Special Feature
The Challenge to Be a Value Innovator
Providing Smart Logistics
Enhancing “visualization and optimization” in logistics, and realizing the value and competitive edge customers seek
Changes in Logistics Value
Advancements in communications technology have significantly changed the form of commercial transactions, and ushered in an era of direct links between companies and individuals. Sales channels have become consumer-to-business (C2B), and logistics, business-to-consumer (B2C), with goods flowing directly to consumers. Any consumer is able to place orders for the things they want anytime and anywhere, and, because goods are delivered directly without passing through stores, the issue in terms of logistics is to serve many and varied individuals in a way that it never had to before. The role played by logistics and the value demanded of logistics are rising rapidly. The material handling systems provided by Daifuku are increasingly important as part of the social infrastructure essential in such a logistics revolution.
The Smart Logistics Customers Need
Consumers and logistics have become directly linked, and the level of service demanded of logistics by customers has risen dramatically. With more-frequent deliveries, a rapidly increasing number of packages, and shorter lead times, logistics centers are becoming larger, with greater speed, precision, and complexity. Logistics systems need to be faster and more precise than ever, with stoppage unacceptable, and immediate recovery when an interruption occurs. By using the Internet of Things (IoT), information and communications technology (ICT), artificial intelligence (AI), and other technologies, Daifuku is accelerating the development speed and is improving delivery quality through virtual verification, and is providing the “smart logistics” customers need. With these technologies, development and testing are possible without physically making anything, the current status of operations can be confirmed without being on site, and predictions and preventive measures are made based on accumulated data. It will also become possible to enhance quality and shorten time in all processes from development to maintenance.
As logistics centers become larger, the need for automation in many different aspects rises. Enhancing “visualization and optimization” in logistics, and achieving lower logistics costs, shorter logistics time, and an improved quality and environment in logistics, delivers the value and competitive edge that customers seek.
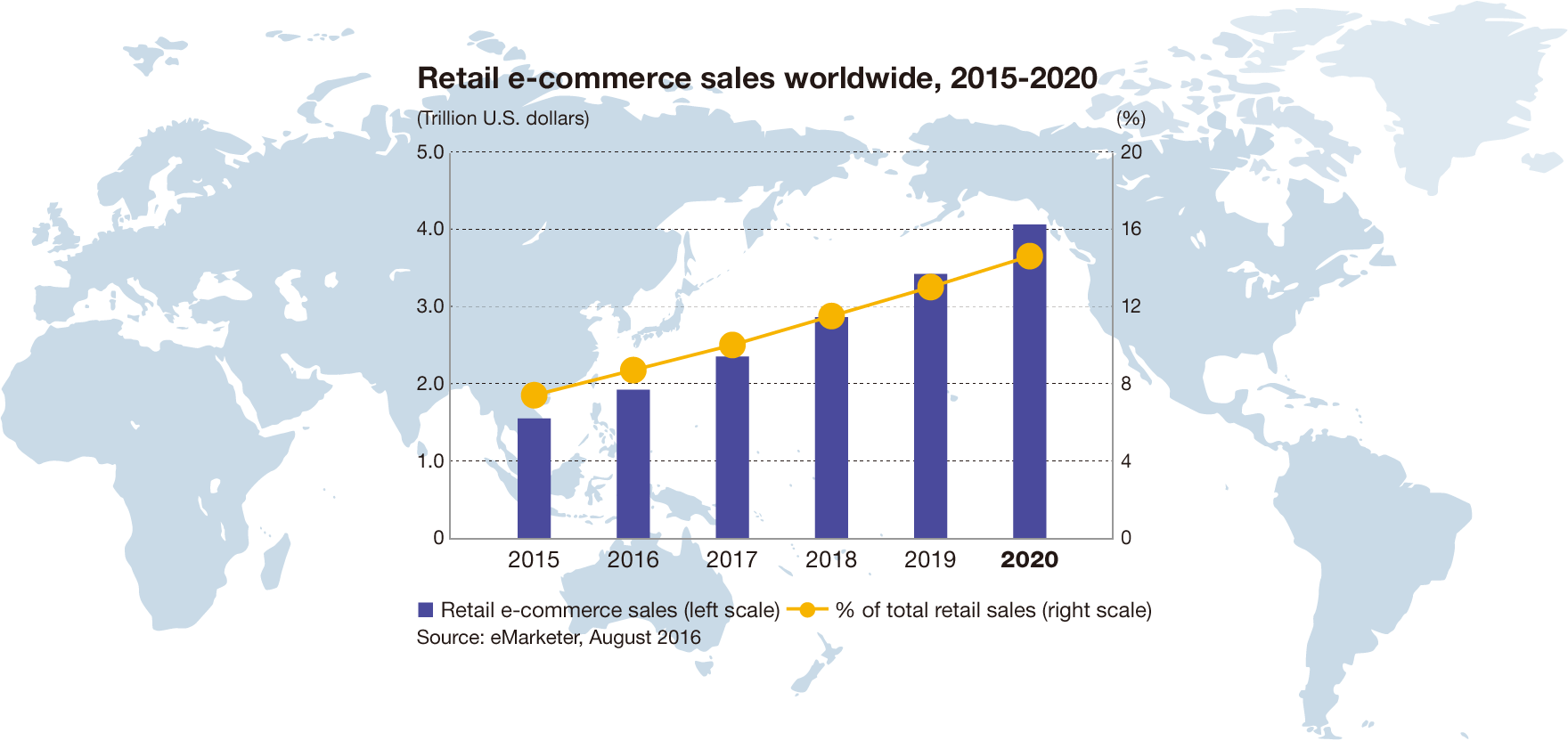
Message from the COO
