Penyimpanan Otomatis & Sistem Pengambilan (AS/RS)
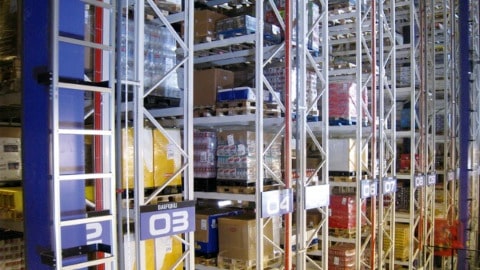
Unit Load AS/RS
Sistem gudang otomatis untuk palet, palet kotak mesh, palet kotak roll, dan muatan berat lainnya.
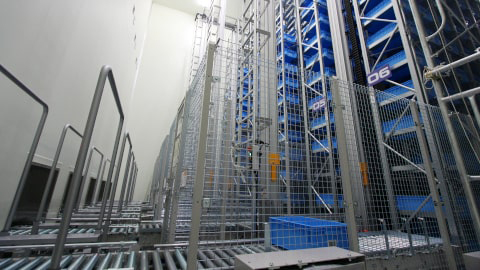
Mini Load AS/RS
Dilengkapi stacker crane yang dirancang untuk menyimpan dan mengambil tas jinjing, kotak, dan baki kecil secara efisien.
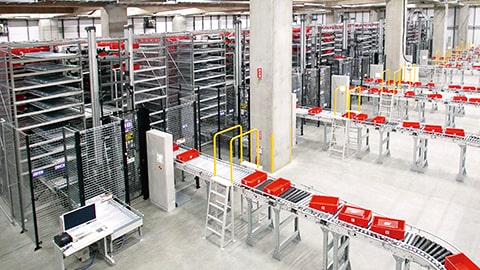
Shuttle Rack M
Mini Load AS/RS berbasis kendaraan yang unggul dalam pengurutan, penyortiran, dan penyimpanan tas, karton, baki, dan barang kecil lainnya secara efisien.
Teknologi dan Aplikasi AS/RS
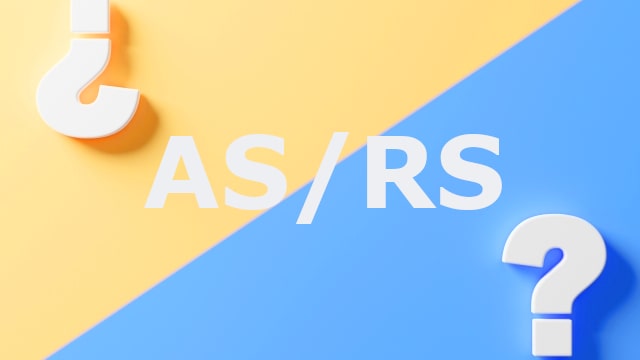
Aplikasi dan Manfaat AS/RS
Cari tahu apa itu AS/RS, aplikasi dan keserbagunaannya, serta pertimbangan utama untuk pemasangan.
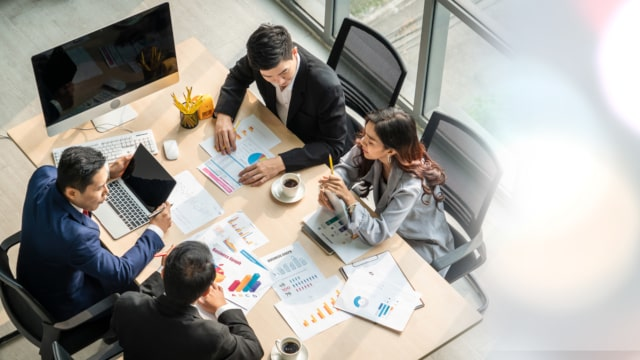
Pengalaman Solusi Total
Jelajahi bagaimana Daifuku mendukung Anda sepanjang perjalanan—mulai dari perencanaan awal hingga dukungan pasca-penjualan.
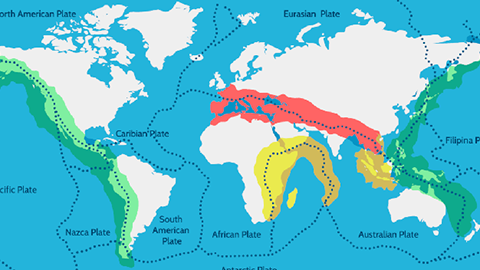
Penanggulangan Gempa AS/RS
Temukan serangkaian solusi yang dirancang untuk memitigasi risiko perpindahan beban di AS/RS selama gempa bumi.
