Essential Daifuku Technologies for Social InfrastructureOur D-PAD Wireless Charging System Combines Compactness and Rapid Charging
It is essential to prevent batteries from running out if you want to ensure stable operation of the AGVs (automatic guided vehicles) and AMRs (autonomous mobile robots) that are needed to automate factories and distribution centers. The automation of charging work is another major challenge as labor shortages continue to bite. That is why we made our D‑PAD wireless charging system much smaller and lighter so that it can be used to charge equipment such as low-platform AGVs. We also launched a model capable of rapid charging at up to 100 A. It enables frequent top-up charging between tasks and helps to boost work efficiency. The developers of the system, Makoto Nunoya, manager of the Cleanroom Division Production Operations Power Device Department, and his colleague Diazo Ninomiya told us more about it.
What kind of system is the D-PAD?
It's a system that automatically and wirelessly charges the battery when attached to equipment such as an AGV or AMR.
It's essential to prevent batteries from running out if you want to ensure stable operation of AGVs. However, it takes time and effort to replace them, and factories and distribution centers have been struggling with labor shortages in recent years, so there's a demand for systems which automate the task. Contact-type charging systems with components such as plugs are also being commercialized, but even a small vibration may cause sparks during charging, which may lead to fires.
The D-PAD wireless charging system solves that issue. When the D-PAD is used, charging stations are placed in locations where AGVs make a temporary stop, such as during the assembly process in a factory or the picking process in a distribution center. Topping up the charge while the AGV is halted ensures that there is no worry of the battery running out.
What are the technical strengths involved?
The D-PAD utilizes a resonant circuit for the power generated via electromagnetic induction by coils and ferrite to efficiently transmit electricity to a battery without contact. This principle has been known for a long time, but conventional electromagnetic induction systems which utilize circular coils require large sizes in order to transmit over long distances, making it difficult to attach them to equipment such as AGVs.
The D-PAD overcomes this drawback, the most important point being its utilization of our proprietary D-shaped coil. Using D-shaped coils makes it possible to achieve a longer transmission distance than a circular coil of the same size. The D-PAD has been able to roughly double the transmission distance of similarly sized systems that utilize circular coils. Charging is possible even with a distance of around 3 cm (6 cm for the 100 A model) between the power transmission pad installed in the charging station and the receiver pad installed in the AGV.
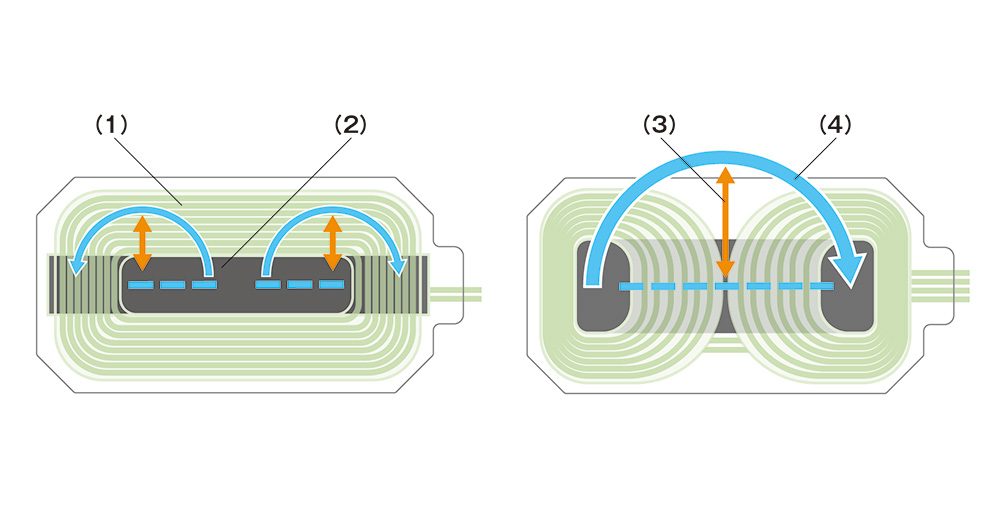
The D-PAD (Right) transmission distance is twice that of a conventional device (Left)
Daifuku commercialized the world's first electrified monorail conveyance system with non-contact power supply
Please tell us about the development process.
In 1992, Daifuku formed an alliance with the University of Auckland in New Zealand regarding wireless power supply technology, and in 1993 we commercialized the world's first electrified monorail conveyance system with non-contact power supply. Daifuku applied that wireless power supply technology to develop the D-PAD charging system. The D-PAD configuration is as follows. When a device is stopped at the charging station, a high-frequency electric current flows from the D-PAD inverter (1) to the power transmission pad (2). Electromagnetic induction is utilized to transmit power to the receiver pad (3). The charge controller (4) uses that power to charge a storage system such as a battery.
We started marketing the system for large AGVs in 2013, and developed a more compact D-PAD for regular AGVs in 2016. The D-PAD charge controller has been made much more compact in the new model launched in April 2019. With dimensions of approximately 17 x 23 x 7 cm, it's roughly 60% smaller in volume than the previous model. It's also roughly 70% lighter.
