Khám phá giải pháp lưu trữ lý tưởng cho hàng hóa và vật liệu dài
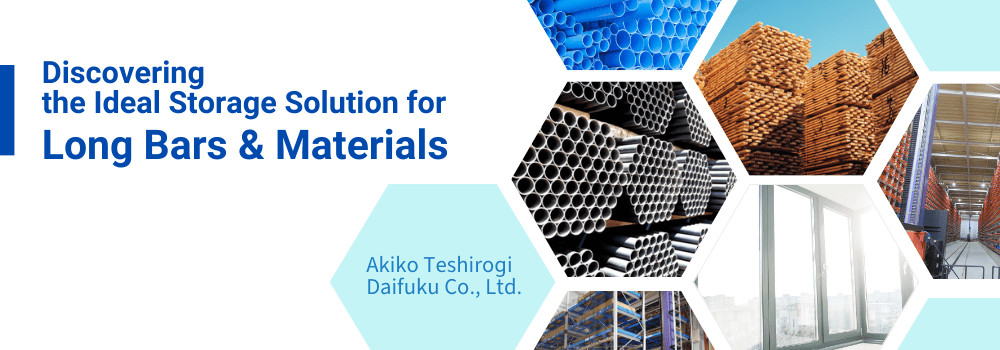
Bắt đầu hành trình tìm hiểu thông tin chi tiết về kho hàng, trong blog trước đây của tôi vào năm 2022, chúng tôi đã khám phá sự phức tạp của Tải trọng Hình tròn trong Tự động hóa Kho hàng – Biết các lựa chọn thay thế cho Cuộn của bạn. Hôm nay, chúng tôi tập trung vào một thách thức đặc biệt khác gặp phải trong tự động hóa kho hàng—xử lý tải trọng dài. Mặc dù nhu cầu của nó tương đối nhỏ và thích hợp nhưng nhiều công ty vẫn phải đối mặt với những thách thức trong việc quản lý hiệu quả các mặt hàng này. Hãy tham gia cùng tôi khi chúng tôi đi sâu vào hai giải pháp để xử lý tải lâu.
Các vật thể dài trong nhà kho và nhà máy
Nhu cầu chủ yếu về hệ thống lưu trữ và truy xuất tự động (AS/RS) chủ yếu tập trung vào các pallet tiêu chuẩn công nghiệp, bao gồm pallet Euro, pallet JIS, pallet GB, pallet Mỹ và các biến thể tiêu chuẩn quốc gia khác, thường nằm trong phạm vi 1.200 x 1.200 mm. Đôi khi, chúng tôi làm việc với những khách hàng đang tìm kiếm giải pháp cho kích thước tải vượt quá phạm vi này một cách đáng kể, từ 2 m đến hơn 6 m. Họ thường xử lý những gì?
Các yêu cầu chính thường bắt nguồn từ các nhà bán buôn thanh và ống kim loại, theo sau là các công ty sản xuất đa dạng xử lý các nguyên liệu thô dài hoặc các sản phẩm đang trong quá trình sản xuất. Trong miền này, các mặt hàng được lưu trữ bao gồm nhiều loại, bao gồm đường ống, thanh kim loại, vật liệu xây dựng, khung cửa sổ, gỗ xẻ, bộ phận máy bay, bộ phận xe lửa, đồ nội thất, thân ô tô, v.v.

