เทคโนโลยีที่จำเป็นสำหรับ Daifuku สำหรับโครงสร้างพื้นฐานทางสังคม ที่ปรับปรุงความน่าเชื่อถือและประสิทธิผลด้วยระบบสายการผลิตเซมิคอนดักเตอร์ของ Daifuku
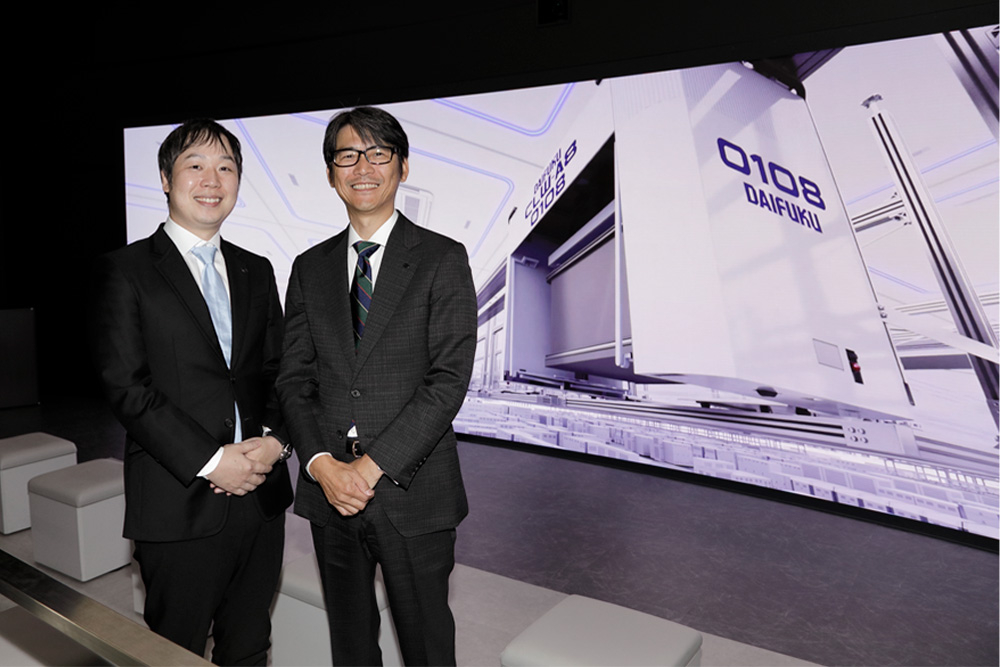
เมื่อพูดถึงการผลิตเซมิคอนดักเตอร์ ระบบการขนส่งและการจัดเก็บที่เชื่อถือได้สูงซึ่งสามารถทำงานได้ตลอด 24 ชั่วโมง 365 วันต่อปีถือเป็นสิ่งสำคัญ เราได้พูดคุยกับตัวแทนฝ่ายวิศวกรรมและการออกแบบจากแผนกคลีนรูมของ Daifuku เกี่ยวกับระบบสายการผลิตเซมิคอนดักเตอร์ของ Daifuku เช่น Cleanway ซึ่งเป็นระบบขนส่งห้องคลีนรูมเพื่อเพิ่มเวลาทำงานของอุปกรณ์ให้สูงสุด และระบบจัดเก็บไนโตรเจนแบบกำจัดที่มีส่วนทำให้เซมิคอนดักเตอร์มีขนาดเล็กลง
แนวโน้มโรงงานผลิตเซมิคอนดักเตอร์: การรวมตัวและขนาดที่เพิ่มขึ้น
เซมิคอนดักเตอร์เป็นส่วนประกอบสำคัญที่ใช้ในอุปกรณ์อิเล็กทรอนิกส์ในชีวิตประจำวันหลายอย่าง เช่น คอมพิวเตอร์และสมาร์ทโฟน นอกจากนี้ยังเป็นส่วนสำคัญของสาขาที่กำลังเติบโต เช่น เทคโนโลยีการขับขี่อัตโนมัติ ยานพาหนะไฟฟ้า (EV) และปัญญาประดิษฐ์ (AI) ผู้ผลิตเซมิคอนดักเตอร์ทั่วโลกจำเป็นต้องเพิ่มกำลังการผลิตเพื่อให้ทันกับความต้องการที่เพิ่มขึ้น รัฐบาลทั่วโลกได้ประกาศนโยบายในการอุดหนุนการลงทุนภายในภูมิภาค ซึ่งปูทางสำหรับการลงทุนที่แข็งแกร่งอย่างต่อเนื่องโดยผู้ผลิต
เพื่อตอบสนองความต้องการที่เพิ่มขึ้น ผู้เล่นหลักหลายรายในอุตสาหกรรมจึงรวบรวมและเพิ่มขนาดของโรงงานผลิตของตน การมีโรงงานผลิตเซมิคอนดักเตอร์ (fabs) ตั้งอยู่ใกล้กันแทนที่จะกระจายไปตามสถานที่ต่างๆ หลายแห่ง ช่วยลดต้นทุนการก่อสร้างและประหยัดทรัพยากรในระหว่างการผลิต การรวมเข้าด้วยกันยังดีสำหรับการใช้งานอุปกรณ์ล้ำสมัยที่มีราคาแพง โดยทำให้โรงงานต่างๆ ใช้อุปกรณ์ดังกล่าวร่วมกันได้ง่ายขึ้น
