Wesentliche Daifuku-Technologien für die soziale Infrastruktur zur Verbesserung der Zuverlässigkeit und Produktivität mit Daifukus Halbleiter-Produktionsliniensystemen
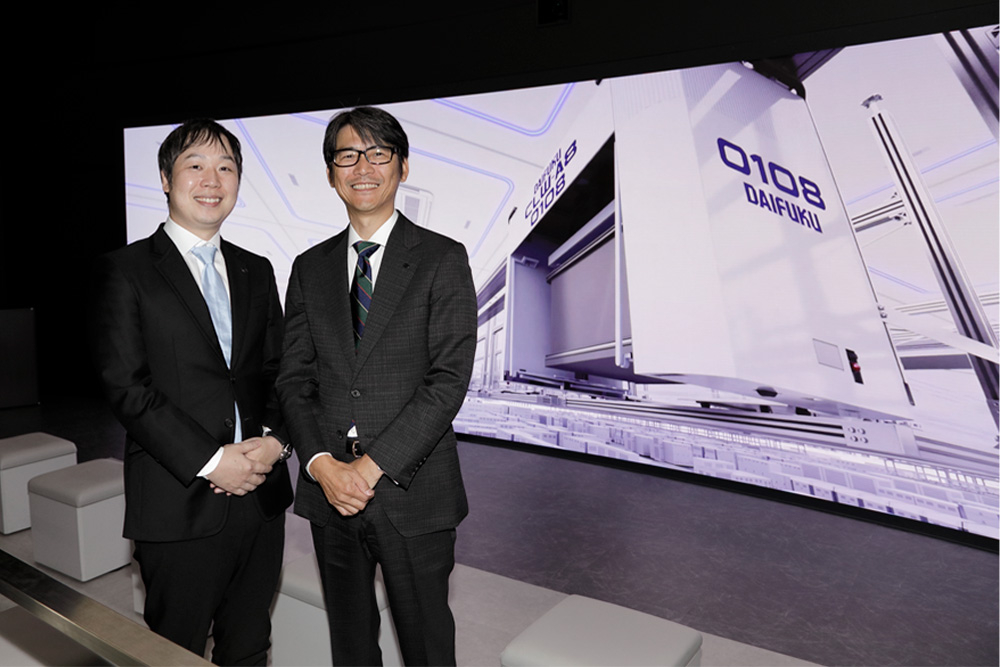
Wenn es um die Halbleiterfertigung geht, sind äußerst zuverlässige Transport- und Lagersysteme, die 24 Stunden am Tag und 365 Tage im Jahr funktionieren, unerlässlich. Wir sprachen mit Vertretern des Ingenieur- und Designpersonals der Reinraumabteilung von Daifuku über Daifukus Halbleiter-Produktionsliniensysteme wie den Cleanway, ein Reinraum-Transportsystem zur Maximierung der Anlagenverfügbarkeit und ein Stickstoffspül-Lagersystem, das zur Miniaturisierung von Halbleitern beiträgt.
Trends bei Halbleiterfabriken: Konsolidierung und Vergrößerung
Halbleiter sind ein wesentlicher Bestandteil vieler alltäglicher elektronischer Geräte wie Computer und Smartphones. Sie sind auch ein wichtiger Teil wachsender Bereiche wie automatisierte Fahrtechnologie, Elektrofahrzeuge (EVs) und künstliche Intelligenz (KI). Halbleiterhersteller auf der ganzen Welt müssen ihre Produktionskapazitäten erhöhen, um mit der wachsenden Nachfrage Schritt zu halten. Regierungen auf der ganzen Welt haben Maßnahmen zur Subventionierung intraregionaler Investitionen angekündigt und damit den Weg für anhaltend starke Kapitalinvestitionen der Hersteller geebnet.
