ダイフク流課題解決天井搬送システムと自動倉庫で乾電池生産をスマート化(パナソニック エナジー株式会社様)
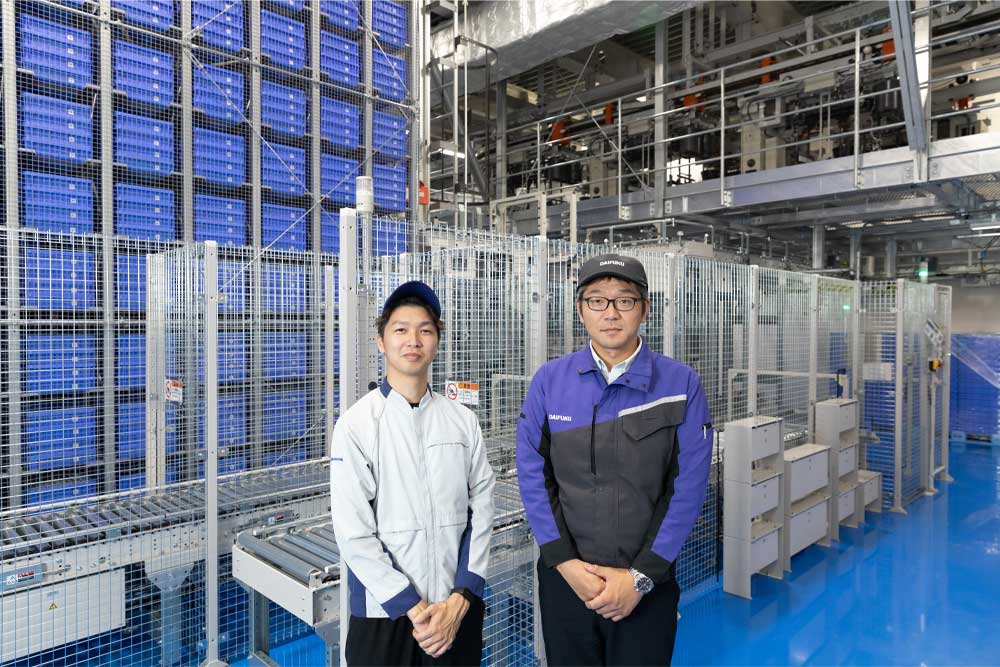
エナジー関連事業の原点ともいえる乾電池事業をはじめ、産業用電池や車載用電池などを手掛けるパナソニック エナジー株式会社様(以下敬称略)。2023年に乾電池の生産拠点を大阪府貝塚市の二色の浜工場へと移転することに伴い、天井搬送と自動倉庫で構成された自動化システムを導入しました。同社初となる大規模な自動化の推進と、約3年間に及ぶ工場移転プロジェクトについて、エナジーデバイス事業部 コンシューマーエナジービジネスユニット生産技術部 プロセス開発課二係 主務の鈴木冬馬様(写真左)と、本件を担当した当社オートモーティブ事業部の桑原護(写真右)が紹介します。
二色の浜工場の概要と、乾電池の生産拠点を移管することになった背景を教えてください。
鈴木(敬称略) 二色の浜工場は当社における日本国内唯一の乾電池生産拠点で、国内最大級の規模を誇ります。単1形から単4形までの乾電池を生産し、主に国内需要に対応しています。以前は太陽電池モジュールの生産拠点でしたが、設備を含め一新し、当社のエナジー関連事業が100周年を迎える2023年に本格稼働を開始しました。
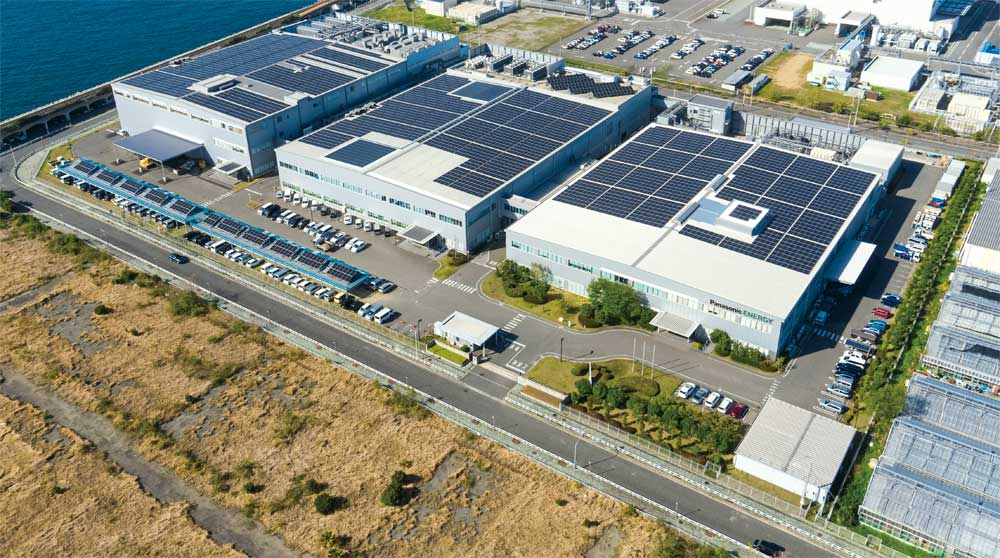
乾電池の生産拠点としてこれまで中心的な役割を果たしてきた守口工場(大阪府守口市)は、90年以上の歴史がある生産拠点でしたが、建屋の老朽化などの課題があったため、乾電池生産を二色の浜工場に移管するプロジェクトが始まり、私は生産設備の設計担当として参画しました。コンセプトは『乾電池事業の未来を拓く「グローバル旗艦工場」』であり、海外も含めた乾電池生産の旗艦工場として相応しいスマートな生産体制を構築し、将来にわたって市場への供給責任を果たしていきます。
在庫の最適化と生産計画の精度向上のために、完成品の一歩手前の状態で在庫管理
二色の浜工場の設備導入の際に重視したのはどのようなことですか。
鈴木 守口工場は単1形から単4形までの乾電池を月に最大4,800万個生産しており、この生産能力を維持することを前提に、さまざまな課題の解決に取り組みました。
