Safety First: The Foundation of Daifuku’s Health and Safety Initiatives
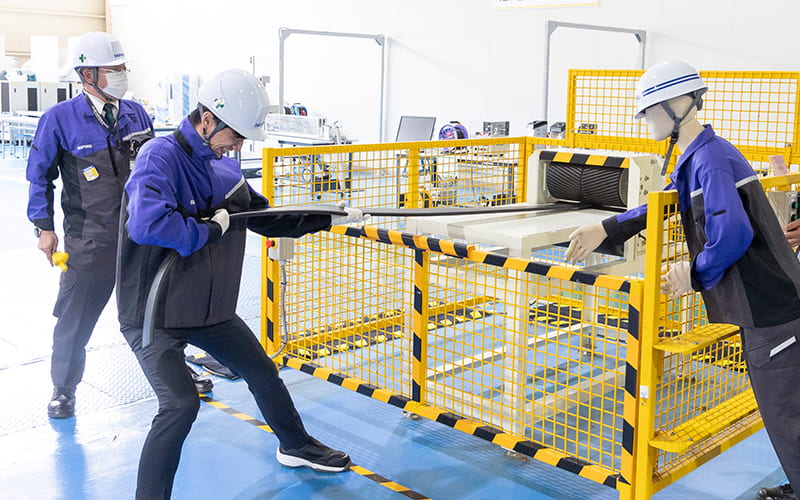
To establish a corporate culture that prioritizes the safety and health of workers at every Daifuku workplace, we have developed a framework for promoting safety and health management across the entire supply chain, including employees, partner companies, and suppliers. Developing personnel who possess not only skills and knowledge but also a high awareness of possible dangers and the ability to respond effectively, is essential for ensuring workplace safety. This article introduces initiatives at Daifuku’s Safety Simulation Center, a special facility where personnel can receive safety education and awareness training through simulated operational hazards.
Safety and health activities across the supply chain
The Daifuku Group operates under the concept that safety is the foundation of our business activities and supersedes all else. To instill this corporate culture, Daifuku established the Central Safety and Health Committee. The committee is chaired by the CEO and regularly reports and shares updates on safety and health. We are also actively promoting safety and health activities for all employees, contractors, and suppliers working at locations both in and out of Japan.
The Analysis of Occupational Accidents in FY2023 published by the Japan Ministry of Health, Labour and Welfare classifies occupational accidents in the manufacturing industry into five types: being caught/trapped, falling, falling to a lower level, reaction or unreasonable action, and cuts and abrasion. In FY2023, the most frequent type of accident in the manufacturing industry was being caught/trapped, followed by falling.
The Daifuku Group’s occupational accident trends reflect these national trends, with being caught/trapped, falling, and falling to a lower level being the most common types of accidents in recent years. Such trends in occupational accidents highlight our need to focus on safety education to prevent accidents throughout the Group.
Emphasizing actual hazards to the Safety Simulation Center’s 9,500 participants
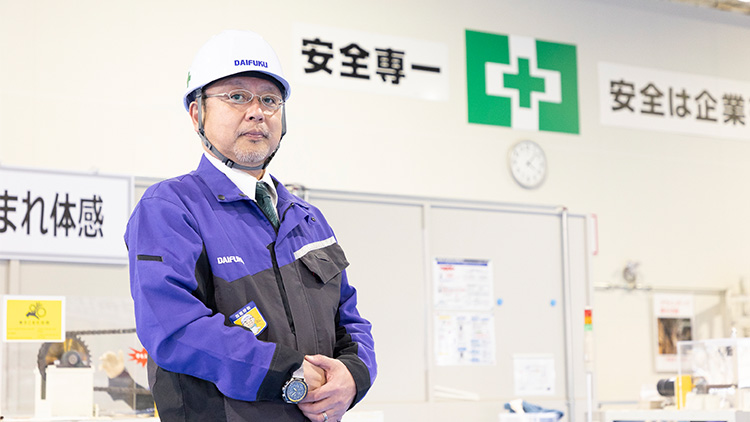
Koji Fukuda
Center Director
Safety Training Center, Safety Management Department, Safety and Health Management Division
Daifuku Co., Ltd.
In addition to classroom-based education on general safety for employees and site management for supervisors, the Daifuku Group provides practical training at the Safety Simulation Center, where participants can experience hazards rather than just learn about them. “Our goal is to teach participants through practical experience so that they can work with safety in mind,” says Safety Education Center director Koji Fukuda.
First opened at Daifuku’s Osaka head office in June 2010, the Safety Simulation Center is now located at Shiga Works. The facility is mainly intended for employees of the Daifuku Group and partner companies in Japan, and as of the end of FY2023, has trained roughly 9,500 people. About 60 training sessions conducted by instructors from the Safety Education Center are held every year, and regular participation is encouraged.
Expanding safety management methods developed in Japan
When evaluating occupational accident occurrence rates, indicators such as the frequency rate and severity rate are analyzed. In FY2022, the Daifuku Group’s frequency and severity rate were both below Japan’s manufacturing industry national average.
Since establishing the Safety and Health Management Division in 2014, we have been steadily strengthening our safety activities, which has allowed us to achieve such results. “We are proud of our record of keeping occupational accidents below the national average, but as there are still accidents occurring, we are determined to reduce these even further,” says Mr. Fukuda.
