DAIFUKU Lösungen Intelligente Produktion von Trockenbatterien mit Überkopf-Transportsystemen und automatisierten Lager- und Bereitstellungssystemen
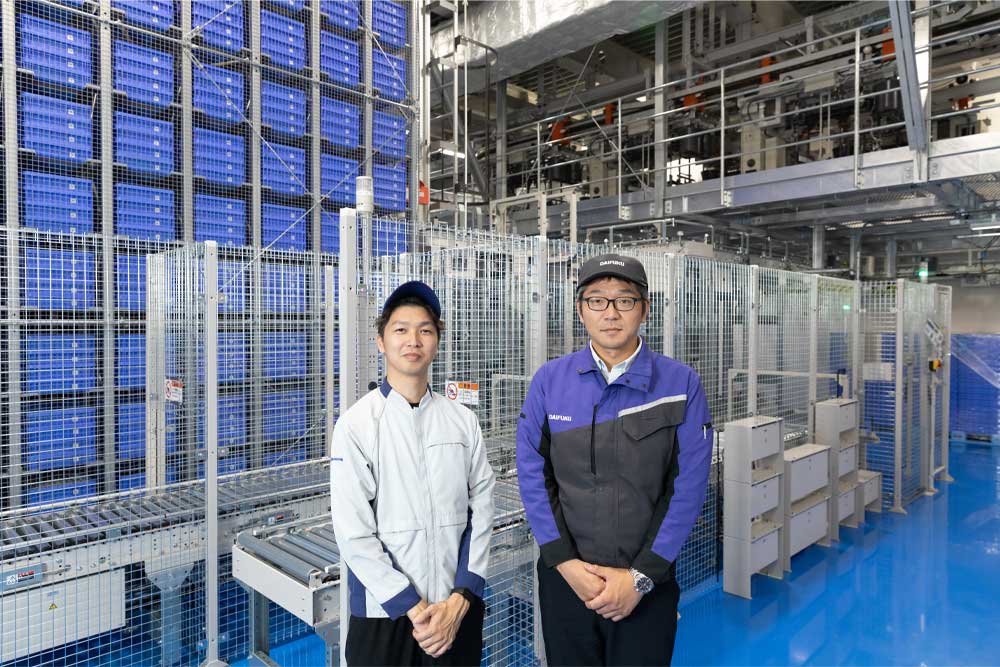
Panasonic Energy Co., Ltd., das alles von Trockenbatterien bis hin zu Industrie- und Autobatterien herstellt, hat seine Produktionsanlagen für Trockenbatterien in die Nishikinohama-Fabrik in Kaizuka City, Osaka, verlegt. Im Zusammenhang mit diesem Umzug führte Panasonic Energy auch eine automatisierte Lösung ein, die aus Überkopf-Transportsystemen und automatisierten Lager- und Bereitstellungssystemen (AS/RSs) besteht. Toma Suzuki (links im Bild), Senior Manager der Produktionstechnikabteilung in der Energy Device Business Division, und Mamoru Kuwahara (rechts) von der Automotive Division von Daifuku, die das Projekt beaufsichtigten, stellen die erste bedeutende Automatisierungsinitiative und das Fabrikverlagerungsprojekt von Panasonic Energy vor, das etwa drei Jahre von 2021 bis 2023 dauerte.
Können Sie uns einen Überblick über das Werk Nishikinohama und die Gründe für die Verlagerung der Produktion von Trockenbatterien dorthin geben?
Suzuki: Die Fabrik in Nishikinohama ist der einzige Produktionsstandort von Panasonic Energy für Trockenbatterien in Japan und einer der größten des Landes. Der Standort produziert Trockenbatterien von D bis AAA und deckt damit in erster Linie den Inlandsbedarf. Die Fabrik war früher eine Produktionsstätte für Solarzellenmodule, aber wir haben die Anlagen vollständig renoviert und 2023, zum 100. Jahrestag unseres Energiegeschäfts, den Vollbetrieb aufgenommen.