Along with providing customers with smart logistics, initiatives to enhance productivity are essential. Daifuku implements fundamental innovations in production, resolving issues of muri (overburden), muda (waste), and mura (unevenness), three concepts originating in Japan that identify and eliminate waste from work, and using such technologies as IoT and AI to reform methods and processes. Pretesting in virtual spaces improves delivery quality, and eliminates the trouble of on-site adjustments. Visibility is enhanced by taking advantage of IoT and image recognition technology, and accumulated data analyzed to shorten recovery time following a disruption. Standardization and automation in operations also help in reducing costs, increasing quality, shortening work time, and in eliminating dependence on specific personnel. The cost and time saved create added value and lead to a sense of fulfillment for employees.
Accelerating innovation removes the limitations of a specific person, time, and place, and allows for the realization of “anything, anytime, anywhere, and anyone,” we believe. IoT and AI are tools to accelerate innovation. Daifuku will strive to enhance productivity and deliver the smart logistics demanded by customers.
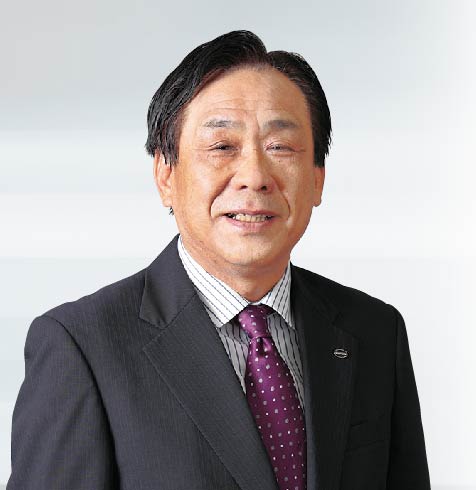
Akio Tanaka
Executive Vice President and COO
The Challenge to Be a Value Innovator
Establishing Airport Technologies
as One of Daifuku’s Four Core
Businesses
Expanding the business
scope to include software
along with hardware
Shifting to a Hybrid Solutions Provider
A total of 3.5 billion people traveled by air worldwide in 2015, and the International Air Transport Association (IATA) is projecting that this will double to around 7.0 billion in the next 20 years. Construction of new airports, new terminals and demand for increased efficiency, expansion and renovation of existing facilities are expected to further increase.
Considering this business environment, the Daifuku Group positions its Airport Technologies (ATec) as one of the four core businesses, which is a theme of the Value Innovation 2020 medium-term business plan. ATec is becoming a key source of revenue for the Group together with the three other core businesses, i.e. for manufacturers and distributors (FA&DA), for semiconductor and flat-panel display factories (eFA), and for automobile production lines (AFA).
At the heart of our growth strategy is a shift to being an end-to-end total solutions provider. In addition to the existing business centered on baggage handling systems (BHS) and other types of hardware, we are expanding the scope of operations to include sophisticated software elements that will assist in streamlining airport activities.
Integrating Solutions for the Future
Airports around the world are actively introducing digital technologies and security systems to create “smart airports” that offer enhanced passenger safety, security, and convenience.