Um der gestiegenen Nachfrage besser gerecht zu werden, konsolidieren und vergrößern viele große Akteure der Branche ihre Produktionsanlagen. Wenn Halbleiterfabriken (Fabs) nahe beieinander liegen und nicht über mehrere verschiedene Standorte verteilt sind, können die Baukosten gesenkt und Ressourcen bei der Herstellung geschont werden. Die Konsolidierung ist auch für den Betrieb teurer, hochmoderner Geräte von Vorteil, da sie die gemeinsame Nutzung dieser Geräte durch verschiedene Werke erleichtert.
Unter Berücksichtigung dieser Branchentrends bietet die Daifuku-Gruppe verschiedene Lösungen an, um nicht nur einen reibungslosen Transport innerhalb einer Fabrik, sondern auch einen effizienten Transport von Halbleiterwafern zwischen verbundenen Fabriken zu gewährleisten.
Beispiellösungen für den zunehmenden Umfang konsolidierter Halbleiterfabriken
Daifuku-Systeme für Front-End- und Back-End-Prozesse
Halbleiter werden in einer Reinraumumgebung hergestellt, in der Staub und andere in der Luft befindliche Partikel streng kontrolliert werden. Rohes Siliziummaterial wird zunächst eingeschmolzen, um einen Barren herzustellen. Dieser Barren wird in dünne, gleichmäßige Scheiben geschnitten. Aktuelle gängige Wafer werden in Scheibenform mit einem Durchmesser von 300 mm geschnitten. Anschließend durchläuft der Wafer Dutzende Male Fotolithographie- und Ätzprozesse, um integrierte Schaltkreise auf die Oberfläche zu prägen. Dies wird als Front-End-Verarbeitung bezeichnet. Die folgenden Prozesse, bei denen die Chips aus dem Wafer geschnitten und in CPUs und andere Produkte umgewandelt werden, werden als Back-End-Verarbeitung bezeichnet.
Daifuku bietet über Cleanway, ein Reinraum-Fördersystem, das elektrisch angetriebene Fahrzeuge verwendet, Transportmittel für die Halbleiterfertigung sowohl für die Front-End- als auch für die Back-End-Verarbeitung an. Bei der Front-End-Verarbeitung werden Wafer in einem versiegelten Behälter namens FOUP gelagert, um sie sauber zu halten, während sie zwischen verschiedenen Verarbeitungsgeräten bewegt werden. Das Cleanway System von Daifuku überträgt alle FOUPs automatisch zwischen den Geräten. Da die Transportschienen des Cleanway Systems über die Decke gespannt und nicht auf dem Boden ausgelegt sind, gibt es im Reinraum Platz für die Installation zahlreicher anderer Geräte, was es zu einer beliebten Wahl in vielen Halbleiterfabriken macht. Auch die für die Räder des Fahrzeugs verwendeten Materialien wurden sorgfältig entwickelt, um die Staubentwicklung zu minimieren.
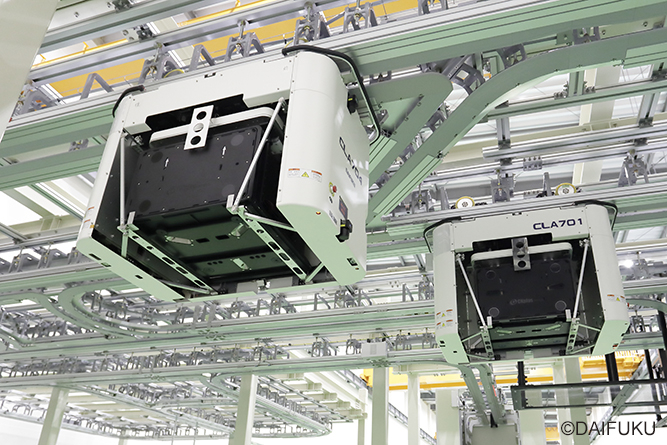
Der Reinraum Stocker ist ein temporäres Speichergerät, das zusammen mit dem Cleanway System verwendet wird. Obwohl Front-End-Verarbeitungsaufgaben wiederholt ausgeführt werden, variiert die für jeden Vorgang erforderliche Zeit. FOUPs, die Wafer enthalten, die darauf warten, zum nächsten Prozess geschickt zu werden, werden in einem stabilen temporären Speichergerät namens Stocker gelagert. Da die Herstellungszeiten immer länger und die Halbleiter immer kleiner werden, wird es immer häufiger, das FOUP mit Stickstoffgas zu füllen, um Oxidation zu verhindern. Um diesem wachsenden Bedarf gerecht zu werden, bietet Daifuku Systeme mit Stickstoffspülfunktionen an.
