Targets and Results
In the four-year business plan for 2027, we have reviewed our priority topics and set KPIs and four-year (fiscal 2024–2027) targets. The progress for our fiscal 2024 initiatives can be found on this page.
- Evolving existing businesses, expanding into new areas, developing next-generation solutions
- Establishing a system to bolster growth
- Revamping overall business operations
- Safety reinforcement
- Eliminating environmental impact
- Strengthening management structure and refining business management
- Organizational strengthening
Evolving existing businesses, expanding into new areas, developing next-generation solutions
We are strengthening the development of products and solutions that incorporate advanced technologies as well as our proposals aimed at new markets and meeting customer needs. We are making steady progress toward achieving the targets set for each business unit.
Materiality | Key Performance Indicators (KPIs) |
Scope | FY2024 Targets and Results | |
---|---|---|---|---|
Targets | Results | |||
Development utilizing advanced technologies including AI | Introduction of cutting-edge technology to products and services | Global |
|
|
Expansion of service business | Service sales | Global | 150.0 billion yen | 149.7 billion yen |
Development of new domains and creation of new businesses | Penetration into new markets and new business areas; commercialization of new products | Global |
|
|
- *Transportation Security Administration
Predictive maintenance system using AI technology
Please enlarge the screen to view
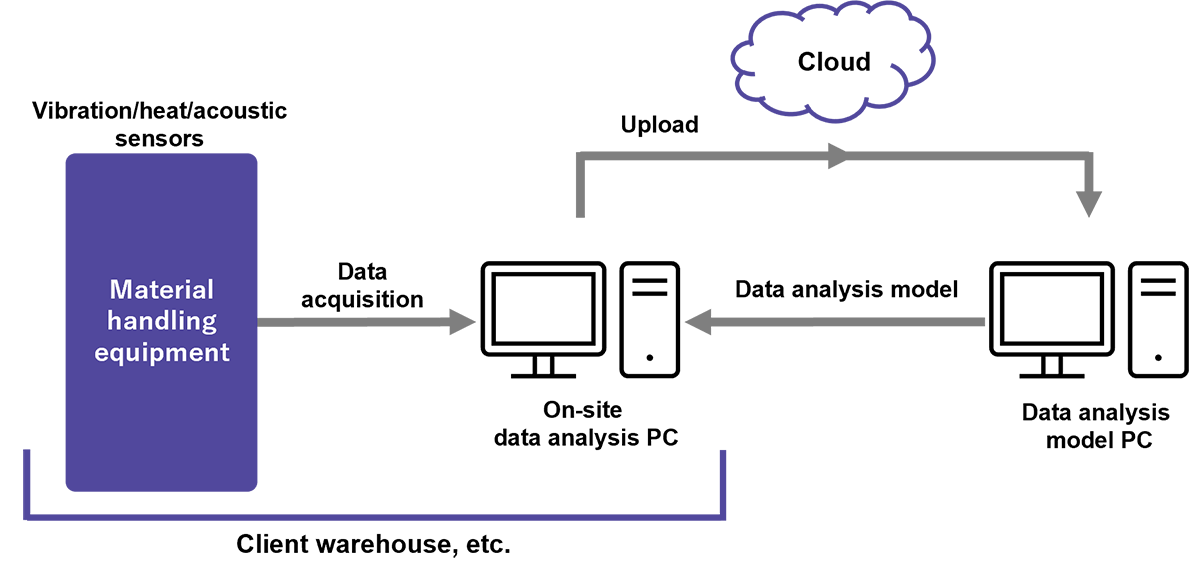
In our intralogistics business, the Group has established a unique predictive maintenance system that automates visual, manual, and auditory inspections. The predictive maintenance system measures vibration, heat generation, and acoustics using our proprietary sensors, analyzes the data collected by edge devices onsite using a PC, and notifies the customer of equipment abnormalities and predicted failure points. The system also automatically uploads data to the cloud, analyzes failure data, and builds an equipment diagnostic abnormality detection model using AI. This system eliminates conveyor system breakdowns and keeps equipment running smoothly.
Establishing a system to bolster growth
We are taking steps for the cultivation of human resources who will lead further growth of the Group and future-oriented technical development. We are also maintaining capital investments in Japan, the United States, and India, as well as investments for digitalization and expansion of our human capital.