Thanh kim loại
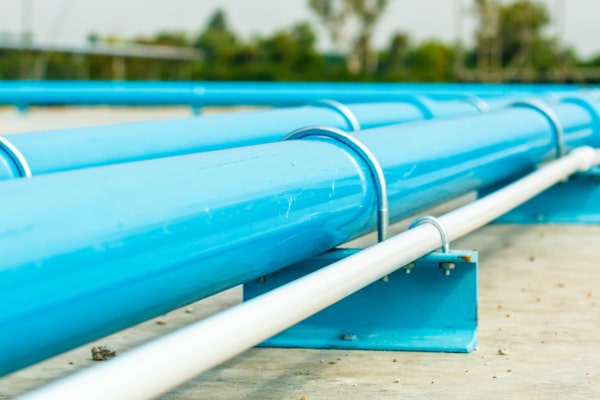
Ống nước
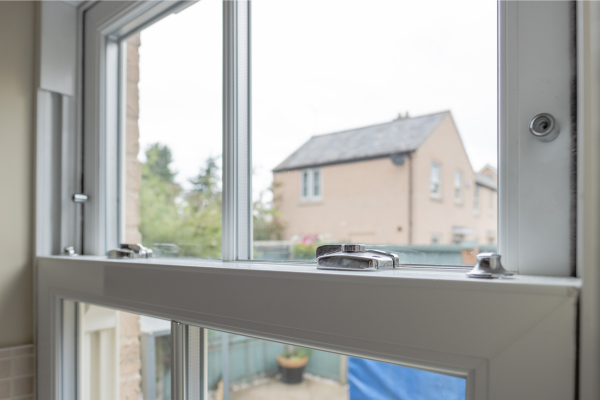
Rèm cửa sổ
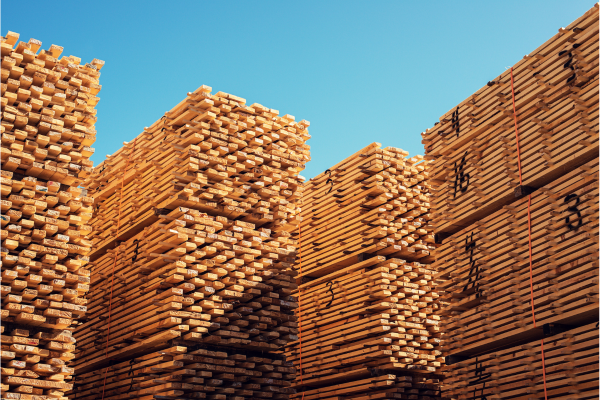
Gỗ xẻ
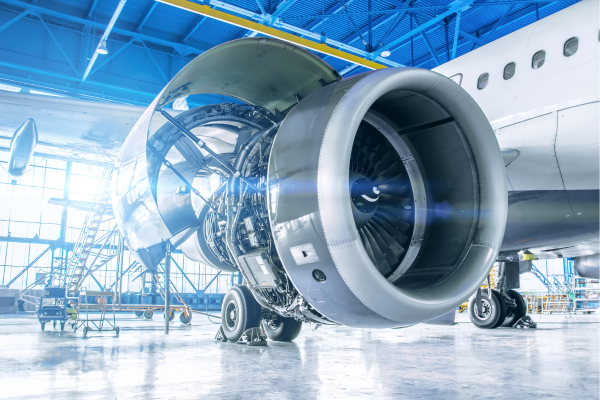
Bộ phận máy bay
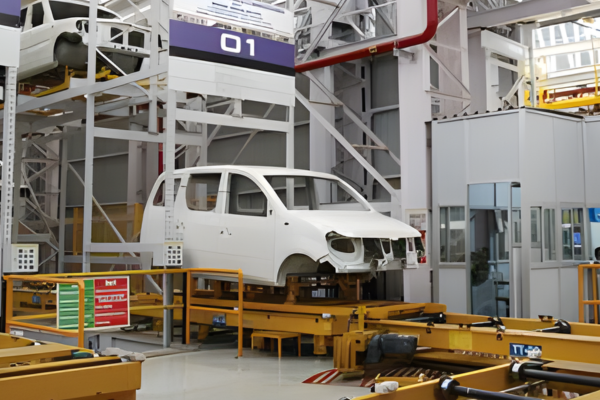
Thân ô tô
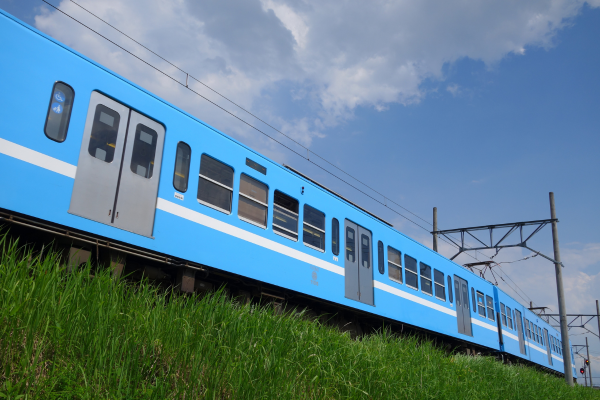
Thành phần đoàn tàu
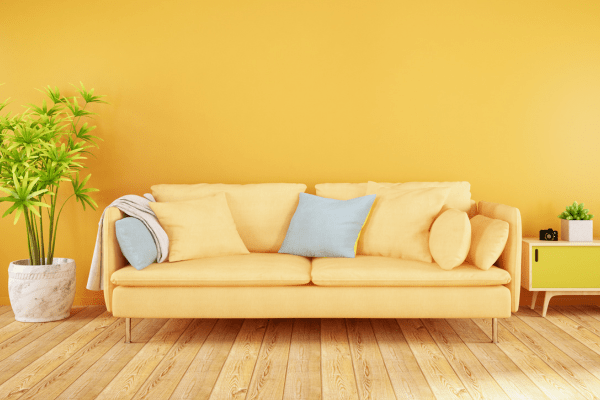
Nội thất
Các vật thể dài được xử lý như thế nào trong một hệ thống tự động?
