Essential Daifuku Technologies for Social InfrastructureHelping Reduce Staff Workload at US Airports with the “MIT” AGV-Based Inspection Table
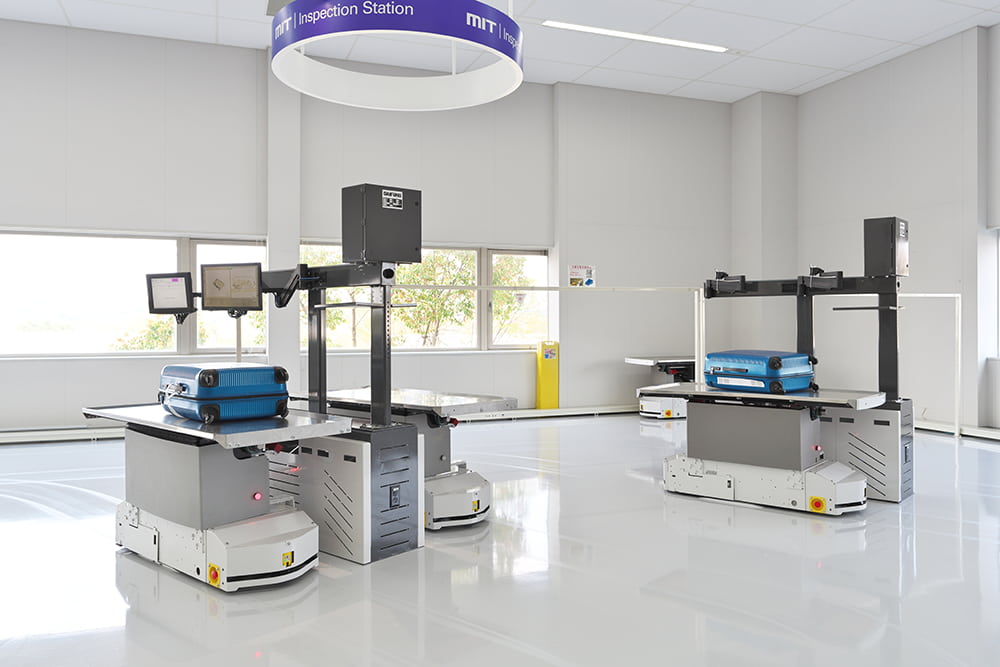
The table height can also be adjusted to make inspections easier for staff.
To ensure safety, airports screen passenger baggage for dangerous items before loading them onto the aircraft. At US airports, TSA* staff move baggage requiring additional inspection to an inspection station. After the safety of the baggage has been confirmed, the staff return the baggage to the conveyor. The MIT’s AGV-based inspection platform helps reduce the workload on staff during this process. Daifuku sat down with Garrett Kelly, Executive Manager of Sales, Marketing, and Estimating, and Nick Ellens, Executive Manager of Autonomous Technologies and Software, at Daifuku Airport America Corporation—the company that developed the MIT technology—to discuss the system and its advantages.
- * TSA: Transportation Security Administration; responsible for security inspections at airports in the US.
The MIT system: Reducing the physical workload of transportation staff
What kind of product is the MIT? Could you give us an overview of the system?
Airports have two main routes: one for passengers and one for checked baggage. After checking in, passengers proceed to the boarding gates, and their checked baggage is carried by conveyor to what’s called the “make-up area,” where the bags are readied for loading onto the plane. Before they arrive at the make-up area, however, the baggage is screened for dangerous items, such as explosives. This screening inspection is performed while the baggage is on the conveyor. Cleared baggage continues on to the make-up area.
Baggage that does not clear the screening, however, is sent along a different route to the checked baggage resolution area, where each bag is inspected by security personnel.
At US airports, the TSA staff manually unload the baggage from the conveyor and take it to the inspection station. After inspection, cleared baggage is then carried and placed back onto the conveyor. Because bags can weigh more than 20 kg, lifting and lowering the baggage is physically demanding, and back pain is a common problem for staff. Accidents have also been an issue for many years.
The MIT solves such problems by using Automatic Guided Vehicles (AGVs) to move the baggage for further inspection. Baggage is loaded onto the MIT and transported to the inspection station, where TSA staff can inspect the bags directly on the MIT. Bags that pass inspection are then taken by the MIT back to the conveyor.
This means the MIT can significantly reduce the workload of staff and improve operations in the checked baggage resolution area. The MIT has also been praised by staff for improving work efficiency, freeing them from the manual labor of manually transporting each bag and allowing them to focus on inspections.
Could you give us a few examples of where the MIT system has been adopted?
One place the MIT system has been introduced is the Detroit Metropolitan Wayne County Airport in Michigan. This airport is one of the busiest in the US, serving more than 33 million passengers every year. Airports are always looking to automate and streamline their systems, and the MIT has not only increased baggage screening efficiency but also reduced the workload on staff by minimizing the amount of heavy lifting needed.
Detroit Metropolitan Wayne County Airport was the first US airport to adopt the MIT system. As one of the busiest airports in the country, the baggage load is very high. Taking advantage of technology is essential for transporting such large numbers of bags quickly, safely, and reliably.
Development of Daifuku’s proven industrial AGVs for airports
While AGVs are used in a variety of applications, what makes the MIT system’s AGV different?
The MIT is essentially a modified industrial AGV developed by Daifuku for use specifically in airports. For example, a tilting table is included to automatically slide inspected baggage back on to the conveyor. We also used stainless steel for a smooth surface and easy cleaning.
What breakthrough technologies did you develop for this system?
The top-loading technology and control system used to load the baggage on to the MIT was adapted for use with AGVs from the system used in our baggage tray systems. We also developed an AGV control system with adjustable obstacle avoidance tolerances for efficient transportation of baggage. These technologies, combined with a new fleet manager to manage all the AGVs and a PLC for automating equipment control, mean the MIT system can solve a variety of problems for airports.
What key features and benefits can an airport expect from introducing the MIT system?
In short, the MIT system offers the following advantages.
- TSA staff no longer have to hand-carry heavy baggage to inspection tables, helping to reduce back pain and alleviate workloads.
- Inspections can be performed at a specified location with greater efficiency.
- Power consumption is lower than conventional conveyor systems.
- Noise levels are lower than conventional conveyor systems.
- Operation routes can be changed as needed simply by moving the magnetic tape on the floor.
- The MIT’s inspection table is the same size as conventional inspection tables but easier to handle.
- Multiple bags can be easily organized for inspection, helping to increase operation times.
- The system includes multiple AGVs, so even if an error occurs, baggage transfers will not be delayed.
Improving the system to make it even better
Can the MIT be used in any airport?
The MIT system is best suited for medium and large airport terminals, either with new airports or when updating the baggage inspection stations. The reason being that there must be enough space to ensure safety with multiple MIT platforms being used.
That said, adopting the MIT system is easier than installing a conveyor system, and layout design is also simpler with no need for installing rails on the floor. The layout can also be changed after installation, so the MIT system should really be thought of as a long-term investment.
Are further improvements to the technology possible?
The MIT platforms are battery-powered, and there are charging points on the floor along the transportation route. So, large-capacity lithium-ion batteries are one way to further improve the system, but we are constantly working on improving the charge balance algorithm as well to make the system even better.