เมื่อคำนึงถึงแนวโน้มของอุตสาหกรรมเหล่านี้ Daifuku Group จึงนำเสนอโซลูชั่นที่หลากหลายเพื่อให้มั่นใจว่าไม่เพียงแต่การขนส่งภายในโรงงานจะราบรื่นเท่านั้น แต่ยังรวมถึงการขนส่งแผ่นเวเฟอร์เซมิคอนดักเตอร์ที่มีประสิทธิภาพระหว่างโรงงานที่เชื่อมต่อกันอีกด้วย
ตัวอย่างโซลูชันสำหรับขนาดที่เพิ่มขึ้นของโรงงานเซมิคอนดักเตอร์แบบรวม
ระบบ Daifuku สำหรับกระบวนการส่วนหน้าและส่วนหลัง
เซมิคอนดักเตอร์ผลิตขึ้นในสภาพแวดล้อมห้องสะอาดซึ่งมีการควบคุมฝุ่นและอนุภาคในอากาศอื่นๆ อย่างเข้มงวด ขั้นแรกวัสดุซิลิกอนดิบจะถูกหลอมจนกลายเป็นแท่งโลหะ ลิ่มนี้หั่นบาง ๆ ให้เป็นแผ่นเวเฟอร์ที่สม่ำเสมอ เวเฟอร์กระแสหลักในปัจจุบันถูกตัดเป็นรูปทรงดิสก์ที่มีเส้นผ่านศูนย์กลาง 300 มม. จากนั้นแผ่นเวเฟอร์จะผ่านกระบวนการพิมพ์หินด้วยแสงและแกะสลักหลายสิบครั้งเพื่อพิมพ์วงจรรวมลงบนพื้นผิว สิ่งนี้เรียกว่าการประมวลผลส่วนหน้า กระบวนการตัดชิปจากเวเฟอร์และแปลงเป็น CPU และผลิตภัณฑ์อื่นๆ ต่อไปนี้เรียกว่าการประมวลผลส่วนหลัง
Daifuku นำเสนอการขนส่งการผลิตเซมิคอนดักเตอร์สำหรับการประมวลผลทั้งส่วนหน้าและส่วนหลังผ่าน Cleanway ซึ่งเป็นระบบลำเลียงในห้องปลอดเชื้อที่ใช้ยานพาหนะที่ขับเคลื่อนด้วยไฟฟ้า ในการประมวลผลส่วนหน้า เวเฟอร์จะถูกจัดเก็บไว้ในภาชนะปิดผนึกที่เรียกว่า FOUP เพื่อรักษาความสะอาดในขณะที่ถูกเคลื่อนย้ายระหว่างอุปกรณ์การประมวลผลต่างๆ ระบบ Cleanway ของ Daifuku จะถ่ายโอน FOUP ทั้งหมดระหว่างอุปกรณ์โดยอัตโนมัติ เนื่องจากรางขนส่งของระบบ Cleanway ถูกยืดข้ามเพดานแทนที่จะวางบนพื้น จึงมีพื้นที่สำหรับติดตั้งอุปกรณ์อื่นๆ มากมายในห้องปลอดเชื้อ ทำให้เป็นตัวเลือกยอดนิยมในโรงงานเซมิคอนดักเตอร์จำนวนมาก วัสดุที่ใช้ในล้อรถได้รับการออกแบบอย่างพิถีพิถันเพื่อลดการเกิดฝุ่น
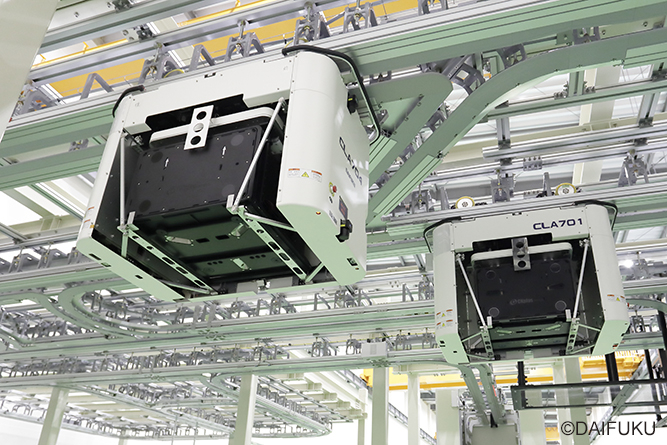