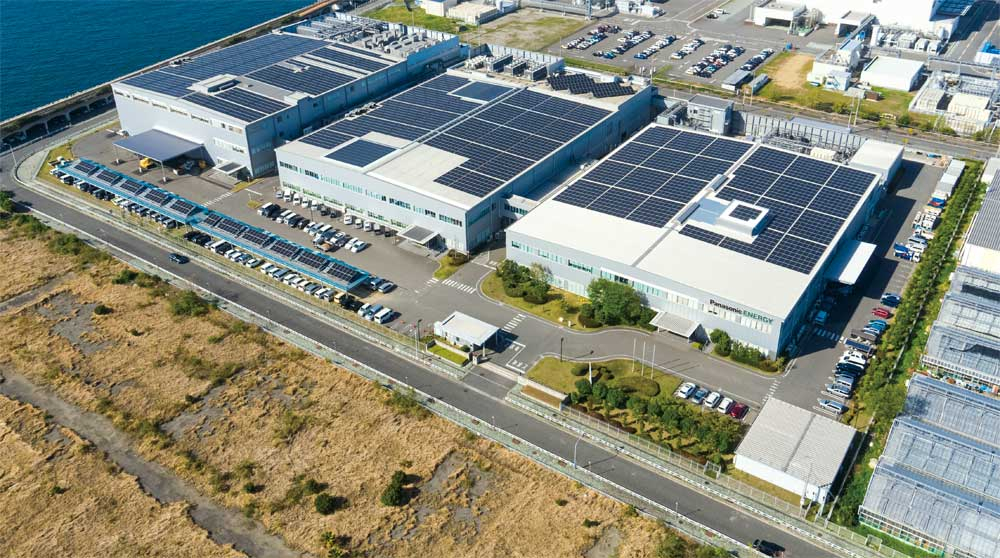
Die Moriguchi-Fabrik in Moriguchi City, Osaka, war über 90 Jahre lang unser Hauptproduktionsstandort für Batterien. Aufgrund von Problemen wie alternden Gebäuden haben wir jedoch das Projekt in Angriff genommen, die Produktion von Trockenbatterien in die Nishikinohama-Fabrik zu verlagern, in der ich als Designer für Produktionsanlagen tätig war. Unser Konzept bestand darin, eine globale Vorzeigefabrik für die Zukunft des Trockenbatteriegeschäfts zu errichten und unserer Verantwortung für die zukünftige Marktversorgung gerecht zu werden. Wir haben uns vorgenommen, ein intelligentes Produktionssystem aufzubauen, das als globales Vorzeigewerk für die Produktion von Trockenbatterien geeignet ist.
Lagerbestandsoptimierung und Verbesserung der Produktionsplanungsgenauigkeit
Auf welche Aspekte haben Sie bei der Installation der Ausrüstung im Werk Nishikinohama am meisten geachtet?
Suzuki: Im Werk Moriguchi produzierten wir bis zu 48 Millionen Trockenbatterien vom Typ D bis AAA pro Monat. Unser Ziel war es, diese Produktionskapazität aufrechtzuerhalten und gleichzeitig verschiedene Produktionsherausforderungen zu bewältigen.
Eine dieser Herausforderungen war die Bestandsverwaltung. Traditionell wurden Trockenbatterien in Schrumpfverpackungen mit mehreren Batterien gelagert. Das bedeutete, dass wir, wenn uns beispielsweise der Vorrat an Zweierpackungen ausging, die Zehnerpackungen nicht für den Versand umpacken konnten. Stattdessen mussten wir neue Batterien produzieren. Indem wir Batterien unverpackt lagerten, konnten wir leichter auf Nachfrageschwankungen reagieren, die Genauigkeit der Produktionsplanung verbessern und den Gesamtbestand reduzieren. Dies ist ein Beispiel dafür, wie wir unser System überarbeitet haben.
Auch die Verbesserung unseres Arbeitsablaufs war unerlässlich. Alle Prozesse in der Fabrik Moriguchi wurden in einem einzigen Gebäude abgewickelt, und wir nutzten Karren und andere Fahrzeuge, um Material zwischen den Prozessen zu transportieren. Da die Fabrik Nishikinohama jedoch 20 % mehr Grundfläche hatte, war sie im Wesentlichen in drei Teile aufgeteilt, wobei Materialien, Halbfabrikate und Fertigprodukte von Gebäude A nach Gebäude C flossen. Angesichts der größeren Entfernungen zwischen den Prozessen berechneten wir, dass wir unsere Belegschaft erheblich aufstocken müssten, um die Produkte weiterhin manuell transportieren zu können. Angesichts der Schwierigkeiten, mehr Personal zu gewinnen, und der Bedenken hinsichtlich des Risikos, dass Trockenbatterien während des Transports herunterfallen oder umkippen könnten, wurde Automatisierung zu einer Notwendigkeit.
Hätte der manuelle Transport mit Karren eine erhebliche Belastung für das Personal dargestellt?
