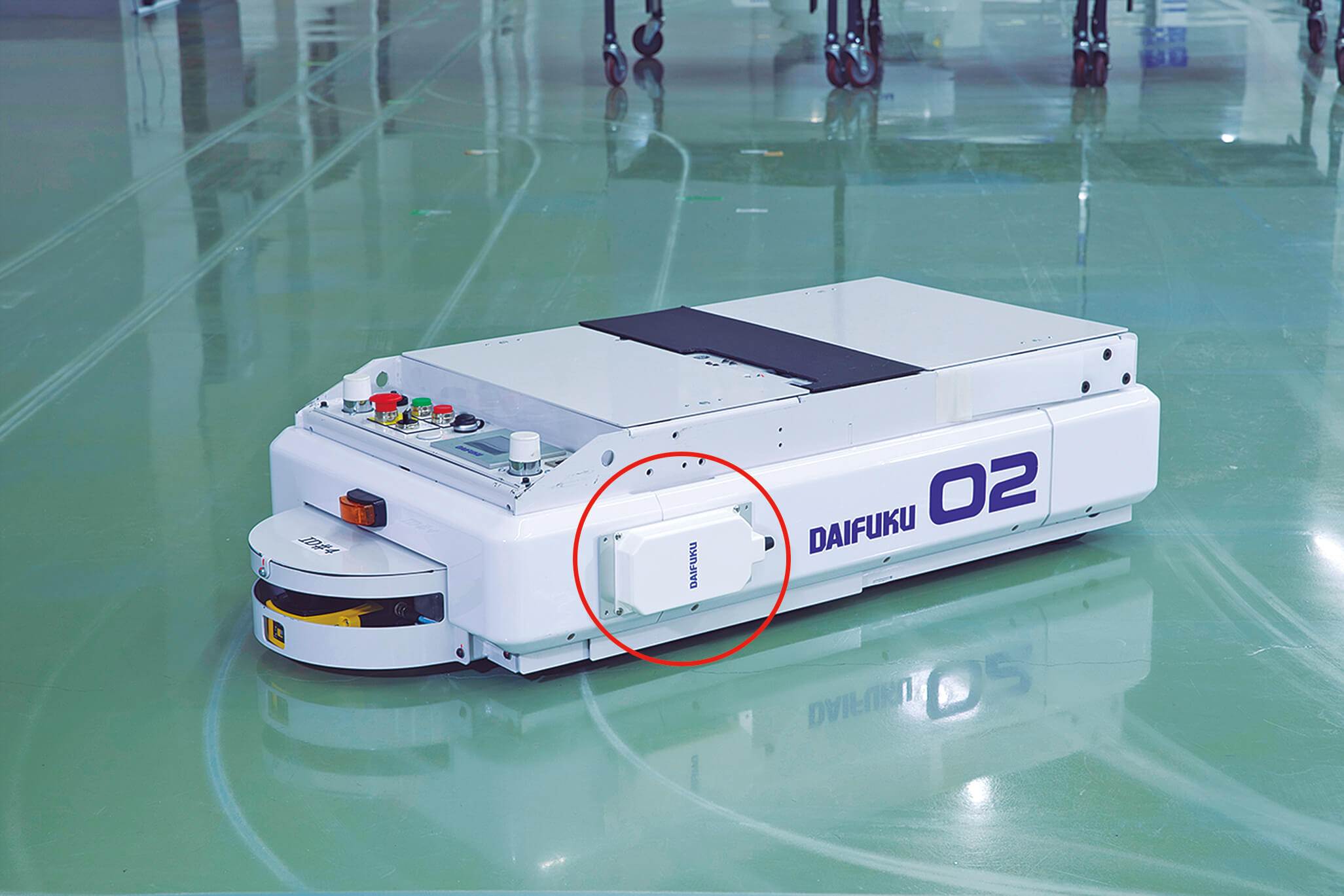
AGVに装着した「D-PAD」。AGV内部に組み込む「充電コントローラー」を従来モデルに比べ、体積比で約60%小型化したことで、低床型のAGVにも装着可能になった。
どのようにして小型化を実現したのでしょうか。
さまざまな工夫を凝らしていますが、1つは冷却システムの変更です。充電コントローラーは高熱を発生するので、冷却システムは欠かせません。
従来モデルは、D-PADを半導体工場などのクリーンルームで使用することも想定し、ルーム内の空気をかくはんしないようにフィンを使った冷却システムを組み込んでいました。一方、今回のモデルは一般の工場や物流センターで稼働するAGVやAMRなどにターゲットを絞り、ファンを活用した冷却システムに変更したのです。そのほか、制御周波数の高速化、風洞の工夫などにより、大幅な小型化を実現しました。
充電コントローラーの機能面の特長を紹介してください。
AGVで使用されるバッテリーは多様ですが、ユーザーの手元でパソコンから充電設定を変更できるようにしており、標準品でさまざまな電圧・電流・バッテリー種別に対応することが可能です。
送・受電パッドが近接したり、ずれて急激に磁束を変化させたりした場合でも、充電電流が変化してバッテリーを破損させない機能も搭載しています。
どのような顧客層を想定しているのでしょうか。
ダイフクとしては、当社のAGVにD-PADを装着して販売するのではなく、充電システム単体で販売します。現在稼働中のAGVやAMRに後付けで組み込むことも可能ですので、こうした搬送機器のエンドユーザーに向けても積極的に展開していきます。
電力容量を100Aに引き上げたモデルも開発し省資源化に貢献
100Aモデルはどのような経緯で生まれたのでしょうか。
近年、活用され始めたAMRの上にロボットを載せたモバイルマニピュレータは、AMRとロボットの両方で電力を使用することから消費電力量が多く、充電のためにAGVが頻繁に停止し稼働率が低下したり、充電時間が長いと充電ステーションを占有してしまったりという課題がありました。そのため、移載やピッキング作業のために停止した時に充電を行う「ちょこちょこ」充電のニーズが高まっていました。そこで当社は、作業の合間に十分な充電を行うため、急速充電が実現できるよう電力容量を100Aに引き上げた新型モデルを開発しました。
開発にあたってはどのような課題がありましたか。
作業の合間に「ちょこちょこ」充電を行うと、送電する側では1カ所で何十台ものAGVに対して1日数千回もの充電を行うことになります。産業用途では大きめといえる100Aで電流を作り出して、繰り返し充電を行うと、熱収縮の問題で送電パッドにクラックが入ったり、絶縁が阻害されたりする恐れがあります。そのため、設計の難易度は高まりますが、シンプルな構造の半導体を使用したり、絶縁材料を追加・変更して熱収縮の問題に対応しました。
またモバイルマニピュレータは、ロボットのアームが動くと本体も振動しますので、充電中の距離が遠くなったり近くなったりして受電パワーが大きく変動する上に、アームの動作による負荷変動があります。一方でリチウムイオン電池への充電出力は高精度化が必要ですし、このような装置に搭載されるリチウムイオン電池は電池保護のため、充電電流を突然カットすることもあります。そのため、高精度で電流と電圧制御を行いながら、高速での応答をいかに両立させるかに工夫を凝らしています。
「ちょこちょこ」充電は、頻繁にバッテリーを充電しますので放電深度を低く使うことができます。そうすると、バッテリーの生涯のエネルギー充放電量を無駄なく使用できますので、省資源化にもつながります。当社では新製品やシステムの開発によって、持続可能な社会の実現に貢献してまいります。
- ※当記事は広報誌「DAIFUKU NEWS No.224」(2019年7月発行)掲載の「開発担当に聞く 新技術のポイント」および新たに取材した内容を再構成したものです。