Take Your Manufacturing Operations to a New Level – Automated Buffers
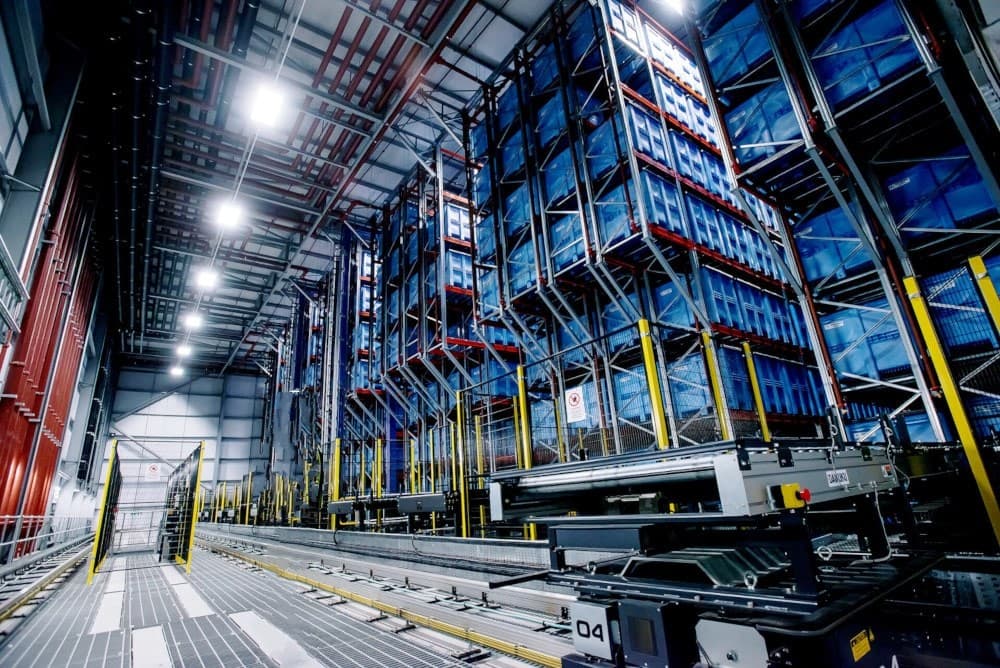
Edward Ray, Vice President of Sales (retired) of Daifuku’s Intralogistics Division, explains his insights on the benefits of incorporating an automated storage and retrieval system into a manufacturer's manufacturing process.
Most manufacturers keep up to speed with manufacturing technology that will help them streamline their manufacturing processes. Checking the newest mixing or cooking machines if you are in the food business, or the newest forming machines or robot assembly if you are in machinery manufacturing, or the newest device placement machines if you are in electronics is just a part of your business and ever-present struggle to stay ahead of competitors.
Sometimes, however, the non-manufacturing parts of a factory can have an even greater impact on overall factory productivity than the manufacturing processes. This is where considering automation of intralogistics processes (getting the right materials, to the right place, at the right time in a factory) can be significant.
Regardless of what kind of manufacturing you are doing, automating key areas within your intralogistics processes can significantly improve your bottom line.
Automated Finished Goods Buffer
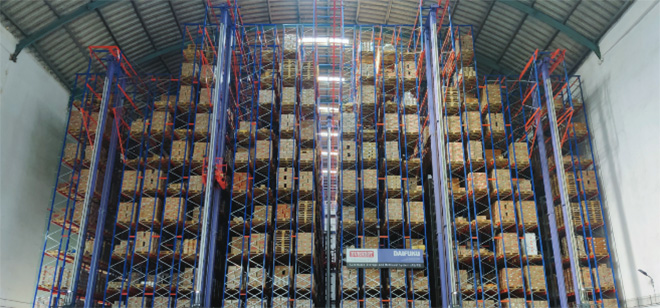
I will start with “shipping” because it is where most manufacturers start the automation of their intralogistics processes. By far the most common intralogistics automation in factories is the finished goods (FG) shipping buffer. The FG buffer achieves two things: First, it allows the factory to continue to operate at its own pace and during the best hours for manufacturing without dependence on people because the AS/RS can continually take products from the end of the line and put them away in the rack, thus keeping the manufacturing lines from getting plugged up. Second, it allows the factory to both focus on manufacturing the most efficient volume and fulfill orders in quantities that are likely much more random and usually of mixed product.