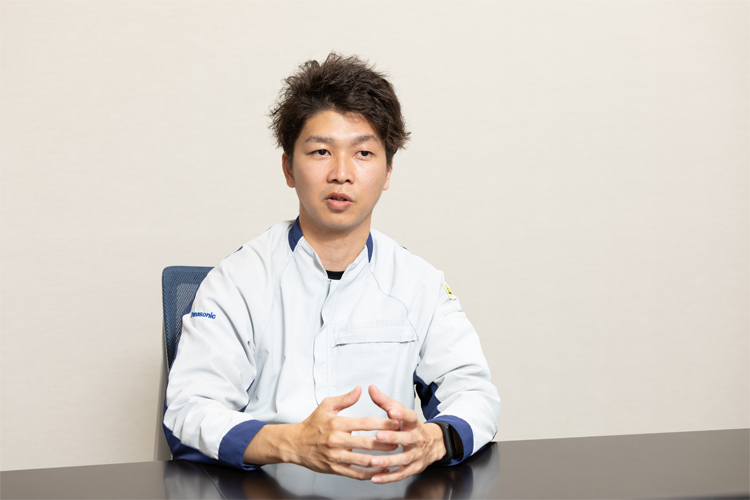
Suzuki: Selbst kleine Batterien haben eine hohe Dichte, und wenn sie in Kartons verpackt sind, werden sie ziemlich schwer und schwierig zu handhaben. Außerdem besteht bei gestapelten Kartons die Gefahr, umzukippen, was hohe Sicherheits- und Qualitätsrisiken mit sich bringt. Deshalb mussten wir nach einer sichereren und effizienteren Möglichkeit suchen, Produkte zu transportieren. Obwohl wir über eine Vielzahl von selbst entwickelten Anlagen verfügen, entschieden wir uns, dass es besser wäre, die Hilfe externer Experten für die Lager- und Transportautomatisierung in Anspruch zu nehmen.
Drastische Verbesserungen bei Bestandsverwaltung und Effizienz durch die Kombination von Überkopf-Transportsystemen und Regalbediengeräten
Ist Daifuku auf diese Weise in das Projekt involviert worden?
Suzuki: Ja, genau. Wir haben mehrere Unternehmen kontaktiert, um herauszufinden, wie wir die unterschiedlich großen Kartons, die während der Produktion verarbeitet werden, automatisch sortieren können, aber keiner konnte uns das bieten, was wir brauchten. Daifuku hat uns Vergleichsdaten und Vorschläge zur Realisierung eines solchen Systems zur Verfügung gestellt, was wir sehr zu schätzen wussten. Obwohl wir ursprünglich vorhatten, Förderbänder für den Transport zu verwenden, war es eine zu große Herausforderung, die Förderbänder in das Layout einzupassen. Daifukus prompte Antworten auf unsere Anfragen führten zu einer reibungslosen Entscheidung, offiziell mit ihnen zusammenzuarbeiten.
Kuwahara: Im Herbst 2021 erhielten wir eine Anfrage zu unserem temporären Lager- und Sortiersystem SPDR (Spider). Im Werk Moriguchi wurden Kartons mit Batterien flach gestapelt, und die Mitarbeiter folgten Versandscheinen für die manuelle Lagerung und Entnahme. Die ursprüngliche Anfrage bestand darin, diesen Arbeitsablauf zu automatisieren, aber wir hielten es für notwendig, ein breiteres Spektrum an Problemen anzugehen. Nach sorgfältiger Überlegung kamen wir zu dem Schluss, dass unser Mini Load AS/RS besser geeignet war, da es die unterschiedlichen Gehäusegrößen von D- bis AAA-Batterien verarbeiten konnte und es uns ermöglichte, den Lagerraum auf ein Drittel des für die flache Lagerung erforderlichen Raums zu reduzieren.
Für den Transport der Produkte haben wir das Ramrun Einschienenbahn-Transportsystem vorgeschlagen, um den Deckenraum des Gebäudes effektiv zu nutzen. Der von uns entwickelte Arbeitsablauf umfasst den Transport fertiger Batterien per Förderband von Gebäude B zum automatisierten Lager in Gebäude C sowie die Verwendung des Ramrun Systems für den Transport der Produkte zu den Verpackungsprozessen und für die Rückgabe leerer Kartons nach dem Transport.