その1つが在庫管理です。従来、乾電池は2個パックや10個パックなどシュリンク包装した状態で在庫していました。この場合、2個パックの在庫が足りなくなった場合でも10個パックを包み替えて出荷するわけにはいかず、2個パック用に新たな電池を生産しなければなりません。しかし、包装前の状態で在庫しておくことで、需要変動に対応しやすく生産計画の精度を向上でき、総在庫量を抑えられるのではないかと考え、システム検討を行いました。
また、業務フローの改善も必須の課題でした。1つの建屋で作業していた守口工場では、工程間の搬送に台車などを活用していました。しかし、二色の浜工場は延床面積が1.2倍になる上に、3棟に分かれた構造になり、材料~仕掛品~完成品へと、A棟を上流に下流のC棟へ流れていきます。工程間の移動距離が長くなり、これまでと同じ方法で搬送した場合の工数を試算したところ、追加で10名以上の人員を確保しなければならないことが分かりました。人手の確保は難しく、また搬送中に乾電池の落下や転倒などのリスクも懸念されたため、搬送の自動化が必要条件でした。
台車搬送は作業される方の負担も大きかったのではないでしょうか。
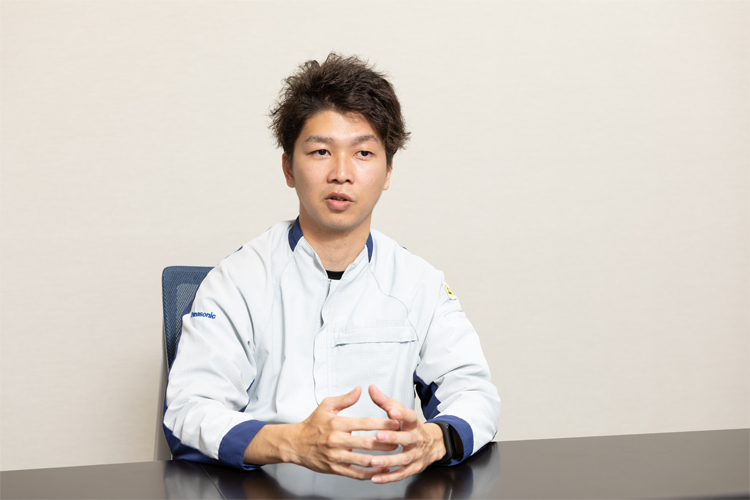
鈴木 電池は小さくても密度が高く、箱詰めすると相当な重量になって上げ下ろしが大変ですし、万が一、積み上げた箱が倒れてしまうと安全面・品質面でリスクが高いことから、効率的で安全な搬送手段を考えなければなりません。当社では、自社設計の設備も多くあり、そこが会社の強みでもあるのですが、保管や搬送の自動化については外部の専門家の力を借りる方が良いと判断しました。
天井搬送と自動倉庫の組み合わせで、在庫管理や作業効率が格段に向上
そこでダイフクに問い合わせをいただいたのですね。
鈴木 はい。工場ではさまざまなサイズのケースを扱うので、それらを自動で仕分ける機械がないかと複数の企業にあたったのですが、良い回答は得られませんでした。そんな中、ダイフクさんには比較資料を添えて、こうした仕組みなら実現できそうという代替案も出していただけてありがたかったです。また、当初は搬送にコンベヤを使うつもりでしたが、どのようにレイアウトを組んでも収めることができずに困っていました。問い合わせにも迅速に対応していただいたので、正式にダイフクさんにお願いすることがスムーズに決まりました。
