Where to Automate First?
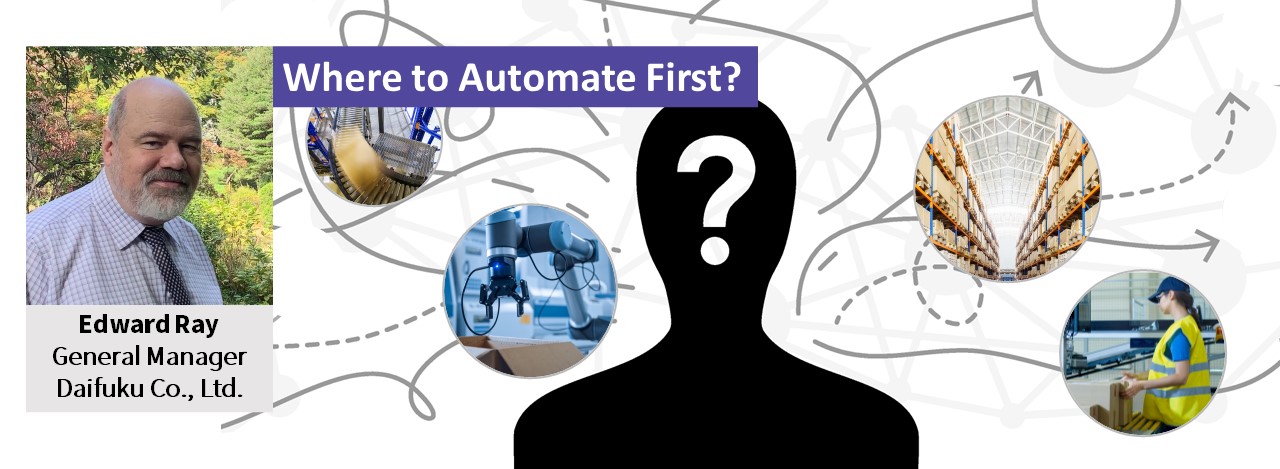
In this day in age, almost anyone in a management position in a factory or distribution center (DC) is considering some sort of automation for materials handling. While some will have experience with automated materials handling, others will not.
If you are starting to feel the pinch of your business growing faster than your manual processes can keep up with, you might be trying to figure out where to start with automation. I would like to offer some general thoughts for consideration, for both a factory and a distribution center. My recommendations will assume that the appropriate warehouse control software will be part of any automated solution.
Recommended First Materials Handling Automation for a Factory
While automating the production line in a factory is beyond the scope of what we will cover here, in a factory, we can generalize that there are the following opportunities for material handling automation:
- Raw materials supply
- Packaging materials supply
- Work-in-process staging
- Finished goods put-away
While the case can be made for automation in all of these areas, it is my opinion that for most companies the first place to begin automation is finished goods put-away.
The logic
Slow handling of finished goods coming of the production line causes clogs that hinder your manufacturing, meaning you cannot realize full production capabilities, leading to unrealized profits.
Automating the put-away process for finished goods means you can extend your factory working hours without extending the hours of your warehousing staff. Further, automating the process means a computer will know where everything is, so later warehouse processes are likely to be streamlined as well.
How it works
As products are finished from your production lines, they are palletized either manually or automatically, and then conveyed to a finished goods automated storage and retrieval system (AS/RS). This system can be located adjacent to your factory, and because it can be built high it maximizes available vertical space and inventory storage capacity. Loads are identified on the way in, and automatically stored by stacker cranes. The computer remembers where each item is, so that later when shipping is necessary, they can be immediately retrieved to support your shipping operations.
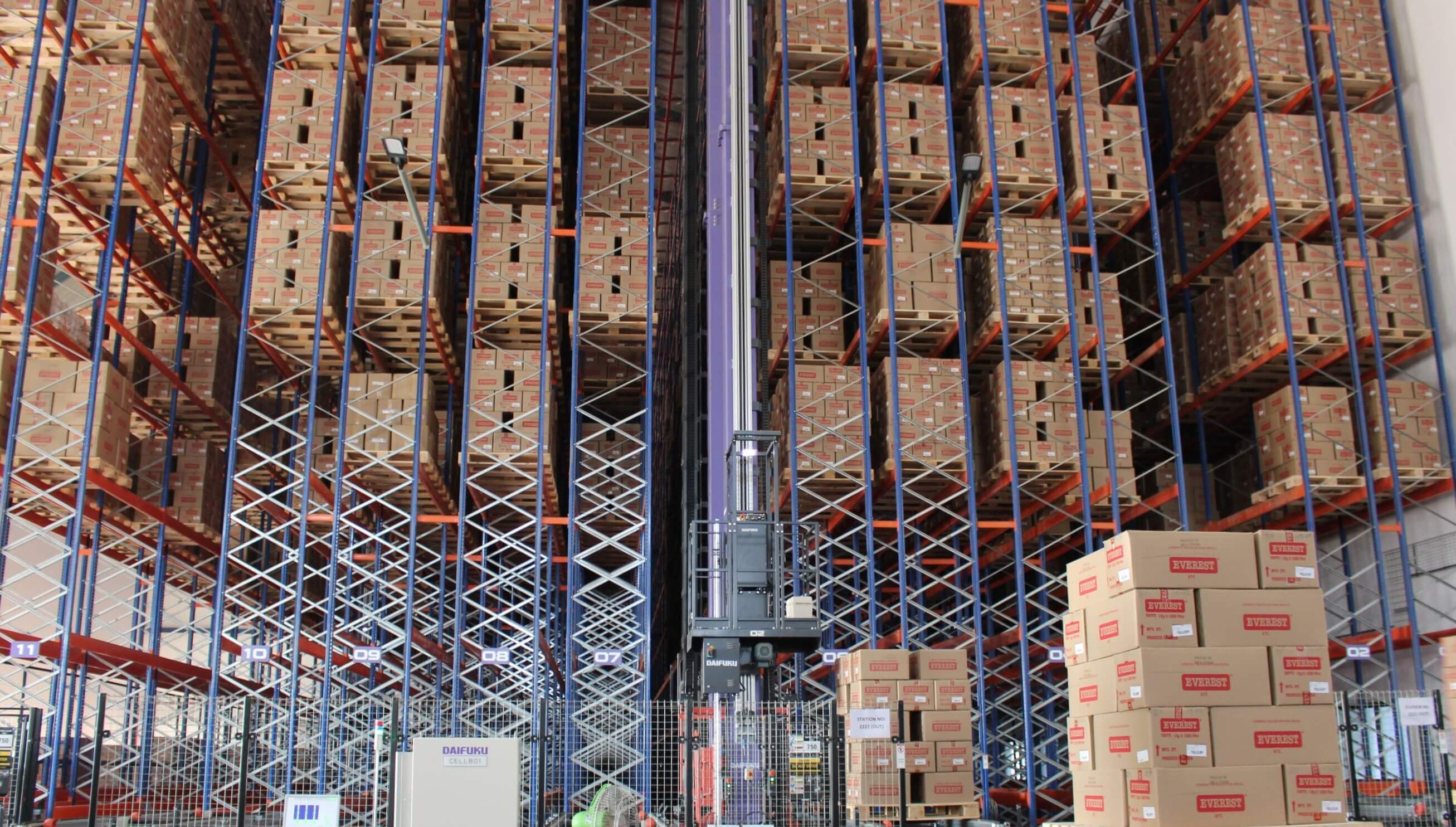
Recommended First Materials Handling Automation for a Distribution Center
The main job of a DC is to get orders to customers. Thus, picking and assembling orders are first on the mind of managers in a DC. From my experience, either order picking or replenishment automation is the ideal place to start. However, when looking at automated solutions from the perspective of the benefits received, order picking automation is typically more expensive per unit of "advantage" (such as workhours saved, space saved, mistakes avoided, etc.) than automating replenishment processes. As a result, replenishment is the best place to start in most cases.
The logic
One of the worst things that can happen to affect your DC is if a picker goes to the location that is to be picked from and the item is not there. At that point there are a few choices, all with consequences:
- Call someone to replenish the item and wait for it to be brought—a significant loss of time for the picking process.