Clean Stocker เป็นอุปกรณ์จัดเก็บชั่วคราวที่ใช้ร่วมกับระบบ Cleanway แม้ว่างานการประมวลผลส่วนหน้าจะดำเนินการซ้ำๆ กัน แต่เวลาที่ต้องใช้สำหรับการดำเนินการแต่ละครั้งจะแตกต่างกันไป FOUP ที่มีเวเฟอร์ที่รอส่งไปยังกระบวนการถัดไปจะถูกจัดเก็บไว้ในอุปกรณ์จัดเก็บข้อมูลชั่วคราวที่มีความเสถียรที่เรียกว่าสต็อกเกอร์ เมื่อระยะเวลาการผลิตนานขึ้นและเซมิคอนดักเตอร์มีขนาดเล็กลง การเติม FOUP ด้วยก๊าซไนโตรเจนเพื่อป้องกันการเกิดออกซิเดชันจึงกลายเป็นเรื่องปกติมากขึ้น Daifuku จัดหาระบบที่มีความสามารถในการกำจัดไนโตรเจนเพื่อตอบสนองความต้องการที่เพิ่มขึ้นนี้
ระบบสายการผลิตเซมิคอนดักเตอร์พร้อมสต็อกเกอร์กำจัดไนโตรเจน
แม้ว่าพื้นที่จัดเก็บ FOUP จำนวนมากที่ผู้จัดเก็บจัดเตรียมไว้จะเป็นประโยชน์ แต่มักจะอยู่ห่างจากเส้นทางการขนย้าย และในเค้าโครงที่ยอดเยี่ยมบางรูปแบบ การเดินทางไปและกลับจากผู้จัดเก็บอาจต้องใช้เวลาระยะหนึ่ง บัฟเฟอร์รางด้านข้าง (STB) ซึ่งเป็นแท่นรับที่ติดตั้งในพื้นที่เปิดโล่งระหว่างรางขนส่ง กำลังกลายเป็นวิธีแก้ปัญหายอดนิยมสำหรับปัญหานี้ ในบางกรณี การใช้ STB สามารถลดระยะเวลาการผลิต 180 วันของ CPU รุ่นล่าสุดได้ประมาณ 5 วัน แม้ว่าการลดกำหนดการผลิต 180 วันลง 5 วันอาจดูไม่มากนักเมื่อมองแวบแรก แต่การลดเวลาการส่งมอบลงอย่างต่อเนื่อง 3% ถือเป็นความสำเร็จที่สำคัญสำหรับโรงงานเซมิคอนดักเตอร์ที่ต้องการเพิ่มประสิทธิภาพและความสามารถในการผลิต
การใช้ STB ยังช่วยสนับสนุนความยั่งยืนอีกด้วย ในขณะที่การติดตั้งสต็อกเกอร์ต้องใช้พื้นที่จำนวนหนึ่ง STB จะใช้แพลตฟอร์มที่แขวนจากเพดาน ซึ่งช่วยประหยัดพื้นที่คลีนรูมสำหรับอุปกรณ์อื่นๆ และลดพื้นที่โดยรวมของโรงงาน ด้วยเหตุผลเหล่านี้ STB จึงกลายเป็นวิธีการยอดนิยมในการประหยัดพลังงานและปรับปรุงประสิทธิภาพ
กำหนดทิศทางการรับส่งข้อมูลด้วย AI
