DAIFUKU SolutionsNojima Corporation: Boosting Productivity through Automated Sorting
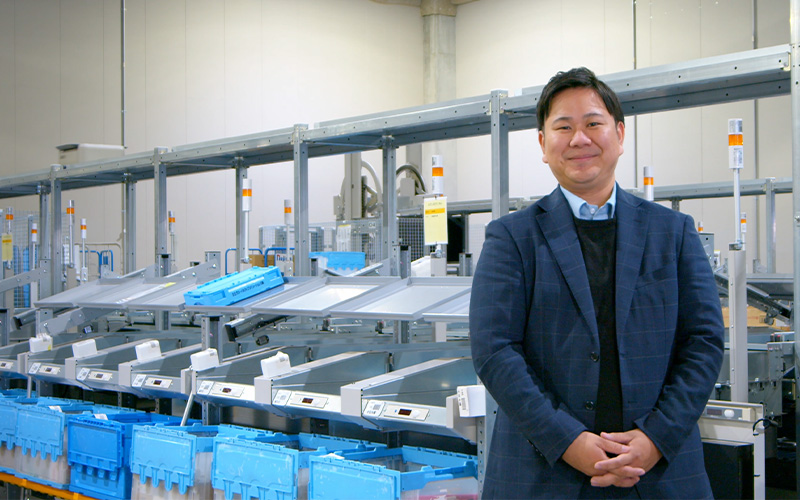
Nojima Corporation, a leading digital electronics retailer, has introduced the SOTR-S sortation system at its Misato Distribution Center in Saitama Prefecture. The system has helped streamline operations and save on processing time. We spoke with Yutaro Maruyama, Group Manager of the Misato Logistics Solutions Group, about the goals behind the implementation and its results.
Can you tell us about the role of the Misato Distribution Center?
As of September 2024, we operate 242 digital electronics stores, primarily in the Tokyo metropolitan area. Previously, our logistics center in Yokohama, Kanagawa Prefecture, handled distribution for all our stores. With the growing number of locations, we established the Misato Distribution Center in 2022 as a new logistics hub. The center is located about 0.5 kilometers from the interchange on a major expressway. This center now serves 87 stores across Saitama, Tokyo, Chiba, and Ibaraki prefectures, and with a shorter distance to the stores than from Yokohama, delivery efficiency has significantly improved.
What types of products are handled at the Misato Distribution Center?
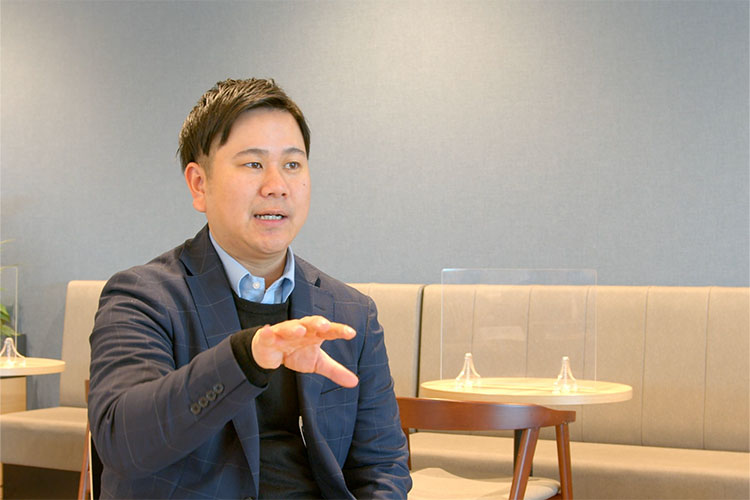
We handle everything sold in our stores—from small items like batteries and SD cards to large appliances such as TVs, refrigerators, and washing machines. The center spans two floors. On the second floor, we receive small to medium-sized products from manufacturers, sort them by delivery area and store, and then ship them out. We’ve implemented Daifuku’s material handling systems to automate and streamline these processes. The third floor is used for managing inventory and shipping large appliances that require installation.
Overcoming Space Constraints with a Smarter Sorting Solution
We understand that sorting of small items was done manually when the center first opened. What did that process involve?
For medium-sized items like rice cookers and microwave ovens, we used a conveyor system to sort and transport the products while still in their cardboard boxes. However, for smaller items like batteries, staff had to sort them manually into store-specific shipping containers before placing them on the conveyor.
Specifically, workers would look at printed picking lists for each store, pick the required items, and then walk around visually checking the labels on each shipping container and placing the items accordingly. For a team of six, this task took about six hours to complete. Team members often commented that the work was tiring due to the amount of walking, visually exhausting due to the constant checking, and mentally taxing due to the need to avoid errors. At our center in Yokohama, similar feedback led us to introduce a slide-shoe type piece sorter in 2019 to automate small-item sorting. We initially considered the same approach for Misato, but faced challenges—most notably, space limitations that made it difficult to install the sorter in the preferred location.
While exploring alternatives, we consulted with our contact at Daifuku, who proposed the SOTR-S sortation system. With the SOTR-S, staff only need to scan the barcode of an item at the input station and place it on a vehicle’s tray. From there, the vehicle moves along a track and automatically sorts the item into the appropriate chute. The system is easy to operate, even for less-experienced staff, and its compact design supports many chutes in a small space—key reasons we decided to implement it.