- Create an "exception order" that goes to a special location for adding the item later—having too many of these processes is very inefficient, and may mean that shipments are delayed.
- Ship the order with the item short—Depending on your industry, this could be business critical, as you risk losing a customer when they have to go somewhere else to get a similar item.
Replenishment in a DC typically refers to the act of moving larger sets of items to places where they will become smaller to fulfill orders. For example, pallets may have cases picked from them to fulfill orders or cases may have pieces picked from them to fulfill orders.
One thing to bear in mind when considering these points is that it is cheaper per unit to automatically store, transport, and handle larger items than smaller ones. For example, if you require a total inventory of 160,000 cases and 40 cases can fit on one pallet, that would be 4,000 pallet locations if stored as pallets – that would require around two or three unit load AS/RS aisles. However, if done via a mini load AS/RS, it would require between 8 and 10 aisles, which will be both more costly and take up more space, so advantages have to be weighed carefully.
How it works
At the most basic level, your Warehouse Management System will be directing your order fulfillment and will be keeping tabs on inventory being decremented in the picking area. At the appropriate time, the Warehouse Management System can direct an AS/RS to bring out an appropriate load for replenishing an SKU that has been depleted by order picking. The load is delivered to the outbound conveyor, signaling to the operator that work is to be done. When the operator scans the load, the WMS will them to refill the appropriate pick location, thus guaranteeing that someone doing picking will always have inventory when they need it and avoiding all the three inefficiencies talked about above.
Some automated replenishment systems can be even more sophisticated, with pick locations being directly filled by automation, such as when an AS/RS is used to directly fill a pick location on the side of the AS/RS.
Conclusion
While there are few hard-and-fast rules for determining where to start with automation, I hope from the above you can see that automating your end-of-production put-away if you are in a factory environment and automating your replenishment if your primary function is distribution, are often the best places to consider your first foray into the world of material handling automation.
Automated System Scale
While automation is often highlighted through large-scale systems, system size is based on individual customer needs. Thus, systems can be small depending on capacity and throughput requirements and available floor space. Check out the Unit Load AS/RS Model Systems page to see how systems of varying sizes can be deployed.
Edward Ray
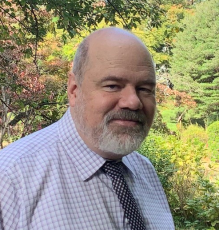
General Manager, Intralogistics Division at Daifuku
Edward Ray has more than 30 years of experience in the automated material handling industry, the majority of which has been spent in international business development. He is based in Tokyo and is currently the General Manager of Sales for Daifuku Co., Ltd.'s Intralogistics Division. Edward is also a board member of Daifuku Group companies Daifuku Intralogistics India and Daifuku Oceania.