桑原 2021年秋にケース一時保管・仕分けシステム「SPDR(スパイダー)」についてお問い合わせをいただき、詳しくお話しを伺いました。守口工場では電池の箱を平積みし、入出庫は従業員が伝票に沿って対応するフローとのことで、この作業の自動化をご要望でしたが、より広範囲の課題を踏まえた改善が必要ではないかと考えました。検討の結果、ケース自動倉庫「ファインストッカー」の方が、単1形から単4形すべてのケースに対応可能なことに加え、保管スペースを平置きに比べて今回の場合であれば3分の1にできるため、適していると判断しました。
そして搬送には、モノレール式搬送システム「ラムラン」を導入することで、天井のスペースを有効活用できますので、その組み合わせでご提案しました。搬送の流れとしては、B棟で完成した電池をコンベヤでC棟の自動倉庫に入庫し、出庫する際はラムランで包装工程に運びます。ラムランで電池の搬送に使用した空箱の回収も行います。
一般に天井搬送は耐荷重が問題になるのですが、当社のラムランは自動車メーカーで車体などの搬送システムとしても使われており、軽量のものから数トンのものまで運ぶことが可能で、お客さまのニーズに合わせて細かくカスタマイズできるのが強みです。二色の浜工場の場合、搬送物の重さは単1形で約80kgとかなりの重量ですが、問題なく導入することができました。また今回は、ラムランの位置や速度指令のやり取りに、バーコードを読み込む方式を採用し、将来的な生産計画の変更や、ラムランのステーションの移設・増設などにも対応しやすくしています。
モノレール式の天井搬送システムでコンテナを自動搬送
コンベヤを介して自動倉庫に在庫として保管
乾電池が積み込まれた搬送コンテナ
自動倉庫や自動搬送の導入は今回が初めてですか。
