Mahindra & Mahindra
Lager- und Sequenzierungs-Regalbediengerät-System für lackierte Fahrzeugkarosserien
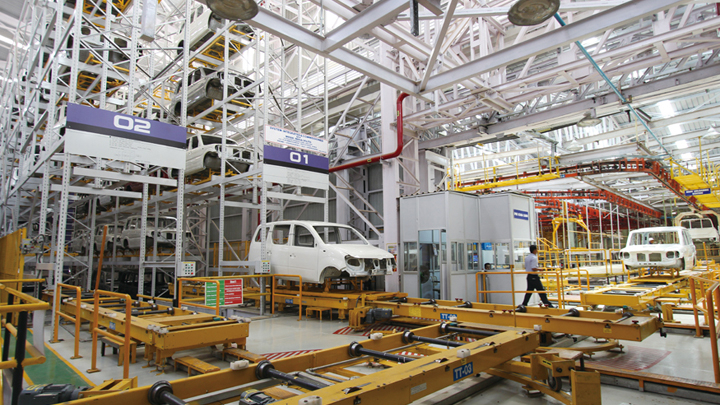
Der indische Automobilhersteller Mahindra & Mahindra Ltd. (M&M; Hauptsitz in Mumbai, Maharashtra) stellt Sport Utility Vehicles (SUV) und leichte Nutzfahrzeuge (LCV) sowie andere Fahrzeuge her. Im Juni 2013 führte M&M im Werk Nashik ein Unitload-Regalbediengerät als Puffersystem für lackierte Fahrzeugkarosserien ein. Das Puffersystem speichert lackierte Fahrzeugkarosserien zwischen und ordnet sie durch Auslagern in Montagereihenfolge, sodass verschiedene Fahrzeugtypen in einer Linie montiert werden können. Das Puffersystem erhöht die Produktivität bei der Bereitstellung von Fahrzeugkarosserien am Montageband und verkürzt die Taktzeit in der Produktion drastisch. Darüber hinaus werden Montageteile, die zuvor über die gesamte Anlage verteilt waren, an einem Ort neben der Montagelinie in dem nun offenen Raum zusammengefasst, der durch die Installation des Regalbediengerät entstanden ist.
Geschichte von Mahindra & Mahindra
M&M, ein Kernunternehmen des Mischkonzerns Mahindra Group, wurde 1945 als Mahindra & Mohamed, ein Stahlhandelsunternehmen, gegründet. 1947 änderte Mahindra & Mohamed seinen Namen in das heutige Mahindra & Mahinda und stieg mit der lizenzierten Produktion des Jeeps in das Automobilherstellungsgeschäft ein.
Mittlerweile betreibt M&M sechs Werke in Indien. Das 1980 in Betrieb genommene Werk in Nashik produziert fünf Fahrzeugtypen, darunter die Hauptmodelle Scorpio und Xylo, mit einer jährlichen Produktionskapazität von 200.000 Fahrzeugen.
Anpassung der Verschiebungsdifferenz zwischen der Lackierstraße und der Montagelinie
Ein Puffersystem fungiert als Kernfunktion beim Ausgleichen der Differenz zwischen der Dreischicht-Lackierstraße und der Zweischicht-Fertigungsstraße.
Das bisherige Puffersystem bestand aus Förderbändern, die Fahrzeugkarosserien lagerten und entsprechend den Auftragsanweisungen vom Montageband abholten. Die Anlieferung einer Fahrzeugkarosserie an das Montageband dauerte bis zu 30 Minuten. Darüber hinaus nahm das bisherige System zu viel Platz ein. Um diese Probleme zu lösen, wurde ein neues Puffersystem mit Regalbediengerät eingeführt.
Die Abrufzeit wurde drastisch auf nur 2 Minuten verkürzt. vs. original 30 min.
Das neue Puffersystem verkürzt die Abrufzeit drastisch von 30 Minuten auf zwei Minuten. Dies verkürzte die Fertigungszykluszeiten und sparte außerdem Stellfläche durch die Verwendung vertikaler Lagerung, wobei fast die gleiche Lagerkapazität wie beim vorherigen System beibehalten wurde.
Darüber hinaus wurden feste Regale zur Lagerung von Montageteilen in dem frei gewordenen Raum neben der Montagelinie aufgestellt, die zuvor über die gesamte Anlage verteilt waren, wodurch die Kommissionierzeit verkürzt und Teile schneller geliefert werden konnten.
-
Fahrzeugkarosserien werden auf dem Drehtisch gedreht und auf Hängeförderer geladen, um zum Montageband transportiert zu werden.
-
Der Regalbediengerät erreicht eine Höhe von 15,5 Metern und bietet Platz für 92 Fahrzeuge. Jedes Rack kann ein maximales Fahrzeug mit einer Breite von 1800 mm, einer Tiefe von 5000 mm und einer Höhe von 1900 mm aufnehmen.
-
Lackierte Fahrzeugkarosserien werden von der Lackierstraße (ganz rechts) gefördert und von Hängeförderern auf Paletten verladen, um sie im Regalbediengerät zu lagern. Die Ein- und Ausgabestationen befinden sich im Zwischengeschoss.
Kontakt
Bei Produktanfragen kontaktieren Sie uns bitte über unsere Kontaktseite.
Zum KontaktformularKontakt
Bei Produktanfragen kontaktieren Sie uns bitte über unsere Kontaktseite.
Zum Kontaktformular