An easy-to-understand example of this is a beverage manufacturer that manufactures 24 hours a day (three-shifts), and usually in large lot sizes. An automated storage and retrieval system (AS/RS) will automatically put away pallets coming from the manufacturing lines with no human involvement. Shipping on the other hand may be limited to a timeframe of 8 hours a day, with trucks being filled with orders comprising small numbers of cases of various products, some of which might have been produced the day before or others 10 days before. A finished-goods AS/RS can both store product in advance and bring it out at the required time to fulfill an order.
Raw Materials & Packaging Materials Supply Buffer
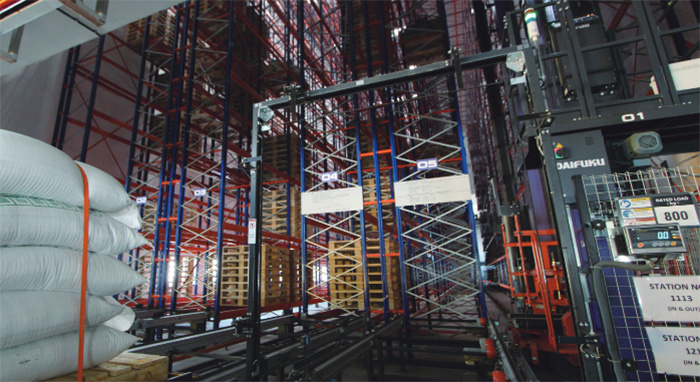
The second area that is usually automated after finished goods is raw materials (RM) supply. In this example I equate packaging materials (PM) supply to raw materials supply because although it may happen toward the end of the line, fundamentally they are the same—the actual finished good is not manufactured until it is in the packaging that it will reside in to be shipped.
In this case, raw materials may be delivered by vendors as they arrive on a given day, and an automated storage and retrieval system buffers all of the material until needed. The AS/RS can bring out the right material at the right time, allowing all processes to be fed on a just-in-time basis, eliminating any inventory clutter on the manufacturing floor while making sure no processes run short of the materials they need.
Work in Process (WIP) Buffer
Another way that automation may be used in the factory is for works in process (WIP). While a WIP buffer is often smaller than similar systems for finished goods or even raw materials/packaging materials, its use can be significantly more complex. WIP buffers are useful in the following situations:
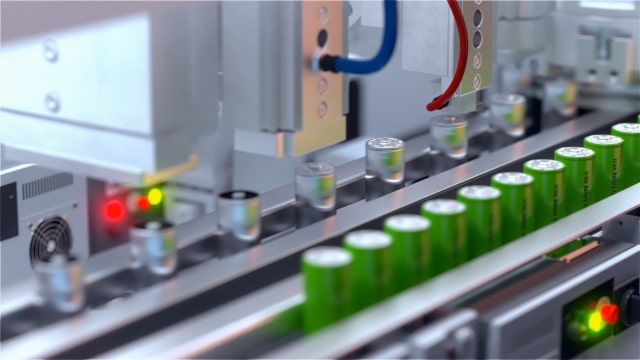
1. Consecutive processes that have different process times. It is also possible that process times may not be entirely consistent, and only when a certain event happens can the next process start.
Example: Parts must be machined one at a time, but then put together in lots of ten so that they can be put through a heat-treating oven.
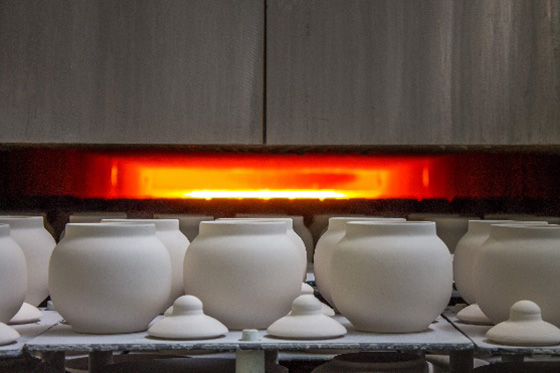
2. A downstream process happens at a different time of the day than an upstream process.
Example: Ceramics are made all day long but firing in the kiln only happens at night when electricity to run the kilns is cheaper.