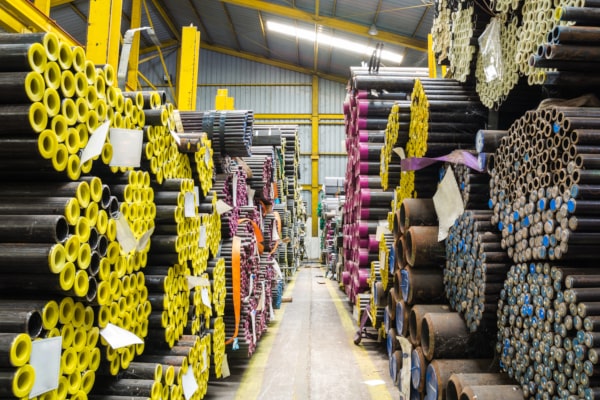
Nếu tự động hóa không được áp dụng, chúng tôi thấy rằng các mặt hàng dài thường được lưu trữ trên sàn, xếp chồng lên nhau. Nhưng cách tiếp cận đó đặt ra những vấn đề và khó khăn sau:
- Chiếm không gian sàn đáng kể.
- Tác động đến việc cung cấp các mặt hàng phù hợp một cách suôn sẻ, kịp thời cho sản xuất hoặc vận chuyển.
- Cản trở sự an toàn tại nơi làm việc do có khả năng sập tải.
- Cản trở tính chính xác của việc quản lý hàng tồn kho.
Tại Daifuku, chúng tôi đã giải quyết những nhu cầu thị trường này kể từ dự án AS/RS đầu tiên cho các thanh thép 6,2 mét vào năm 1986 và kể từ đó chúng tôi đã phát triển hai giải pháp lưu trữ tự động chính.
Càng nâng AS/RS
Giải pháp lưu trữ phổ biến nhất là lấy tải bằng hai càng nâng từ dưới lên. Điều này đặc biệt phù hợp với các công ty sản xuất muốn tận dụng không gian hạn chế dọc theo bức tường nhà xưởng. Ví dụ: khi sử dụng hệ thống AS/RS để lưu trữ các pallet thép có kích thước 6,2 x1,0 m, hệ thống này thường yêu cầu chiều rộng khoảng 3,6 m. Đầu vào và đầu ra của AS/RS có thể được thực hiện từ cuối lối đi của cần cẩu hoặc từ phía giá đỡ, tùy thuộc vào nhu cầu vận hành.
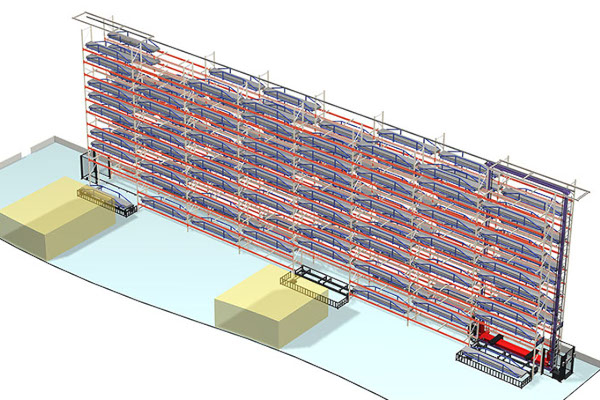
Băng tải nạp/ra và máy cắt được đặt ở hai bên của giá đỡ. Cấu hình này đảm bảo việc thu hồi, gắp và cấp liệu cho máy cắt diễn ra suôn sẻ.