The Group has built a global network covering markets in North America, Europe, and Asia Pacific, with strengths centered on total solutions incorporating BHSs, operations and maintenance, as well as self-service bag drop (SBD) systems. Using excellent innovative technology from the Group’s other core businesses, Daifuku ATec is in a very strong position to develop value-added solutions that will revolutionize the airports market. Some of the innovative products that have been developed include use of FA&DA’s highly innovative Automated Storage & Retrieval Systems (AS/RS) for early baggage storage and sortation batching, and the Mobile Inspection Table*1 that offers a new solution to enhance the effectiveness of baggage inspection.
Daifuku ATec has also started to integrate digital systems with the existing products as part of a plan to transition to a high-value-added business model. Examples of this include sharing of data acquired through the SBD system with an airline’s departure control system (DCS), integration of BHS/SBD information with various other airport systems including but not limited to airport management systems (AMS), airport operational databases (AODB), and baggage reconciliation systems (BRS) allowing for more efficient integrated management of airline, airport, passenger, and baggage information.
Self-service using SBD systems reduces passenger wait time and enhances the efficiency of airport operations. The SBD system is a device product that integrates hardware and software, and we expect it to generate strong earnings with more widespread adoption at airports, including for low-cost carriers.
The Sym3 software and control package is a 3D software tool incorporating on a single platform the three functions of simulation (system design verification), emulation (software verification), and SCADA (supervisory control and data acquisition).
Sym3 is able to test various operational scenarios in a simulation, allowing latent problems to be discovered at an early stage. The simulation data can also be forwarded to the emulation function to verify the control operation for the entire layout of actual equipment. We plan to apply this technology to the Group’s other core businesses, e.g. FA&DA’s manufacturing and distribution automation as well as airport facilities.
The SCADA function is also used in airport machinery facilities as an overall monitoring and control system. Tracking and managing baggage in real time enable immediate notification of alerts, which can be shared over mobile terminals to facilitate a prompt on-site response, helping to eliminate instances of lost baggage and strengthening security hence taking the IATA 753 requirements and compliance to an even higher level.
*1 Mobile Inspection Table (MIT): The MIT, using our “SmartCart” automatic guided cart, automatically transfers baggage from a conveyor, and transports it to a security inspection officer. The system uses an ergonomics approach to enhance the efficiency of inspection, eliminating the need for the security officer to lift or turn the bag. Baggage is automatically returned to the conveyor after inspection.
Message from the Head of Airport Technologies
In 2016, we received our first order for the Baggage Tray System (BTS), a promising new high-speed conveyor system, from Montreal Airport in Canada. The move prompted airports around the world to consider adopting the BTS, giving momentum to our sales activities.
This project was the result of a concerted effort among the Group companies*2 around the world, and serves as a new business model of global integration. Our ATec business is being handled as a unified operation under the Daifuku Airport Technologies brand. We will further strengthen our brand at the global level, focusing on the growing markets in the North American region.
*2 Companies include BCS Group Limited, Elite Line Services, Inc., Jervis B. Webb Company, Logan Teleflex, Inc., and Daifuku Logan Ltd., which all operate under the Daifuku ATec banner.
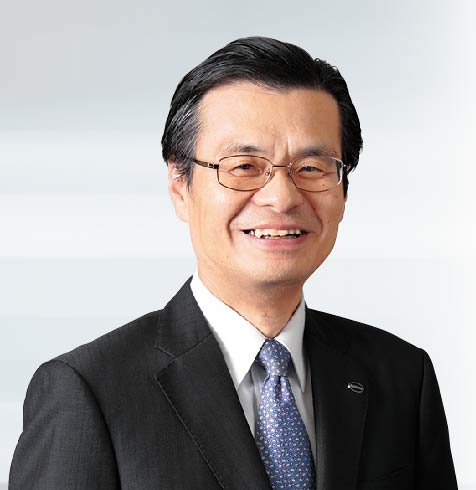
Shuichi Honda
Director
Senior Managing Officer
Corporate Business Development
Airport Technologies
The Challenge to Be a Value Innovator
Financial Strategies and Profit Allocation
Four years of
our strengthened financial
position led to enhanced
brand power
Establishing a Robust Financial Position under Value Innovation 2017
Increasing shareholders’ equity was one of the themes for the financial strategies in the four-year business plan Value Innovation 2017. Daifuku decided to issue 15.0 billion yen in convertible bonds, with an option for advanced redemption if the share price exceeded the conversion price by 120% or more for 20 business days, and after two years the share price rose steadily, with it eventually exceeding the 120% mark, leading to advanced redemptions being announced. Finally converting all convertible bonds to shares pushed Daifuku’s capital to 15.0 billion yen for the first time in a quarter century, with the equity ratio rising to 45.8%, compared to 40.4% in fiscal 2012, which was prior to the launch of Value Innovation 2017. We had a concern that the increased number of issued shares would dilute net income per share; however, through an increase in earning power, we raised this from 40 yen to 137 yen. Interest-bearing liabilities declined from 53.3 billion yen to 39.7 billion yen, with the D/E ratio falling from 0.64 times to 0.29 times.