So space efficiency was a key factor in choosing the system?
Yes, exactly. The center was already equipped with various systems, so it was essential to fit the new solution into the area where manual sorting had been done. The SOTR-S uses a two-tier structure, with vehicles running on vertically stacked lanes, which makes efficient use of vertical space compared to typical sortation systems. We were able to install 62 chutes—far more than with a conventional slide-shoe sorter—maximizing the number of chutes possible within our space constraints.
In order to obtain internal approval to introduce the system, we had to determine if it would offer benefits in addition to the space savings over a slide-shoe sorter. In other words, it also had to further ease labor and reduce processing time. And the SOTR-S cleared these conditions.
Barcodes are scanned, and the products are placed on a vehicle’s tray.
The vehicle quickly moves the product to the appropriate location.
The tray tilts to sort products into the appropriate chute.
The lifter moves the vehicle to the upper level and back to above the product entrance.
How did the installation go?
At our Yokohama center, the main conveyor and the sorter are not connected. Staff have to manually transfer items between them, which is a burden. At the time of installation, the systems were from different manufacturers and placed far apart, so we didn’t even consider connecting them.
This time, however, the systems were being installed closer together, and because we were standardizing with Daifuku equipment, we were determined to avoid similar issues by directly connecting the systems. At the same time, we couldn’t allow any disruption to store deliveries, so we needed to avoid shutting down the main conveyor during the installation. After many discussions with Daifuku, we found a single location where the connection could be made without stopping operations. Internally, that successful connection was one of the most highly praised aspects of the project.
From start to finish, the installation took about one month—much faster than we expected. Daifuku quickly grasped our intentions and responded with speed and precision, which was a great help.
A worker transfers a container filled with products to the conveyor.
Products are conveyed to the dispatch area.
Vehicles automatically recharge as needed.
Cutting Work Time by More Than Half
What impact has the system had since installation?
When introducing any material handling system, our top priorities are stable operation and improved productivity. We trusted that the system, like the main conveyor we already had in place, would provide a reliable foundation, and in practice, we’ve been very satisfied with both the system’s performance and the accuracy of the sorting.
In terms of productivity, the time required for sorting small items has been reduced to just three hours with five people—less than half of what it used to be. That’s a significant improvement compared with the manual process we had previously. Although internal coordination was a challenge, the results have exceeded our expectations, and we’re glad to have installed the system. Going forward, we plan to continue advancing automation through digital transformation, and to reinvest the capacity we’ve gained into other tasks and new initiatives.
What plans do you have for the Misato Distribution Center in the future?
At Nojima, we promote a unique sales strategy called “consulting sales,” which focuses on understanding the needs of customers and providing the most suitable products. Because the growth and success of each employee are essential to this approach, we don’t define ourselves primarily as a home electronics retailer, but rather as a “people development company,” and we embrace the philosophy of nurturing talent, giving opportunities to everyone regardless of their tenure, age, or employment status. In line with our guiding principle, “Each employee cultivates the mindset of management,” we encourage every team member to think, make decisions, and take action like an entrepreneur.
This emphasis on individual initiatives extends beyond sales floors to all areas of our operations. For example, decisions about implementing material handling systems aren’t made solely by managers. It’s the on-site teams who raise issues, share ideas, and work together to find solutions. The decision to introduce the SOTR-S system also came from the voices on the ground, and I helped move the project forward as the main liaison.
Although we’re fortunate not to face labor shortages—thanks to our location in a residential area with a nearby train station—we remain committed to reducing the burden on our employees. Our next challenge is to automate the sorting and transport of large appliances like refrigerators. We’ll be working closely with the on-site team to explore concrete solutions moving forward.
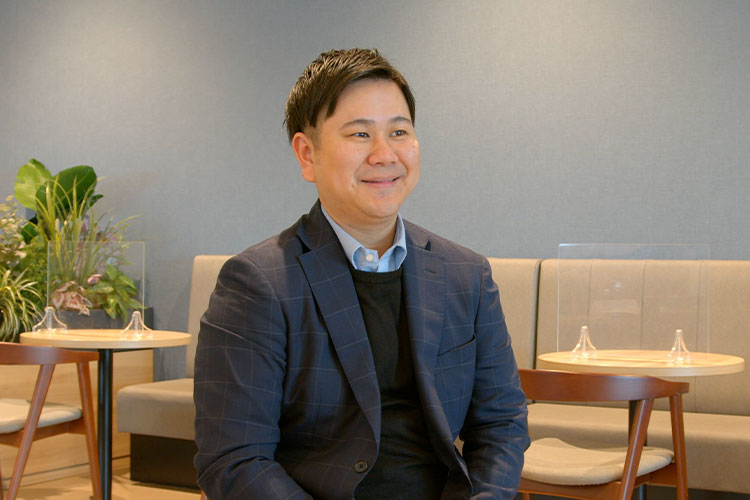
Yutaro Maruyama, Group Manager
Misato Logistics Solutions Group
Customer Relations Department
Nojima Corporation
Yutaro Maruyama joined the company in 2014 and was appointed department leader after working just one year in in-store sales. He went on to serve in the Human Resource Development Group and the Logistics Solutions Group at the company’s head office before transferring to the Misato Distribution Center in 2022, where he currently leads operations.