Logistics ViewSafety Measures Should Assume People Will Make Mistakes and Machines Will Break Down
Various safety measures are implemented in factories and logistics centers. However, the on-site environment is constantly changing. It is impossible to completely eliminate unforeseen problems and mistakes. Maintaining a high level of safety requires what exactly? How will safety evolve with the emergence of new technologies? We asked Masao Mukaidono, Chairman of The Institute of Global Safety Promotion, Professor Emeritus of Meiji University, and a leading figure in safenology, a discipline that systematizes safety issues common to different fields.
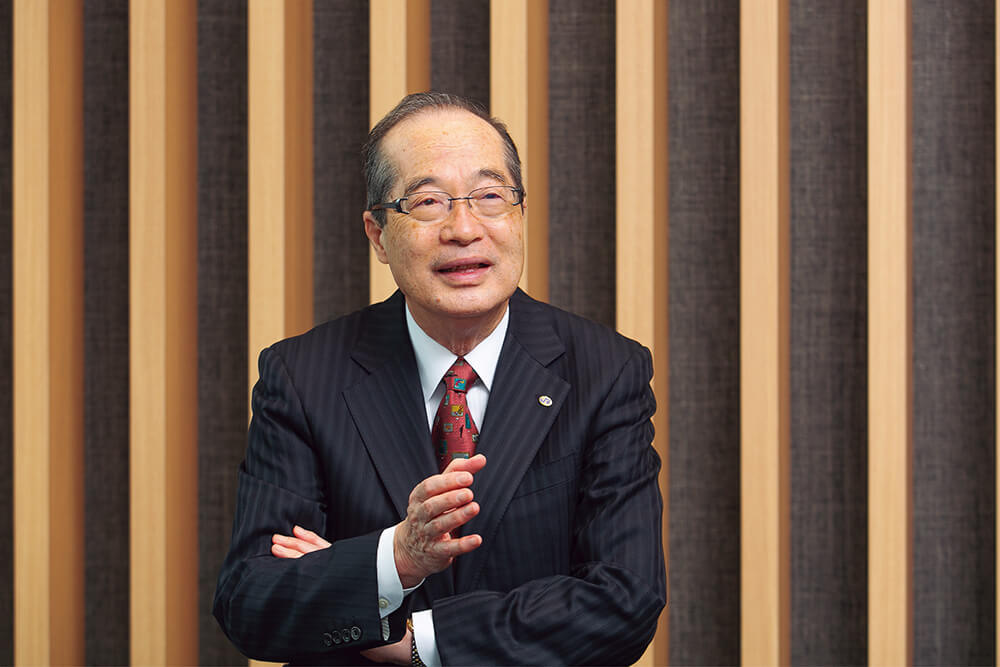
Masao Mukaidono
Chairman of The Institute of Global Safety Promotion
I've heard that your specialist area, safenology, is a relatively new discipline.
Research into safety has traditionally been carried out in separate fields, such as medical care, automobiles, nuclear power, and food, for example. Why is safety necessary? Because we want to prevent harm to people's lives or health, the economy, information, and the global environment. Although the things being protected are different, the thinking is similar so there are bound to be things that could be learned from other fields as well as elements that different fields have in common. However, the differences in the various definitions and terminologies obstruct communication.
I thought that, if we selected ubiquitous knowledge from various research fields and systematized it, we could use it as a foundation to carry out research and develop this new discipline. There is the discipline of safety engineering in the manufacturing field, but it focuses on engineering. Safety involves not just engineering and the natural sciences, but also the humanities, such as philosophy and ethics, as well as social sciences such as economics and law. Safenology deals comprehensively with all of them.
Safenology was conceived as communication between experts, but now I'd like top executives and the general public to know more about it. For example, experts make recommendations about infection control measures based on their scientific knowledge, but it is politicians that make decisions based on those recommendations and it is the general public that actually puts them into action. So, even though the experts may be very knowledgeable about safety, that in itself doesn't necessarily keep society safe.
How do safety awareness and approaches vary in different fields?
A certain amount of risk is sometimes permissible in medical care to protect a patient's life, while complying with industrial safety is a prime challenge in factories. I think it's true to say that in factories, where mechanization and automation are increasingly utilized, a situation where machinery operates smoothly and doesn't stop is a form of "safety." As you can see, the approach to safety depends on the field.
What they all have in common is that "there is no such thing as absolute safety." A kitchen knife may be safe for someone who knows how to handle it properly, but there's still a risk of injury. Nothing is risk-free. This way of thinking is shared throughout the world, but Japan has a strong tendency to insist upon safety, and to require absolute safety from manufacturers. It is not only manufacturers who are responsible for safety, but also the users and the countries that impose regulations. I want it to be common knowledge that all parties concerned need to accept risks and responsibilities in their respective situations.
Related terms
- Foolproof
- Safety measures are incorporated from the design stage onwards to prevent a product from becoming dangerous, even if mistakes are made in its use
- Fail-Safe
- Mechanisms are designed and constructed so that safety is always guaranteed even if they break down
- Fault Avoidance
- Creation of highly reliable parts and products by incorporating design and structural mechanisms that do not break easily
- *Based on "An Introduction to Safenology" by Masao Mukaidono and the contents of this interview
Collaborations with robots mean
DX is part of the safety field too
Even though nothing is risk-free, we must implement safety measures as far as possible. Please tell us about the important points of safety measures.
