TPM: Critical Approach to Optimal Productivity
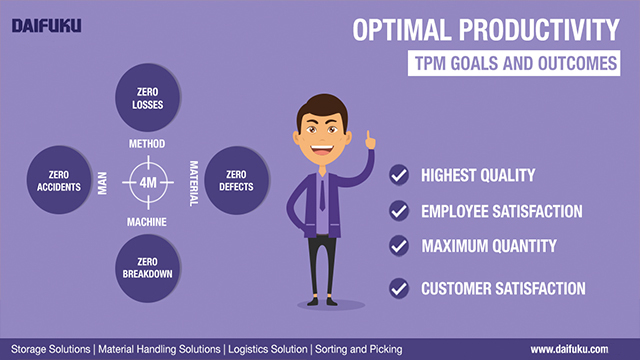
Considered the medical science of machines, TPM (Total Productive Maintenance) is an innovative concept introduced by the Japanese to the world. Japan is widely recognized as a master in quality production. The origin of TPM can be traced way back to 1951, when preventive maintenance was introduced in the country. With increasing automation, regular and preventive maintenance of machines became crucial to increase productivity.
What is TPM?
The idea behind introducing TPM was to get operators involved in maintaining their equipment and make them responsible for their machines, encouraging them to proactively carry out maintenance to achieve ideal production and zero breakdowns, prevent losses and defects, and ensure a safe working environment.
More accurately, TPM is a timely maintenance program carried out in a factory to increase productivity of its machines and equipment with modest investments in maintenance. TPM has a holistic approach to improve the Overall Equipment Effectiveness (OEE) of plant equipment, which is its main objective, along with improving the quality and quantity of production and boosting employee morale and job satisfaction.
TPM is made up of five elements – Man, Machine, Material, Method (know as 4M) and Tools. TPM creates the right environment between all these factors of production, which helps maximize the operational efficiency and achieve manufacturing excellence. In other words, efficient material handling is crucial for successful TPM.
TPM vs. TQM
Total Quality Management (TQM), another management system, is sometimes compared to TPM. While there is some overlap between the two, each has distinct points that differentiate it from the other.
TQM is the continual process of detecting and reducing (or eliminating) errors in manufacturing, streamlining supply chain management, improving the customer experience, and ensuring that employees are up to speed with training. It can be said that TQM aims to hold all people involved in the production process accountable for the overall quality of the final product or service.
If we look at both in terms of their core goals, TQM focuses on improving the quality of goods and services, while TPM focuses on the equipment and processes used to produce the product.
The 8 Pillars of TPM – Way towards 5S Manufacturing Excellence
5S is the very foundation on which the eight pillars of TPM can exist. Implementing 5S helps make problems easily visible and the workplace clean and well-organized.
- Jishu hozen (autonomous maintenance) – small maintenance tasks on a continual basis
- Making operators responsible for the up keep of their equipment with small, regular tasks to help prevent equipment from deteriorating.
- Kobetsu kaizen (KK) – small improvements on a continual basis.
- Kaizen is the most well-known philosophy introduced by Japan to the world. Kaizen simply means 'change for the better' through continuous improvement, which is not only pertaining to manufacturing but improvements in all areas of a company.
- Planned maintenance – proactive and reactive approaches
- Scheduled maintenance based on the predicted and measured failure rates to ensure trouble-free machines and defect-free products. Customer satisfaction is the end goal.
- Quality maintenance – Proactive method
- The goal for any manufacturing facility is to have 'defect-free manufacturing'. This is achievable only by maintaining the highest level of quality standards. Being proactive in quality control and assurance helps detect errors and eliminate them, which leads to fewer customer complaints.
- Training and education – a well-informed workforce
- In order to do away with the knowledge gaps, the workforce has to be well informed. The operator should develop skills to understand not only how the machine works, but also the reasons behind any potential problems, if any. Training and education develop the personnel's skills and techniques to deal with a particular problem in a proactive way. Proper training of personnel is necessary for achieving TPM goals.
- Safety, health, and environment (SHE) – peripheral necessities
- The aim is to have an 'accident-free workspace'. It focuses on the elimination of potential risks of accident and fires. Personnel dedicated to HSE can make the workplace operator-friendly by implementing timely safety measures.
- Development management – new product development
- Before any new product is incorporated into the manufacturing process, getting practical knowledge of the new product helps easy amalgamation of it into ongoing processes. Further, it also helps reach the pre-planned maintenance level quicker. TPM facilitates understanding of the new equipment, which in turn supports product design and development.
- TPM in administration – supporting plant operations
- Improving administrative function is crucial for improving how a plant operates and increasing productivity. this also includes analyzing the processes and procedures to eliminate losses. TPM in administration is a step usually taken after the four basic pillars are in place.
To add to this, material handling is considered to be another pillar of TPM. The linking element between man, machine, material, and method is material handling. Increase in total productivity cannot be possible if material handling is not organized and efficient.
Companies introducing TPM in their factories start by implementing the first four pillars (JH, KK, planned maintenance and quality maintenance) initially and then slowly widen their scope to include the remaining pillars to have complete implementation. For either a new or existing factory introducing TPM, introducing efficient material handling systems early on will help ensure successful TPM implementation.
Advantages of TPM in a factory
When it comes to production efficiency, TPM is the answer for every factory. TPM addresses all facets of the factory from material, machines, equipment, processes, and employees.
It brings in a positive approach in workers by bringing them into the loop of being responsible for their machines and its production. It helps workers develop multiple skills.
When it comes to machines, machines also become efficient because of timely maintenance. Regular maintenance ensures that systems and machines do not experience serious breakdowns or accidents. It ensures defect-free production along with maintaining the highest level of quality.
Also, the benefit of TPM in administration adds to this by having all people involved in support functions, with a focus on improving the plant performance. This results in the improvement of Overall Equipment Efficiency (OEE) of the plant.
TPM leads to TPM
Total Productive Maintenance leads to Total Profit Management. When TPM ensures zero defects, zero losses, and zero accidents while maintaining the highest level of quality, the result is customer satisfaction and increased business profits. If we do a cost-volume-profit analysis for an organization having introduced TPM effectively, total revenue will exceed total cost.
Daifuku's Role with TPM
Along with implementation, making way for the success of TPM starts with efficient material handling. Daifuku provides the means to achieve TPM goals with its Automated Storage and Retrieval Systems (AS/RS). Reaching TPM goals of zero defects, zero losses and zero accidents is made easy with Daifuku AS/RS technology. Automated storage solutions help utilize manpower efficiently and save on space. Automation and optimization increase productivity and help improve production quality and volume, setting new levels of manufacturing excellence and customer satisfaction.
About Daifuku Intralogistics India Pvt. Ltd.
Established in 1986, Daifuku Intralogistics India Pvt. Ltd., formerly known as Vega Conveyors and Automation Private Limited, is a leading provider of automated storage and conveying solutions in the Indian intralogistics market, with 350+ customers served. Employing around 200 people, the company is headquartered near Hyderabad, Telangana with offices in Mumbai and Pune as well.