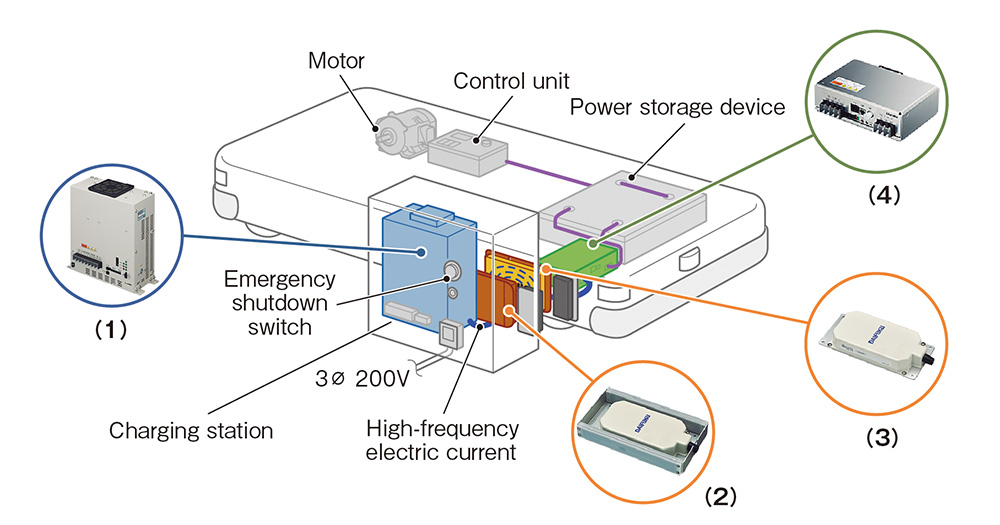
The structure of the D-PAD wireless charging system
Why did you make it more compact?
In recent years low-platform AGVs and AMRs are widely utilized in factories and distribution centers, so we made a more compact model to be compatible with them.
In order to utilize the D-PAD, a receiver pad must be attached to the surface of the AGV or AMR, and a charge controller installed inside. But there isn't much empty space inside small conveyance devices such as low-platform AGVs and AMRs, so it was hard to install a charge controller in them. We made the charge controller more compact so that it can be installed without having to make design changes to existing AGVs and AMRs.
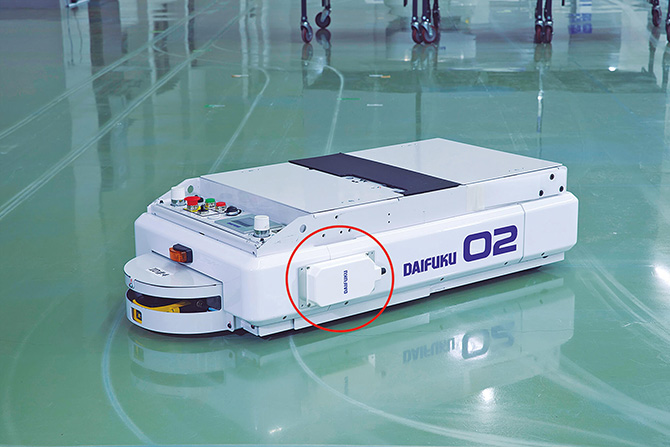
A D-PAD installed in an AGV. The charge controller installed in AGVs has been made roughly 60% smaller in volume than the previous model, which means it can also be installed in low-platform AGVs.
What did you do to make the device more compact?
We came up with various ideas, one of which was to modify the cooling system. The charge controller generates a lot of heat, so the cooling system is essential.
The previous model was designed on the assumption that it would be used in clean rooms, such as in semiconductor factories, and was installed with a cooling system which uses fins so that it wouldn't agitate the air in the room. The new model, however, targets devices such as AGVs and AMRs that operate in ordinary factories and distribution centers, so we changed to a cooling system which utilizes a fan. Other improvements, such as employing special electronic components, have enabled us to make the charge controller significantly more compact.
Please tell us about the functional strengths of the charge controller.
A variety of batteries are used in AGVs, so we've made it possible for users to adjust the charging settings on a computer and make the system compatible with the various voltages, currents, and battery types.
Furthermore, the charge controller is also equipped with a feature that prevents the battery from being damaged by a change in the charging current, such as from a sudden change in magnetic flux due to the power transmission and receiver pads getting too close together or shifting out of alignment.
What kind of customer base do you envision?
Instead of selling our AGVs with the D-PAD installed, we sell the charging system separately. It can be retrofitted to AGVs and AMRs already in operation, so we will market it to end users of such conveyance devices.
Our development of a model with a higher power capacity of 100 A helps to conserve resources
How did the 100 A model come about?
In recent years people have started to use AMRs with more complex functions that require more electricity to operate. This led to the following issues: the operating rate would decline if AMRs had to make frequent stops to charge, and the charging station would end up being occupied for too long if the AMRs took a long time to charge. As a result, there was a growing need for frequent top-up charging when devices had stopped to perform transfers or picking work. So, to ensure sufficient charging between tasks, we've developed a model with a higher power capacity of 100 A that can deliver rapid charging.
What kind of challenges did you confront in the development process?
Frequent top-up charging between tasks means that, on the transmission side, dozens of AGVs are charged at one location thousands of times a day. A 100 A current is on the large side for industrial purposes, and when such a current is generated repeatedly, there is a risk of thermal contraction causing the transmission pad to crack or leading to insulation problems. This complicates the design, but we utilize semiconductors with a simple structure, and added or modified insulating materials to address the thermal contraction.
In addition, the AMR itself also vibrates when its robot arm moves, so there are large fluctuations in the received power as the distance during charging becomes farther or closer. Furthermore, the movements of the arm cause the electrical load to fluctuate. Meanwhile, the charging output to a lithium battery needs to be made highly precise, and the charging current may sometimes be cut suddenly to protect the lithium battery installed in such equipment. We therefore devised a way to ensure both a rapid response and precise control of the current and voltage.
The battery is charged frequently with top-up charging so can be used with a low depth of discharge. This means the battery's lifetime charge/discharge capacity can be used efficiently, thereby helping to conserve resources. In ways such as this, Daifuku is committed to helping to create a sustainable society via its products and systems.
- *This article is based on the content of "Interesting Info from Developers about New Technologies" featured in DAIFUKU NEWS No. 224 (published in July 2019) and on a new interview.