鈴木 今回のような大規模な自動化システムの導入は初めてで、準備に少々苦労しましたが、追加の人員の確保が不要になったことは大きな効果だと考えています。また、守口工場では品質トラブルが起きた場合は床に並ぶパレットから目視で対象物を探していたことに対して、トラッキングシステムで対象物を迅速に探すことができるようになり、オペレーション効率を向上できました。
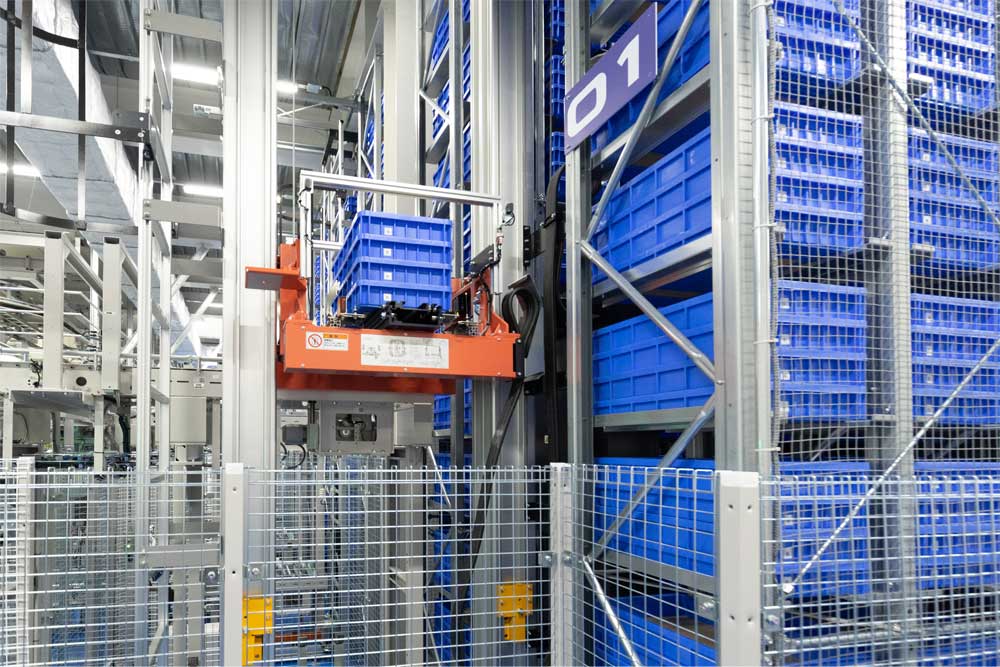
人が行う作業を見極め、適切な自動化・機械化を検討
オペレーションの変更や業務フローの見直しに対する社内の反応はいかがでしたか。
鈴木 現場は従来の生産方式に慣れていることもあり、当初、社内では変更や見直しに好意的な意見ばかりではありませんでした。そこで、設計段階から情報を開示し、二色の浜工場では移動距離が長くなるなどの課題を可視化して伝えたほか、どのような自動化設備があるのかを一緒に視察しました。また、自動倉庫の導入後の総在庫数が減ることを懸念する声も多かったので、過去3年分の生産実績をもとにシミュレーションを行い、在庫を減らしても問題ないことを伝えて理解を得ました。何がどう変わるのか想像できないと不安に思う方もいるので、情報を可視化や数値化することを意識しました。
移管の際に苦労された点はありますか。
鈴木 工場の移管はおおむねスムーズに進みました。二色の浜工場は1階で単1形と単2形を、2階で単3形と単4形を生産し、どちらの階にもほぼ同じ設備が入っています。移管に際しては乾電池の生産を止めることがないよう、まずは守口工場で単1形と単2形を重点的に生産し、十分な在庫を持ってから生産設備を解体して二色の浜工場で組み上げ、その後に単3形と単4形で同じ作業を実施し、段階的に移管しました。
ところが、機器を設置するときに想定外の事態が起こりました。二色の浜工場は2003年まで太陽電池モジュールを生産していた拠点で、建設当時の設計図を参照して各種設備のレイアウトを組んだのですが、いざ現場に入ってみると図面にない電気設備や配管があったり、屋根が緩やかに傾斜していて2階は天井の高さが場所によって違ったりすることが分かったのです。新設の工場にはない大変さがありましたが、天井搬送のレールを延長させるなど、突発的な課題にもダイフクさんには柔軟に対応してもらいました。