Normalerweise ist die Ladekapazität beim Überkopftransport ein großes Problem, aber Ramrun System von Daifuku wird auch von Automobilherstellern zum Transport von Fahrzeugkarosserien und anderen schweren Teilen verwendet und kann leicht an verschiedene Anforderungen angepasst werden, darunter den Transport von Objekten von leichten bis hin zu mehreren Tonnen schweren Teilen. Im Werk Nishikinohama beträgt das maximale Transportgewicht für D-Batterien etwa 80 kg, was das System problemlos bewältigen kann. Dieses Projekt umfasste auch ein Barcodesystem zum Ändern von Positions- und Geschwindigkeitsbefehlen mit Ramrun, um eine einfache Anpassung an zukünftige Änderungen im Produktionsplan oder an die Verlagerung oder Erweiterung der Ramrun-Stationen zu gewährleisten.
Automatisiertes Einschienenhängebahnsystem für den Transport von Containern
Lagerung von Lagerbeständen in einem Regalbediengerät über ein Förderband
Transportcontainer beladen mit Trockenbatterien
War dies das erste Mal, dass Sie AS/RS oder automatisierte Transportsysteme eingeführt haben?
Suzuki: Dies war das erste Mal, dass wir ein automatisiertes System in einem so großen Maßstab eingeführt haben. Die Vorbereitung war zwar ziemlich anspruchsvoll, aber der Wegfall der Notwendigkeit, zusätzliches Personal einzustellen, war ein großer Vorteil. Außerdem mussten wir in der Fabrik in Moriguchi visuell nach Produkten auf Paletten suchen, die auf dem Boden aufgereiht waren. Das neue Trackingsystem ermöglicht es uns nun, bestimmte Produkte schnell zu lokalisieren, was die Betriebseffizienz erheblich verbessert.
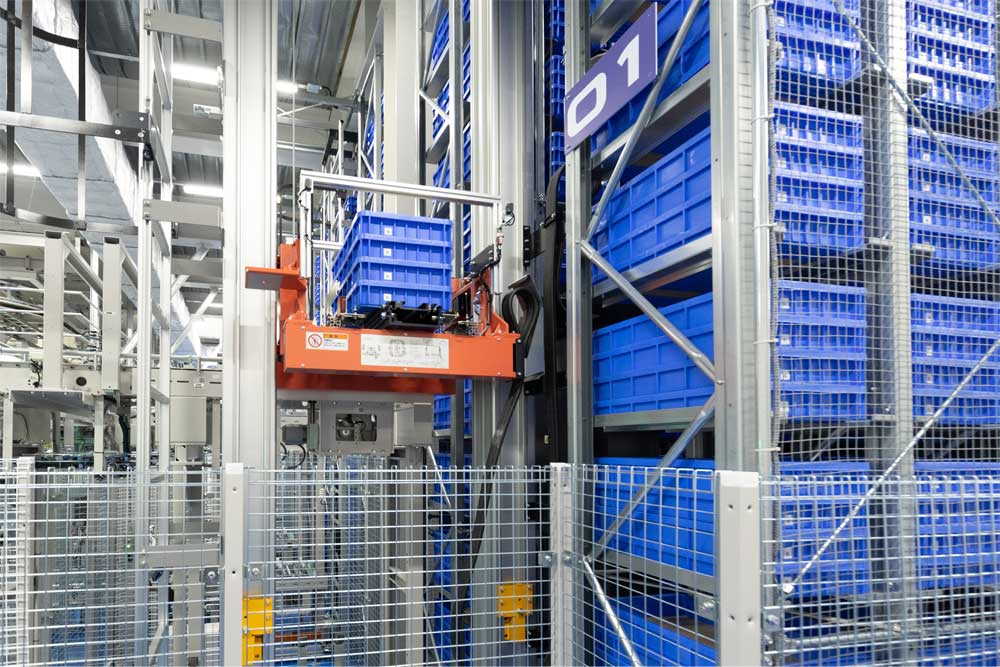
Optimierung der Automatisierung und Mechanisierung bei gleichzeitiger Entscheidung, welche Aufgaben manuell ausgeführt werden sollen
Wie haben Ihre Mitarbeiter auf die Veränderungen in Abläufen und Arbeitsabläufen reagiert?