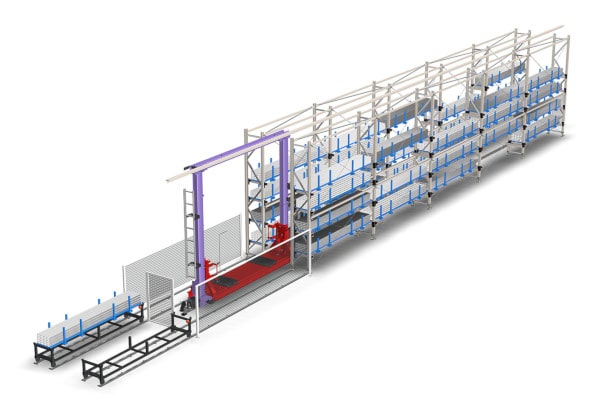
Băng tải đầu vào/đầu ra được đặt ở cuối kho tự động. Chiều rộng cài đặt có thể được giảm thiểu.
AS/RS với giá đỡ tổ ong và cần cẩu xếp kéo đẩy
Vào năm 2015, Daifuku đã cung cấp cho Sakuma Special Steel AS/RS dạng tổ ong cho các thanh thép dài 6,2 mét. Hệ thống này bao gồm hai cần cẩu xếp chồng được trang bị máy kéo đẩy và giá đỡ kiểu tổ ong sâu chứa hơn 2.500 vị trí pallet, cho phép lưu trữ mật độ cao khối lượng lớn ở một nơi. Hệ thống này độc đáo ở chỗ tải được lưu trữ theo hướng xoay 90°, so với việc xử lý càng nâng con thoi.
Mặc dù hệ thống cung cấp mật độ lưu trữ vượt trội so với giải pháp extractor càng nâng, nhưng nó có nhược điểm là chu kỳ lưu trữ hoặc truy xuất lâu hơn do cần cẩu phải đẩy và kéo tải trọng 6,2 mét đến và đi từ giá đỡ. Daifuku đã khắc phục vấn đề này bằng cách áp dụng giải pháp cần cẩu kép, một hệ thống trong đó hai cần cẩu xếp chồng hoạt động đồng thời trên cùng một lối đi.
Mặc dù mật độ lưu trữ của hệ thống extractor đẩy có vẻ hấp dẫn nhưng nó không phải là giải pháp phổ biến cho mọi doanh nghiệp. Vì phương pháp lưu trữ này yêu cầu không gian có chiều rộng khoảng 19 m nên nó có thể không lý tưởng cho những người đang tìm kiếm kho lưu trữ có khối lượng trung bình trong không gian nhà xưởng hoặc nhà kho hạn chế. Vì lý do này, nó thường được khuyến nghị cho các doanh nghiệp xử lý khối lượng lớn trong môi trường nhà kho chuyên dụng, chẳng hạn như nhà phân phối và bán buôn vật liệu kim loại.
