자동차 조립 라인용 Daifuku 컨베이어 시스템의 역사
1957년에 Daifuku는 세계 최고의 컨베이어 제조업체 중 하나인 미국 회사인 Jervis B Webb International Co..와 체인 컨베이어 기술 제휴를 맺었습니다. 1957년에 Daifuku는 첫 번째 제품인 트롤리 컨베이어를 Toyota Auto Body Co., Ltd.의 Kariya 공장에 납품했습니다. 해당 연도 국내 자동차 생산량은 약 18만2000대로 1955년의 3배에 달했다. 1957년은 일본 자동차 제조사들이 자동차를 대량 생산하기 시작한 해다. 미국에서 널리 사용되던 Webb 형 체인 컨베이어가 일본에서 최초로 출시되었습니다.
다음은 일본 자동차 산업 성장의 원동력이었던 Webb 형 체인 컨베이어부터 현재의 주요 모델인 새로운 Flexible Drive System까지 Daifuku의 자동차 조립 라인용 컨베이어 시스템 개발에 대해 설명합니다.
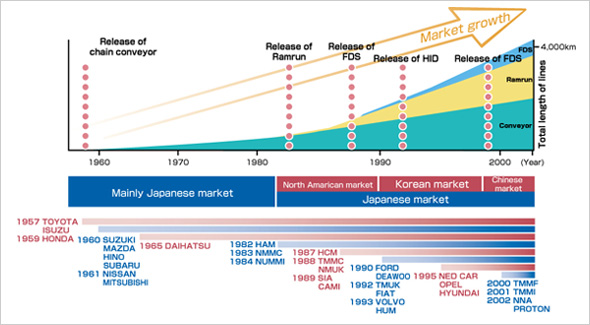
보려면 화면을 확대해 보세요.
체인 컨베이어 시스템
Webb 체인컨베이어에 사용되는 체인의 가장 큰 장점은 단조강으로 제작되어 리벳리스 구조로 되어 있어 매우 견고하고, 손으로 쉽게 조립 및 분해가 가능하다는 점입니다. 가파른 경사각과 유연한 레이아웃이 가능한 경하중 이송용 U 컨베이어 체인과 높은 절단강도를 갖춘 중하중 이송용 JX형 체인의 두 가지 유형이 있습니다. Daifuku의 체인 컨베이어 시스템은 머리 위 및 바닥 설치에 사용할 수 있습니다. 트롤리 모델과 Daifuku Magic 모델도 사용 가능합니다. 다양한 운송 조건에서 사용할 수 있습니다(그림 1). 높은 기능성과 신뢰성은 현재 구성에서도 여전히 유용합니다. 우리는 자동차 제조업체뿐만 아니라 다른 업계의 제조업체에도 많은 체인 컨베이어를 납품해 왔습니다.
Daifuku Magic Conveyor는 직접 걸이 구성에서만 사용할 수 있었던 트롤리 유형 컨베이어의 발전입니다. Daifuku Magic Conveyor는 축적을 포함하여 복잡한 운송 레이아웃을 수용할 수 있습니다(사진 1). 1957년, Daifuku는 Tsurumi 공장의 엔진 조립 라인을 위해 Isuzu Motors Limited에 최초의 Daifuku Magic Conveyor를 납품했습니다. 이 특별한 컨베이어 시스템은 당시 조립 라인에서 널리 사용되었던 기존의 롤러 컨베이어를 대체할 혁신적인 제품으로 주목받았습니다. 이후 승용차용 신규 공장 건설이 급증하면서 컨베이어 모델에 대한 주문이 급증했다.