Halbleiter-Produktionsliniensystem mit Stickstoffspüllager
Obwohl die von Lagerhaltern bereitgestellten FOUP-Massenlager hilfreich sind, befinden sie sich häufig abseits der Transferroute, und in einigen Fabriklayouts kann der Weg zum und vom Lagerhalter einige Zeit dauern. Side Track Buffer (STBs) – Empfangsplattformen, die im offenen Raum zwischen den Transportschienen installiert werden – werden zu einer beliebten Lösung für dieses Problem. In einigen Fällen kann die Verwendung von STBs die 180-tägige Herstellungszeit der neuesten CPUs um etwa 5 Tage verkürzen. Während eine Verkürzung um 5 Tage gegenüber einem 180-Tage-Produktionsplan auf den ersten Blick nicht viel erscheint, ist eine konstante Verkürzung der Lieferzeit um 3 % eine bedeutende Errungenschaft für jede Halbleiterfabrik, die ihre Effizienz und Produktivität steigern möchte.
Der Einsatz von STBs trägt auch zur Nachhaltigkeit bei. Während für die Installation von Lagern eine gewisse Stellfläche erforderlich ist, verwenden STBs an der Decke hängende Plattformen, die dazu beitragen, Platz im Reinraum für andere Geräte zu sparen und so die Gesamtfläche der Anlage zu reduzieren. Aus diesen Gründen werden STBs zu einer beliebten Methode zur Energieeinsparung und Verbesserung der Effizienz.
Den Verkehr mit KI lenken
Da Halbleiterfabriken immer größer werden, kann die Gesamtlänge der Cleanway Schienen eine Gesamtlänge von über 200 km erreichen, auf denen mehr als 10.000 Fahrzeuge fahren. Obwohl die Wafer-Bearbeitungsvorgänge einer festen Reihenfolge unterliegen, kann die Zeit, die für die einzelnen Schritte benötigt wird, stark variieren. Dies kann zu Staus führen, da sich die Fahrzeuge zu bestimmten Zeiten um bestimmte Geräte konzentrieren. Diese Staus schränken die Produktivität ein, und Daifuku hat damit begonnen, KI in der Cleanway Systemsteuerungssoftware einzusetzen, um das Auftreten solcher Staus zu verhindern. Genau wie bei Navigationssystemen im Auto wird mithilfe von KI eine Route ermittelt, die Staus vermeidet und jedes Fahrzeug auf seine optimale Route leitet. Während herkömmliche Systeme die Route nach der kürzesten Entfernung auswählen, ermöglicht der Einsatz von KI die dynamische Bestimmung und Auswahl der schnellstmöglichen Route, auch wenn es sich bei dieser Route tatsächlich um eine längere Entfernung handelt. Aufgrund der erwarteten Fortschritte in der KI-Technologie besteht ein großes Potenzial für die weitere Verbesserung von Systemen, und Daifuku wird ihren Einsatz weiterhin erforschen.
Verbesserung der Halbleiterfertigung durch fortschrittliche Steuerungstechnologie
Der Betrieb einer Großanlage 24 Stunden am Tag, 365 Tage im Jahr ist keine leichte Aufgabe. Deshalb legt Daifuku nicht nur Wert darauf, langlebige Hardware anzubieten, die einer Langzeitnutzung standhält, sondern auch Hilfssysteme zu entwickeln und Redundanz für den Support bereitzustellen Stabiler und reibungsloser Fab-Betrieb.
