A Photographic History of DaifukuRamrun Monorail Transport System: Targeting Industrial Robot Synergy
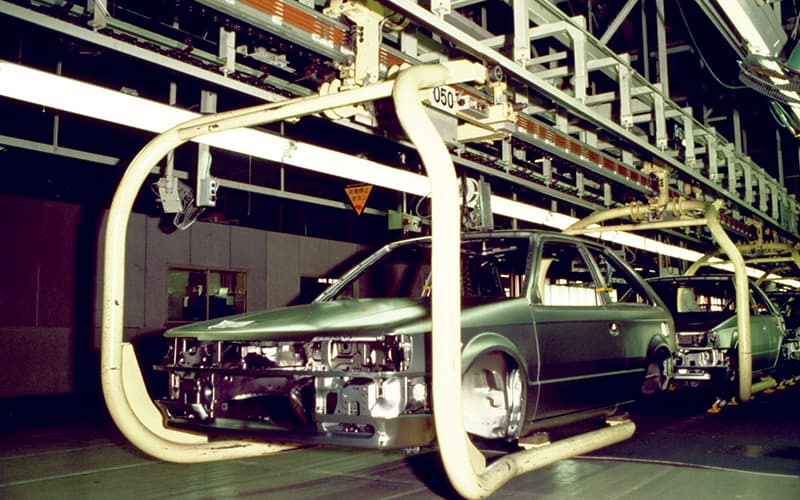
The early 1980s saw an increase in demand for industrial robots across various fields. Increases in production demand in the automotive sector led to an urgent need for further automation of production lines. However, traditional mainstream chain conveyor systems could not accommodate the agile movements of the robots, resulting in insufficient production efficiency and giving rise to the need for a new type of transport system.
Daifuku met that need in 1983 with its Ramrun monorail transport system. The Ramrun system made it possible to utilize both continuous and intermittent conveyance * through computer-based control. With a maximum transport speed of 120 meters per minute and a large speed range with 20 settings, Ramrun could be adapted to both robotic and manual production line operations. The system is offered in overhead and floor-based configurations.
- *Conveyance with repeated starting and stopping
The “Ram” in “Ramrun” stands for “Random Access Monorail,” (adapted from the computer term Random Access Memory) reflecting the flexibility and ease of access of the transport system. Daifuku marketed the system under the slogan of “Freedom of movement in factory automation” with the first system being introduced at Toyota Motor Corporation’s Motomachi Plant in 1983. Later that same year, the second system was delivered to Kanto Auto Works Ltd.’s Higashi-Fuji Plant. Since then, the Ramrun system has piqued the interest of a wide variety of companies in a variety of industries beyond the automotive sector, leading Ramrun to become one of Daifuku’s best-selling products.
In 1987, Daifuku introduced the Ramrun LIM, a linear-motor-driven system for small, light-weight parts capable of high-speed conveyance of 400 meters per minute. Then, in 1993, Daifuku introduced the Ramrun HID, the world’s first non-contact power supply system utilizing high-efficiency power distribution (HID). This system has also been adopted in automotive factories around the world due to its superior safety and maintainability.
- *This article is based on the content of “Hini Arata Nari: 50 Years of Daifuku History,” “Daifuku Group 70th Anniversary Magazine: Material Handling and Beyond,” and other documents.