DAIFUKU SolutionsEnabling Flexible Manufacturing: New Door Auto Mounting System
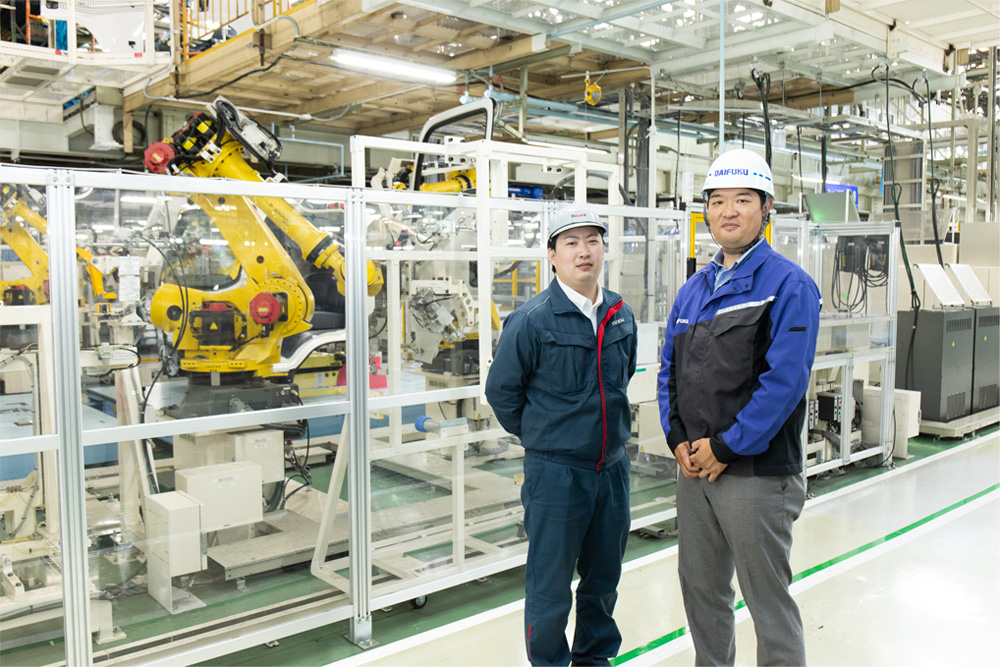
Isuzu Motors Limited (hereinafter Isuzu) boasts the top share for commercial vehicles in Japan. With the main exception of engines manufactured at Isuzu’s Tochigi Plant, most of the production processes, including manufacturing and assembly, are carried out at the Fujisawa Plant in Kanagawa. Since operation commenced at the Fujisawa Plant in 1962, Isuzu has regularly updated its equipment to match the times. In the summer of 2022, it was time for the door auto mounting system to be updated. Isuzu’s Yusuke Ueki of the Cab Assembly Group in the Vehicle Engineering Department (left in photo), and project lead Yusuke Hayashi of the Daifuku Automotive Division (right in photo), briefed us about what changed with the deployment of this new system.
What processes are carried out at the Fujisawa Plant?
Ueki: The plant assembles our light-, medium-, and heavy-duty trucks, and is also equipped with a research facility. With a site area of about 820,000 ㎡, it takes approximately 20 minutes to walk from end to end. The site has four plant buildings: Plant 1 handles the pressing, welding, and painting, Plant 2 carries out the cabin outfitting and vehicle assembly, and Plant 3 and Plant 4 manufacture the axle, transmission, and other parts of the powertrain.
What kind of work does the outfitting performed at Plant 2 involve?
Ueki: Outfitting includes fitting parts to the cabin, such as the front glass, seats, and instrument panel, as well as mounting the doors. Plant 1 carries out the metalwork to make the cabin and door frames, as well as painting, which is done with the doors mounted. After painting is completed, the cabin is transferred to Plant 2. However, it is difficult to perform outfitting, both inside and outside the cabin, while the doors are mounted. Therefore, in Plant 2, the doors are removed from the cabin at the entrance to the outfitting line. The cabin and doors are placed on separate lines where they are each outfitted. Once completed, the lines merge together and the doors are remounted to the cabin. This is where the system to automatically mount the doors was updated.