ROE rose from 5.6% to 12.6%. Net assets (the denominator) increased with the bond conversion, but was offset by an upturn in the total asset turnover (1.03 times → 1.07 times), the result of steady growth in net income (4.4 billion yen → 16.7 billion yen), and an expansion in non-Japan sales, making it easier to collect advances. Free cash flow also increased, from 2.0 billion yen to 21.2 billion yen.
In 2016, Daifuku was included in the JPX-Nikkei Index 400, meeting the requirements including three-year cumulative operating income, three-year average ROE, and market capitalization. An additional factor was our proactive efforts to comply with Japan’s Corporate Governance Code introduced in 2015.
Daifuku also managed to drive its bond rating a bit further, from A-minus to A-flat. In short, these four years were a period in which strengthening our financial position also led to enhanced brand power.
Prior to Value Innovation 2017 (FY2012) | Value Innovation 2017 Targets | Value Innovation 2017 Results (FY2016) | Value Innovation 2020 Targets (FY2020) | |
---|---|---|---|---|
ROE | 5.6% | (Revised) 10% | 12.6% | Secure 10% or higher |
Net assets | ¥85.6 billion | — | ¥142.3 billion | — |
Net income per share | ¥40 | ¥137 | ||
Year-end stock price | ¥771 | ¥2,775 | ||
Annual dividend | ¥15 | ¥42 |
Capital Policy
The Daifuku Group has benefited greatly from the business environment, and is still in a position for more growth.
Our share price has reached 3,400 yen (on June 1, 2017), a considerable increase from 771 yen at the end of March 2012. Meeting market expectations of our growth, and continually increasing net income, is the royal road to enhancing corporate value and ROE.
For capital investment to ensure the next stage of growth, we plan to focus on expanding production facilities to support further growth beyond our target of 420 billion yen in net sales (picture top right: Daifuku’s U.S. demo center coming fall 2017). Our M&A efforts will center on incorporating leading-edge technologies, while supporting the business in Europe.
For shareholder returns, we continue to adhere to a payout ratio of 30%, and in fiscal 2016 paid a record dividend of 42 yen per share, which we plan to increase for a fifth consecutive year in fiscal 2017 to 47 yen.
Message from the CFO
The responsibility of a CFO is to enhance corporate value by establishing a robust financial position, providing for flexible investment, and ensuring appropriate shareholder returns. We achieved well-balanced results under the Value Innovation 2017 business plan, with net sales, total assets, and market capitalization over 300 billion yen.
At the same time, through communications with non-Japanese investors in particular, we realized that a company is not defined solely in terms of business results and figures. We also need to both minimize downside risk in corporate value with strict compliance, and to enhance upside potential by boosting our brand power.
Under the Value Innovation 2020 business plan, we aim to become the truly global leader in material handling. To accomplish this, we need a global management structure, and collaboration with subsidiaries and affiliates around the world.
Daifuku’s management division has formulated the C3 Declaration, comprising “Communication” (ensuring understanding with colleagues around the globe), “Creation” (proposals and remarks that anticipate change), and “Contribution” (contributing to business).
This is an internal declaration, but one that is equally applicable to a wide range of stakeholders. We will further enhance corporate value through C3-focused activities.
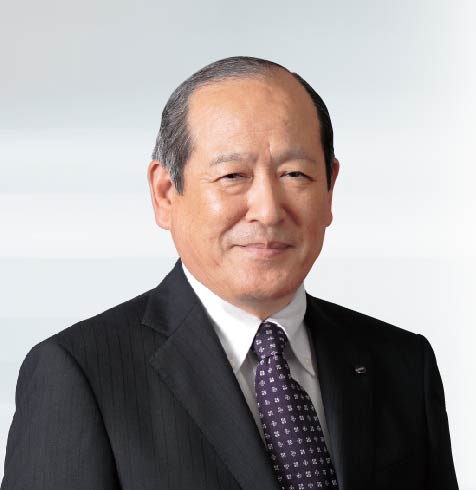
Mikio Inohara
Executive Vice President
CFO and CRO