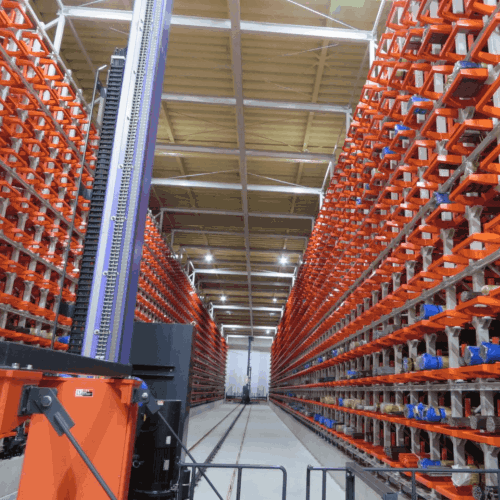
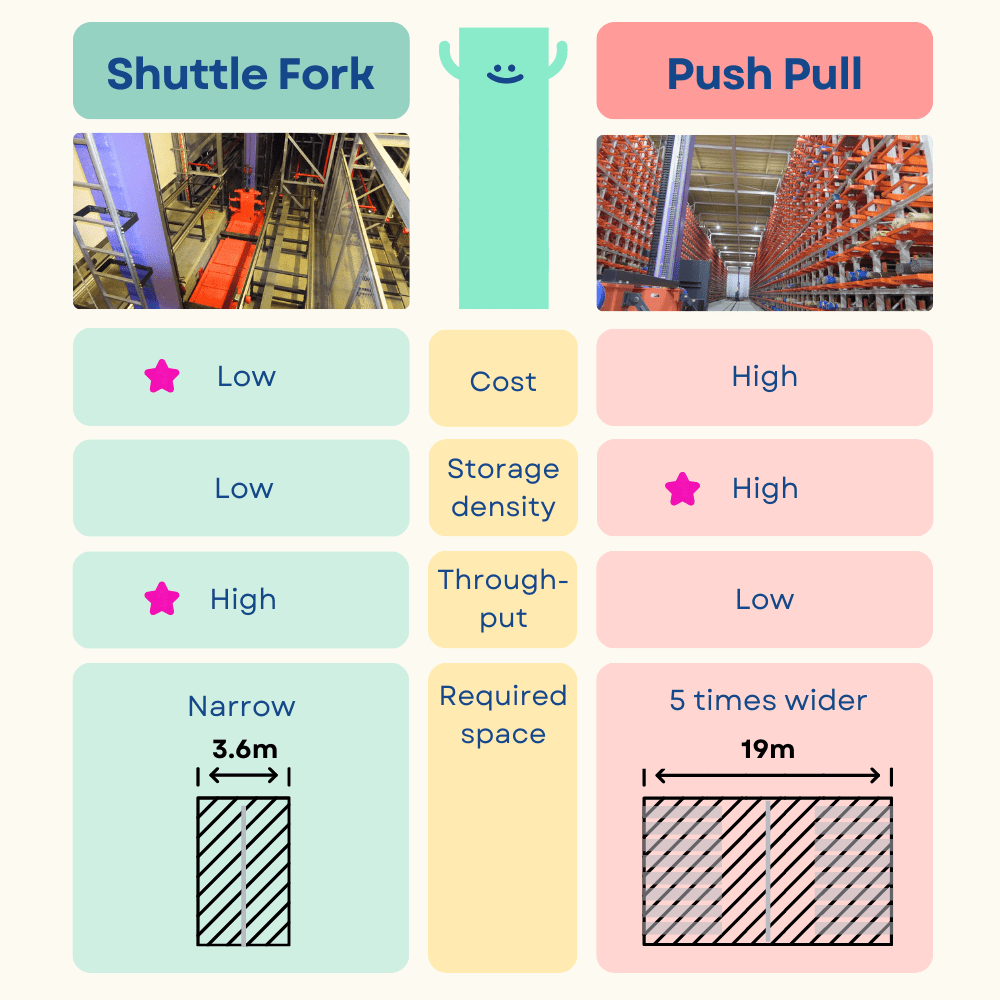
Cách chọn giải pháp tốt nhất cho những món đồ dài của bạn
Việc quản lý các mặt hàng có hình dạng kỳ lạ thường đòi hỏi sự thận trọng và thời gian hơn so với việc xử lý các pallet tiêu chuẩn công nghiệp. Nếu bạn muốn nâng cao hiệu quả và độ an toàn khi xử lý các mặt hàng dài, hãy cân nhắc việc đánh giá khối lượng bạn cần lưu trữ tại chỗ, tần suất truy xuất và không gian sẵn có. Những cân nhắc sau đó sẽ hướng dẫn bạn chọn giải pháp nĩa con thoi hoặc giải pháp tổ ong. Không chắc chắn về việc bắt đầu từ đâu? Hãy liên hệ với đội ngũ bán hàng toàn cầu của chúng tôi để được tư vấn.
Akiko Teshirogi
Trưởng phòng tiếp thị, Daifuku Intralogistics
Akiko Teshirogi là giám đốc tiếp thị của doanh nghiệp Intralogistics tại Tokyo, Nhật Bản. Bà đã tham gia vào hoạt động bán hàng và kỹ thuật của các hệ thống tự động hóa kho trong hơn 15 năm. Từ năm 2015, bà đã thúc đẩy các hoạt động tiếp thị cho doanh nghiệp Daifuku Intralogistics.