Soluciones DAIFUKU que permiten una fabricación flexible: nuevo sistema de montaje automático de puertas
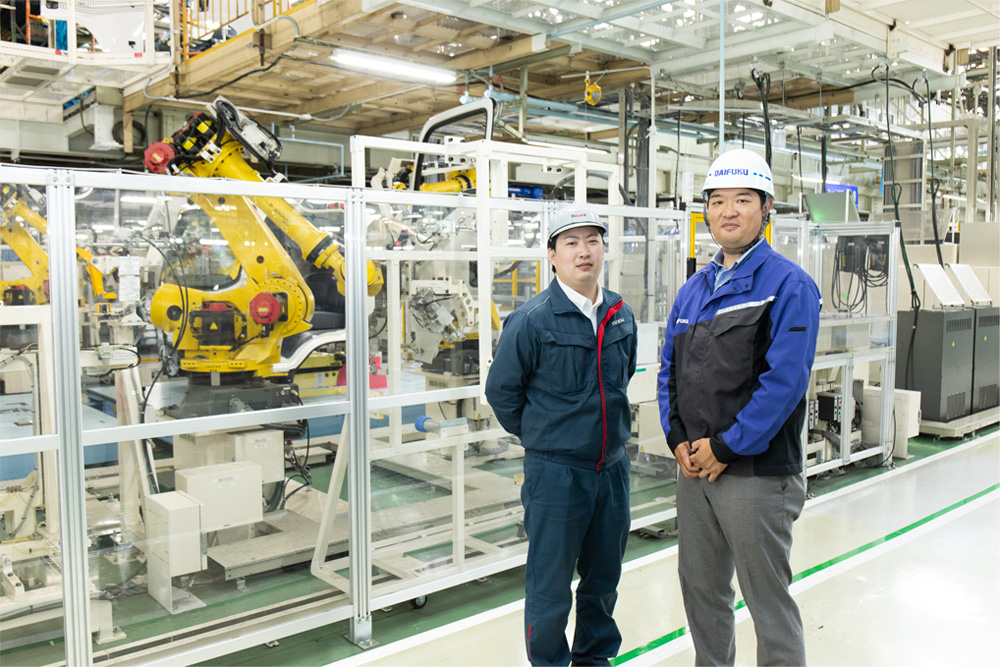
Isuzu Motors Limited (en adelante Isuzu) cuenta con la mayor cuota de vehículos comerciales en Japón. Con la principal excepción de los motores fabricados en la planta de Isuzu en Tochigi, la mayoría de los procesos de producción, incluidos la fabricación y el montaje, se llevan a cabo en la planta de Fujisawa en Kanagawa. Desde que comenzó la operación en la planta de Fujisawa en 1962, Isuzu ha actualizado periódicamente sus equipos para adaptarse a los tiempos. En el verano de 2022, llegó el momento de actualizar el sistema de montaje automático de puertas. Yusuke Ueki del Grupo de Ensamblaje de Cabinas de Isuzu en el Departamento de Ingeniería de Vehículos (a la izquierda en la foto), y el líder del proyecto Yusuke Hayashi de la División Automotriz de Daifuku (a la derecha en la foto), nos informaron sobre lo que cambió con la implementación de este nuevo sistema.
¿Qué procesos se llevan a cabo en la Planta Fujisawa?
Ueki: La planta ensambla nuestros camiones ligeros, medianos y pesados y también está equipada con una instalación de investigación. Con una superficie de unos 820.000 ㎡, se tarda aproximadamente 20 minutos en caminar de un extremo a otro. El sitio cuenta con cuatro edificios de planta: la Planta 1 se encarga del prensado, la soldadura y la pintura, la Planta 2 realiza el equipamiento de la cabina y el ensamblaje del vehículo, y la Planta 3 y la Planta 4 fabrican el eje, la transmisión y otras partes del tren motriz.
¿Qué tipo de trabajos implica el equipamiento realizado en la Planta 2?