เนื่องจากโรงงานเซมิคอนดักเตอร์ยังคงขยายขนาดให้ใหญ่ขึ้น ความยาวรวมของราง Cleanway จึงสามารถมีความยาวรวมกันได้มากกว่า 200 กม. โดยมียานพาหนะมากกว่า 10,000 คันวิ่งอยู่บนนั้น แม้ว่าขั้นตอนการประมวลผลแผ่นเวเฟอร์จะมีลำดับตายตัว แต่เวลาที่ใช้ในการดำเนินการแต่ละขั้นตอนให้เสร็จสิ้นอาจแตกต่างกันอย่างมาก และอาจนำไปสู่ปัญหาการจราจรติดขัดได้เนื่องจากยานพาหนะเพ่งความสนใจไปที่อุปกรณ์บางอย่างในช่วงเวลาหนึ่ง รถติดเหล่านี้จำกัดประสิทธิภาพการทำงาน และ Daifuku ได้เริ่มใช้ AI ในซอฟต์แวร์ควบคุมระบบ Cleanway เพื่อป้องกันไม่ให้เกิดปัญหารถติดดังกล่าว เช่นเดียวกับระบบนำทางในรถยนต์ AI ถูกใช้เพื่อกำหนดเส้นทางที่หลีกเลี่ยงการจราจรติดขัด โดยรถแต่ละคันจะถูกนำทางไปยังเส้นทางที่เหมาะสมที่สุด ในขณะที่ระบบทั่วไปเลือกเส้นทางตามระยะทางที่สั้นที่สุด การนำ AI มาใช้ทำให้สามารถกำหนดและเลือกเส้นทางที่เร็วที่สุดแบบไดนามิกได้ แม้ว่าเส้นทางนั้นจะเป็นระยะทางที่ยาวกว่าก็ตาม ความก้าวหน้าที่คาดหวังในเทคโนโลยี AI หมายความว่ามีศักยภาพที่ดีในการปรับปรุงระบบเพิ่มเติม และ Daifuku จะยังคงสำรวจการใช้งานต่อไป
การปรับปรุงการผลิตเซมิคอนดักเตอร์ผ่านเทคโนโลยีการควบคุมขั้นสูง
การดำเนินงานโรงงานขนาดใหญ่ตลอด 24 ชั่วโมง 365 วันต่อปีไม่ใช่เรื่องง่าย ดังนั้น Daifuku จึงทุ่มเทไม่เพียงแต่ในการนำเสนอฮาร์ดแวร์ที่ทนทานซึ่งทนทานต่อการใช้งานในระยะยาวเท่านั้น แต่ยังรวมไปถึงการพัฒนาระบบเสริมและการจัดเตรียมระบบสำรองเพื่อรองรับ การดำเนินงาน fab ที่มั่นคงและราบรื่น
ตัวอย่างเช่น ระบบ Cleanway ใช้ระบบจ่ายไฟแบบไม่สัมผัส HID เพื่อลดการเกิดฝุ่นที่อาจเกิดจากการเสียดสีของแหล่งจ่ายไฟแบบสัมผัส ระบบ HID ยังรวมเอามาตรการสำรองเพื่อให้แน่ใจว่ามีการจ่ายพลังงานให้กับยานพาหนะอย่างต่อเนื่อง ส่วนประกอบการทำงานของระบบที่จำเป็น เช่น ตัวควบคุมและเซิร์ฟเวอร์ก็ถูกจัดเตรียมไว้เหมือนกัน เพื่อให้มั่นใจว่าการทำงานจะต่อเนื่องแม้ว่าอุปกรณ์จะทำงานผิดปกติก็ตาม
