A Photographic History of DaifukuJapan’s First Automated Warehouse Developed
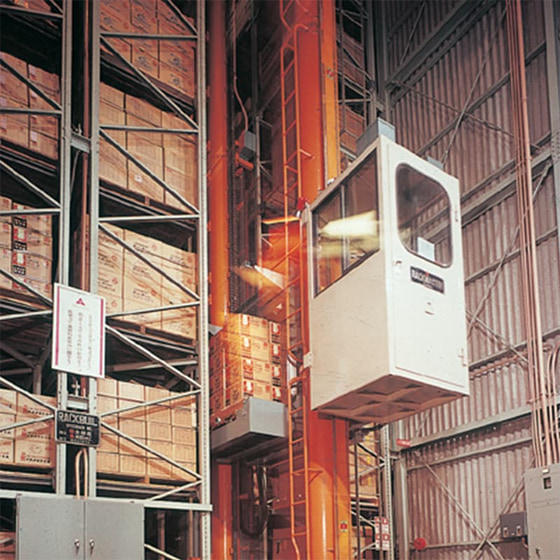
In 1966, Daifuku developed and delivered the Rackbuil and Rack Master System, Japan’s first multi-tier automated warehouse. Rackbuil integrates racking with a building by attaching racks to the roof and walls, and Rack Master performs the storage and retrieval of the goods and materials in the racks. At the time, warehouses were typically single-story with the storage and retrieval work being done manually. The automated warehouse that emerged under these circumstances was a groundbreaking technological innovation that overturned the traditional concept of warehousing by allowing goods to be stored in a high-rise system.
Up until the beginning of the 1970s, automated warehouses had mostly been used by manufacturers to store finished goods and raw materials. However, since a large amount of investment was required to construct one, they were mainly delivered to large companies. Operation of automated warehouses evolved from the initial method of a controller in an operator’s cab to full automation by computer control and the accuracy of inventory management was also improved by location management being done simultaneously with retrieval and storage. These innovations led to automobile parts centers that manage tens of thousands of items and pharmaceutical companies that require high accuracy to also begin deploying automated warehouses.
From the mid-1970s, demand continued to grow for automated warehouses. In response to these needs, we developed and commenced the sales of standardized unit load AS/RS and mini load AS/RS solutions.
From then onwards, the effectiveness of automated warehouses was recognized in the Japanese industrial world, and the market for them further expanded as even smaller companies began to adopt them amid the growth in the Japanese economy. During this period, we developed automated warehouses for special environments, such as cold storage where certain temperatures need to be maintained and semiconductor manufacturing where high levels of cleanliness are required. In recent years, we have rolled out a lineup of shuttle storage systems equipped with higher storage and retrieval capacity as well as sorting and alignment functions, and delivered them to distribution, e-commerce, and other industries’ logistics centers. As automated warehouses make up the core of material handling solutions, we are continuing to develop the capabilities of our systems so as to build optimal solutions for each of our customers.
- * This article is based on the content of “Hini Arata Nari: 50 Years of Daifuku History” and other documents.