Ueki: El equipamiento incluye la instalación de piezas en la cabina, como el cristal delantero, los asientos y el panel de instrumentos, además del montaje de las puertas. La Planta 1 realiza la carpintería metálica para la realización de la cabina y marcos de puertas, además de la pintura, que se realiza con las puertas montadas. Una vez terminada la pintura, la cabina se transfiere a la Planta 2. Sin embargo, es difícil realizar el equipamiento, tanto dentro como fuera de la cabina, mientras se montan las puertas. Por ello, en la Planta 2 se retiran las puertas de la cabina de entrada a la línea de equipamiento. La cabina y las puertas se colocan en líneas separadas donde cada una está equipada. Una vez completadas, las líneas se fusionan y las puertas se vuelven a montar en la cabina. Aquí es donde se actualizó el sistema para montar automáticamente las puertas.
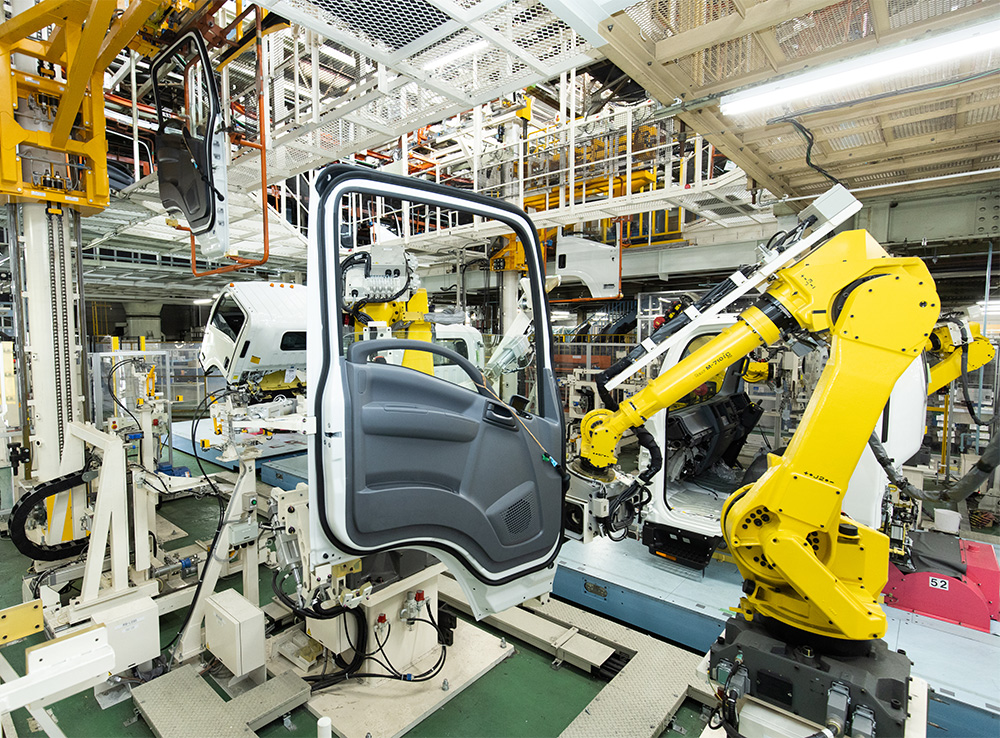
¿Por qué se acercó a Daifuku para actualizar su sistema?
Ueki: A medida que la cabina avanza a lo largo de una línea en el primer piso, las puertas retiradas se levantan y se colocan en una sublínea ubicada en el nivel del entresuelo. Esta sublínea de puertas también es un sistema Daifuku y han transcurrido unos 30 años desde su implementación. Creo que la calidad para soportar tantos años de funcionamiento es asombrosa. Dado que los sistemas de Daifuku también se incorporan a otras líneas e Isuzu está en contacto regular con la empresa, decidimos consultar también sobre la actualización del sistema de montaje automático de puertas.
Esforzarnos por mejorar la productividad y proporcionar soporte flexible para nuevos modelos de vehículos.
¿Qué te hizo empezar a pensar que era hora de actualizar el sistema?
Ueki: Hubo dos razones. El primero fue el deseo de aumentar el rendimiento de los equipos y mejorar la productividad. La industria del automóvil está viviendo una revolución y debemos responder a los cambios del mercado. Las bases de producción siempre están tratando de pensar en formas de mejorar la eficiencia, así que creo que esto es extremadamente natural.