-
그림 1: 체인 컨베이어의 유형
-
사진 1: Daifuku Magic Power & Free Roller Conveyor (Overhead Type)
1980년대 초반 일본에서 미국으로의 자동차 수출이 180만 대에 이르고 북미에서 일본 자동차의 시장 점유율이 20%를 넘으면서 일본과 미국 사이에 무역 갈등이 표면화되었습니다. 일본 자동차 회사는 해외 사업과 현지 생산을 계속 확장했습니다. Daifuku는 Honda Motor Company의 Ohio 공장과 Nissan Motor Company의 Tennessee 공장을 비롯한 많은 공장에 다양한 유형의 컨베이어 시스템을 공급했습니다. 한편, 자동차 생산 수요가 증가하면서 생산 라인의 자동화가 시급한 과제가 되었습니다. 산업용 로봇의 구현은 그 기간 동안 절정에 달했습니다. 그러나 체인 컨베이어가 산업용 로봇의 빠른 움직임을 따라가지 못하여 생산 효율이 좋지 않아 새로운 운송 시스템에 대한 요구가 나타났습니다.
1983년에 Daifuku는 RAMRUN 모노레일 시스템을 개발했습니다(사진 2). 같은 해에 우리는 Toyota Motor Corporation의 모토마치 공장과 Kanto Auto Works Ltd.의 Higashi-Fuji 공장에 각각 첫 번째와 두 번째 RAMRUN을 납품했습니다. RAMRUN의 가장 큰 장점은 컴퓨터로 제어되는 연속, 간헐적 운전으로 고도화된 자동차 생산라인 구축이 가능하다는 점이다. 최대 전송 속도 120m/분, 전송 범위 1:20 등 고성능 외에도 다음과 같은 이점도 있습니다.
- 로봇 작업 뿐만 아니라 수작업에도 적용 가능
- flexibe 배치 허용
- 기능 확장 및 축소 용이
- 조용하고 깨끗하며 먼지가 적음
- 미려한 외관과 쾌적한 작업환경 조성에 기여
Daifuku RAMRUN은 당시 고객의 요구를 정확히 충족했습니다. 그것은 매우 잘 팔렸고 Daifuku의 베스트 셀러 제품 중 하나가 되었습니다. 선형 유도 전동기가 설치된 추가 모델 RAMRUN-LIM은 가볍고 작은 하중을 고속 운송(400m/분)하고 처리 중인 카트 수를 줄이는 데 도움이 되었습니다.
-
사진 2: 램런(오버헤드형)
-
사진 3: Flexible Drive System (플로어형)
팔레트형 Flexible Drive System (FDS)
1988년에 Daifuku는 슬랫 컨베이어를 대체하기 위해 팔레트형 FDS를 개발했습니다(사진 3). FDS는 팔레트에 장착된 차체를 연속적으로 운반하는 우레탄 롤러 컨베이어입니다. 작업자는 조립 작업을 위해 팔레트 위에 올라갈 수 있으며, 기존 슬랫 컨베이어처럼 조립 라인을 따라 걸어갈 필요가 없습니다. FDS는 근로자의 멀미를 없애고 근로자 친화적인 환경 구축을 가능하게 하는 장점이 있습니다. 첫 번째 FDS는 1988년에 Kanto Auto Works Ltd.의 Fukaura 공장에 납품되었습니다.
비접촉 전원 공급 시스템 HID(고효율 유도 배전 기술)
1993년, Daifuku는 뉴질랜드 오클랜드 대학교와 공동으로 비접촉 전원 공급 시스템 HID를 개발했습니다. HID는 예를 들어 RAMRUN(사진 4)과 팔레트형 FDS에서 리프트 장치에 전력을 공급하는 데 사용됩니다. 이 비접촉 전원 공급 시스템은 안전하고 깨끗한 작업 환경 구현에 기여하고 유지 보수 비용을 획기적으로 줄이는 데 기여했습니다.
트롤리 라인과 컬렉터를 사용하는 기존의 접촉 전원 공급 기술은 컬렉터의 마모, 마모 파편 및 먼지, 라인 분리에 의해 발생하는 스파크 등의 단점이 있습니다. HID는 기존 트롤리 라인 대신 2개의 유도 케이블, 수집기 대신 픽업 코일 및 수전 장치로 구성됩니다(그림 2). 전원 공급 패널은 상용 전력을 비접촉 전원 공급에 적합한 주파수로 변환하여 유도 케이블에 공급합니다. 유도 케이블 주변에 자기장이 발생하여 움직이는 물체에 효율적으로 전력을 공급합니다.