นอกจากนี้ แม้ว่าก่อนหน้านี้จะมีการติดตั้งตัวควบคุมที่ทางแยกรางเพื่อป้องกันการชนกันของยานพาหนะ แต่ระบบปัจจุบันใช้การควบคุมแบบไร้สาย ทำให้ไม่จำเป็นต้องวางอุปกรณ์ควบคุม ข้อมูลจะถูกแบ่งปันแบบไร้สายระหว่างยานพาหนะที่เข้าใกล้ทางแยก และหลังจากพิจารณาแล้วว่ายานพาหนะจะไม่ชนกันเท่านั้นจึงจะได้รับอนุญาตให้ดำเนินการต่อได้ ด้วยการลดจำนวนอุปกรณ์ที่ติดตั้งบนราง ทำให้ระบบมีต้นทุนน้อยลง ติดตั้งเร็วขึ้น และใช้วัสดุและพลังงานน้อยลง ทำให้เป็นมิตรต่อสิ่งแวดล้อมมากขึ้น
ตอบสนองความต้องการระบบอัตโนมัติในกระบวนการแบ็คเอนด์
ในช่วงไม่กี่ปีที่ผ่านมา มีความต้องการระบบอัตโนมัติในกระบวนการแบ็คเอนด์ของการผลิตเซมิคอนดักเตอร์เพิ่มมากขึ้น แม้ว่าก่อนหน้านี้การปรับปรุงประสิทธิภาพการผลิตผ่านความก้าวหน้าในกระบวนการส่วนหน้าเป็นเรื่องปกติ แต่ความก้าวหน้าในกระบวนการแบ็คเอนด์ เช่น การตัดแผ่นเวเฟอร์และการบรรจุชิป ก็มีความสำคัญต่อการปรับปรุงประสิทธิภาพในโรงงานผลิตเช่นกัน เมื่อเปรียบเทียบกับกระบวนการส่วนหน้า กระบวนการแบ็คเอนด์จะต้องอาศัยแรงงานคนมากขึ้น รวมถึงการขนส่งชิป และมักเกิดขึ้นนอกห้องปลอดเชื้อ ดังนั้นโดยการย้ายไปยังสภาพแวดล้อมที่สะอาดที่มีการควบคุมและการถ่ายโอนระหว่างกระบวนการโดยอัตโนมัติ fabs สามารถผลิตสินค้าคุณภาพสูงและมีประสิทธิภาพเพิ่มขึ้น
การรองรับเวเฟอร์รูปสี่เหลี่ยมผืนผ้าก็มีความต้องการเพิ่มขึ้นเช่นกัน ในกระบวนการส่วนหน้าปัจจุบัน วงจรมักจะถูกอบให้เป็นเวเฟอร์ซิลิคอนทรงกลม แต่เนื่องจากเวเฟอร์ถูกตัดเป็นชิปสี่เหลี่ยมในการประมวลผลแบ็คเอนด์ เวเฟอร์จึงไม่จำเป็นต้องเป็นแบบวงกลม ด้วยเหตุนี้ การใช้บรรจุภัณฑ์ทรงสี่เหลี่ยมที่คล้ายคลึงกับผลิตภัณฑ์ขั้นสุดท้ายจึงกลายเป็นวิธียอดนิยมในการป้องกันของเสียในกระบวนการแบ็คเอนด์