El segundo era dar cabida a nuevos modelos con diferentes ángulos de apertura de puertas. Las puertas de los modelos anteriores se abrieron casi 90 grados durante el montaje y 70 grados en el momento del envío después de colocar piezas adicionales. Para mejorar la eficiencia y reducir la cantidad de piezas, decidimos embarcarnos en el desarrollo de un modelo de vehículo con un ángulo de apertura de puerta de 70 grados durante el montaje de la puerta. Como el sistema de montaje automático de puertas que estábamos usando no admitía un ángulo de montaje de 70 grados, comenzamos a considerar una actualización del sistema.
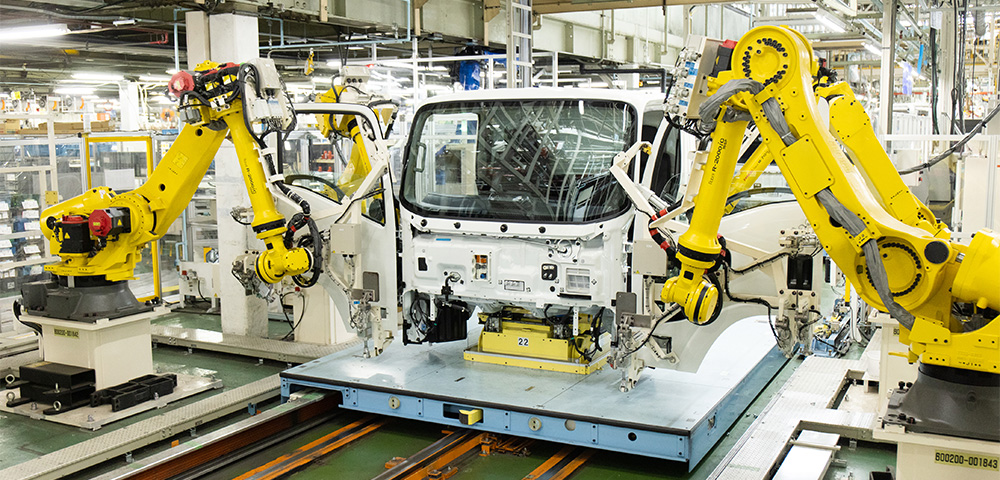
Hay un total de cuatro robots, dos a cada lado. Uno sostiene la puerta y el otro determina la posición de fijación y luego realiza el trabajo de fijación.
¿Existe una gran diferencia entre 90 grados y 70 grados?
Ueki: La diferencia es enorme. Se inserta un brazo robótico en el lado interior de la puerta para apretar los pernos durante el montaje, pero reducir el ángulo de apertura a 70 grados disminuye el rango en el que el brazo puede moverse. Necesitábamos un sistema capaz de realizar el trabajo de montaje de forma segura y adecuada, porque no podemos enviar un vehículo si una puerta o la carrocería terminan dañadas por trabajar en ese espacio tan estrecho.
También queríamos eliminar la necesidad de posicionar la cabina. Con el sistema anterior, la cabina y el transportador debían estar correctamente posicionados en el punto donde comenzaba el proceso de automatización de la puerta. Sin embargo, esto aumenta el tiempo del ciclo, lo que reduce la productividad, y era un punto clave que buscábamos mejorar.
Reducir el ángulo de apertura de la puerta a 70 grados.
La diferencia de 20 grados fue un desafío difícil
¿Qué le llevó a elegir Daifuku para actualizar su sistema?
Ueki: Consultamos con varios fabricantes sobre cómo lograr estos objetivos y propusieron varias tecnologías e ideas. Entre los fabricantes, fue Daifuku quien claramente proporcionó toda la información que necesitábamos para tomar una decisión.