When thinking about safety we must assume that people will always make mistakes and machines will break down at some point. Since human error is more common than mechanical error, the order we should adopt when thinking about measures is to first think about how to make machinery and facilities mechanically safe, as it is the side with less possibilities, and then think about the human element.
Anyway, people will always make mistakes, so you design things not to proceed to the next step if some kind of mistake occurs. You set things up so that a slight mistake doesn't develop into an accident or incident. For example, making it so that a device won't work if the battery is the wrong way round, or a lid won't close if the battery is the wrong size. The word for this is "foolproof." Next you design machinery and facilities to ensure safety even if some kind of trouble occurs. For railways, halting operation is the ironclad rule. That's because it would be dangerous to recklessly keep trains running when you don't understand the root cause of the trouble. The word for such a method of ensuring safety is "fail-safe."
Recently we're starting to see cases where devices such as autonomous mobile robots are being installed in factories and logistics centers. What approaches do you recommend for their safety measures?
I suggest "collaborative safety" utilizing ICT (information and communications technologies) and DX (digital transformation) as the safety strategy of the future. This is an approach where information is shared between people, machines, and structures to collaboratively achieve safety.
One cause of accidents is the energy gap between human beings and machines. If they happen to come into physical contact, it will be the human, who has less energy, that will fare badly. To prevent that happening, the basic measures up until now have been "safety distances" where the operating areas of people and machines are kept separate, and "safety stoppages" where machinery is stopped when someone enters its operating area. Collaborative safety utilizing ICT is essential if autonomous mobile robots and people are to work in the same operating area.
Collaborative safety makes it possible to utilize information to avert risks, and to incorporate controls that decrease machine energy and alert workers. For example, if a someone is approaching, an autonomous mobile robot can alter its route to avoid contact or slow down to reduce impact if physical contact does happen, and a forced stop can be imposed if neither of those measures would be completed in time. People can also be alerted if a machine is approaching. (Diagram) Averting the danger before a total shutdown becomes needed is good for both safety and productivity. Going forward, it will doubtless be important to consider how best to utilize technology for collaborations between people and machines.
Please enlarge the screen to view
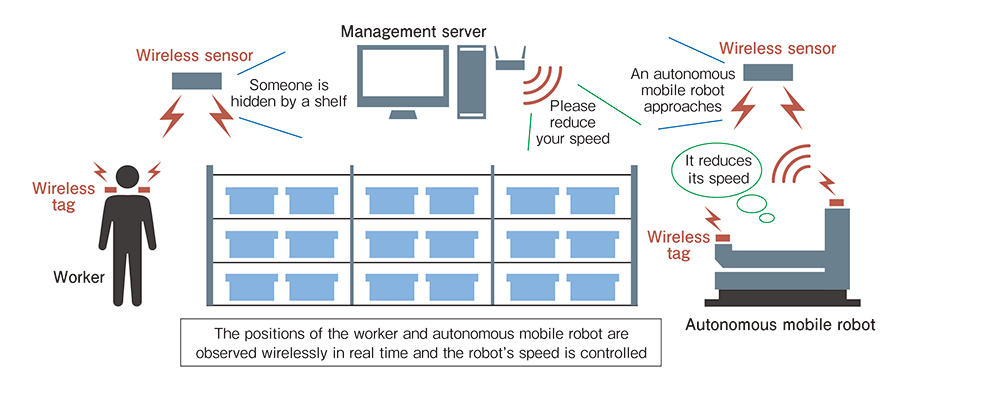
Please give us some examples of collaborative safety utilizing new technologies.
There's a company involved in road surfacing and maintenance that uses IC tags to reduce work accidents. A heavy machine called a tire roller is used in road surfacing, and apparently it can sometimes hit workers when it's reversing if the operator doesn't notice that they're there. So, the company developed a system where workers wear IC tags and the tire roller automatically performs an emergency stop if a worker accidentally enters the area behind it. The tire roller only senses the area behind it, and it doesn't stop if there are people working in front of it or to the side so work can proceed smoothly.
There's also a construction company that utilizes ICT for work inside tunnels. Tunnels are high risk areas because they are cramped and dark, and workers and machines are crowded together. So, the company operates a system that matches qualifications with the level of difficulty of the work. There are restrictions on which workers can engage in high-risk tasks. Workers wear an IC tag containing information about their qualifications, and their movements in and out of the tunnel, and their current location, are monitored. Apparently, a red lamp and alert are triggered, and the machinery stopped, if an unqualified worker has entered a danger zone. In combination with equipment such as an image recognition system, it also monitors the physical condition of the workers based on the temperature and humidity inside the tunnel.
We've started a demonstration experiment of warehouse stocktaking using drones. What kind of safety measures are required?