Materiality | Key Performance Indicators (KPIs) |
Scope | FY2024 Targets and Results | |
---|---|---|---|---|
Targets | Results | |||
Investment and platform fortification for innovation creation | Investments in areas of growth* | Global |
|
|
Cultivation of human resources proficient in AI and other digital skills |
|
|
||
Promotion of industry-government-academia collaboration, M&A, alliances, etc. |
|
|
- *Capital investment, R&D expenses, investment in human capital, etc.
Advancing into the back-end processes of semiconductor manufacturing
The process of manufacturing semiconductors is divided into the front-end process of forming circuits on silicon wafers and the back-end process of cutting chips individually from wafers and working them into finished products. The cleanroom business of our Group has mainly provided transportation systems for the front-end process of semiconductor manufacturing lines. In recent years, however, we are gaining momentum in the development of next-generation technologies for back-end processes such as 3D stacking, in which multiple chips are stacked to enhance performance. As the importance of the back-end processes in the semiconductor manufacturing process increases, so does the need for automated transfer. In order to provide automated solutions for back-end processes, we are working to develop products that can accommodate the increased weight and diversified shapes of materials to be transported.
In addition, beginning in fiscal 2024, we are participating as a founding member of the Semiconductor Assembly Test Automation and Standardization Research Association (SATAS). SATAS was founded by 15 companies and organizations, which include semiconductor manufacturers, semiconductor manufacturing equipment and automated transport equipment manufacturers, and standardization organizations. At SATAS, we are creating the technologies and industry standard specifications necessary for back-end process automation as well as developing and integrating equipment and verifying its operation. We are aiming for practical application by 2028.
Construction of new plants
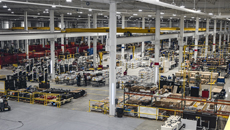
In fiscal 2023, Daifuku (Suzhou) Cleanroom Automation Co., Ltd., which handles sales and manufacturing of transport systems for LCD and semiconductor plants in Suzhou, China, relocated and began operations at a newly built headquarters and plant. The site has an area of approximately 31,000m2 and a total floor area of approximately 37,000m2, and this new facility is expected to increase production capacity by about 1.4 times that of the previous. The facility was built based on the concepts of progressiveness, energy conservation, CO2 emissions reduction, and social contribution, and it includes a display line for customers, a large-scale photovoltaic system on the roof, and a work environment that contributes to employee productivity.
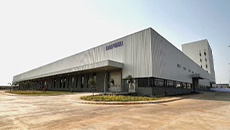
Daifuku Intralogistics India Private Limited, which develops systems for general manufacturing and distribution industries, has constructed a new plant in Telangana, India, and full-scale operations began in April of 2025. Due to the growth of the Indian market in recent years, the demand for material handling systems is increasing dramatically. With the construction of this new factory, the company will manufacture automated warehouses, conveyors, and other systems for manufacturers in the food, chemicals, machinery, and rubber product industries as well as retail, transport, and warehousing distributors, expanding the product lineup. The production space has been expanded to approximately four times that of the previous plant, and it is expected to double in size again in the future with further expansion. In addition, photovoltaic systems have been installed on the premises, and initiatives to reduce CO2 emissions are underway.
Revamping overall business operations
In order to disseminate the Group’s Sustainable Procurement Guidelines and to understand and mitigate risks in the supply chain, we started implementing a self-assessment questionnaire (SAQ) for suppliers in Japan based on these guidelines. We are strengthening our management of procurement risks through audits based on the results of responses to this questionnaire and interviews with subsidiaries outside of Japan among other measures.
Materiality | Key Performance Indicators (KPIs) |
Scope | FY2024 Targets and Results | |
---|---|---|---|---|
Targets | Results | |||
Social responsibility in the supply chain | Strengthening of supply chain management | Global |
|
|
Pursuit of product quality and product safety | Number of serious accidents* related to product and system safety | Global | 0 occurrences | 0 occurrences |
- *Accidents caused by the malfunction of Daifuku’s products or systems leading to death or serious illness and/or injury during operations (injury and/or illness requiring 30 or more days of treatment)
Safety reinforcement
Within and outside of Japan, the number of accidents resulting in lost time remained at the same level as the previous fiscal year. In order to prevent the recurrence of similar accidents, we will strengthen safety training within and outside of Japan, such as by sharing examples of past accidents.