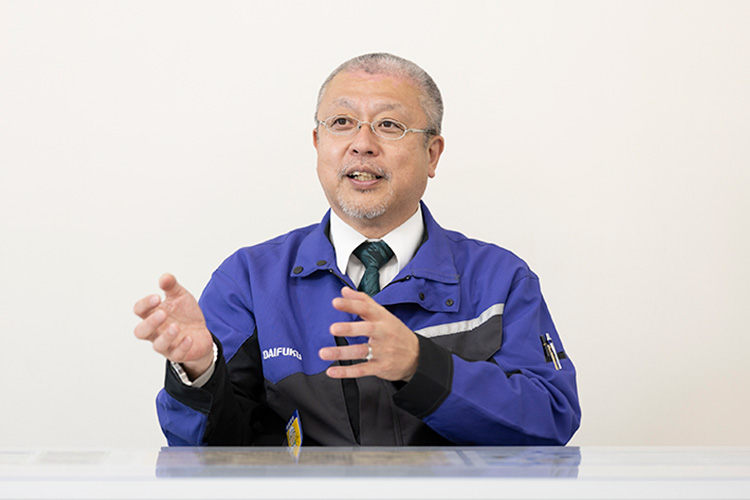
Mr. Fukuda discusses his goals for thorough safety awareness.
Daifuku is also dedicated to promoting the establishment of Safety Simulation Centers at Group companies, with similar facilities currently available in China, Thailand, and Indonesia. “Compared to Japan, the frequency and severity of occupational accidents tend to be higher at our Group companies, so we are trying to expand the safety management methods developed in Japan to our global offices,” says Mr. Fukuda.
Enhancing awareness of potential hazards through simulated experiences
The Safety Simulation Center aims to prevent the recurrence of occupational accidents that have occurred within the Group and includes occupational accident exhibits; hands-on workshops for electrical safety, being caught/trapped, flying/falling objects, falling to a lower level, and general work conditions (falling, back pain, etc.); and information on identifying hazards. Participants experience a variety of occupational hazards and learn when they are likely to face such dangers.
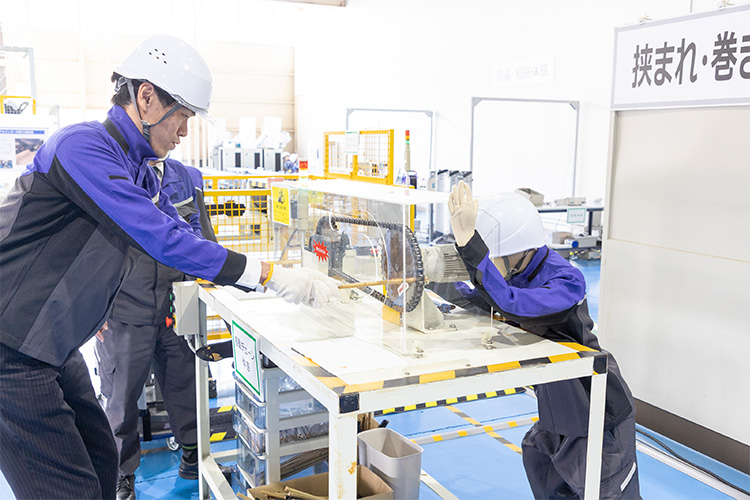
This exhibit uses wooden rods to show a simulated experience of becoming caught in machinery.
For becoming caught/trapped, participants experience several situations where their hands or arms can be caught in operating machinery in the factory. These simulated experiences allow participants to learn about the strong force of rotating machinery, the instinctive reactions of one who becomes caught, and how familiarity can lead to a relaxed awareness of danger. These experiences help reaffirm the importance of caution around machinery and the reasons behind established rules.
For the workshop on falling to a lower level, participants are taught the importance of always wearing safety harnesses when working at heights by observing a 75 kg mannequin’s violent fall from a height of 3.5 m. Participants can also experience the sensations involved with a fall accident through VR equipment. These experiences help promote awareness of the dangers of working with heights.
-
A mannequin takes a violent fall from a height of 3.5 m.
-
A participant experiences a simulation of a fall accident using VR equipment.
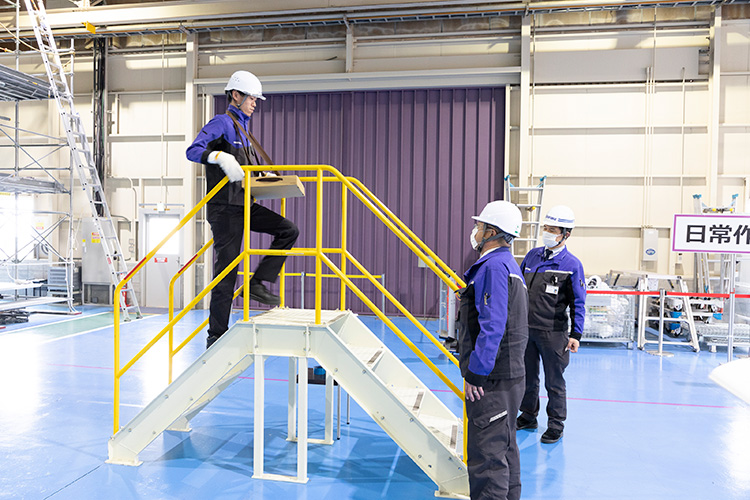
A participant ascends and descends stairs with slightly irregular spacing.
For general work-related falls, participants experience the risks of hazards that are easily overlooked. By climbing and descending stairs with modified step intervals and slopes while carrying items or looking at a handheld memo as if it were a smartphone, participants learn the importance of holding onto handrails as well as how distractions can lead to falls.
At the Safety Simulation Center, we will continue to give participants insights into everyday dangers through the abovementioned experiences and others to ensure the ability to apply these lessons in their work. We will continue to update and improve the content of these experiences going forward.
Continuing our focus on preventing occupational accidents
Even if we see a temporary drop in the number of occupational accidents, risks are always present. As such, continued promotion of safety and health awareness is essential. To ensure the Daifuku Group’s business endeavors remain sustainable, we will continue our emphasis on our safety-above-all culture and thoroughly promote safety and health initiatives throughout the supply chain.