Con nuestros planes de alejarnos del posicionamiento preciso de la cabina, cada accesorio de puerta tendría cambios mínimos en las posiciones de los pernos y necesitaríamos una combinación de cámaras, sensores y otras herramientas de alto rendimiento, ya que no existe una solución universal que pueda realizar la tarea sola. Cada propuesta que recibimos vino como un conjunto singular de sistemas que tenía sus propias ventajas y desventajas. Daifuku, sin embargo, proporcionó un documento que detalla las características de cada producto, la compatibilidad de las combinaciones de productos, los motivos para proponer dichas combinaciones y otra información que nos permitió realizar rápidamente una revisión comparativa. Este documento fue extremadamente útil ya que pudimos circularlo fácilmente internamente para ayudar con el proceso de toma de decisiones.
Además, ya habíamos decidido cambiar la ubicación de instalación del sistema de montaje automático de puertas y previamente habíamos consultado con Daifuku sobre la mejora de la sublínea de puertas. Dado que la propuesta que recibimos de Daifuku cuando consultamos sobre el sistema de montaje automático de puertas también fue excelente, esperábamos que la calidad de la operación mejorara aún más si le pedíamos a Daifuku que abordara todo el proyecto, desde la transferencia de la puerta hasta el montaje automático.
Además, la respuesta a nuestra consulta fue impresionante. Aunque no hubo gran diferencia entre la velocidad con la que respondió cada empresa, la respuesta de Daifuku fue precisa y rápida, por lo que sentimos que existe una fuerte colaboración entre los departamentos de ingeniería y ventas, así como un entorno de comunicación fluido.
¿Por qué cambió la ubicación de instalación del nuevo sistema de montaje automático de puertas?
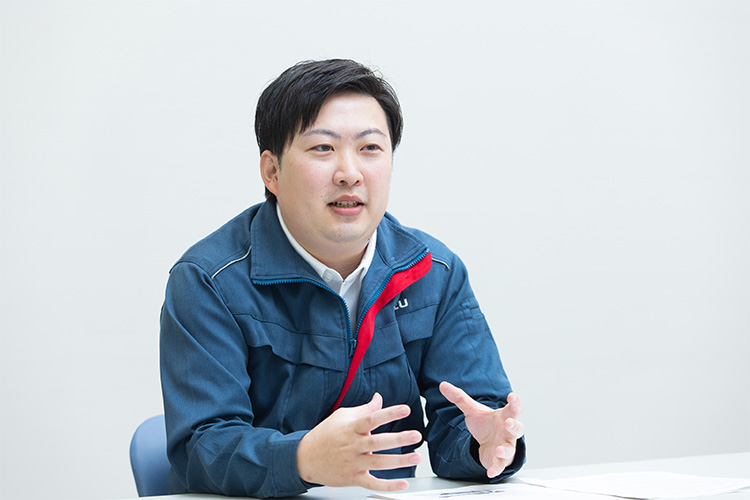
Ueki: Para permitir que la producción continúe al mismo tiempo. No es posible detener la producción en una planta en funcionamiento sólo porque se están actualizando los equipos. El equipo original debe permanecer operativo mientras se instala el nuevo equipo. La programación y la gestión de procesos fueron extremadamente difíciles ya que el trabajo se limitaba a los sábados y domingos cuando la planta estaba cerrada. Además, el trabajo debía terminarse temprano cada domingo para probar el funcionamiento del equipo y garantizar que no afectaría la producción a partir del lunes.
El trabajo de instalación se realizó primero para el elevador de caída que alimenta las puertas desde la sublínea de puertas hasta el sistema de montaje automático. El trabajo para obtener medidas de instalación precisas y crear el diseño del nuevo sistema de montaje automático de la puerta se realizó simultáneamente con el trabajo de instalación del elevador de caída. Tuvimos reuniones con Daifuku casi todas las semanas y después de dos meses de planificación, recibimos los diagramas de instalación y los modelos 3D. Después de resolver algunos detalles restantes, se completaron los planos finales.
¿Qué en particular planteó un desafío en el proceso de diseño?
Ueki: La mayoría de las conversaciones con Daifuku fueron sobre el atornillador y el manejo de materiales. El sistema de montaje automático de puertas tiene una llave dinamométrica neumática, llamada atornillador, para apretar los pernos automáticamente. El atornillador está fijado al extremo de un brazo robótico. Dado que el brazo robótico del nuevo modelo tendría una disminución en su rango de movimiento, le pedimos a Daifuku que diseñara el sistema para garantizar que el brazo no golpeara la cabina o la puerta.