Materiality | Key Performance Indicators (KPIs) |
Scope | FY2024 Targets and Results | |
---|---|---|---|---|
Targets | Results | |||
Ensure occupational safety and health | Frequency rate: Japan (outside of Japan)*1 |
Global | 0.261 (0.6) | 0.460 (0.7) |
Severity rate: Japan (outside of Japan)*1 |
0.006 (0.020) | 0.026 (0.009) | ||
Number of serious accidents*1, *2 | 0 occurrences | 1 occurrence |
- *1Calculations include installation contractors
- *2Accidents resulting in death or permanent injury during work at Daifuku
Eliminating environmental impact
To achieve the Daifuku Environmental Vision 2050, we are working to reduce the CO2 emissions generated throughout our supply chain and introduce electricity derived from renewable energy sources, and we are globally expanding our activities related to biodiversity conservation.
Materiality | Key Performance Indicators (KPIs) |
Scope | FY2024 Targets and Results | |
---|---|---|---|---|
Targets | Results | |||
Addressing climate change | Daifuku CO2 emissions reduction rate (compared to FY2018) (Scopes 1 + 2) |
Global | 51% | 56.4% |
Percentage of electricity derived from renewable energy sources | 60% | 66.6% | ||
Reduction rate of CO2 emissions from purchased goods and services*1 (Scope 3 Category 1) |
|
|
||
Reduction rate of CO2 emissions from the use of sold products*1 (Scope 3 Category 11) |
|
|
||
Promoting resource recycling | Landfill disposal rate | Global | Domestic: less than 1% Outside of Japan: less than 5% |
Domestic: 0.9% Outside of Japan: 8.7% |
Reduction rate of waste emissions per unit sales*3 (compared to FY2023) |
4% | 6.8% | ||
Reduction rate of water consumption per unit sales*4 (compared to FY2018) |
40% | 37.6% | ||
Coexisting with nature | Rate of implementation of biodiversity conservation activities at major sites*5 | Global | 10% | 36.4% |
Global expansion of Sustainability Action*6 |
|
|
- *1For Scope 3 Category 1 and Category 11, pursue qualitative targets with the aim of a 30% reduction (compared to FY2018) by FY2030
- *2Daifuku’s own framework on efforts (sharing of goals and supporting measures to reduce emissions, etc.) to reduce CO2 emissions at suppliers
- *3Waste generated (tons) divided by net sales (100 million yen)
- *4Water consumption (1,000 m3) divided by net sales (100 million yen)
- *5Sites with 100 or more employees
- *6Daifuku’s unique program for sustainability awareness and training
Strengthening management structure and refining business management
In addition to strengthening our management structure by improving the effectiveness of the Board of Directors, we are working to disseminate the management philosophy, Group policies, management strategies, etc., and to strengthen our response to critical risks with a view to refining business management on a global scale. We will also continue to engage in dialogue with all stakeholders and reflect the findings into our measures.
Materiality | Key Performance Indicators (KPIs) |
Scope | FY2024 Targets and Results | |
---|---|---|---|---|
Targets | Results | |||
Strengthening governance | Improvement of the effectiveness of the Board of Directors | Daifuku Co., Ltd |
|
|
Dissemination of management philosophy and strategies | Global |
|
|
|
Ensuring compliance |
|
|
||
Implementation of countermeasures against major risks |
|
|
||
Fulfillment of stakeholder communication | Number of dialogue meetings held with shareholders and investors (non-unique) | Global | More than 900 companies | 1,190 companies |
Enhancement of communication with stakeholders |
|
|
||
Maintenance and improvement of evaluations from external rating agencies |
|
|
Organizational strengthening
We are working to expand the human capital necessary to achieve further growth and to create an environment where each employee is able to realize a sense of job satisfaction and ease of work. Moreover, we are increasing our efforts to respect human rights, including by continuing to conduct human rights due diligence and beginning to consider the introduction of grievance mechanisms to support this process.
Materiality | Key Performance Indicators (KPIs) |
Scope | FY2024 Targets and Results | |
---|---|---|---|---|
Targets | Results | |||
Staff recruitment, retention, and training | Rate of sufficiency of number of prospective successors for key positions | Global |
|
|
Compounding of the human resources system in response to securement of specialized human resources | Daifuku Co., Ltd. |
|
|
|
Respect for human rights | Establishment of a human rights due diligence system | Global |
|
|
Implementation of human rights training |
|
|
||
Diversity and inclusion | Number of female managers (ratio) | Daifuku Co., Ltd. |
|
40 female managers (5.4%) |
Creation of an environment where diverse personnel can work effectively |
|
|
||
Improvement of employee engagement | Engagement survey score | Global |
|
|
Implementation of engagement survey and issue response |
|
|
Please refer to the document below for the priority topics and results of the Sustainability Action Plan, effective fiscal 2021 through fiscal 2023.