DAIFUKU SolutionsIntroduction of a High-Capacity Sortation System to Handle Increases in Air Cargo
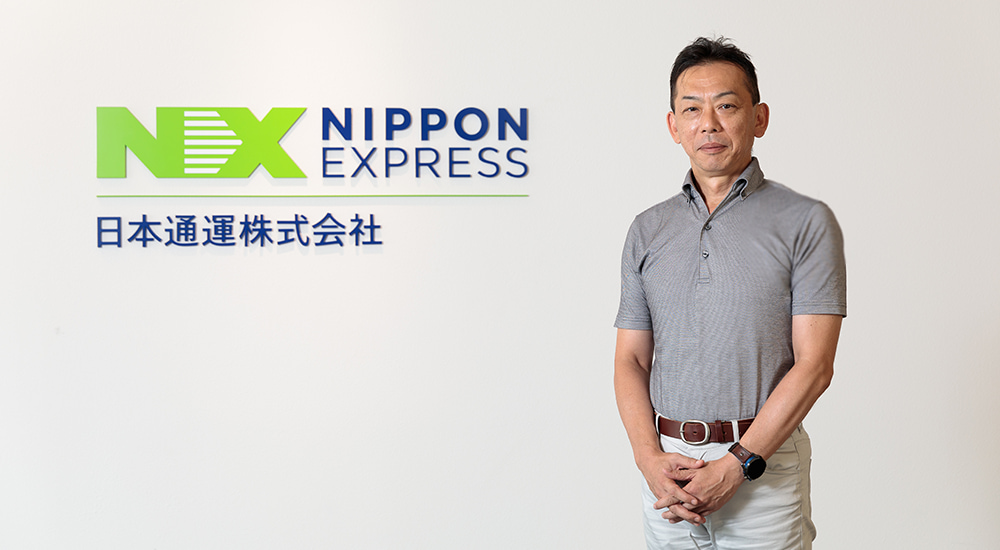
In October 2021, Nippon Express Co., Ltd. (hereinafter Nippon Express) opened NEX Amagasaki, an urban logistics base, in Amagasaki, Hyogo. The Osaka Airport Cargo Center in Toyonaka, Osaka, was relocated to the first floor of this new facility, while the sortation system—the center’s core equipment—was renovated in anticipation of an increase in air cargo handling needs. To learn more about how the company’s new cargo center ensures on-time delivery for a wide variety of cargo, we interviewed Takayuki Akiyama, manager of the Transit Department of the Osaka Airport Service Division at Nippon Express’s Osaka Air Service Branch.
Could you tell us about the role of the Osaka Airport Cargo Center?
This center operates 24 hours a day and is an important hub for our domestic air cargo network, as well as a gateway for domestic air cargo in West Japan. As its name suggests, the center handles air cargo to and from Osaka International Airport, also known as Itami Airport. One of the advantages of air cargo is being able to offer same-day delivery to customers, even in remote areas, and can fulfill the short lead times of urgent shipments, such as pharmaceuticals, precision equipment, and perishable items.
In addition to air cargo, the center also handles trucking services. We sort packages arriving from all over Japan and send them out to our offices in the Kansai area, where we also collect packages to bring to the center to sort and ship nationwide.
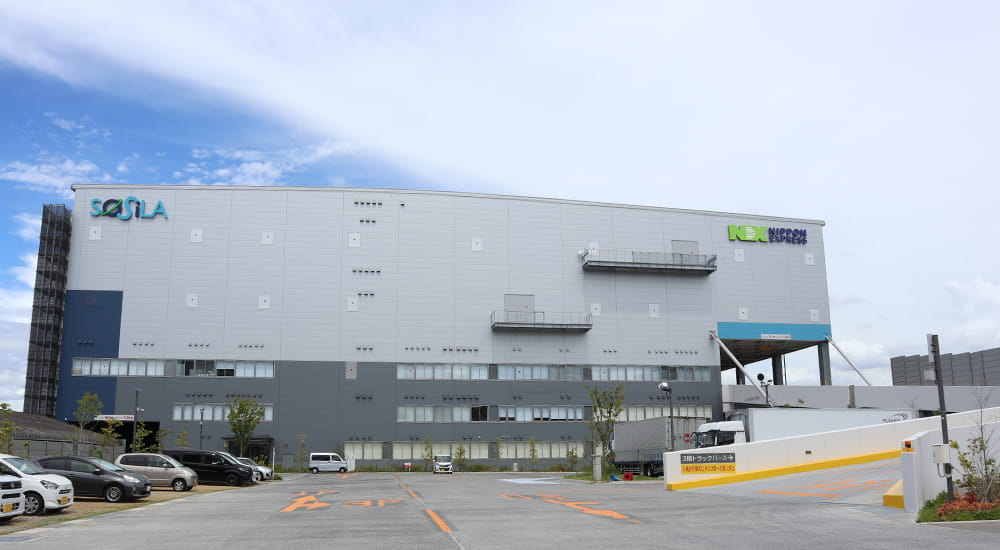
What is a typical day at the Center like?