HID는 Kanto Auto Works Ltd.의 이와테 공장에 납품된 RAMRUN에 처음 설치되었습니다. 그런 다음 General Motors Company에 유사한 운송 시스템을 제공했습니다. 이 제품은 전 세계적으로 주목을 받았으며 HID는 전 세계 많은 고객이 활용하고 있습니다. 현재 비접촉 전원 공급 시스템은 자동차 공장뿐만 아니라 청정 환경이 요구되는 반도체, 액정 공장의 자재 운반 장비에도 널리 사용되고 있다.
-
사진 4: RAMRUN HID(오버헤드형)
-
그림 2: HID 시스템 구성
새로운 Flexible Drive System (New FDS)
1999년 Daifuku는 팔레트 유형에서만 사용할 수 있었던 FDS의 기능을 개선하고 천장 및 바닥 유형을 추가했습니다(사진 5). New FDS라는 이름으로 라인업을 강화했습니다. New FDS의 장점 중 하나는 사용자가 마찰(그림 3), 체인 및 롤러 드라이브를 선택할 수 있다는 것입니다. 기존의 FDS에서는 구동 방식의 선택이 불가능했습니다. 예를 들어, 동일한 조립 라인에서 운송 작업을 위한 체인 드라이브와 마찰 드라이브를 구현하여 건조 작업을 위해 캐리어에서 캐리어로 차체를 이동할 필요를 제거할 수 있습니다. 또한 다음과 같은 장점이 있습니다.
- 이송 속도는 1~40m/분 범위에서 설정 가능(기본 사양)
- 캐리어는 간단하게 구성되며 자체 드라이브 소스가 없습니다. 그들은 쉽게 유지됩니다. 가성비도 높다
- 선로제어에 전선절약장치를 사용하여 공사기간 단축
- 마찰구동 우레탄 롤러의 필요한 부분만 작동합니다. 에너지 절약이 우수하고 소음도가 체인 컨베이어보다 10dB 이상 낮습니다.
FDS는 기존의 단일 운전 모드와 달리 최적의 운전 방법을 선택하고 조립 라인의 목적에 가장 적합한 운송 시스템을 구축할 수 있습니다. FDS는 주로 자동차 생산 라인에 적용됩니다.
-
사진 5: New FDS(Overhead Type)
-
그림 3: New FDS의 마찰 구동(바닥형)
결론
제2차 세계 대전 이후 일본 자동차 회사는 놀라울 정도로 빠른 성장과 확장을 이루었습니다. 1980년대 후반에는 연간 생산량이 1,100만 개에 달했습니다. 이후 자동차 제조사들은 무역마찰과 엔화 강세의 영향을 받아 자동차를 세계 각지에서 생산하는 등 해외 사업을 확대해 나가고 있다. 한편, 자동차 제조사의 운송 시스템 요구 사항은 대량 생산, 자동화 시스템, 다중 모델 혼합 생산, 리드 타임 단축, 생태 및 안전 강조 등의 요구 사항을 포함하여 빠르고 급격하게 변화하고 있습니다. Daifuku는 다양한 요구를 충족시키기 위해 자재 취급 장비를 개발했습니다.
최근 자동차 제조사들의 제품 다변화 경향이 강해지고 있다. 다중 모델 혼합 생산을 지원하는 조립 라인이 이제 가장 일반적입니다. 또한, 신차 모델의 개발 기간이 해마다 짧아짐에 따라 자재 취급 장비의 납기도 짧아져야 합니다. 이러한 수요를 충족하기 위해 Daifuku는 디지털 엔지니어링을 채택하고 전 세계 최적의 위치에서 생산을 구현함으로써 설계 및 생산의 효율성을 개선했습니다.
관련된 링크들
Automotive문의하기
제품문의는 Contact Us 페이지를 통해 연락주시기 바랍니다.
문의하기문의하기
제품문의는 Contact Us 페이지를 통해 연락주시기 바랍니다.
문의하기