Suzuki: Anfangs waren nicht alle Mitarbeiter von den Änderungen begeistert, was teilweise daran lag, dass die Arbeiter vor Ort an das herkömmliche Produktionssystem gewöhnt waren. Um etwaige Bedenken auszuräumen, gaben wir Informationen aus der Entwurfsphase weiter und visualisierten und kommunizierten Probleme wie die längeren Transportentfernungen im Werk Nishikinohama. Außerdem besuchten wir gemeinsam die Anlagen, um zu zeigen, welche Arten von Automatisierungsgeräten verfügbar waren. Viele befürchteten, dass der Gesamtbestand nach der Einführung eines Regalbediengerät sinken würde, also führten wir Simulationen auf Grundlage der Produktionsergebnisse der letzten drei Jahre durch. So konnten wir zeigen, dass ein reduzierter Bestand kein Problem darstellen würde. Wir konzentrierten uns auf die Visualisierung und Quantifizierung von Informationen, um die Unsicherheit darüber zu verringern, was die Änderungen mit sich bringen würden.
Vor welchen Herausforderungen standen Sie während des Umzugs?
Suzuki: Der Umzug der Fabrik verlief ziemlich reibungslos. Im Werk Nishikinohama produzieren wir im ersten Stock D- und C-Batterien und im zweiten AA- und AAA-Batterien, wobei wir auf beiden Stockwerken ähnliche Geräte verwenden. Um sicherzustellen, dass die Produktion von Trockenbatterien während des Umzugs nicht unterbrochen wird, konzentrierten wir uns im Werk Moriguchi auf die Produktion von D- und C-Batterien. Sobald ausreichend Lagerbestände aufgebaut waren, wurden die Produktionsanlagen abgebaut und im Werk Nishikinohama wieder aufgebaut. Anschließend taten wir dasselbe für AA- und AAA-Batterien und schlossen den Umzug schrittweise ab.
Bei der Installation der Ausrüstung traten jedoch einige unerwartete Probleme auf. In der Fabrik in Nishikinohama wurden bis 2003 Solarzellenmodule hergestellt. Obwohl wir unsere Ausrüstung anhand der ursprünglichen Konstruktionszeichnungen verlegten, fanden wir nicht gekennzeichnete elektrische Anlagen und Rohrleitungen vor. Außerdem stellten wir fest, dass das Dach leicht geneigt ist, was zu unterschiedlichen Deckenhöhen im zweiten Stock führt. Daifuku hat sich jedoch Möglichkeiten überlegt, diese unvorhergesehenen Probleme flexibel zu lösen, beispielsweise durch die Erweiterung des Überkopftransportsystems.
Kuwahara: Obwohl wir unerwartet Materialien besorgen und Arbeiten zur Schienenverlängerung organisieren mussten, konnten wir die Installation dank der Zusammenarbeit aller vor Ort ohne größere Probleme abschließen, was eine Erleichterung war.
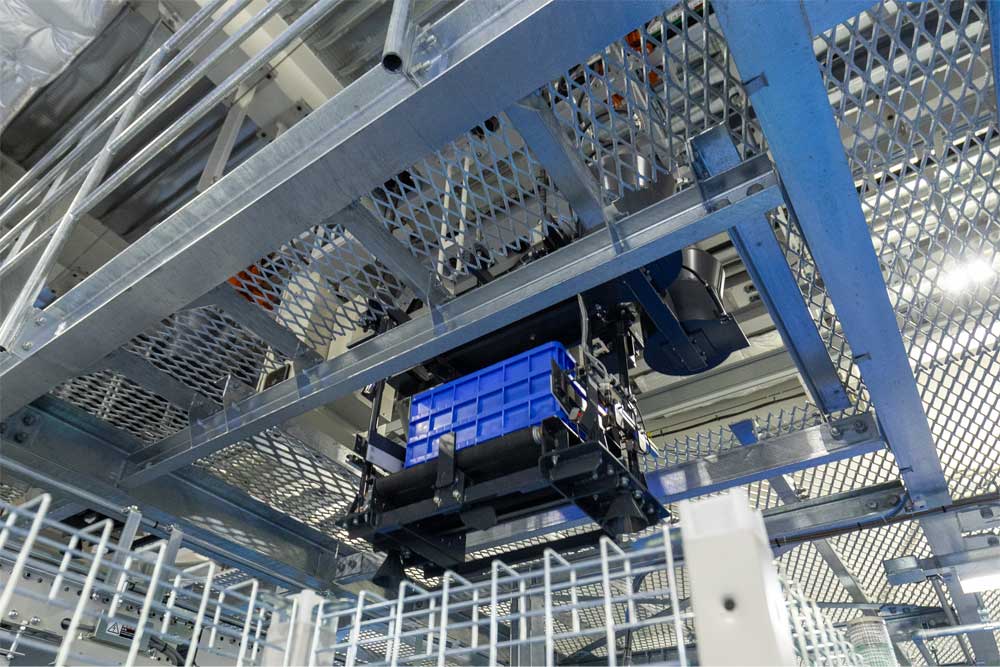
Haben Sie als Fabrik, die sich der Zukunft der Trockenbatterien verschrieben hat, weitere Automatisierungspläne für die Zukunft?