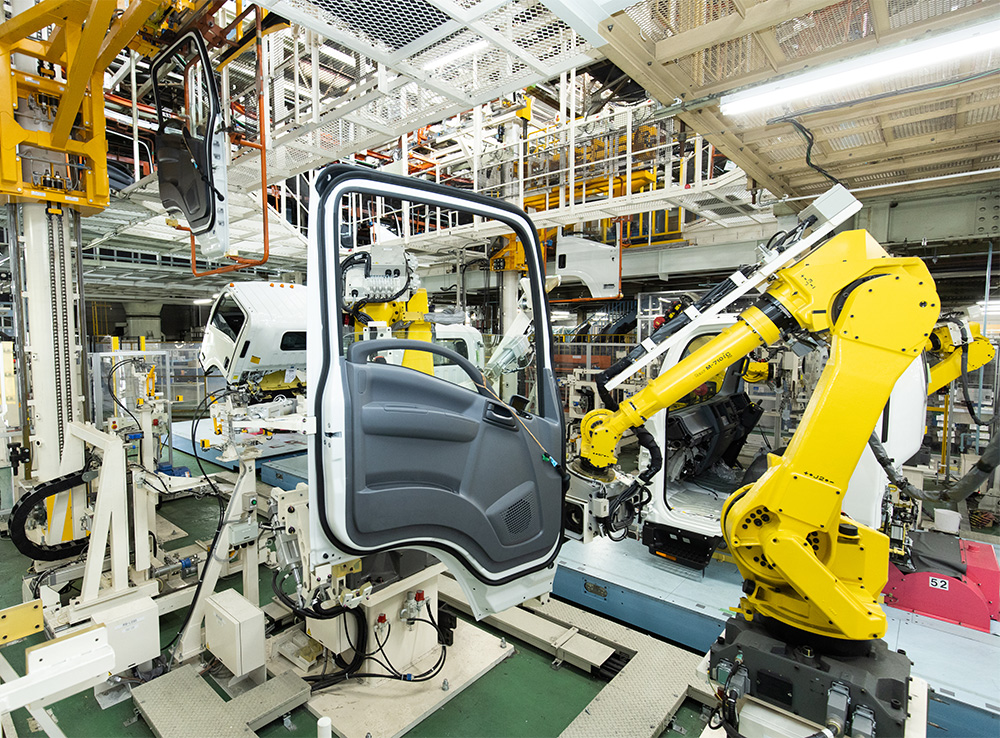
Why did you approach Daifuku to update your system?
Ueki: As the cabin moves along a line on the 1st floor, the removed doors are lifted up and outfitted on a sub-line located at mezzanine level. This door sub-line is also a Daifuku system, and about 30 years have elapsed since its deployment. I think the quality to withstand so many years of operation is amazing. Since Daifuku’s systems are also incorporated into other lines and Isuzu is in regular contact with the company, we decided to also consult about updating the door auto mounting system.
Striving to improve productivity and provide flexible support for new vehicle models
What made you start thinking it was time to update the system?
Ueki: There were two reasons. The first was the desire to increase equipment performance and improve productivity. The automotive industry is undergoing a revolution, and we must respond to the changes in the market. Production bases are always trying to think of ways to improve efficiency, so I think this is extremely natural.
The second was to accommodate new models with different door opening angles. The doors of previous models opened to nearly 90 degrees during mounting, and 70 degrees at shipment after additional parts had been attached. To improve efficiency and reduce the number of parts, we decided to embark on the development of a vehicle model with a door opening angle of 70 degrees during door mounting. As the door auto mounting system we were using did not support a 70 degree mounting angle, we began considering an update to the system.