Das Cleanway System verwendet beispielsweise das berührungslose HID-Stromversorgungssystem, um die Staubentwicklung zu minimieren, die durch den Abrieb einer Kontaktstromversorgung entstehen würde. Das HID-System umfasst außerdem Redundanzmaßnahmen, um eine kontinuierliche Stromversorgung der Fahrzeuge sicherzustellen. Wesentliche Systembetriebskomponenten wie Controller und Server sind ebenfalls doppelt vorbereitet, so dass auch bei Geräteausfällen ein Weiterbetrieb gewährleistet ist.
Während früher an Bahnknotenpunkten Steuerungen installiert wurden, um Fahrzeugkollisionen zu verhindern, nutzt das aktuelle System außerdem eine drahtlose Steuerung, sodass keine Steuerungsausrüstung angebracht werden muss. Informationen werden drahtlos zwischen Fahrzeugen ausgetauscht, die sich einer Kreuzung nähern, und erst wenn festgestellt wird, dass die Fahrzeuge nicht miteinander kollidieren, dürfen sie weiterfahren. Durch die Reduzierung der auf den Schienen installierten Ausrüstung kostet das System weniger, lässt sich schneller installieren und verbraucht weniger Material und Energie, was es umweltfreundlicher macht.
Erfüllung der Automatisierungsanforderungen in Back-End-Prozessen
In den letzten Jahren besteht ein wachsender Bedarf an Automatisierung in den Back-End-Prozessen der Halbleiterfertigung. Während es früher üblich war, Produktivitätssteigerungen durch Fortschritte bei Front-End-Prozessen zu erzielen, sind Fortschritte bei Back-End-Prozessen wie Wafer-Schneiden und Chip-Verpackung auch für die Effizienzsteigerung in Fabriken von entscheidender Bedeutung. Im Vergleich zu Front-End-Prozessen sind Back-End-Prozesse stärker auf manuelle Arbeit angewiesen, einschließlich des Transports der Chips, und finden häufig außerhalb eines Reinraums statt. Durch den Umzug in eine kontrollierte, saubere Umgebung und die Automatisierung von Transfers zwischen Prozessen sind Fabs dies in der Lage, qualitativ hochwertigere Produkte mit erhöhter Effizienz herzustellen.
Auch die Unterstützung rechteckiger Wafer besteht zunehmend im Bedarfsfall. In aktuellen Front-End-Prozessen werden Schaltkreise üblicherweise in kreisförmige Siliziumwafer eingebrannt, aber da die Wafer bei der Back-End-Verarbeitung in quadratische Chips geschnitten werden, müssen die Wafer nicht unbedingt kreisförmig sein. Daher wird die Verwendung quadratischer Verpackungen, die dem Endprodukt ähnlicher sind, zu einer beliebten Methode, um Verschwendung in Back-End-Prozessen zu vermeiden.
Daifuku nutzt die für den Transport von OLED-Panels entwickelte Technologie und hat FOUP-Transportsysteme für Panel-Level-Packages (PLPs) entwickelt, die 600-mm-Quadratsubstrate transportieren können. Durch die Anpassung an quadratische Substrate und andere Systemverbesserungen bieten Daifuku-Lösungen noch weitere Vorteile für die Effizienz von Halbleiterfabriken.