Suzuki: Wir haben den Prozess bis kurz vor dem Verpacken mit Schrumpffolie automatisiert, denken aber auch über Verbesserungen in den nachfolgenden Prozessen nach. Derzeit müssen wir Kartons mit Produkten, die 15 kg oder mehr wiegen, manuell auf Paletten laden, die wir dann mit Gabelstaplern auf Lkw verladen. Wir müssen diese Kartons täglich mehr als 1.000 Mal anheben und entladen, deshalb möchten wir diesen Prozess automatisieren.
Insgesamt haben wir etwa 80 % der Abläufe im Werk Nishikinohama automatisiert. Die verbleibenden 20 % betreffen hauptsächlich die Versorgung mit positiven und negativen Elektrodenmaterialien. Obwohl es noch Raum für Automatisierung gibt, planen wir nicht, alle Abläufe im Werk zu automatisieren. Es gibt immer noch einige Situationen, die menschliches Eingreifen erfordern, beispielsweise bei vorübergehenden Maschinenstopps. Um auf solche Situationen angemessen reagieren zu können, müssen wir zunächst eine sichere Arbeitsumgebung gewährleisten. Um die Produktion im Falle eines Problems weiterlaufen zu lassen, ist außerdem eine gewisse Vertrautheit mit dem Standort erforderlich, und dies erfordert ebenfalls menschliches Eingreifen. In Zukunft werden wir weiterhin darüber nachdenken, wie wir unsere Arbeiter und Maschinen am besten zusammenarbeiten lassen können.
Seit der Betriebsaufnahme im Jahr 1966 haben wir uns auch auf das Engagement der Gemeinschaft konzentriert. Mehr als eine Million Menschen haben an Werksführungen und Workshops zur Batterieherstellung teilgenommen. Wir haben diese Programme auch überarbeitet, um noch bereicherndere Erfahrungen anzubieten. Auch in Zukunft planen wir, unsere Fabrik weiterhin mit der Öffentlichkeit zu teilen, um eine gemeinschaftsorientiertere Einrichtung als je zuvor zu werden.
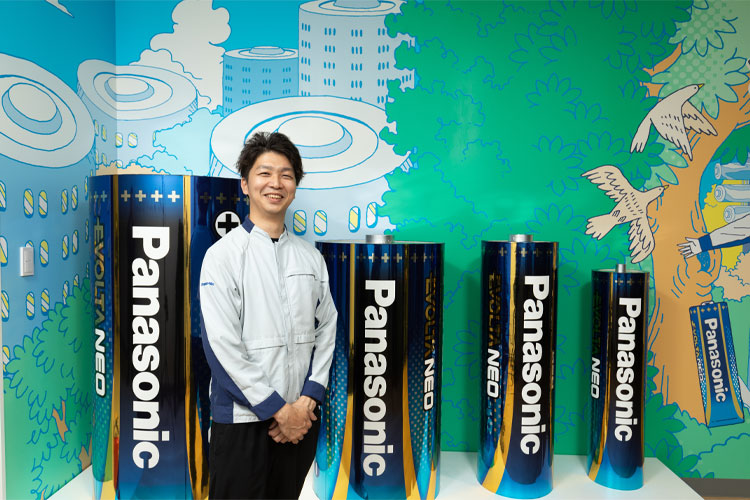
Suzuki-Chef
Abteilung Betriebstechnik, Produktionsmanagement, Geschäftsbereich Verbraucherenergie
Geschäftsbereich Energiegeräte
Panasonic Energy Co., Ltd.
Toma Suzuki kam 2016 zu Panasonic Energy. Er war an der Wartung, dem Design und der Entwicklung von Produktionsanlagen im Werk Moriguchi beteiligt, das sich auf die Produktion von Trockenbatterien konzentrierte. Im Jahr 2020 wechselte er in die Abteilung Global Manufacturing Promotion, wo er an der Einführung neuer Anlagen an ausländischen Produktionsstandorten, darunter in Thailand, arbeitete. Er ist seit 2022 in seiner aktuellen Position und widmet sich weiterhin dem Aufbau von Fertigungssystemen, die die Zukunft des Trockenbatteriegeschäfts prägen werden.