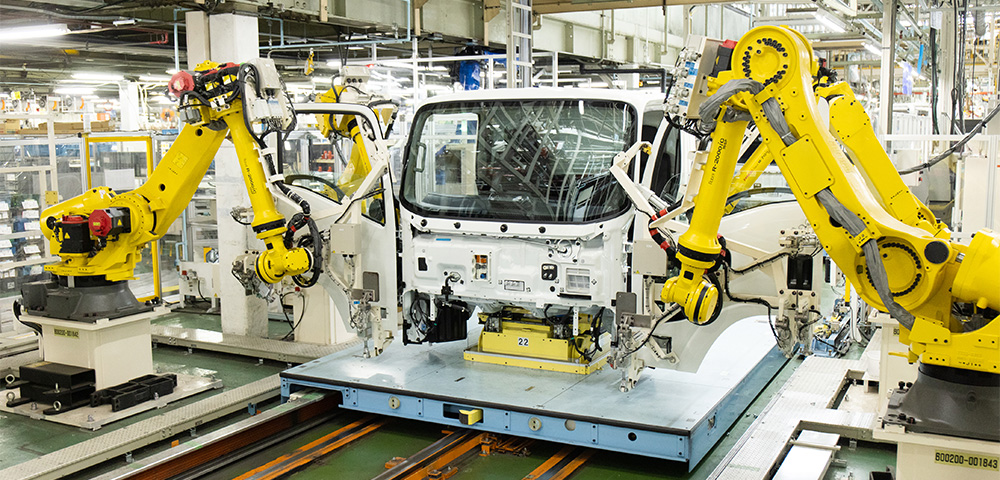
There are a total of four robots, two on each side. One holds the door, and the other determines the fixing position and then performs the fixing work.
Is there a big difference between 90 degrees and 70 degrees?
Ueki: The difference is huge. A robot arm is inserted on the inner side of the door to tighten the bolts when mounting, but reducing the opening angle to 70 degrees decreases the range in which the arm can move. We needed a system capable of performing the mounting work safely and properly, because we cannot ship a vehicle if a door or the body ends up damaged due to working in that narrow space.
We also really wanted to eliminate the need to position the cabin. With the previous system, the cabin and conveyor had to be correctly positioned at the point where the door automation process began. This, however, increases cycle time, thus reducing productivity, and was a key point we were looking to improve.
Reducing the door opening angle to 70 degrees
The 20-degree difference was a difficult challenge
What led you to choose Daifuku for your system upgrade?
Ueki: We consulted with several manufacturers about how to achieve these goals, and they proposed various technologies and ideas. Among the manufacturers, it was Daifuku that clearly provided all the information that we required to make a decision.
With our plans to step away from precise cabin positioning, each door attachment would have minute changes to the bolting positions, and we would need a combination of cameras, sensors, and other high performance tools since there is no all-purpose solution that can perform the task alone. Each proposal we received came as a singular set of systems which had their own advantages and disadvantages. Daifuku, however, provided a document detailing the features of each product, the compatibility of product combinations, the reasons for proposing such combinations, and other information that allowed us to quickly carry out a comparative review. This document was extremely useful as we were able to easily circulate it internally to help with the decision-making process.
In addition, we had already decided to change the installation location for the door auto mounting system, and had previously consulted with Daifuku about improving the door sub-line. Since the proposal we received from Daifuku when consulting about the door auto mounting system was also outstanding, we expected operation quality would be even further improved if we requested Daifuku to tackle the whole project from door transfer to automatic mounting.
Furthermore, the response to our inquiry was impressive. Although there was no big difference between the speed at which each company responded, Daifuku’s reply was both accurate and prompt, so we sensed that there is strong collaboration between the engineering and sales departments, as well as a smooth communication environment.
Why did you change the installation location for the new door auto mounting system?