Back-End-Verarbeitungslösungen für die Halbleiterfertigung
Nutzung von Niederlassungen auf der ganzen Welt für örtliche Antworten
Neben Shiga Works, dem Flaggschiff-Produktionswerk von Daifuku, verfügt das Cleanroom Global Business auch über Produktionsstätten in China, Taiwan und Südkorea sowie Tochtergesellschaften in den USA und Singapur. Obwohl die Kernkomponenten der Ausrüstung aus Japan verschickt werden, werden die Transportschienen und andere Komponenten in lokalen Fabriken entworfen und montiert. Dies wird allgemein als „lokale Produktion für den lokalen Verbrauch“ bezeichnet. Lokale Niederlassungen beschäftigen nicht nur Vertriebsmitarbeiter, sondern auch Ingenieure, was eine detailliertere Kommunikation mit den Kunden ermöglicht. Dies ermöglicht es Ingenieuren, direkt mit Kunden zusammenzuarbeiten und auf Anfragen und Feedback zu reagieren, ohne dass Mitarbeiter aus Japan vor Ort sein müssen. Diese einzigartige Fähigkeit, unmittelbar auf Kundenwünsche zu reagieren, ist eine der größten Stärken der Daifuku-Gruppe und ermöglicht es, Feedback von Anwendern auf der ganzen Welt in die Gestaltung und Entwicklung von Produkten einzubeziehen.
Produktionsstandorte in China (links) und Südkorea (rechts)
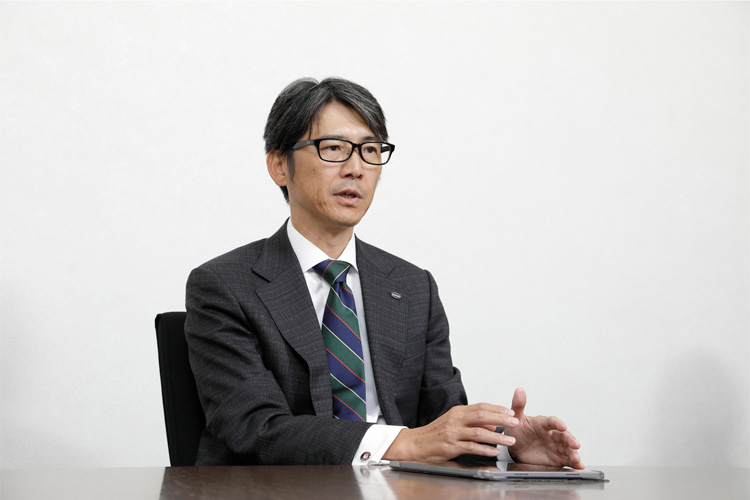
Shinichi Nakashima
Manager, technische Abteilung, Vertriebsbetrieb, Reinraumabteilung
Daifuku Co., Ltd.
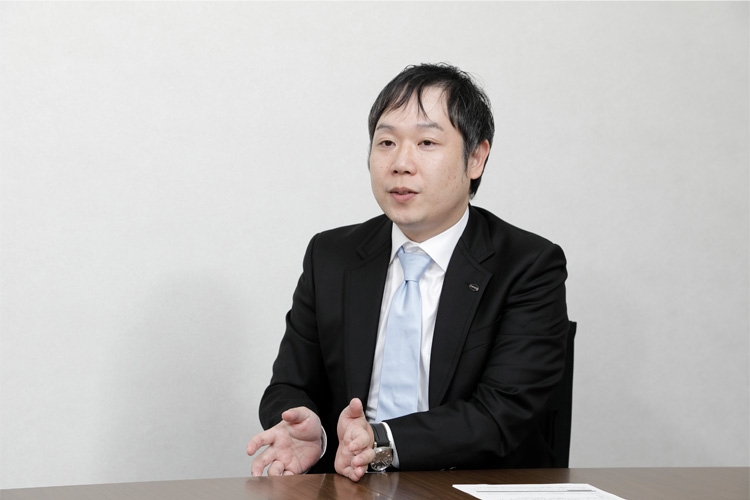
Tatsuki Ii
Stellvertretender Leiter, VHL-Designabteilung 2
Transport Design Group, Designabteilung, Produktionsbetrieb, Reinraumabteilung
Daifuku Co., Ltd.