The center sorts packages that arrive from Itami Airport by 10:00 a.m. so that our offices throughout the Kansai area can deliver them in the afternoon. Operations begin to slow down before noon, but after that, we start receiving packages from our Kansai offices, which we will sort and get ready for shipment from the afternoon into early morning the next day. Operations at the Center are in full swing from about 8:00 p.m. to 5:00 a.m. the next morning, as this is when we receive a lot of loads.
What led to your decision to move operations to NEX Amagasaki, and how is the location working out?
The Cargo Center was previously located in Toyonaka, Osaka, but as the number of packages we were handling increased, our processing capacity was reaching its limit. That, combined with the fact that various facilities had become obsolete, led to our decision to relocate the Center. The new location is only about 1.6 km from the Amagasaki Interchange on the Meishin Expressway, and only about 10 km from Itami Airport. It’s also close to residential areas and within walking distance of Amagasaki Station, which made securing our workforce easy. While logistics bases are usually built in the suburbs, NEX Amagasaki is an urban logistics base, making it a new endeavor for us.
Why did you decide to revamp the sortation system when relocating the center?
The main reason was that the sortation system at the old center was nearing the end of its service life, but we also wanted to revamp the system because the processing capacity of the old system couldn’t handle the increasing volume.
Cross-belt sorter—the best choice for higher throughput
Could you please tell us why you chose Daifuku’s cross-belt sorter at the center?
We handle a wide variety of packages at the center. The packages not only vary in size, weight, and shape, but also in packing material, with some in cardboard boxes and others in plastic, and we have to sort all of these. In addition, one of the top values we offer our customers is timeliness, so sorting speed is also a necessity. The cross-belt sorter makes it possible for us to automatically handle a wide variety of packages and deliver them on-time with quality service. Another major factor that led to this decision is that we have been working with Daifuku for more than 10 years, so they have a good understanding of our work, and we trust in their services, especially their support system.
The old center had a slide shoe system that moved cargo on a slat conveyor. When the cargo reached a junction, a shoe would push it out for sorting. With the cross-belt sorter, however, cargo is loaded onto connected carts that run on rails, and sorting is done using a belt drive. In this system, the carts are managed individually, which improves throughput, and if a cart ever breaks down, we can simply stop loading cargo onto that cart, so the entire line doesn’t need to be stopped. Not having to stop the entire flow of operations is a huge benefit.
Plus, the cross-belt sorter can handle high-capacity loads as it uses two belts on one cart. Only one belt is used for small loads, and two are used for large loads, so sorting is more efficient for a wide variety of loads.
Cargo is loaded onto connected carts and sorted using a belt drive.
Small loads are conveyed using only one belt, and large loads using two.
What points did you emphasize during the renewal process?
The biggest goal was to improve processing capacity. At the old center, the length of the conveyor from the cargo input area to the sorter was too short, so if a lot of packages came all at once, we wouldn’t have been able to process them. In the new center, the conveyor between the input area and the sortation system is long enough that we can use it as a buffer, and we also increased the number of input conveyors to four.
This, combined with the change in sortation system, means the new center can handle up to 12,000 packages per hour, whereas the old center could only handle up to 7,500.
Four conveyors lead into the cross-belt sorter’s input.
How do goods flow through the center?
Our staff manually feed incoming cargo onto the conveyors, and if the cargo can fit on one of the cross-belt’s carts, it will be transferred to the sorter. Items that are large and long, such as golf bags and roll screens, are put into the manual sorting line and conveyed to an area where staff manually sort them.
With the cross-belt sorter, the cargo information is linked to the cart, and when the cart reaches the specified chute, the cart belt is used to discharge the cargo into the chute. On the other end of the chute, staff manually load the cargo into air cargo containers and cage carts that are then loaded onto trucks for shipment.