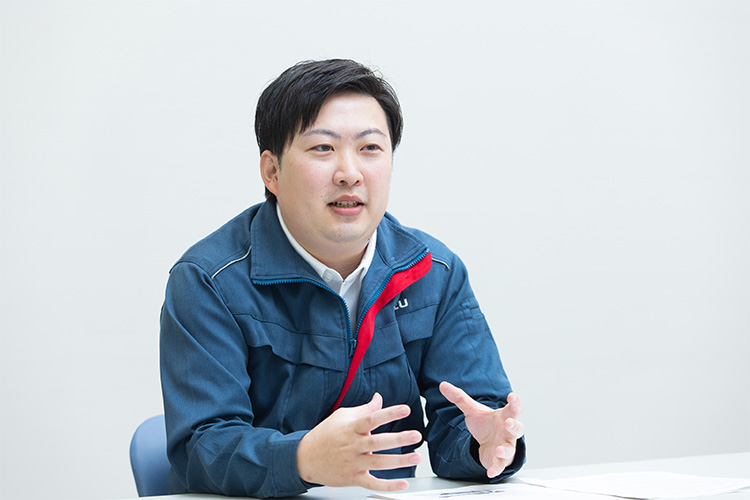
Ueki: To enable production to continue concurrently. It is not possible to stop production in an operating plant just because equipment is being updated. The original equipment must remain operational while the new equipment is being installed. Scheduling and process management were extremely difficult as the work was limited to Saturdays and Sundays when the plant was closed. In addition, the work had to be finished early each Sunday to test the operation of the equipment to ensure there would be no influence on production beginning on Monday.
The installation work was performed first for the drop lifter that supplies doors from the door sub-line to the auto mounting system. The work to obtain precise installation measurements and create the design for the new door auto mounting system proceeded concurrently with the installation work of the drop lifter. We had meetings with Daifuku almost every week and after two months of planning, we received the installation diagrams and 3D models. After ironing out some remaining details, the final blueprints were completed.
What in particular posed a challenge in the design process?
Ueki: Most of the discussions with Daifuku were about the nutrunner and material handling. The door auto mounting system has a pneumatic torque wrench, called a nutrunner, for automatically tightening bolts. The nutrunner is attached to the end of a robot arm. Since the robot arm of the new model would have a decrease in its range of movement, we asked Daifuku to design the system to ensure that the arm would not hit the cabin or door.
Hayashi: We asked various manufacturers if they had a nutrunner that could operate in a narrow space, but there was no existing product with the required capabilities. So, we used 3D modeling to test making the head of the nutrunner thinner and test a new bracket shape. After a great deal of consideration, we developed a unique shape and submitted a proposal of this new nutrunner to a manufacturer. Our new nutrunner design was adopted, enabling us to create a system that allowed the door attachment work to be carried out safely in the limited 2 to 3 mm allowance.
Successfully realizing production goals
Adapting to new vehicle models
With such strict conditions, did you find it difficult to design the overall system?
Ueki: I believe it must have been hard to meet our demand to make a mechanism that has the nutrunner flexibly make fine adjustments to its alignment for each operation. When the nutrunner inserts the bolts for assembly, if it is misaligned, the bolts will be inserted at an angle. If that happens, a worker will have to go and fix the problem, and in some cases, the door may need replacing. The old equipment allowed for some movement, but we wanted the new equipment to move more flexibly when inserting the bolt. However, if the nutrunner is too loose on the arm it will sway and be unable to properly lift up the bolt at all, so we held many discussions about the design to ensure that the nutrunner is only adjusting when fastening the bolt into its hole.
Hayashi: This problem is related to the issue of positioning. The old equipment first lifted the cabin to precisely position it and then began the door mounting process. But the new system performs the door mounting work while the cabin is still on the conveyor, so variations in the cabin position are inevitable. Therefore, we installed the new door auto mounting system to improve installation flexibility.
A camera is used to identify the position of the bolt holes, but the camera used with the old equipment could only capture a set location, meaning accurate information could not be acquired if the cabin position varies. We imagined a control system in which one robot is made to hold a camera, and the positioning of the other two robots are determined based on its information. We contacted several manufacturers to try to find a camera system meeting the conditions, but no existing product did. In the end, we developed a new system in coordination with one of the manufacturers.
Positioning is identified with a camera (left) and then the door is mounted (right)
There were a number of new experimental ideas incorporated into the new equipment. Were there any worries?