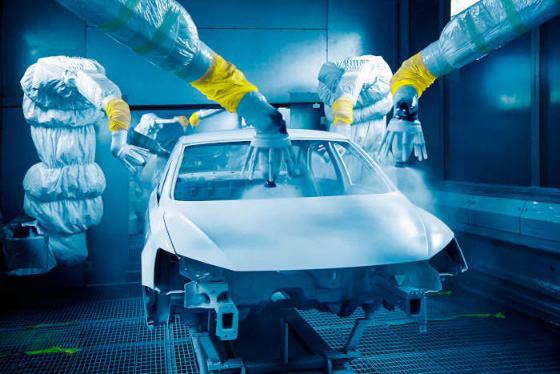
3. Upstream items need to be sequenced before feeding a downstream process.
Example: Painted car doors are being fed to a painted body line for assembly, but a defect is found in the yellow doors. The yellow bodies can be temporarily taken out of the line and re-sequenced back into the line when the quality issue is solved.
4. Two or more processes with their own not-in-sync process times must feed into a subsequent process.
Example: It takes one base and four side parts to build a steel box. The time it takes to build a base is longer because it has more welding of feet, etc., but still not four times as long as a side. Bases can be stored up over night and then fed on a one to four ratio with the side panels in a just-in-time basis to the assembly machines.
(1) Processes do not have the same “tact” time, (2) either process does not have a fixed, (3) a downstream process happens during different hours than an upstream process, (4) items must be re-sequenced, and (5) two not-in-sync processes must feed a third process.
View the image enlarged.
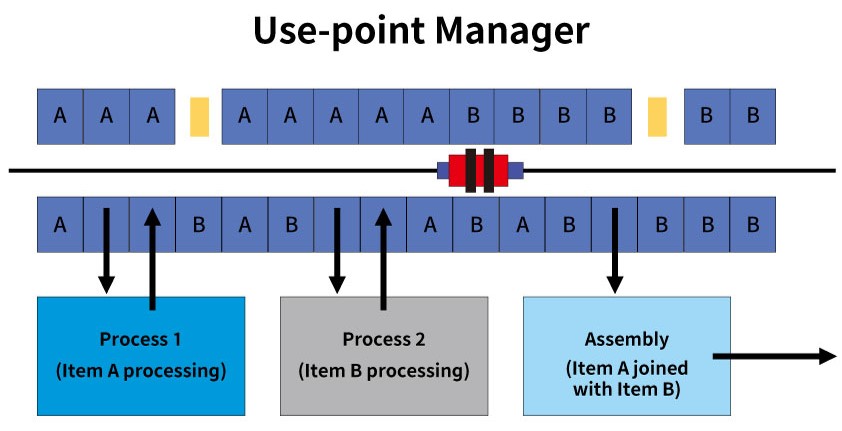
Process 1 is a cell on the far left that does something to a part A, process 2 is a cell that does something to part B, then both processed parts are brought out to the assembly area where they are combined into a finished product. The AS/RS is used to provide just-in-time supply to all processes, allowing for buffering between processes as well.
Conclusion
In all the examples of how strategic automated buffers (finished goods buffer, raw materials/packaging materials buffer, work-in-process, and use-point manager) are used, an automated storage and retrieval system is at the center and allows a factory to handle the material that goes into its processes as efficiently as possible and in a safe and timely manner.
An AS/RS brings the right items, at the right time, in the right quantities to the right place. To read more about how an AS/RS can be used as a buffer solution, visit our Work-in-Process Handling page on the Daifuku website.
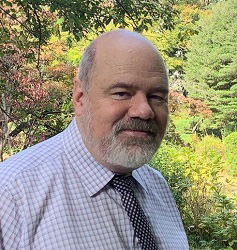
Edward Ray
General Manager (retired)
Intralogistics Division Sales
Daifuku Co., Ltd.