Drones are machines so eventually they will break down, and they can't be controlled if telecommunications are interrupted. Those considerations are the starting point for safety measures. If some kind of trouble occurs while a drone is flying, you'd want to shut it down just as you would when controlling a machine, but there's the danger of it falling into an area where people or machines are operating if it comes to a sudden stop while in mid-flight. The ideal would be for the drone to be capable of an autonomous soft landing. There's also the possibility that it would become incapable of autonomous flight, so it would be a good idea to have some mechanism in place for it to come down safely, such as making a slow descent or a parachute opening. Those don't involve difficult technologies. It would be sufficient to install a self-checking program and to design the drone so that a fail-safe comes into operation if the program detects a telecommunications or control error.
Do the drones in use today contain such mechanisms?
In Japan, there are airspace segregation rules that limit the areas in which drones can be used, but at the present time hardware safety measures are left to the manufacturer. Given that drones are becoming more widely used, I think the government should set safety standards for them.
Methods to achieve safety fall into two categories: preemptive prevention and prevention of recurrence. Although you want to prevent all accidents from occurring, doing so preemptively for all levels of severity will lead to overly strict safety standards that will prevent new technologies from being developed.
We must hypothesize the severity level of accidents, so that when developing safety standards there is leeway for some amount of risk to be taken, while still preventing any serious accidents from occurring. Then, prevention of recurrence comes into play. After preemptively mitigating serious risk, other issues can be adapted to through trial and error while the new technology is being developed. I think the ideal form is to be able to actively develop new technologies while still implementing safety measures through a mix of preemptive prevention and prevention of recurrence.
Boost safety awareness
Accurate knowledge aids corporate growth
Technology is used by people, so we also need to provide safety training, don't we?
Some business owners think that safety is a matter of course, but that's not the case at all. The staff responsible for safety in factories and logistics centers put in a lot of effort on a daily basis. Safety is important for everyone, so I think the people in charge of it should receive more recognition, and I'd like each individual employee to become more aware of safety.
The Institute of Global Safety Promotion has certification systems for qualifications as safety assessors and safety officers. The former qualification is primarily for people who design machinery, and the latter is a training certification system for executives, including top management, as well as for managers and staff.
This system of qualifications can be utilized in safety training, and the number of people who have gained certification serves as a criterion to assess a company's safety initiatives. There is also the safety basic assessor qualification for people who use machines. It covers content that we would like everyone involved in machine operations to know. Acquiring accurate knowledge and insights about safety in greater depth can be expected to drive safety throughout a company and be an effective aid to corporate growth and boosting corporate value.
What kind of communication is needed so that a company and its customers can jointly create safety? Please share your thoughts about this.
Important elements in the communication linking a company and its users include: transparency, active disclosure of information, and accountability. In addition to disclosing information on how safety is structured and on what risks there are in a worst-case scenario, it's essential to communicate to reach a consensus on residual risks and arrive at a mutual agreement. A company must not simply unilaterally convey what it wants to say; it must also listen to what its clients and end users have to say.
I will say it again: whatever safety measures you may take, nothing is risk-free and there's no such thing as absolute safety. When trouble does occur, while any financial loss can be made up for afterwards, human lives and people's trust once lost can never be regained. Accurately understanding and promoting safety aids corporate growth and helps to boost corporate value.
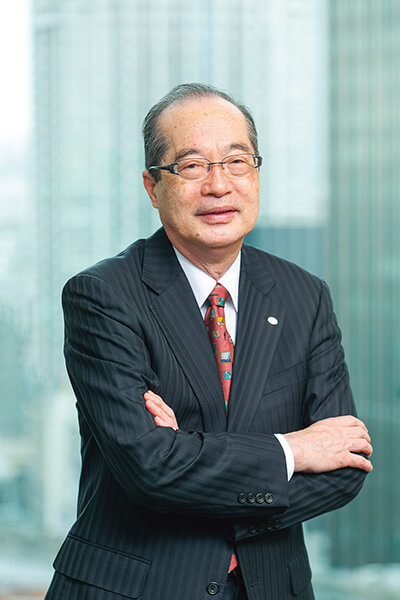
Masao Mukaidono
Born in 1942. Meiji University Honorary Advisor, Professor Emeritus, and Chairman of the Meiji University Alumni Association. Chairman of the Railway Technical Research Institute. Chairman of the Japan Universities Association for Computer Education. Chairman of The Institute of Global Safety Promotion. Doctor of Engineering upon completion of the doctoral course of the Graduate School, Division of Engineering, Meiji University. Previous positions include associate professor in the Department of Electrical Engineering, Faculty of Engineering, Meiji University; professor in the Department of Computer Science, Meiji University School of Science and Technology; and dean of the Meiji University School of Science and Technology. Specializes in safenology, informatics, and logic. Has also served in positions such as chairman of the Japan Society for Fuzzy Theory, and chairman of the Reliability Engineering Association of Japan. Received the 2015 Prime Minister's Commendations on Contributors to Public Safety.
- *This article is based on the content of "Logistics View: Thinking about Safety on the Assumption that People Make Mistakes and Machines Break Down" featured in DAIFUKU NEWS No. 230 (published in April 2021).