Ueki: When updating equipment, Isuzu always requests that equipment operation be thoroughly tested. Even if there are no problems in the 3D simulations, some problems or points to improve may be found during actual operation. If problems are found after full integration, there will be constraints in terms of work time and methods when making corrections. We thus ask for testing to be carried out in advance and demo runs of the system were conducted months prior to full integration. When I inspected the system in operation, I was extremely impressed because it was exactly what we were looking for. Although a few minor adjustments were still needed, it was an exceptionally high level of perfection.
Nearly a year has passed since the system began operation. Are you satisfied?
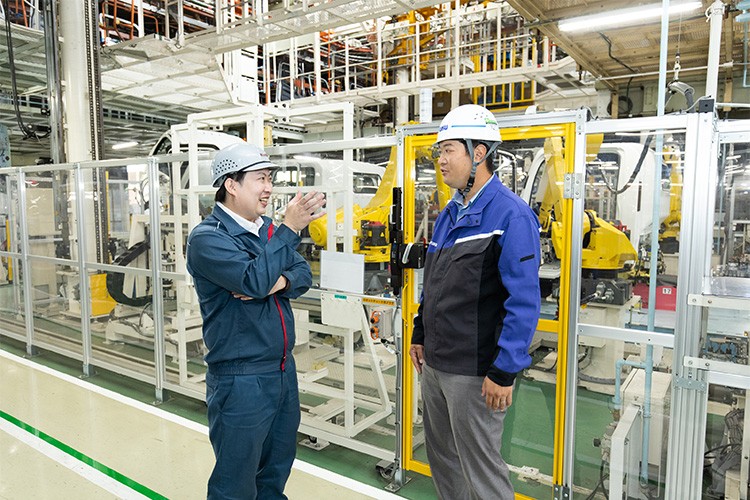
Ueki: The results that we envisioned during the planning phase have been sufficiently realized. Our goal of shortening cycle time has been achieved, and the system also has no problem adapting to new vehicle models. Amid the changes taking place in the automotive industry, Isuzu will take on the challenge of developing various vehicle types in the future. Production must be able to handle such changes, which is why eliminating cabin positioning with this update was very important to us. In terms of the overall plant, we want to build a system that can respond flexibly, which means we still have further aspects that we wish to consult about with Daifuku.
Hayashi: In recent years, Daifuku has been strengthening its support, not just for conventional transport systems, but also for robotization. Meanwhile, while there were many challenges deploying this new system, we are extremely grateful to Isuzu Motors for creating an environment where it was easy to propose new ideas. We will continue working to fulfil the future needs of automation in the diversifying automotive industry.
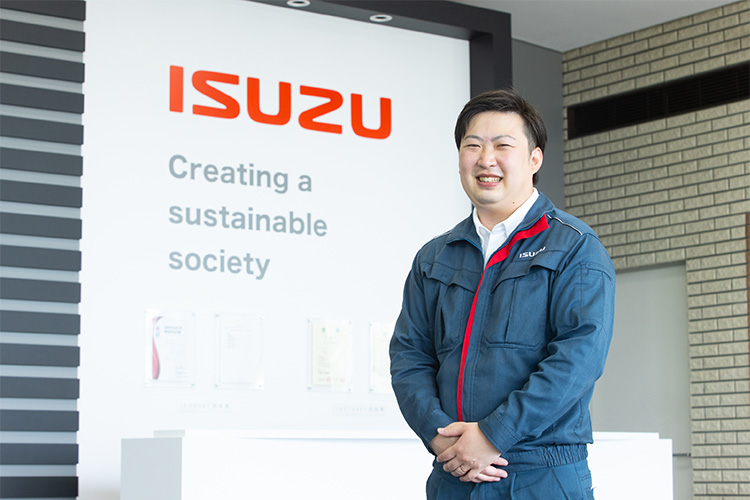
Yusuke Ueki
Cab Assembly Group, Vehicle Engineering Department
Isuzu Motors Limited
Yusuke Ueki joined Isuzu Motors Limited and was assigned to the Manufacturing Department in 2014. After gaining experience in multiple departments, including the Maintenance Section, he was transferred to the Cab Assembly Group in 2016. He currently works at Fujisawa Plant in Kanagawa, which assembles light-, medium-, and heavy-duty trucks.