Cargo is manually loaded from a container onto the conveyor.
Cargo is sorted by destination and loaded onto cage carts.
Improved working environment thanks to the quietness of the new system
Was the move to the new location difficult?
As a logistics company with a long history, the move itself was not such a big problem, but we couldn’t stop handling packages during the move, so we ended up having to use both the old center and the new one during the transition. We did get off to a bit of a rocky start at first, but we knew that Daifuku would be there to support us with any problems we had, so we could get things up and running with confidence.
Is it true that you wanted to focus on reducing noise at the new center?
Yes, the new sortation system is much quieter than the previous one. During the demo at Daifuku’s Shiga Works, we were impressed by how quiet the system was, and now that we have it up and running at the center, we have even more appreciation for how quiet it is. At the old center, we had to speak quite loudly to be heard, but at the new center, we can have normal conversations again, so the working environment has really improved. Also, because it is an urban logistics base surrounded by residential area, we paid special care to the material of the walls on the first floor where the sortation system is located, building them with excellent sound insulation to prevent sound leakage.
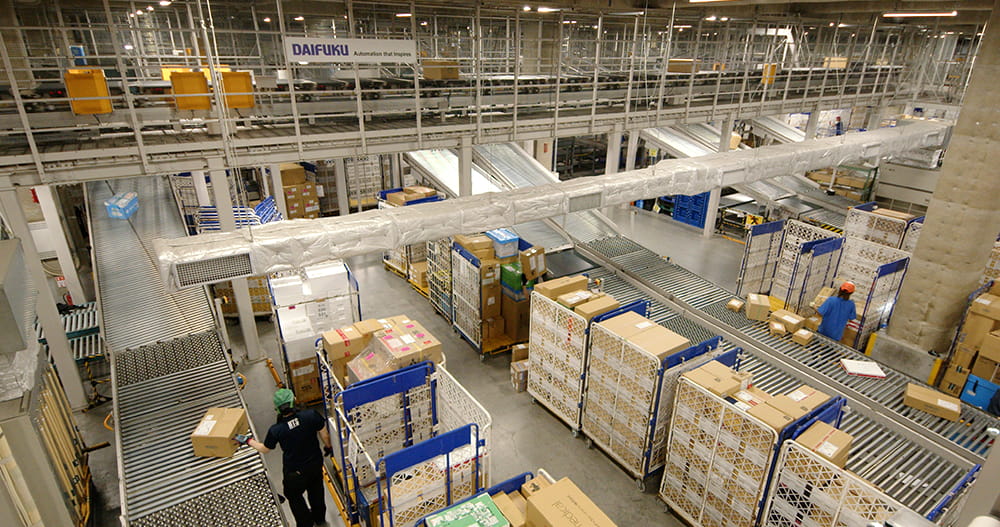
Last question: What is your outlook for the future?
The logistics industry has been struggling with labor shortages for some time, so we plan to make the most of NEX Amagasaki’s advanced automation to continue growing our operations. We are also dedicated to improving efficiency and promoting work environment improvements so that we can provide customers with even faster and higher quality services.
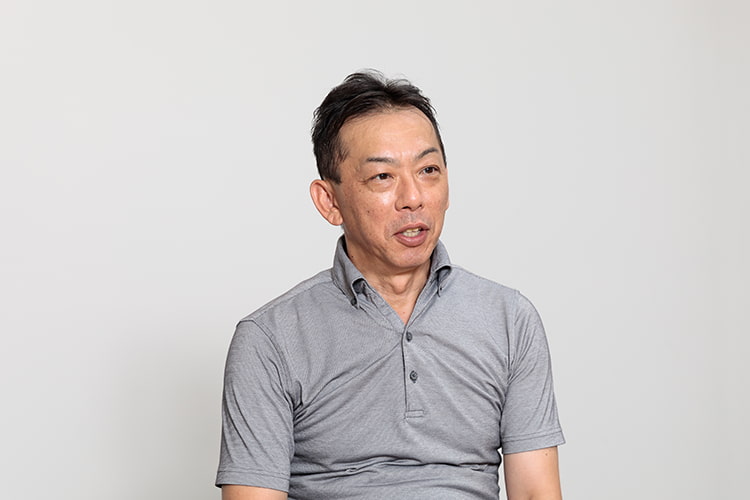
Takayuki Akiyama
Manager
Osaka Airport Service Division, Transit Department
Nippon Express Co., Ltd.