桑原 急遽、レールを延長するための部材確保や工事が発生しましたが、現場の皆さまの協力のおかげもあり、大きな問題もなく設置できてほっとしています。
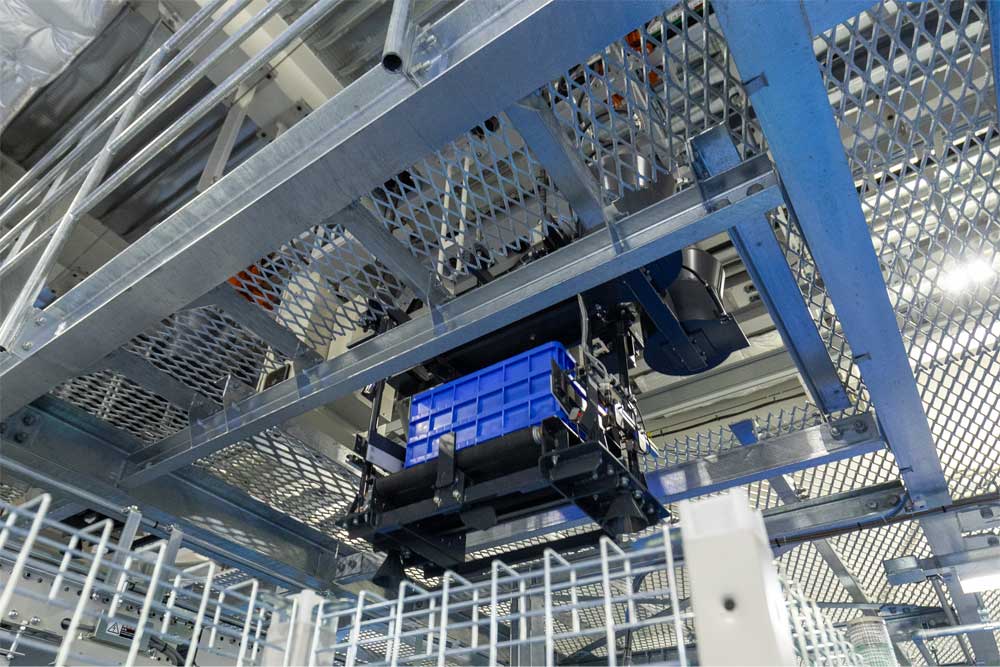
自動倉庫や包装工程のコンベヤに荷台を昇降して移載
乾電池の未来を見据えた工場ということで、さらなる自動化などの計画があればお聞かせください。
鈴木 今回はシュリンク包装する前の工程を自動化しましたが、後工程の改善も検討しています。現在は、製品が入った15kg以上の段ボール箱を手作業でパレットに載せ、フォークリフトでトラックに積み込んでいます。箱の上げ下ろし作業が1日あたり1,000回以上発生しており、自動化を進めたいと思っています。
二色の浜工場全体では約80%の作業を自動化できています。残る20%は正極材料や負極材料の供給プロセスがほとんどで、自動化の余地は残っていますが、工場の完全無人化までは考えていません。例えば機械が一時停止した場合など、人の介入が必要な場面があり、そこで適切に対処するためには人が安全に作業できる環境を確保しておかなければなりませんし、トラブルの際に生産活動を止めないためには人が現場の作業を分かっていなければなりませんから、一定程度の人の関与は必要不可欠です。人と機械をどこまで協働させることができるのか、日々考えていきたいと思っています。
そして社会との共生にも注力し、1966年に開始してから累計100万人以上にご参加いただいた、小学生向け工場見学や手づくり乾電池教室をより充実した内容にリニューアルしました。今後は一般公開も予定し、これまで以上に地域に開かれた工場を目指します。
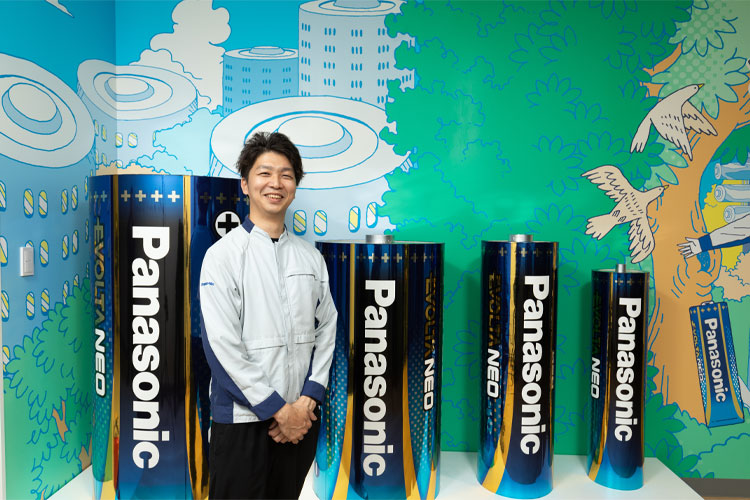
パナソニック エナジー株式会社
エナジーデバイス事業部
コンシューマーエナジービジネスユニット
生産技術部 プロセス開発課二係 主務
鈴木 冬馬 様
2016年入社。乾電池を生産する守口工場で生産設備の保全、設計・開発に携わる。2020年にグローバルモノづくり推進部に異動し、タイをはじめ海外生産拠点の新規設備導入を手掛ける。2022年から現職。乾電池事業の未来を拓くモノづくり体制の構築に挑戦し続けている。