Hayashi: Preguntamos a varios fabricantes si tenían un aprietatuercas que pudiera funcionar en un espacio reducido, pero no existía ningún producto con las capacidades necesarias. Entonces, utilizamos el modelado 3D para probar cómo adelgazar la cabeza del atornillador y probar una nueva forma de soporte. Después de mucho pensarlo, desarrollamos una forma única y presentamos una propuesta de este nuevo atornillador a un fabricante. Se adoptó nuestro nuevo diseño de atornillador, lo que nos permitió crear un sistema que permitía realizar el trabajo de fijación de la puerta de forma segura dentro del margen limitado de 2 a 3 mm.
Alcanzar con éxito los objetivos de producción.
Adaptación a nuevos modelos de vehículos
Con condiciones tan estrictas, ¿le resultó difícil diseñar el sistema global?
Ueki: Creo que debe haber sido difícil satisfacer nuestra demanda de crear un mecanismo que permita al atornillador realizar ajustes finos y flexibles en su alineación para cada operación. Cuando el atornillador inserta los pernos para el montaje, si está desalineado, los pernos se insertarán en ángulo. Si eso sucede, un trabajador tendrá que ir a solucionar el problema y, en algunos casos, es posible que sea necesario reemplazar la puerta. El equipo antiguo permitía cierto movimiento, pero queríamos que el nuevo equipo se moviera con mayor flexibilidad al insertar el perno. Sin embargo, si el aprietatuercas está demasiado flojo en el brazo, se balanceará y no podrá levantar el perno correctamente, por lo que sostuvimos muchas discusiones sobre el diseño para asegurarnos de que el aprietatuercas solo se ajuste cuando apriete el perno en su orificio.
Hayashi: Este problema está relacionado con el tema del posicionamiento. El equipo antiguo primero levantó la cabina para colocarla con precisión y luego comenzó el proceso de montaje de la puerta. Pero el nuevo sistema realiza el trabajo de montaje de la puerta mientras la cabina todavía está en el transportador, por lo que las variaciones en la posición de la cabina son inevitables. Por lo tanto, instalamos el nuevo sistema de montaje automático de puertas para mejorar la flexibilidad de la instalación.
Se utiliza una cámara para identificar la posición de los orificios de los pernos, pero la cámara utilizada con el equipo antiguo sólo podía capturar una ubicación determinada, lo que significa que no se podía adquirir información precisa si la posición de la cabina varía. Imaginamos un sistema de control en el que un robot sostiene una cámara y la posición de los otros dos robots se determina en función de su información. Nos pusimos en contacto con varios fabricantes para intentar encontrar un sistema de cámara que cumpliera las condiciones, pero ningún producto existente lo hizo. Al final, desarrollamos un nuevo sistema en coordinación con uno de los fabricantes.
El posicionamiento se identifica con una cámara (izquierda) y luego se monta la puerta (derecha)
Se incorporaron una serie de nuevas ideas experimentales al nuevo equipo. ¿Hubo alguna preocupación?
Ueki: Al actualizar equipos, Isuzu siempre solicita que se pruebe minuciosamente el funcionamiento del equipo. Incluso si no hay problemas en las simulaciones 3D, se pueden encontrar algunos problemas o puntos a mejorar durante la operación real. Si se encuentran problemas después de la integración total, habrá limitaciones en términos de tiempo de trabajo y métodos al realizar las correcciones. Por lo tanto, solicitamos que se realicen pruebas con anticipación y se realizaron ejecuciones de demostración del sistema meses antes de la integración completa. Cuando inspeccioné el sistema en funcionamiento, quedé muy impresionado porque era exactamente lo que estábamos buscando. Aunque todavía eran necesarios algunos ajustes menores, se trataba de un nivel de perfección excepcionalmente alto.
Ha pasado casi un año desde que el sistema entró en funcionamiento. ¿Estás satisfecho?