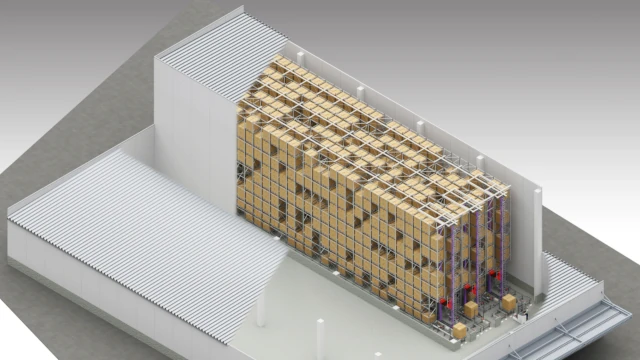
Sistem Model
Dapatkan inspirasi untuk perencanaan Anda dengan menjelajahi sistem model Unit Load AS/RS kami yang telah teruji.
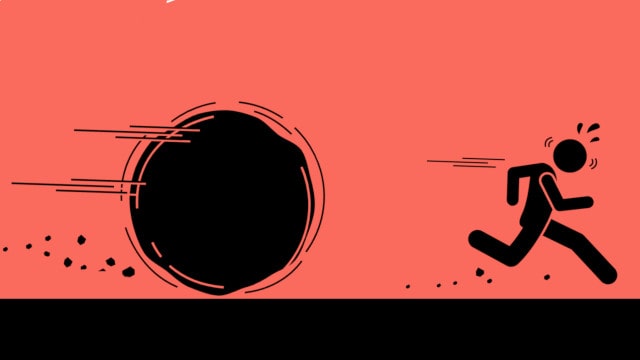
Penanganan Material Gulungan
Solusi efisien untuk menangani muatan berbentuk bulat—jelajahi alternatif untuk gulungan Anda.
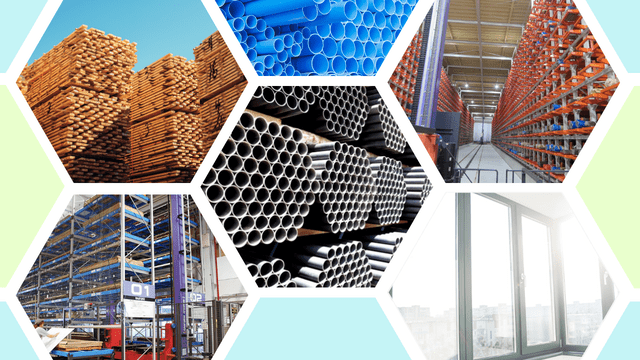
Penanganan Beban Panjang
Jelajahi solusi penyimpanan optimal yang dirancang untuk muatan jangka panjang.
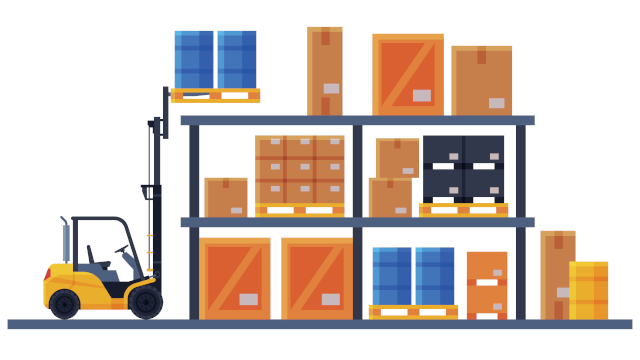
Pengisian Otomatis
Mengisi kembali stok secara efisien untuk mengambil jendela menggunakan derek penumpuk.
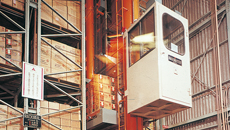
Sejarah Gudang Otomatis di Daifuku
Temukan bagaimana Daifuku memelopori pasar otomatisasi gudang dengan AS/RS sejak tahun 1966.
Solusi oleh Industri
Hubungi kami
Untuk pertanyaan produk, silakan menghubungi kami melalui halaman Hubungi Kami.
Hubungi kamiHubungi kami
Untuk pertanyaan produk, silakan menghubungi kami melalui halaman Hubungi Kami.
Hubungi kami