ด้วยการใช้เทคโนโลยีที่ปลูกฝังในการขนส่งแผง OLED Daifuku ได้พัฒนาระบบการขนส่ง FOUP สำหรับบรรจุภัณฑ์ระดับแผง (PLP) ที่สามารถจัดการพื้นผิวสี่เหลี่ยมจัตุรัสขนาด 600 มม. ด้วยการปรับให้เข้ากับพื้นผิวสี่เหลี่ยมจัตุรัสและการปรับปรุงระบบอื่นๆ โซลูชันของ Daifuku มอบคุณประโยชน์เพิ่มเติมให้กับประสิทธิภาพของโรงงานเซมิคอนดักเตอร์
โซลูชันการประมวลผลส่วนหลังสำหรับการผลิตเซมิคอนดักเตอร์
ใช้สำนักงานทั่วโลกเพื่อการตอบสนองในระดับท้องถิ่น
นอกจาก Shiga Works ซึ่งเป็นโรงงานผลิตหลักของ Daifuku แล้ว Cleanroom Global Business ยังมีโรงงานผลิตในจีน ไต้หวัน และเกาหลีใต้ รวมถึงบริษัทในเครือในสหรัฐอเมริกาและสิงคโปร์ แม้ว่าส่วนประกอบหลักของอุปกรณ์จะถูกส่งจากญี่ปุ่น แต่รางขนส่งและส่วนประกอบอื่นๆ ได้รับการออกแบบและประกอบในโรงงานท้องถิ่น ซึ่งโดยทั่วไปเรียกว่า “การผลิตในท้องถิ่นเพื่อการบริโภคในท้องถิ่น” บริษัทสาขาในพื้นที่ไม่เพียงจ้างตัวแทนฝ่ายขายเท่านั้น แต่ยังจ้างวิศวกรด้วย ซึ่งช่วยให้สามารถสื่อสารกับลูกค้าในรายละเอียดได้มากขึ้น ทำให้วิศวกรสามารถทำงานร่วมกับลูกค้าได้โดยตรง รวมถึงการตอบสนองต่อคำขอและข้อเสนอแนะ โดยที่พนักงานจากประเทศญี่ปุ่นไม่ต้องเข้าเยี่ยมชมสถานที่ ความสามารถพิเศษในการตอบสนองต่อลูกค้าทันทีถือเป็นจุดแข็งที่ยิ่งใหญ่ที่สุดของ Daifuku Group และทำให้สามารถรวมผลตอบรับจากผู้ใช้ทั่วโลกในการออกแบบและพัฒนาผลิตภัณฑ์ได้
แหล่งผลิตในจีน (ซ้าย) และเกาหลีใต้ (ขวา)
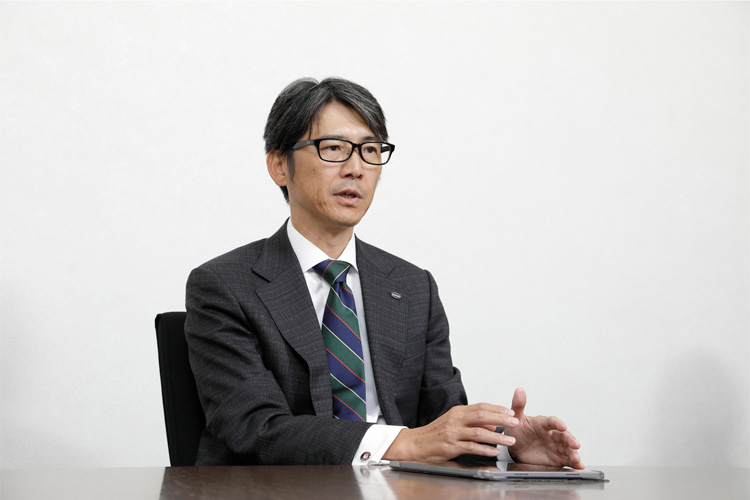
ชินิจิ นากาชิมะ
ผู้จัดการฝ่ายวิศวกรรม ฝ่ายปฏิบัติการขาย แผนกคลีนรูม
Daifuku Co., Ltd.
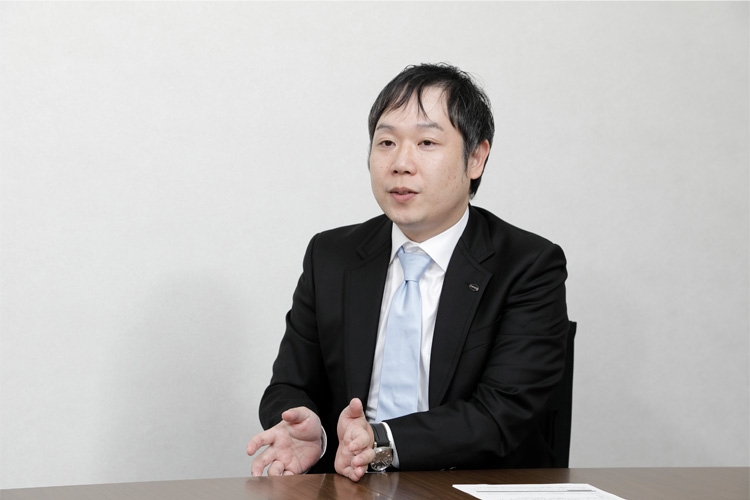
ทัตสึกิ II
ผู้ช่วยผู้จัดการฝ่ายออกแบบ VHL ส่วนที่ 2
กลุ่มออกแบบขนส่ง ฝ่ายออกแบบ ฝ่ายปฏิบัติการการผลิต ฝ่ายห้องคลีนรูม
Daifuku Co., Ltd.