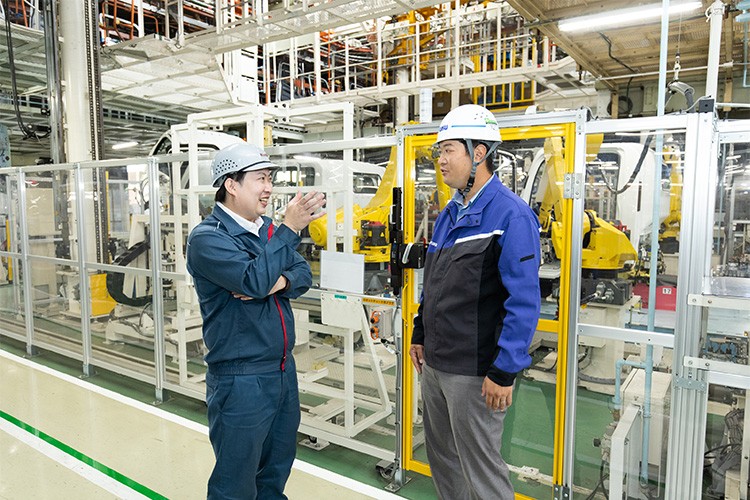
Ueki: Los resultados que imaginamos durante la fase de planificación se han realizado suficientemente. Nuestro objetivo de acortar el tiempo del ciclo se ha logrado y el sistema tampoco tiene problemas para adaptarse a los nuevos modelos de vehículos. En medio de los cambios que se están produciendo en la industria automotriz, Isuzu asumirá el desafío de desarrollar varios tipos de vehículos en el futuro. La producción debe ser capaz de manejar tales cambios, por lo que para nosotros era muy importante eliminar el posicionamiento de la cabina con esta actualización. En términos de la planta en general, queremos construir un sistema que pueda responder de manera flexible, lo que significa que todavía tenemos otros aspectos sobre los que deseamos consultar con Daifuku.
Hayashi: En los últimos años, Daifuku ha ido fortaleciendo su apoyo, no sólo a los sistemas de transporte convencionales, sino también a la robotización. Mientras tanto, si bien hubo muchos desafíos al implementar este nuevo sistema, estamos extremadamente agradecidos con Isuzu Motors por crear un entorno en el que fue fácil proponer nuevas ideas. Continuaremos trabajando para satisfacer las necesidades futuras de automatización en la diversificada industria automotriz.
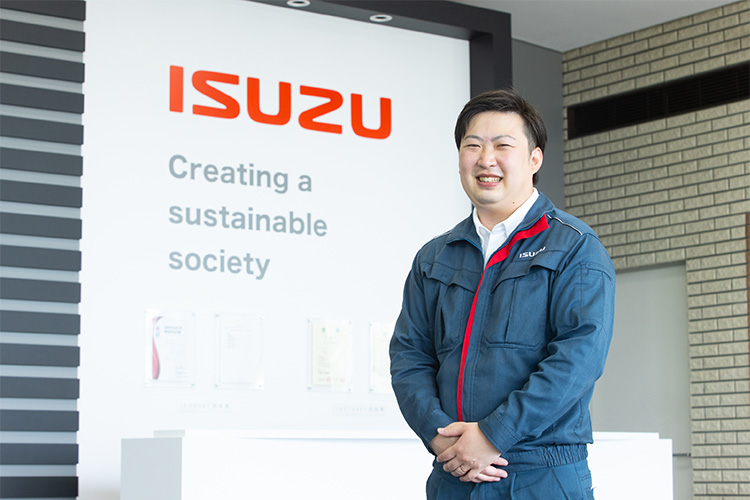
Yusuke Ueki
Grupo de ensamblaje de cabinas, Departamento de ingeniería de vehículos
Isuzu Motors Limitado
Yusuke Ueki se unió a Isuzu Motors Limited y fue asignado al Departamento de Fabricación en 2014. Después de adquirir experiencia en múltiples departamentos, incluida la Sección de Mantenimiento, fue transferido al Grupo de Ensamblaje de Cabinas en 2016. Actualmente trabaja en la Planta Fujisawa en Kanagawa, que ensambla Camiones livianos, medianos y pesados.